Information injection-pump assembly
BOSCH
F 01G 003 002
f01g003002
ZEXEL
101609-3712
1016093712
KOMATSU
4063622
4063622
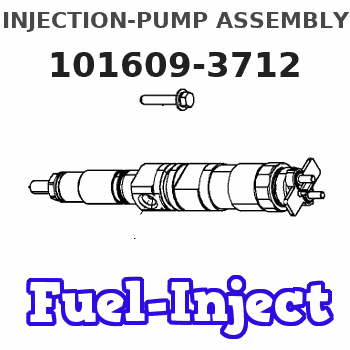
Rating:
Compare Prices: .
As an associate, we earn commssions on qualifying purchases through the links below
£1,985.47
31 Oct 2018
Robert Bos: Robert Bosch GmbH Au
Bosch F01G003002 Fuel-Injection Pump
Service parts 101609-3712 INJECTION-PUMP ASSEMBLY:
1.
_
5.
AUTOM. ADVANCE MECHANIS
6.
COUPLING PLATE
7.
COUPLING PLATE
8.
_
9.
_
11.
Nozzle and Holder
12.
Open Pre:MPa(Kqf/cm2)
22.0(224)
15.
NOZZLE SET
Include in #1:
101609-3712
as INJECTION-PUMP ASSEMBLY
Include in #2:
104265-4072
as _
Cross reference number
BOSCH
F 01G 003 002
f01g003002
ZEXEL
101609-3712
1016093712
KOMATSU
4063622
4063622
Zexel num
Bosch num
Firm num
Name
101609-3712
F 01G 003 002
4063622 KOMATSU
INJECTION-PUMP ASSEMBLY
SAA6D102E K 14BE INJECTION PUMP ASSY PE6A PE
SAA6D102E K 14BE INJECTION PUMP ASSY PE6A PE
101609-3712
F 01G 003 002
6738711150 KOMATSU
INJECTION-PUMP ASSEMBLY
SAA6D102E K 14BE INJECTION PUMP ASSY PE6A PE
SAA6D102E K 14BE INJECTION PUMP ASSY PE6A PE
Calibration Data:
Adjustment conditions
Test oil
1404 Test oil ISO4113 or {SAEJ967d}
1404 Test oil ISO4113 or {SAEJ967d}
Test oil temperature
degC
40
40
45
Nozzle and nozzle holder
105780-8140
Bosch type code
EF8511/9A
Nozzle
105780-0000
Bosch type code
DN12SD12T
Nozzle holder
105780-2080
Bosch type code
EF8511/9
Opening pressure
MPa
17.2
Opening pressure
kgf/cm2
175
Injection pipe
Outer diameter - inner diameter - length (mm) mm 6-2-600
Outer diameter - inner diameter - length (mm) mm 6-2-600
Overflow valve
131424-3420
Overflow valve opening pressure
kPa
255
221
289
Overflow valve opening pressure
kgf/cm2
2.6
2.25
2.95
Tester oil delivery pressure
kPa
255
255
255
Tester oil delivery pressure
kgf/cm2
2.6
2.6
2.6
Direction of rotation (viewed from drive side)
Right R
Right R
Injection timing adjustment
Direction of rotation (viewed from drive side)
Right R
Right R
Injection order
1-5-3-6-
2-4
Pre-stroke
mm
2.6
2.55
2.65
Rack position
After adjusting injection quantity. R=A
After adjusting injection quantity. R=A
Beginning of injection position
Drive side NO.1
Drive side NO.1
Difference between angles 1
Cal 1-5 deg. 60 59.5 60.5
Cal 1-5 deg. 60 59.5 60.5
Difference between angles 2
Cal 1-3 deg. 120 119.5 120.5
Cal 1-3 deg. 120 119.5 120.5
Difference between angles 3
Cal 1-6 deg. 180 179.5 180.5
Cal 1-6 deg. 180 179.5 180.5
Difference between angles 4
Cyl.1-2 deg. 240 239.5 240.5
Cyl.1-2 deg. 240 239.5 240.5
Difference between angles 5
Cal 1-4 deg. 300 299.5 300.5
Cal 1-4 deg. 300 299.5 300.5
Injection quantity adjustment
Adjusting point
A
Rack position
11
Pump speed
r/min
1000
1000
1000
Average injection quantity
mm3/st.
