Information injection-pump assembly
BOSCH
9 400 618 299
9400618299
ZEXEL
106871-8750
1068718750
HINO
220203700A
220203700a
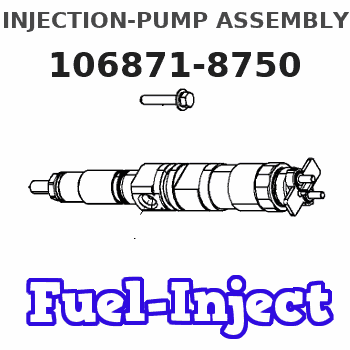
Rating:
Service parts 106871-8750 INJECTION-PUMP ASSEMBLY:
1.
_
7.
COUPLING PLATE
8.
_
9.
_
11.
Nozzle and Holder
23600-1660A
12.
Open Pre:MPa(Kqf/cm2)
21.6{220}
15.
NOZZLE SET
Include in #1:
106871-8750
as INJECTION-PUMP ASSEMBLY
Cross reference number
BOSCH
9 400 618 299
9400618299
ZEXEL
106871-8750
1068718750
HINO
220203700A
220203700a
Zexel num
Bosch num
Firm num
Name
106871-8750
9 400 618 299
220203700A HINO
INJECTION-PUMP ASSEMBLY
EF750T * K
EF750T * K
Calibration Data:
Adjustment conditions
Test oil
1404 Test oil ISO4113 or {SAEJ967d}
1404 Test oil ISO4113 or {SAEJ967d}
Test oil temperature
degC
40
40
45
Nozzle and nozzle holder
105780-8140
Bosch type code
EF8511/9A
Nozzle
105780-0000
Bosch type code
DN12SD12T
Nozzle holder
105780-2080
Bosch type code
EF8511/9
Opening pressure
MPa
17.2
Opening pressure
kgf/cm2
175
Injection pipe
Outer diameter - inner diameter - length (mm) mm 8-3-600
Outer diameter - inner diameter - length (mm) mm 8-3-600
Overflow valve
134424-3120
Overflow valve opening pressure
kPa
127
107
147
Overflow valve opening pressure
kgf/cm2
1.3
1.1
1.5
Tester oil delivery pressure
kPa
157
157
157
Tester oil delivery pressure
kgf/cm2
1.6
1.6
1.6
Direction of rotation (viewed from drive side)
Right R
Right R
Injection timing adjustment
Direction of rotation (viewed from drive side)
Right R
Right R
Injection order
1-8-6-2-
7-5-4-3
Pre-stroke
mm
3.9
3.84
3.9
Beginning of injection position
Drive side NO.1
Drive side NO.1
Difference between angles 1
Cal 1-8 deg. 45 44.75 45.25
Cal 1-8 deg. 45 44.75 45.25
Difference between angles 2
Cal 1-6 deg. 90 89.75 90.25
Cal 1-6 deg. 90 89.75 90.25
Difference between angles 3
Cyl.1-2 deg. 135 134.75 135.25
Cyl.1-2 deg. 135 134.75 135.25
Difference between angles 4
Cal 1-7 deg. 180 179.75 180.25
Cal 1-7 deg. 180 179.75 180.25
Difference between angles 5
Cal 1-5 deg. 225 224.75 225.25
Cal 1-5 deg. 225 224.75 225.25
Difference between angles 6
Cal 1-4 deg. 270 269.75 270.25
Cal 1-4 deg. 270 269.75 270.25
Difference between angles 7
Cal 1-3 deg. 315 314.75 315.25
Cal 1-3 deg. 315 314.75 315.25
Injection quantity adjustment
Adjusting point
A
Rack position
8.5
Pump speed
r/min
750
750
750
Average injection quantity
mm3/st.
160.9
158.9
162.9
Max. variation between cylinders
%
0
-4
4
Fixing the rack
*
Injection quantity adjustment_02
Adjusting point
B
Rack position
8.7
Pump speed
r/min
750
750
750
Average injection quantity
mm3/st.
