Information injection-pump assembly
ZEXEL
101495-3412
1014953412
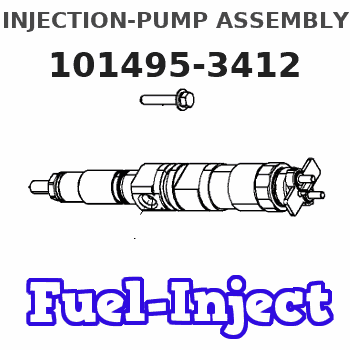
Rating:
Service parts 101495-3412 INJECTION-PUMP ASSEMBLY:
1.
_
5.
AUTOM. ADVANCE MECHANIS
6.
COUPLING PLATE
7.
COUPLING PLATE
8.
_
9.
_
11.
Nozzle and Holder
6204-11-3100
12.
Open Pre:MPa(Kqf/cm2)
19.6{200}
15.
NOZZLE SET
Include in #1:
101495-3412
as INJECTION-PUMP ASSEMBLY
Cross reference number
ZEXEL
101495-3412
1014953412
Zexel num
Bosch num
Firm num
Name
101495-3412
INJECTION-PUMP ASSEMBLY
4D95LE 14BC PE4A,5A, PE
4D95LE 14BC PE4A,5A, PE
Calibration Data:
Adjustment conditions
Test oil
1404 Test oil ISO4113 or {SAEJ967d}
1404 Test oil ISO4113 or {SAEJ967d}
Test oil temperature
degC
40
40
45
Nozzle and nozzle holder
105780-8140
Bosch type code
EF8511/9A
Nozzle
105780-0000
Bosch type code
DN12SD12T
Nozzle holder
105780-2080
Bosch type code
EF8511/9
Opening pressure
MPa
17.2
Opening pressure
kgf/cm2
175
Injection pipe
Outer diameter - inner diameter - length (mm) mm 6-2-600
Outer diameter - inner diameter - length (mm) mm 6-2-600
Tester oil delivery pressure
kPa
157
157
157
Tester oil delivery pressure
kgf/cm2
1.6
1.6
1.6
Direction of rotation (viewed from drive side)
Right R
Right R
Injection timing adjustment
Direction of rotation (viewed from drive side)
Right R
Right R
Injection order
1-2-4-3
Pre-stroke
mm
3.2
3.15
3.25
Beginning of injection position
Drive side NO.1
Drive side NO.1
Difference between angles 1
Cyl.1-2 deg. 90 89.5 90.5
Cyl.1-2 deg. 90 89.5 90.5
Difference between angles 2
Cal 1-4 deg. 180 179.5 180.5
Cal 1-4 deg. 180 179.5 180.5
Difference between angles 3
Cal 1-3 deg. 270 269.5 270.5
Cal 1-3 deg. 270 269.5 270.5
Injection quantity adjustment
Adjusting point
A
Rack position
10.2
Pump speed
r/min
1050
1050
1050
Average injection quantity
mm3/st.
56
55
57
Max. variation between cylinders
%
0
-2.5
2.5
Basic
*
Fixing the lever
*
Injection quantity adjustment_02
Adjusting point
-
Rack position
7.7+-0.5
Pump speed
r/min
565
565
565
Average injection quantity
mm3/st.
8
7
9
Max. variation between cylinders
%
0
-15
15
Fixing the rack
*
Remarks
Adjust only variation between cylinders; adjust governor according to governor specifications.
Adjust only variation between cylinders; adjust governor according to governor specifications.
Injection quantity adjustment_03
Adjusting point
D
Rack position
-
Pump speed
r/min
100
100
100
Average injection quantity
mm3/st.
