Information injection-pump assembly
BOSCH
9 400 613 473
9400613473
ZEXEL
101609-3810
1016093810
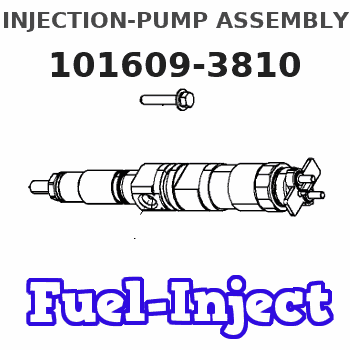
Rating:
Service parts 101609-3810 INJECTION-PUMP ASSEMBLY:
1.
_
5.
AUTOM. ADVANCE MECHANIS
6.
COUPLING PLATE
7.
COUPLING PLATE
8.
_
9.
_
11.
Nozzle and Holder
12.
Open Pre:MPa(Kqf/cm2)
22.0{224}
15.
NOZZLE SET
Include in #1:
101609-3810
as INJECTION-PUMP ASSEMBLY
Include in #2:
104268-1120
as _
Cross reference number
BOSCH
9 400 613 473
9400613473
ZEXEL
101609-3810
1016093810
Zexel num
Bosch num
Firm num
Name
101609-3810
9 400 613 473
INJECTION-PUMP ASSEMBLY
SAA6D102 14BE INJECTION PUMP ASSY PE6A PE
SAA6D102 14BE INJECTION PUMP ASSY PE6A PE
9 400 613 473
6738711190 KOMATSU
INJECTION-PUMP ASSEMBLY
SAA6D102 * K 14BE INJECTION PUMP ASSY PE6A PE
SAA6D102 * K 14BE INJECTION PUMP ASSY PE6A PE
Calibration Data:
Adjustment conditions
Test oil
1404 Test oil ISO4113 or {SAEJ967d}
1404 Test oil ISO4113 or {SAEJ967d}
Test oil temperature
degC
40
40
45
Nozzle and nozzle holder
105780-8140
Bosch type code
EF8511/9A
Nozzle
105780-0000
Bosch type code
DN12SD12T
Nozzle holder
105780-2080
Bosch type code
EF8511/9
Opening pressure
MPa
17.2
Opening pressure
kgf/cm2
175
Injection pipe
Outer diameter - inner diameter - length (mm) mm 6-2-600
Outer diameter - inner diameter - length (mm) mm 6-2-600
Overflow valve
131424-3420
Overflow valve opening pressure
kPa
255
221
289
Overflow valve opening pressure
kgf/cm2
2.6
2.25
2.95
Tester oil delivery pressure
kPa
255
255
255
Tester oil delivery pressure
kgf/cm2
2.6
2.6
2.6
Direction of rotation (viewed from drive side)
Right R
Right R
Injection timing adjustment
Direction of rotation (viewed from drive side)
Right R
Right R
Injection order
1-5-3-6-
2-4
Pre-stroke
mm
2.6
2.55
2.65
Rack position
After adjusting injection quantity. R=A
After adjusting injection quantity. R=A
Beginning of injection position
Drive side NO.1
Drive side NO.1
Difference between angles 1
Cal 1-5 deg. 60 59.5 60.5
Cal 1-5 deg. 60 59.5 60.5
Difference between angles 2
Cal 1-3 deg. 120 119.5 120.5
Cal 1-3 deg. 120 119.5 120.5
Difference between angles 3
Cal 1-6 deg. 180 179.5 180.5
Cal 1-6 deg. 180 179.5 180.5
Difference between angles 4
Cyl.1-2 deg. 240 239.5 240.5
Cyl.1-2 deg. 240 239.5 240.5
Difference between angles 5
Cal 1-4 deg. 300 299.5 300.5
Cal 1-4 deg. 300 299.5 300.5
Injection quantity adjustment
Adjusting point
A
Rack position
10.6
Pump speed
r/min
1000
1000
1000
Average injection quantity
mm3/st.
127.5
126.5
128.5
Max. variation between cylinders
%
0
-2.5
2.5
Basic
*
Fixing the lever
*
Boost pressure
kPa
140
140
Boost pressure
mmHg
1050
1050
Hydraulic cylinder ON
*
Injection quantity adjustment_02
Adjusting point
-
Rack position
7.2+-0.5
Pump speed
r/min
450
450
450
Average injection quantity
mm3/st.
