Information injection-pump assembly
BOSCH
F 01G 000 00T
f01g00000t
ZEXEL
101609-3850
1016093850
KOMATSU
4063554
4063554
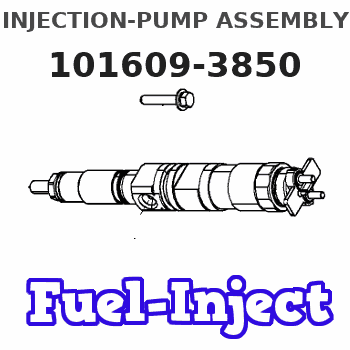
Rating:
Compare Prices: .
As an associate, we earn commssions on qualifying purchases through the links below
Service parts 101609-3850 INJECTION-PUMP ASSEMBLY:
1.
_
5.
AUTOM. ADVANCE MECHANIS
6.
COUPLING PLATE
7.
COUPLING PLATE
8.
_
9.
_
11.
Nozzle and Holder
12.
Open Pre:MPa(Kqf/cm2)
22.0{224}
15.
NOZZLE SET
Include in #1:
101609-3850
as INJECTION-PUMP ASSEMBLY
Include in #2:
104268-1200
as _
Cross reference number
BOSCH
F 01G 000 00T
f01g00000t
ZEXEL
101609-3850
1016093850
KOMATSU
4063554
4063554
Zexel num
Bosch num
Firm num
Name
101609-3850
F 01G 000 00T
4063554 KOMATSU
INJECTION-PUMP ASSEMBLY
SAA6D102E K 14BE INJECTION PUMP ASSY PE6A PE
SAA6D102E K 14BE INJECTION PUMP ASSY PE6A PE
101609-3850
F 01G 000 00T
6738711220 KOMATSU
INJECTION-PUMP ASSEMBLY
SAA6D102E K 14BE INJECTION PUMP ASSY PE6A PE
SAA6D102E K 14BE INJECTION PUMP ASSY PE6A PE
Calibration Data:
Adjustment conditions
Test oil
1404 Test oil ISO4113 or {SAEJ967d}
1404 Test oil ISO4113 or {SAEJ967d}
Test oil temperature
degC
40
40
45
Nozzle and nozzle holder
105780-8140
Bosch type code
EF8511/9A
Nozzle
105780-0000
Bosch type code
DN12SD12T
Nozzle holder
105780-2080
Bosch type code
EF8511/9
Opening pressure
MPa
17.2
Opening pressure
kgf/cm2
175
Injection pipe
Outer diameter - inner diameter - length (mm) mm 6-2-600
Outer diameter - inner diameter - length (mm) mm 6-2-600
Overflow valve
131424-3420
Overflow valve opening pressure
kPa
255
221
289
Overflow valve opening pressure
kgf/cm2
2.6
2.25
2.95
Tester oil delivery pressure
kPa
255
255
255
Tester oil delivery pressure
kgf/cm2
2.6
2.6
2.6
Direction of rotation (viewed from drive side)
Right R
Right R
Injection timing adjustment
Direction of rotation (viewed from drive side)
Right R
Right R
Injection order
1-5-3-6-
2-4
Pre-stroke
mm
2.6
2.55
2.65
Rack position
After adjusting injection quantity. R=A
After adjusting injection quantity. R=A
Beginning of injection position
Drive side NO.1
Drive side NO.1
Difference between angles 1
Cal 1-5 deg. 60 59.5 60.5
Cal 1-5 deg. 60 59.5 60.5
Difference between angles 2
Cal 1-3 deg. 120 119.5 120.5
Cal 1-3 deg. 120 119.5 120.5
Difference between angles 3
Cal 1-6 deg. 180 179.5 180.5
Cal 1-6 deg. 180 179.5 180.5
Difference between angles 4
Cyl.1-2 deg. 240 239.5 240.5
Cyl.1-2 deg. 240 239.5 240.5
Difference between angles 5
Cal 1-4 deg. 300 299.5 300.5
Cal 1-4 deg. 300 299.5 300.5
Injection quantity adjustment
Adjusting point
A
Rack position
8.4
Pump speed
r/min
1150
1150
1150
Average injection quantity
mm3/st.