130.5
129.5
131.5
Max. variation between cylinders
%
0
-2.5
2.5
Basic
*
Fixing the lever
*
Boost pressure
kPa
70
70
Boost pressure
mmHg
525
525
Hydraulic cylinder ON
*
Injection quantity adjustment_02
Adjusting point
C
Rack position
7.4+-0.5
Pump speed
r/min
425
425
425
Average injection quantity
mm3/st.
11
10
12
Max. variation between cylinders
%
0
-15
15
Fixing the rack
*
Boost pressure
kPa
0
0
0
Boost pressure
mmHg
0
0
0
Hydraulic cylinder ON
*
Injection quantity adjustment_03
Adjusting point
E
Rack position
11.3++
Pump speed
r/min
100
100
100
Average injection quantity
mm3/st.
100
95
105
Fixing the lever
*
Boost pressure
kPa
0
0
0
Boost pressure
mmHg
0
0
0
Hydraulic cylinder OFF
*
Rack limit
*
Injection quantity adjustment_04
Adjusting point
F
Rack position
R1(11)
Pump speed
r/min
800
800
800
Average injection quantity
mm3/st.
133
123
143
Fixing the lever
*
Boost pressure
kPa
70
70
Boost pressure
mmHg
525
525
Hydraulic cylinder ON
*
Boost compensator adjustment
Pump speed
r/min
800
800
800
Rack position
8.9
Boost pressure
kPa
17.3
17.3
17.3
Boost pressure
mmHg
130
130
130
Boost compensator adjustment_02
Pump speed
r/min
800
800
800
Rack position
R1-1.3
Boost pressure
kPa
30.7
29.4
32
Boost pressure
mmHg
230
220
240
Boost compensator adjustment_03
Pump speed
r/min
800
800
800
Rack position
R1(11)
Boost pressure
kPa
56.7
56.7
56.7
Boost pressure
mmHg
425
425
425
Test data Ex:
Governor adjustment
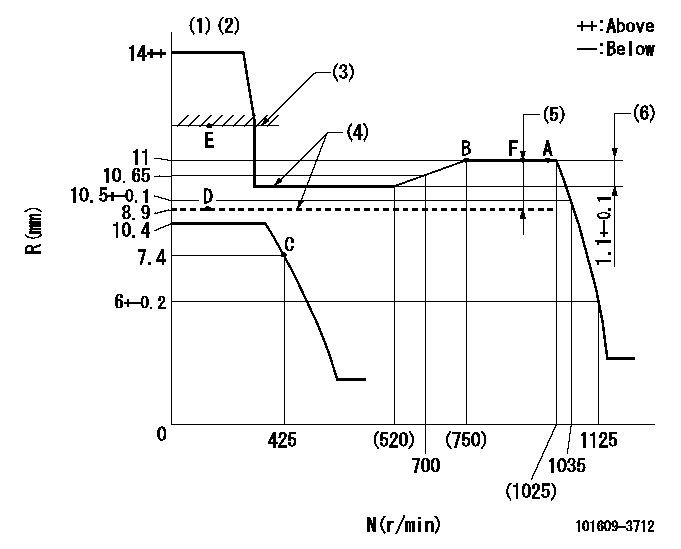
N:Pump speed
R:Rack position (mm)
(1)Target notch: K
(2)Tolerance for racks not indicated: +-0.05mm.
(3)RACK LIMIT (When hydraulic cylinder is OFF)
(4)When hydraulic cylinder ON: P1
(5)Boost compensator stroke: BCL
(6)Rack difference between N = N1 and N = N2
----------
K=16 P1=127+-10kPa(1.3+-0.1kgf/cm2) BCL=(2.1)mm N1=1000r/min N2=450r/min
----------
----------
K=16 P1=127+-10kPa(1.3+-0.1kgf/cm2) BCL=(2.1)mm N1=1000r/min N2=450r/min
----------
Speed control lever angle

F:Full speed
I:Idle
(1)Stopper bolt setting
----------
----------
a=12deg+-5deg b=33.5deg+-5deg
----------
----------
a=12deg+-5deg b=33.5deg+-5deg
Stop lever angle

N:Pump normal
S:Stop the pump.