60
55
65
Fixing the lever
*
Rack limit
*
Test data Ex:
Governor adjustment
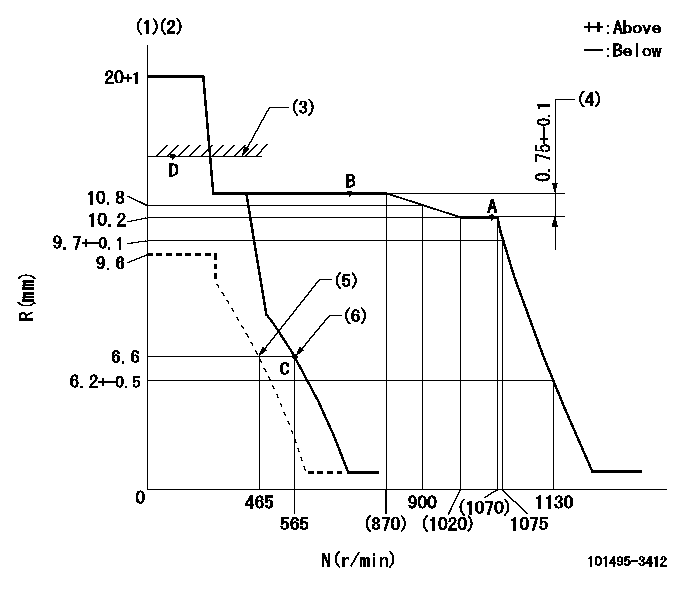
N:Pump speed
R:Rack position (mm)
(1)Target notch: K
(2)Tolerance for racks not indicated: +-0.05mm.
(3)RACK LIMIT
(4)Rack difference between N = N1 and N = N2
(5)Set idle sub-spring
(6)Main spring setting
----------
K=15 N1=1050r/min N2=750r/min
----------
----------
K=15 N1=1050r/min N2=750r/min
----------
Speed control lever angle
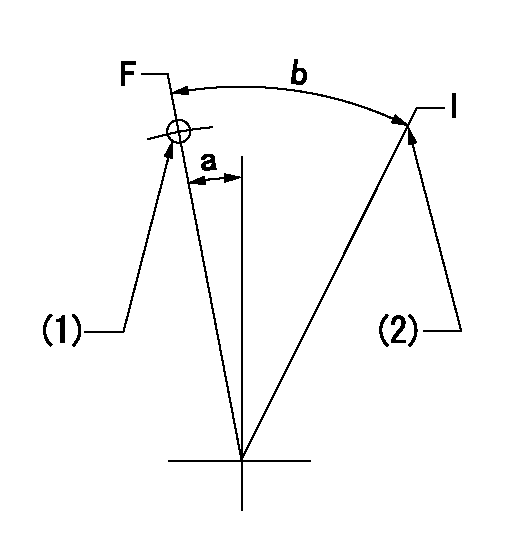
F:Full speed
I:Idle
(1)Use the hole at R = aa
(2)Stopper bolt setting
----------
aa=74mm
----------
a=6deg+-5deg b=24deg+-5deg
----------
aa=74mm
----------
a=6deg+-5deg b=24deg+-5deg
Stop lever angle
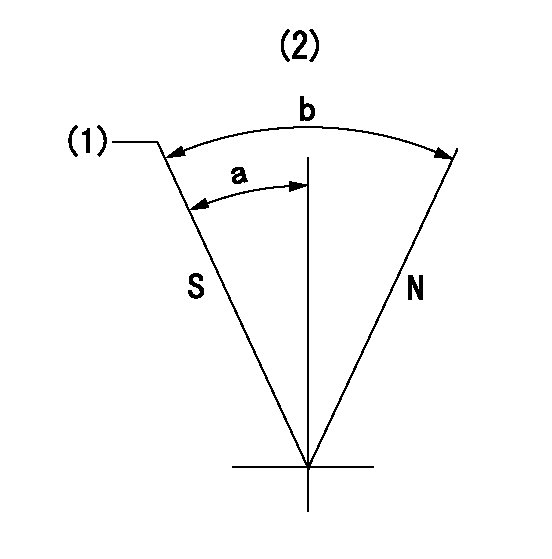
N:Pump normal
S:Stop the pump.