84
83
85
Max. variation between cylinders
%
0
-2.5
2.5
Basic
*
Fixing the lever
*
Boost pressure
kPa
90.7
90.7
Boost pressure
mmHg
680
680
Hydraulic cylinder ON
*
Injection quantity adjustment_02
Adjusting point
-
Rack position
6.9+-0.5
Pump speed
r/min
350
350
350
Average injection quantity
mm3/st.
17.5
16.5
18.5
Max. variation between cylinders
%
0
-15
15
Fixing the rack
*
Boost pressure
kPa
0
0
0
Boost pressure
mmHg
0
0
0
Hydraulic cylinder ON
*
Remarks
Adjust only variation between cylinders; adjust governor according to governor specifications.
Adjust only variation between cylinders; adjust governor according to governor specifications.
Injection quantity adjustment_03
Adjusting point
E
Rack position
9.8+-0.5
Pump speed
r/min
100
100
100
Average injection quantity
mm3/st.
80
75
85
Fixing the lever
*
Boost pressure
kPa
0
0
0
Boost pressure
mmHg
0
0
0
Hydraulic cylinder OFF
*
Rack limit
*
Boost compensator adjustment
Pump speed
r/min
750
750
750
Rack position
7.7
Boost pressure
kPa
9.3
9.3
9.3
Boost pressure
mmHg
70
70
70
Boost compensator adjustment_02
Pump speed
r/min
750
750
750
Rack position
R1-0.3
Boost pressure
kPa
50.7
48
53.4
Boost pressure
mmHg
380
360
400
Boost compensator adjustment_03
Pump speed
r/min
750
750
750
Rack position
R1(8.4)
Boost pressure
kPa
77.3
74.6
80
Boost pressure
mmHg
580
560
600
Test data Ex:
Governor adjustment
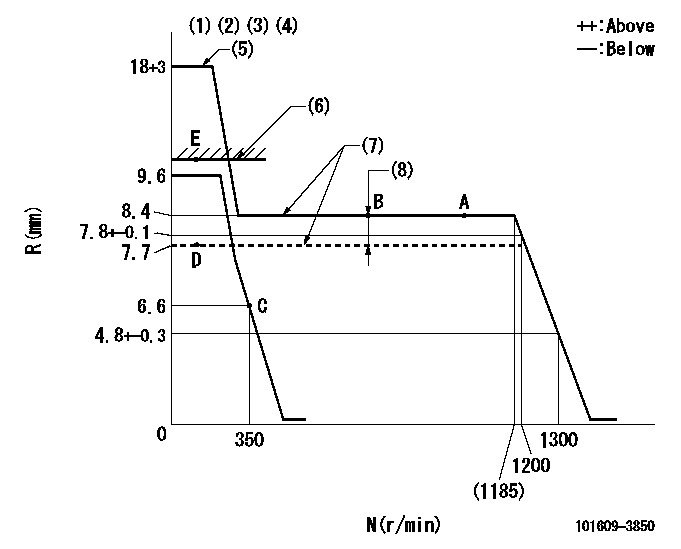
N:Pump speed
R:Rack position (mm)
(1)Target notch: K
(2)Tolerance for racks not indicated: +-0.05mm.
(3)Idle spring not operating.
(4)The torque control spring does not operate.
(5)When the hydraulic cylinder is OFF
(6)RACK LIMIT
(7)When hydraulic cylinder ON: P1
(8)Boost compensator stroke: BCL
----------
K=15 P1=(127+-10kPa(1.3+-0.1kgf/cm2)) BCL=(0.7)mm
----------
----------
K=15 P1=(127+-10kPa(1.3+-0.1kgf/cm2)) BCL=(0.7)mm
----------
Speed control lever angle

F:Full speed
I:Idle
(1)Stopper bolt setting
----------
----------
a=18.5deg+-5deg b=23deg+-5deg
----------
----------
a=18.5deg+-5deg b=23deg+-5deg
Stop lever angle

N:Pump normal
S:Stop the pump.