168.3
166.3
170.3
Max. variation between cylinders
%
0
-2
2
Basic
*
Fixing the rack
*
Injection quantity adjustment_03
Adjusting point
C
Rack position
4.8+-0.5
Pump speed
r/min
360
360
360
Average injection quantity
mm3/st.
10.8
7.8
13.8
Max. variation between cylinders
%
0
-15
15
Fixing the rack
*
Injection quantity adjustment_04
Adjusting point
D
Rack position
-
Pump speed
r/min
100
100
100
Average injection quantity
mm3/st.
154
154
174
Fixing the lever
*
Timer adjustment
Pump speed
r/min
750++
Advance angle
deg.
0
0
0
Remarks
Do not advance until starting N = 750.
Do not advance until starting N = 750.
Timer adjustment_02
Pump speed
r/min
-
Advance angle
deg.
2.5
2.5
2.5
Remarks
Measure the actual speed, stop
Measure the actual speed, stop
Test data Ex:
Governor adjustment
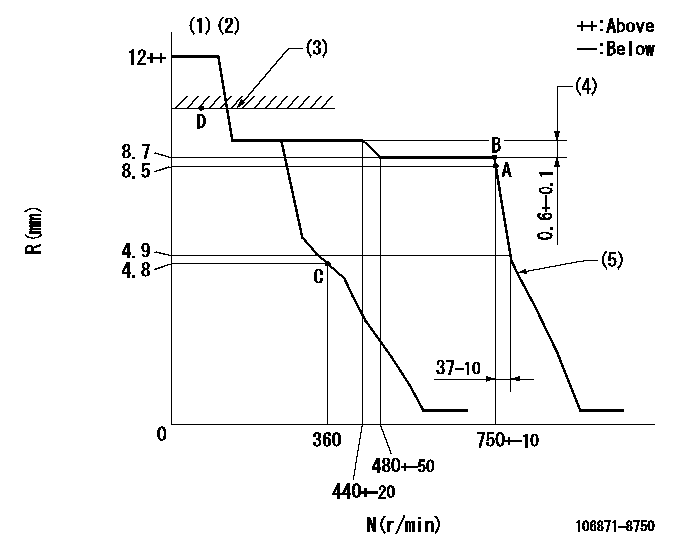
N:Pump speed
R:Rack position (mm)
(1)Target notch: K
(2)Damper spring does not operate.
(3)RACK LIMIT
(4)Rack difference between N = N1 and N = N2
(5)Idle sub spring setting: L1.
----------
K=13 N1=750r/min N2=400r/min L1=4.7-0.2mm
----------
----------
K=13 N1=750r/min N2=400r/min L1=4.7-0.2mm
----------
Speed control lever angle
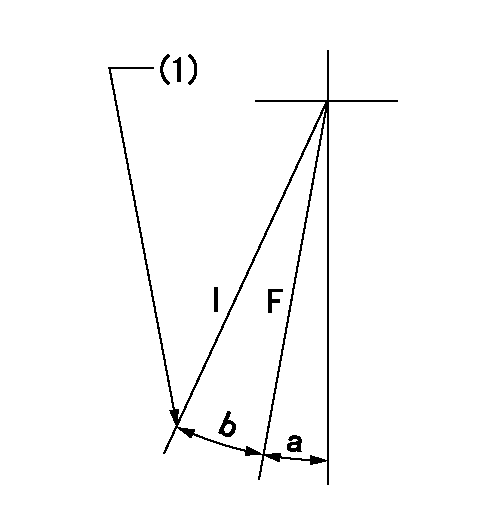
F:Full speed
I:Idle
(1)Stopper bolt setting
----------
----------
a=5deg+-5deg b=17deg+-5deg
----------
----------
a=5deg+-5deg b=17deg+-5deg
Stop lever angle
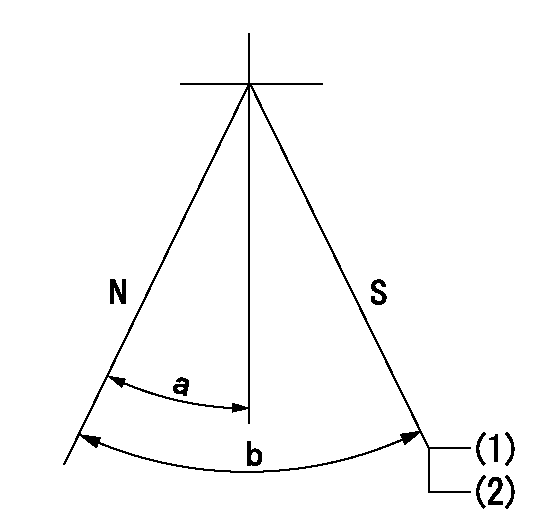
N:Pump normal
S:Stop the pump.