(1)Rack position = aa, speed = bb (stamp at delivery)
(2)No return spring
----------
aa=1-0.5mm bb=0r/min
----------
a=27.5deg+-5deg b=(55deg)
----------
aa=1-0.5mm bb=0r/min
----------
a=27.5deg+-5deg b=(55deg)
Timing setting
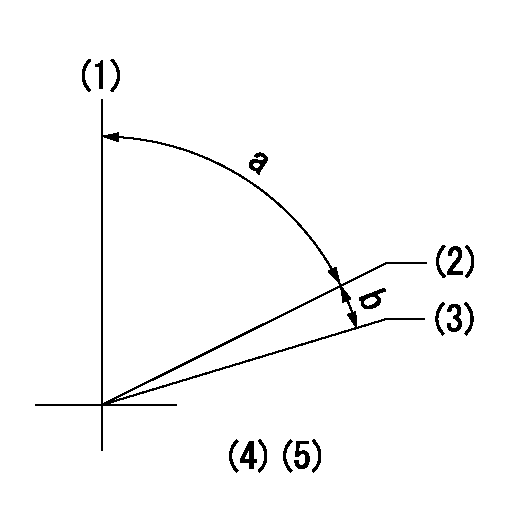
(1)Pump vertical direction
(2)Position of key groove at No 1 cylinder's beginning of injection
(3)Stamp aligning marks on the pump housing flange.
(4)B.T.D.C.: aa
(5)-
----------
aa=12deg
----------
a=58deg+-3deg b=2deg+-30min
----------
aa=12deg
----------
a=58deg+-3deg b=2deg+-30min
Information:
Cat does not warrant the quality or performance of non-Cat fluids.
Do NOT mix brands or types of SCA. Do NOT mix SCAs and extenders.Failure to follow the recommendations can result in shortened cooling system component life.
Use Only Approved SCAs. Conventional coolants require the maintenance addition of SCA throughout their expected life. Do NOT use an SCA with a coolant unless specifically approved by the coolant supplier for use with their coolant. It is the responsibility of the coolant manufacturer to ensure compatibility and acceptable performance.Failure to follow the recommendations can result in shortened cooling system component life.
Follow the maintenance information provided in the “Coolant and General Maintenance Recommendations” section in this Special Publication.Select a commercial diesel engine antifreeze coolant that meets all the requirements given in Table 1. The table contains the requirements for coolant to meet the published service intervals.The provided requirements are applicable to finished coolants and not for the concentrates. When concentrated coolant/antifreeze is mixed, Cat recommends mixing the concentrate with distilled water or with deionized water. If distilled water or deionized water is not available, water which has the required properties may be used. For the water properties, refer to this Special Publication, "General Coolant Information" article.Coolant/antifreezes for heavy-duty applications that meet "ASTM D6210" do not require treatment with SCA at the initial fill. Use the recommended 1:1 or higher concentration with recommended water. Treatment with SCA is required on a maintenance basis.The SCA manufacturer is responsible for ensuring the SCA is compatible with water meeting the “Caterpillar Minimum Acceptable Water Quality Requirements” as found in this Special Publication, and "ASTM D6210-08, Table X1.1". The coolant manufacturer and the SCA manufacturer are responsible to ensure that the products will not cause cooling system harm.Do not mix brands or types of coolants with different brands or types of SCA or extender.If using non Cat coolants, refer to the coolant manufacturer for information on a compatible SCA.Treat the compatible commercial coolant with 3 to 6 percent Cat SCA by volume. Maintain a 3 to 6 percent concentration level of SCA in the cooling system. For more information, refer to this Special Publication, "Conventional Coolant/Antifreeze Cooling System Maintenance" article.
Table 1
Technical Requirements for Commercial Diesel Engine Antifreeze Coolants
Specifications ASTM D6210-08
Additional Requirements Silicon: 100 ppm minimum to 275 ppm maximum
Nitrites: maintained at 1200ppm (70 grains/US gal) minimum to 2400 ppm (140 grains/US gal) maximum
Cat SCA at 3 to 6 percent (if Cat SCA is added)
Maintenance ASTM D6210-08 Add compatible SCA at maintenance intervals
Clean and flush the cooling system at drain intervals
Have questions with 101495-3412?
Group cross 101495-3412 ZEXEL
101495-3412
INJECTION-PUMP ASSEMBLY
4D95LE
4D95LE