(1)No return spring
----------
----------
a=0deg+-5deg b=53deg+-5deg
----------
----------
a=0deg+-5deg b=53deg+-5deg
0000001501 TAMPER PROOF
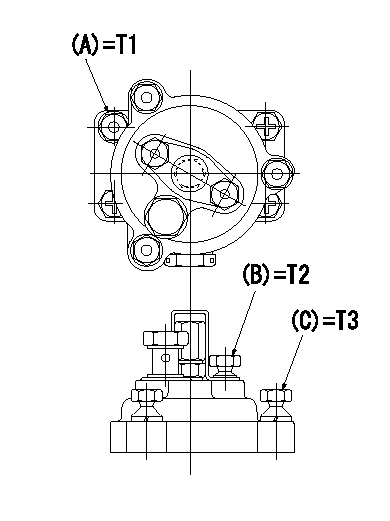
Tamperproofing-equipped boost compensator cover installation procedure
(1)After adjusting the governor and the boost compensator, tighten to the specified torque to break off the bolt heads.
(Tightening torque T = T1 maximum)
(2)After adjusting the governor and the boost compensator, tighten to the specified torque to break off the bolt heads.
(Tightening torque T = T2)
(3)After adjusting the governor and the boost compensator, tighten to the specified torque to break off the bolt heads.
(Tightening torque T = T3)
----------
T1=7.16~9.12N-m(0.73~0.93kgf-m) T2=2.9~4.4N-m(0.3~0.45kgf-m) T3=2.9~4.4N-m(0.3~0.45kgf-m)
----------
----------
T1=7.16~9.12N-m(0.73~0.93kgf-m) T2=2.9~4.4N-m(0.3~0.45kgf-m) T3=2.9~4.4N-m(0.3~0.45kgf-m)
----------
0000001601 I/P WITH LOAD PLUNGER ADJ
Adjusting procedure for load plunger equipped pump with RSV (cam lock) governor (see service information S.I. 434 for details).
At cam lift h+-0.01, set the camshaft c deg from the * mark in accordance with the timing adjustment procedure.
2. Align the flyweight's timing tooth position and the lock pin groove and then fully tighten the flyweight to the camshaft. Then, remove the lock pin.
3. Adjust the maximum variation between cylinders and injection quantity.
4. Adjust using the pre-stroke adjusting shim so that the pre-stroke value is the value for 4/4 load (standard point A).
5. After adjusting the pre-stroke, reconfirm that the injection quantity and the maximum variation between cylinders are as specified.
6. At delivery, again fix the flyweight using the lock pin.
----------
h=2.6+-0.01mm c=5deg54min+-30min
----------
----------
h=2.6+-0.01mm c=5deg54min+-30min
----------
Timing setting
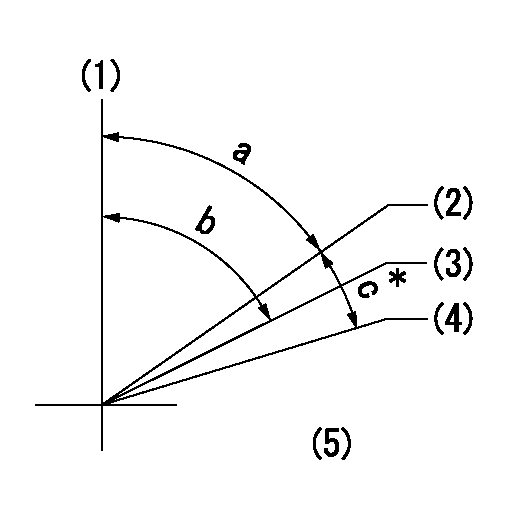
(1)Pump vertical direction
(2)Key groove position for No. 1 cylinder's cam lift h = cc (at BTDC aa).
(3)Key groove position for No. 1 cylinder's beginning of injection (at point A after injection quantity adjustment).
(4)Position of the key groove of the No. 1 cylinder at B.T.D.C. bb (fix the governor flyweight at this position for delivery).