13
12
14
Max. variation between cylinders
%
0
-15
15
Fixing the rack
*
Boost pressure
kPa
0
0
0
Boost pressure
mmHg
0
0
0
Hydraulic cylinder ON
*
Remarks
Adjust only variation between cylinders; adjust governor according to governor specifications.
Adjust only variation between cylinders; adjust governor according to governor specifications.
Injection quantity adjustment_03
Adjusting point
F
Rack position
11.3++
Pump speed
r/min
100
100
100
Average injection quantity
mm3/st.
105
100
110
Fixing the lever
*
Boost pressure
kPa
0
0
0
Boost pressure
mmHg
0
0
0
Hydraulic cylinder OFF
*
Rack limit
*
Boost compensator adjustment
Pump speed
r/min
750
750
750
Rack position
8.9
Boost pressure
kPa
20
13.3
26.7
Boost pressure
mmHg
150
100
200
Boost compensator adjustment_02
Pump speed
r/min
750
750
750
Rack position
10.2
Boost pressure
kPa
80
76
84
Boost pressure
mmHg
600
570
630
Boost compensator adjustment_03
Pump speed
r/min
750
750
750
Rack position
11.1
Boost pressure
kPa
127
127
127
Boost pressure
mmHg
950
950
950
Test data Ex:
Governor adjustment
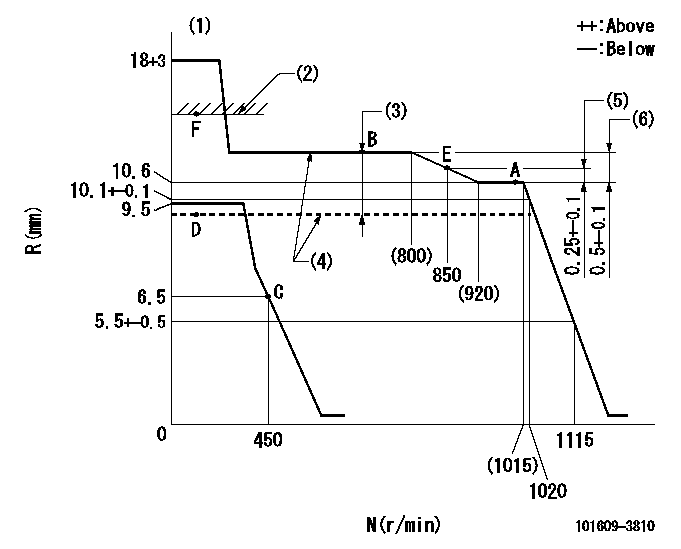
N:Pump speed
R:Rack position (mm)
(1)Target notch: K
(2)RACK LIMIT (When hydraulic cylinder is OFF)
(3)Boost compensator stroke: BCL
(4)When hydraulic cylinder ON: P1
(5)Rack difference from N = N1
(6)Rack difference between N = N2 and N = N3
----------
K=10 BCL=2.2+-0.1mm P1=127+-10kPa(1.3+-0.1kgf/cm2) N1=1000r/min N2=1000r/min N3=750r/min
----------
----------
K=10 BCL=2.2+-0.1mm P1=127+-10kPa(1.3+-0.1kgf/cm2) N1=1000r/min N2=1000r/min N3=750r/min
----------
Speed control lever angle
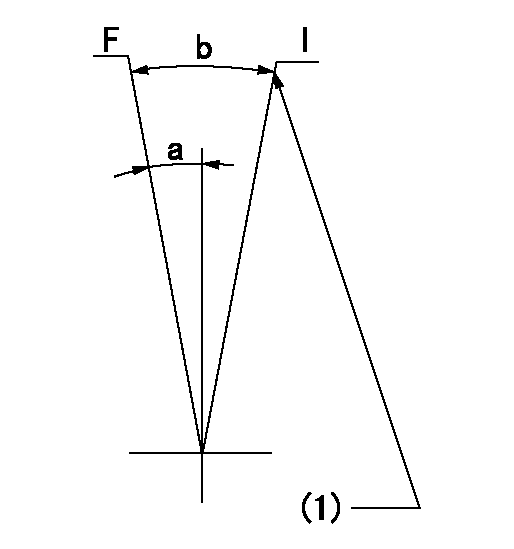
F:Full speed
I:Idle
(1)Stopper bolt setting
----------
----------
a=11deg+-5deg b=30deg+-5deg
----------
----------
a=11deg+-5deg b=30deg+-5deg
Stop lever angle

N:Pump normal
S:Stop the pump.