(1)No return spring
----------
----------
a=0deg+-5deg b=53deg+-5deg
----------
----------
a=0deg+-5deg b=53deg+-5deg
0000001501 TAMPER PROOF
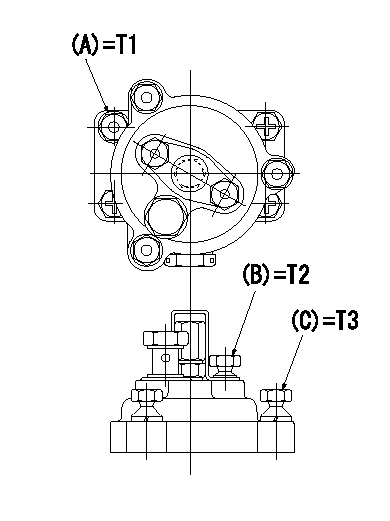
Tamperproofing-equipped boost compensator cover installation procedure
(1)After adjusting the governor and the boost compensator, tighten to the specified torque to break off the bolt heads.
(Tightening torque T = T1 maximum)
(2)After adjusting the governor and the boost compensator, tighten to the specified torque to break off the bolt heads.
(Tightening torque T = T2)
(3)After adjusting the governor and the boost compensator, tighten to the specified torque to break off the bolt heads.
(Tightening torque T = T3)
----------
T1=7.16~9.12N-m(0.73~0.93kgf-m) T2=2.9~4.4N-m(0.3~0.45kgf-m) T3=2.9~4.4N-m(0.3~0.45kgf-m)
----------
----------
T1=7.16~9.12N-m(0.73~0.93kgf-m) T2=2.9~4.4N-m(0.3~0.45kgf-m) T3=2.9~4.4N-m(0.3~0.45kgf-m)
----------
0000001601 I/P WITH LOAD PLUNGER ADJ
Adjusting procedure for load plunger equipped pump with RSV (cam lock) governor (see service information S.I. 434 for details).
At cam lift h+-0.01, set the camshaft c deg from the * mark in accordance with the timing adjustment procedure.
2. Align the flyweight's timing tooth position and the lock pin groove and then fully tighten the flyweight to the camshaft. Then, remove the lock pin.
3. Adjust the maximum variation between cylinders and injection quantity.
4. Adjust using the pre-stroke adjusting shim so that the pre-stroke value is the value for 4/4 load (standard point A).
5. After adjusting the pre-stroke, reconfirm that the injection quantity and the maximum variation between cylinders are as specified.
6. At delivery, again fix the flyweight using the lock pin.
----------
h=2.6+-0.01mm c=5deg15min+-30min
----------
----------
h=2.6+-0.01mm c=5deg15min+-30min
----------
Timing setting
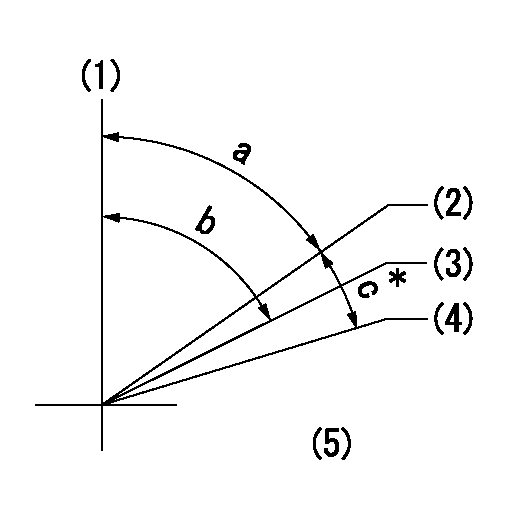
(1)Pump vertical direction
(2)Key groove position for No. 1 cylinder's cam lift h = cc (at BTDC aa).
(3)Key groove position for No. 1 cylinder's beginning of injection (at point A after injection quantity adjustment).
(4)Position of the key groove of the No. 1 cylinder at B.T.D.C. bb (fix the governor flyweight at this position for delivery).