(5)B.T.D.C.: aa
----------
aa=11.8deg bb=0deg cc=2.6+-0.01mm
----------
a=55deg18min+-3deg b=55deg18min+-3deg13min48sec c=5deg54min+-30min
----------
aa=11.8deg bb=0deg cc=2.6+-0.01mm
----------
a=55deg18min+-3deg b=55deg18min+-3deg13min48sec c=5deg54min+-30min
Information:
January 9, 2003
O-10
Priority PRODUCT IMPROVEMENT PROGRAM FOR INSTALLINGA NEW WIRE ASSEMBLY IN THE INJECTION ACTUATION PRESSURE CONTROL ON CERTAIN325C AND 325C L EXCAVATORS AND 950G II AND 962G II WHEEL LOADERS
1408 PI30431
This Program must be administered assoon as possible. When reporting the repair, use "PI30431" as the Partnumber and "7751" as the Group Number, "56" as the Warranty Claim DescriptionCode and "T" as the SIMS Description Code. Exception: If the repair isdone after failure, use "PI30431" as the Part Number, "7751" as the GroupNumber, "96" as the Warranty Claim Description Code, and "Z" as the SIMSDescription Code. The information supplied in this serviceletter may not be valid after the termination date of this program. Donot perform the work outlined in this Service Letter after the terminationdate without first contacting your Caterpillar product analyst.
COMPLETION DATE
TERMINATION DATE
July 31, 2003 January 31, 2004PROBLEM
A new wire assembly needs to be installed in theinjection actuation pressure control on certain 325C and 325C L Excavatorsand 950G II and 962G II Wheel Loaders. The injection actuation pressurecontrol valve connector may have been assembled incorrectly some 3126BEngine harness. This can lead to intermittent engine operation or can causethe engine to stop. The wire assembly must be replaced.AFFECTED PRODUCT
Model Identification Number
325C L CRB465, 466, 468, 469
325C CSJ571, 572, 574, 578, 582, 586
950G II AYL587, 591, 592, 598-601,610, 612, 615AYB486-491
962G AYE459
962G II BAB336, 338PARTS NEEDED
1 - 2324367 Wire AssemblyACTION REQUIRED
See the attached Rework Procedure.SERVICE CLAIM ALLOWANCES
Caterpillar Dealer Suggested Customer Suggested
Parts Labor Hrs. Parts Labor Hrs. Parts Labor Hrs.
100% 1 0 0 0 0
This is a 1-hour job.PARTS DISPOSITION
Handle the parts in accordance with your WarrantyBulletin on warranty parts handling.
MAKE EVERY EFFORT TO COMPLETE THIS PROGRAMAS SOON AS POSSIBLE.Attach. (1-Sample of Owner Notification)
(2-Rework Procedure)SAMPLE OF OWNER NOTIFICATION
XYZ Corporation
3240 Arrow Drive
Anywhere, YZ 99999PRIORITY - Install A New Wire Assembly In TheInjection Actuation Pressure ControlMODELS INVOLVED - 325C and 325C L Excavatorsand 950G II and 962G II Wheel LoadersDear Caterpillar Product Owner:A new wire assembly needs to be installed inthe injection actuation pressure control on certain 325C and 325C L Excavatorsand 950G II and 962G II Wheel Loaders. The injection actuation pressurecontrol valve connector may have been assembled incorrectly some 3126BEngine harness. This can lead to intermittent engine operation or can causethe engine to stop. The wire assembly must be replaced. A new wire assemblyneeds to be installed on the products listed below. You will not be chargedfor the service performed.Contact your local Caterpillar dealer immediatelyto schedule this service. The dealer will advise you of the time requiredto complete this service. Please refer the dealer to their Service Letterdated January 9, 2003 when scheduling this service.We regret the inconvenience this may causeyou, but urge you to have this service performed as soon as possible toprevent unscheduled downtime.Caterpillar Inc.
Identification #(s)Attached to January 9, 2003 Service Letter
Rework Procedure
Disconnect the IAP control valve connector (seeIllustration 1).
Cut the wires behind the connector.
Strip the ends of both wires.
Install 2324367 harness by crimping the strippedwires inside the splice. Take care to connect pink wire to pink wire onone hand, purple wire to purple wire on the other hand.
Heat both heat shrinkable tubes in order to insulateboth splices.