(1)No return spring
----------
----------
a=0deg+-5deg b=53deg+-5deg
----------
----------
a=0deg+-5deg b=53deg+-5deg
0000001501 TAMPER PROOF
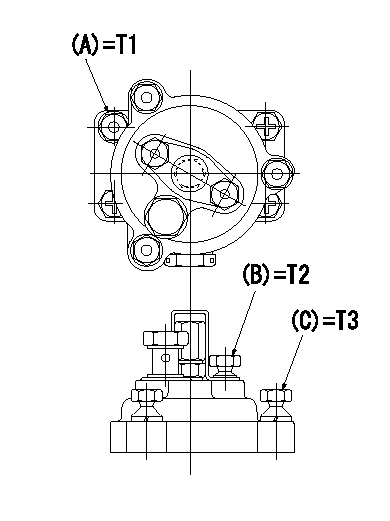
Tamperproofing-equipped boost compensator cover installation procedure
(1)After adjusting the governor and the boost compensator, tighten to the specified torque to break off the bolt heads.
(Tightening torque T = T1 maximum)
(2)After adjusting the governor and the boost compensator, tighten to the specified torque to break off the bolt heads.
(Tightening torque T = T2)
(3)After adjusting the governor and the boost compensator, tighten to the specified torque to break off the bolt heads.
(Tightening torque T = T3)
----------
T1=7.16~9.12N-m(0.73~0.93kgf-m) T2=2.9~4.4N-m(0.3~0.45kgf-m) T3=2.9~4.4N-m(0.3~0.45kgf-m)
----------
----------
T1=7.16~9.12N-m(0.73~0.93kgf-m) T2=2.9~4.4N-m(0.3~0.45kgf-m) T3=2.9~4.4N-m(0.3~0.45kgf-m)
----------
0000001601 I/P WITH LOAD PLUNGER ADJ
Adjusting procedure for load plunger equipped pump with RSV (cam lock) governor (see service information S.I. 434 for details).
At cam lift h+-0.01, set the camshaft c deg from the * mark in accordance with the timing adjustment procedure.
2. Align the flyweight's timing tooth position and the lock pin groove and then fully tighten the flyweight to the camshaft. Then, remove the lock pin.
3. Adjust the maximum variation between cylinders and injection quantity.
4. Adjust using the pre-stroke adjusting shim so that the pre-stroke value is the value for 4/4 load (standard point A).
5. After adjusting the pre-stroke, reconfirm that the injection quantity and the maximum variation between cylinders are as specified.
6. At delivery, again fix the flyweight using the lock pin.
----------
h=2.6+-0.01mm c=5deg15min+-30min
----------
----------
h=2.6+-0.01mm c=5deg15min+-30min
----------
Timing setting
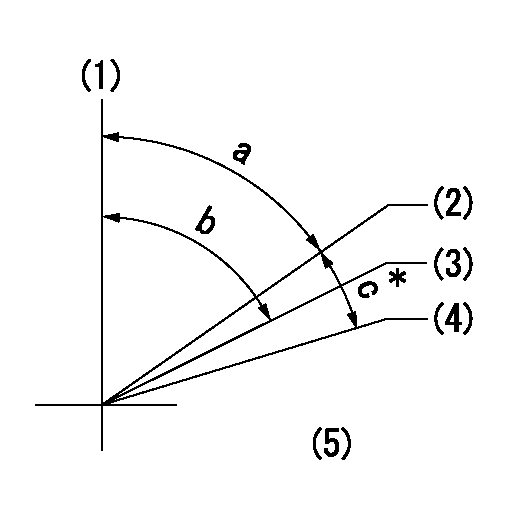
(1)Pump vertical direction
(2)Key groove position for No. 1 cylinder's cam lift h = cc (at BTDC aa).
(3)Key groove position for No. 1 cylinder's beginning of injection (at point A after injection quantity adjustment).
(4)Position of the key groove of the No. 1 cylinder at B.T.D.C. bb (fix the governor flyweight at this position for delivery).