(1)At shipping
(2)Rack position aa or less, pump speed bb
----------
aa=4.3mm bb=0r/min
----------
a=26.5deg+-5deg b=53deg+-5deg
----------
aa=4.3mm bb=0r/min
----------
a=26.5deg+-5deg b=53deg+-5deg
Timing setting

(1)Pump vertical direction
(2)Coupling's key groove position at No 1 cylinder's beginning of injection
(3)-
(4)-
----------
----------
a=(90deg)
----------
----------
a=(90deg)
Information:
start by:a) remove turbocharger 1. Make a mark on compressor housing (1), cartridge assembly (3) and the turbine housing (4) for correct installation. 2. Loosen clamp assembly (2). Remove compressor housing (1) and cartridge assembly (3) from the turbine housing.3. Remove bolts (6) and plates (5) that hold cartridge assembly in the compressor housing. Remove cartridge assembly (3). 4. Remove O-ring seal (7) from the cartridge assembly. 5. Put cartridge assembly (3) in position in tooling (A) and loosen nut on the compressor wheel with tooling (C).6. Remove nut (8) and the compressor wheel (9). 7. Remove shaft and wheel assembly (10) from the cartridge assembly. 8. Remove shroud (11) from the cartridge assembly. 9. Remove four bolts (12) and then remove backplate (13) from the cartridge assembly.10. Remove spacer (14) from the backplate. 11. Remove two seal rings (15) from the spacer. 12. Remove snap ring (16) from cartridge housing with tool (B). 13. Remove bearing (17) and rings from the cartridge housing.14. Remove snap ring (18) from cartridge housing with tool (B). 15. Turn the cartridge housing over and then remove screws (20), plate (21) and collar (19). 16. Remove bearing (22) from the cartridge housing. 17. Remove snap ring (23) from the cartridge housing with tool (B).Assemble Turbocharger
Make sure all of the oil passages in the turbocharger cartridge housing are clean and free of dirt and foreign material. Put clean engine oil on all parts of the cartridge assembly. 1. Install snap ring (1) in the cartridge housing with tool (A). Make sure the oil hole in plate (5) is open and clean to prevent a bearing failure.2. Install bearing (2), collars (3), plate (5) and screws (4). Tighten the screws to
Make sure all of the oil passages in the turbocharger cartridge housing are clean and free of dirt and foreign material. Put clean engine oil on all parts of the cartridge assembly. 1. Install snap ring (1) in the cartridge housing with tool (A). Make sure the oil hole in plate (5) is open and clean to prevent a bearing failure.2. Install bearing (2), collars (3), plate (5) and screws (4). Tighten the screws to
Have questions with 106871-8750?
Group cross 106871-8750 ZEXEL
Hino
106871-8750
9 400 618 299
220203700A
INJECTION-PUMP ASSEMBLY
EF750T
EF750T