Reconnect the
O-10
Priority PRODUCT IMPROVEMENT PROGRAM FOR INSTALLINGA NEW WIRE ASSEMBLY IN THE INJECTION ACTUATION PRESSURE CONTROL ON CERTAIN325C AND 325C L EXCAVATORS AND 950G II AND 962G II WHEEL LOADERS
1408 PI30431
This Program must be administered assoon as possible. When reporting the repair, use "PI30431" as the Partnumber and "7751" as the Group Number, "56" as the Warranty Claim DescriptionCode and "T" as the SIMS Description Code. Exception: If the repair isdone after failure, use "PI30431" as the Part Number, "7751" as the GroupNumber, "96" as the Warranty Claim Description Code, and "Z" as the SIMSDescription Code. The information supplied in this serviceletter may not be valid after the termination date of this program. Donot perform the work outlined in this Service Letter after the terminationdate without first contacting your Caterpillar product analyst.
COMPLETION DATE
TERMINATION DATE
July 31, 2003 January 31, 2004PROBLEM
A new wire assembly needs to be installed in theinjection actuation pressure control on certain 325C and 325C L Excavatorsand 950G II and 962G II Wheel Loaders. The injection actuation pressurecontrol valve connector may have been assembled incorrectly some 3126BEngine harness. This can lead to intermittent engine operation or can causethe engine to stop. The wire assembly must be replaced.AFFECTED PRODUCT
Model Identification Number
325C L CRB465, 466, 468, 469
325C CSJ571, 572, 574, 578, 582, 586
950G II AYL587, 591, 592, 598-601,610, 612, 615AYB486-491
962G AYE459
962G II BAB336, 338PARTS NEEDED
1 - 2324367 Wire AssemblyACTION REQUIRED
See the attached Rework Procedure.SERVICE CLAIM ALLOWANCES
Caterpillar Dealer Suggested Customer Suggested
Parts Labor Hrs. Parts Labor Hrs. Parts Labor Hrs.
100% 1 0 0 0 0
This is a 1-hour job.PARTS DISPOSITION
Handle the parts in accordance with your WarrantyBulletin on warranty parts handling.
MAKE EVERY EFFORT TO COMPLETE THIS PROGRAMAS SOON AS POSSIBLE.Attach. (1-Sample of Owner Notification)
(2-Rework Procedure)SAMPLE OF OWNER NOTIFICATION
XYZ Corporation
3240 Arrow Drive
Anywhere, YZ 99999PRIORITY - Install A New Wire Assembly In TheInjection Actuation Pressure ControlMODELS INVOLVED - 325C and 325C L Excavatorsand 950G II and 962G II Wheel LoadersDear Caterpillar Product Owner:A new wire assembly needs to be installed inthe injection actuation pressure control on certain 325C and 325C L Excavatorsand 950G II and 962G II Wheel Loaders. The injection actuation pressurecontrol valve connector may have been assembled incorrectly some 3126BEngine harness. This can lead to intermittent engine operation or can causethe engine to stop. The wire assembly must be replaced. A new wire assemblyneeds to be installed on the products listed below. You will not be chargedfor the service performed.Contact your local Caterpillar dealer immediatelyto schedule this service. The dealer will advise you of the time requiredto complete this service. Please refer the dealer to their Service Letterdated January 9, 2003 when scheduling this service.We regret the inconvenience this may causeyou, but urge you to have this service performed as soon as possible toprevent unscheduled downtime.Caterpillar Inc.
Identification #(s)Attached to January 9, 2003 Service Letter
Rework Procedure
Disconnect the IAP control valve connector (seeIllustration 1).
Cut the wires behind the connector.
Strip the ends of both wires.
Install 2324367 harness by crimping the strippedwires inside the splice. Take care to connect pink wire to pink wire onone hand, purple wire to purple wire on the other hand.
Heat both heat shrinkable tubes in order to insulateboth splices.
Reconnect the
Have questions with 101609-3850?
Group cross 101609-3850 ZEXEL
Komatsu
Komatsu
Komatsu
101609-3850
F 01G 000 00T
4063554
INJECTION-PUMP ASSEMBLY
SAA6D102E
SAA6D102E
101609-3850
F 01G 000 00T
6738711220
INJECTION-PUMP ASSEMBLY
SAA6D102E
SAA6D102E