(5)B.T.D.C.: aa
----------
aa=10.5deg bb=0deg cc=2.6+-0.01mm
----------
a=55deg18min+-3deg b=55deg18min+-3deg13min48sec c=5deg15min+-30min
----------
aa=10.5deg bb=0deg cc=2.6+-0.01mm
----------
a=55deg18min+-3deg b=55deg18min+-3deg13min48sec c=5deg15min+-30min
Information:
2. Remove pipe (1) and the gasket between aftercooler cover (2) and the turbocharger. If necessary, remove the O-ring seals from the pipe.3. Remove the bolts and clamps that hold tube assemblies (3) to each end of the aftercooler. Remove tube assemblies (3) from each end of the aftercooler. If necessary, remove the O-ring seals from the tube assemblies. An O-ring seal on each end of the aftercooler core holds the adapters in position.4. Remove adapters (4) and the gaskets from each end of the aftercooler.5. Remove all bolts (5) that hold aftercooler cover (2) in position. Remove the aftercooler cover and gasket from the engine. 6. Remove aftercooler core (6) and the gasket from the engine. If necessary, remove the O-ring seals from the aftercooler core. Two of the bolts that hold the aftercooler housing in position are on the inside of the aftercooler housing.7. Remove the bolts and spacers that hold aftercooler housing (7) to the engine. Make a note of the location of the spacers. Remove the aftercooler housing and gaskets from the engine.Install Aftercooler
Inspect all O-ring seals and gaskets, and make replacements if necessary. 1. Put the gaskets and aftercooler housing (1) in position on the engine. Install the bolts and spacers that hold the aftercooler housing.2. Install the O-ring seals on the aftercooler core, and put a thin layer of clean engine oil on them. Put the gasket and aftercooler core (2) in position on the engine. 3. Put the gasket and aftercooler cover (3) in position. Install the bolts that hold the aftercooler cover. Force may be required to push the adapters around the O-ring seals on the aftercooler core. Make sure the O-ring seals stay in position on the aftercooler core.4. Put a thin layer of clean engine oil in the bores of adapters (4). Install a gasket and adapter on each end of the aftercooler core. 5. Install the O-ring seals on tube assemblies (5), and put a thin layer of clean engine oil on them. Put the tube assemblies in position on each end of the aftercooler, and install the bolts and clamps that hold them.6. Install the O-ring seals on pipe (6), and put a thin layer of clean engine oil on them. Put the pipe and gasket in position between the aftercooler and the turbocharger. Install the bolts that hold it.7. Fill the radiator with coolant to the correct level. See the Operation & Maintenance Manual.
Inspect all O-ring seals and gaskets, and make replacements if necessary. 1. Put the gaskets and aftercooler housing (1) in position on the engine. Install the bolts and spacers that hold the aftercooler housing.2. Install the O-ring seals on the aftercooler core, and put a thin layer of clean engine oil on them. Put the gasket and aftercooler core (2) in position on the engine. 3. Put the gasket and aftercooler cover (3) in position. Install the bolts that hold the aftercooler cover. Force may be required to push the adapters around the O-ring seals on the aftercooler core. Make sure the O-ring seals stay in position on the aftercooler core.4. Put a thin layer of clean engine oil in the bores of adapters (4). Install a gasket and adapter on each end of the aftercooler core. 5. Install the O-ring seals on tube assemblies (5), and put a thin layer of clean engine oil on them. Put the tube assemblies in position on each end of the aftercooler, and install the bolts and clamps that hold them.6. Install the O-ring seals on pipe (6), and put a thin layer of clean engine oil on them. Put the pipe and gasket in position between the aftercooler and the turbocharger. Install the bolts that hold it.7. Fill the radiator with coolant to the correct level. See the Operation & Maintenance Manual.
Have questions with 101609-3712?
Group cross 101609-3712 ZEXEL
Komatsu
Komatsu
101609-3712
F 01G 003 002
4063622
INJECTION-PUMP ASSEMBLY
SAA6D102E
SAA6D102E
101609-3712
F 01G 003 002
6738711150
INJECTION-PUMP ASSEMBLY
SAA6D102E
SAA6D102E