(5)B.T.D.C.: aa
----------
aa=10.5deg bb=0deg cc=2.6+-0.01mm
----------
a=55deg18min+-3deg b=55deg18min+-3deg13min48sec c=5deg15min+-30min
----------
aa=10.5deg bb=0deg cc=2.6+-0.01mm
----------
a=55deg18min+-3deg b=55deg18min+-3deg13min48sec c=5deg15min+-30min
Information:
Start By:a. remove flywheelb. remove crankshaft rear seal and wear sleeve **Remove the crankshaft rear seal and wear sleeve only if the engine is equipped with the later design seal. The later design seal can be identified by the rotation marks on the seal.
Some flywheel housings will have more bolts holding the flywheel housing to the cylinder block.
1. If the engine is equipped with an electric starting motor, remove the electric starting motor from the flywheel housing.2. Remove the bolts that hold the oil pan plate to the flywheel housing. Loosen the bolts that hold the oil pan plate to the cylinder block.3. Install spacers between the oil pan plate and the cylinder block to hold the oil pan plate away from the flywheel housing.
3306 Engine Shown4. On 3306 Engines, remove turbocharger oil drain pipe (1).5. Install Tool (A) on the flywheel housing as shown, and fasten a hoist to it.6. Remove all bolts (2) and the flywheel housing from the engine. The weight of the flywheel housing is 37 kg (82 lb).Install Flywheel Housing
3306 Engine Shown1. Install Tool (A) on the flywheel housing. Fasten a hoist to the flywheel housing. 2. Put the gasket and flywheel housing in position on the engine. Install bolts (2) that hold it. Tighten the bolts to a torque of 100 14 N m (74 10 lb ft) as shown.3. Remove Tool (A) from the flywheel housing.4. On 3306 Engines, install turbocharger oil drain line (1).5. Cut the bottom of the flywheel housing gasket off even with the cylinder block and flywheel housing. Put 3S6252 RTV Silicone Adhesive/Sealant on the bottom of the gasket where it makes contact with the oil pan plate gasket.6. Remove the spacers from between the oil pan plate and the cylinder block. Install the bolts that hold the oil pan plate to the flywheel housing. Tighten the bolts that hold the oil pan plate to the cylinder block.7. If the engine is equipped with an electric starting motor, install it on the flywheel housing.End By:a. install crankshaft rear seal and wear sleeveb. install flywheel
Some flywheel housings will have more bolts holding the flywheel housing to the cylinder block.
1. If the engine is equipped with an electric starting motor, remove the electric starting motor from the flywheel housing.2. Remove the bolts that hold the oil pan plate to the flywheel housing. Loosen the bolts that hold the oil pan plate to the cylinder block.3. Install spacers between the oil pan plate and the cylinder block to hold the oil pan plate away from the flywheel housing.
3306 Engine Shown4. On 3306 Engines, remove turbocharger oil drain pipe (1).5. Install Tool (A) on the flywheel housing as shown, and fasten a hoist to it.6. Remove all bolts (2) and the flywheel housing from the engine. The weight of the flywheel housing is 37 kg (82 lb).Install Flywheel Housing
3306 Engine Shown1. Install Tool (A) on the flywheel housing. Fasten a hoist to the flywheel housing. 2. Put the gasket and flywheel housing in position on the engine. Install bolts (2) that hold it. Tighten the bolts to a torque of 100 14 N m (74 10 lb ft) as shown.3. Remove Tool (A) from the flywheel housing.4. On 3306 Engines, install turbocharger oil drain line (1).5. Cut the bottom of the flywheel housing gasket off even with the cylinder block and flywheel housing. Put 3S6252 RTV Silicone Adhesive/Sealant on the bottom of the gasket where it makes contact with the oil pan plate gasket.6. Remove the spacers from between the oil pan plate and the cylinder block. Install the bolts that hold the oil pan plate to the flywheel housing. Tighten the bolts that hold the oil pan plate to the cylinder block.7. If the engine is equipped with an electric starting motor, install it on the flywheel housing.End By:a. install crankshaft rear seal and wear sleeveb. install flywheel
Have questions with 101609-3810?
Group cross 101609-3810 ZEXEL
Komatsu
101609-3810
9 400 613 473
INJECTION-PUMP ASSEMBLY
SAA6D102
SAA6D102