Information injection-pump assembly
BOSCH
9 400 611 423
9400611423
ZEXEL
101492-3880
1014923880
KOMATSU
6205711243
6205711243
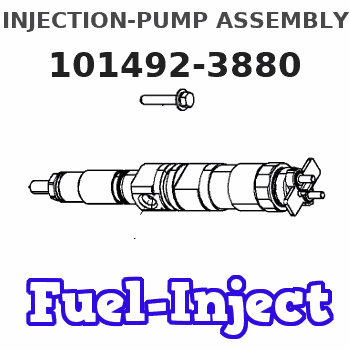
Rating:
Service parts 101492-3880 INJECTION-PUMP ASSEMBLY:
1.
_
5.
AUTOM. ADVANCE MECHANIS
6.
COUPLING PLATE
7.
COUPLING PLATE
8.
_
9.
_
11.
Nozzle and Holder
6202-13-3300
12.
Open Pre:MPa(Kqf/cm2)
22.1{225}
15.
NOZZLE SET
Cross reference number
BOSCH
9 400 611 423
9400611423
ZEXEL
101492-3880
1014923880
KOMATSU
6205711243
6205711243
Zexel num
Bosch num
Firm num
Name
101492-3880
9 400 611 423
6205711243 KOMATSU
INJECTION-PUMP ASSEMBLY
S4D95L K 14BC INJECTION PUMP ASSY PE4A,5A, PE
S4D95L K 14BC INJECTION PUMP ASSY PE4A,5A, PE
Calibration Data:
Adjustment conditions
Test oil
1404 Test oil ISO4113 or {SAEJ967d}
1404 Test oil ISO4113 or {SAEJ967d}
Test oil temperature
degC
40
40
45
Nozzle and nozzle holder
105780-8140
Bosch type code
EF8511/9A
Nozzle
105780-0000
Bosch type code
DN12SD12T
Nozzle holder
105780-2080
Bosch type code
EF8511/9
Opening pressure
MPa
17.2
Opening pressure
kgf/cm2
175
Injection pipe
Outer diameter - inner diameter - length (mm) mm 6-2-600
Outer diameter - inner diameter - length (mm) mm 6-2-600
Overflow valve
131424-7420
Overflow valve opening pressure
kPa
255
221
289
Overflow valve opening pressure
kgf/cm2
2.6
2.25
2.95
Tester oil delivery pressure
kPa
157
157
157
Tester oil delivery pressure
kgf/cm2
1.6
1.6
1.6
Direction of rotation (viewed from drive side)
Right R
Right R
Injection timing adjustment
Direction of rotation (viewed from drive side)
Right R
Right R
Injection order
1-2-4-3
Pre-stroke
mm
3.2
3.15
3.25
Beginning of injection position
Drive side NO.1
Drive side NO.1
Difference between angles 1
Cyl.1-2 deg. 90 89.5 90.5
Cyl.1-2 deg. 90 89.5 90.5
Difference between angles 2
Cal 1-4 deg. 180 179.5 180.5
Cal 1-4 deg. 180 179.5 180.5
Difference between angles 3
Cal 1-3 deg. 270 269.5 270.5
Cal 1-3 deg. 270 269.5 270.5
Injection quantity adjustment
Adjusting point
A
Rack position
10
Pump speed
r/min
1100
1100
1100
Average injection quantity
mm3/st.
73.5
72.5
74.5
Max. variation between cylinders
%
0
-2.5
2.5
Basic
*
Fixing the lever
*
Injection quantity adjustment_02
Adjusting point
-
Rack position
7.8+-0.5
Pump speed
r/min
450
450
450
Average injection quantity
mm3/st.
10.5
9.5
11.5
Max. variation between cylinders
%
0
-15
15
Fixing the rack
*
Remarks
Adjust only variation between cylinders; adjust governor according to governor specifications.
Adjust only variation between cylinders; adjust governor according to governor specifications.
Test data Ex:
Governor adjustment
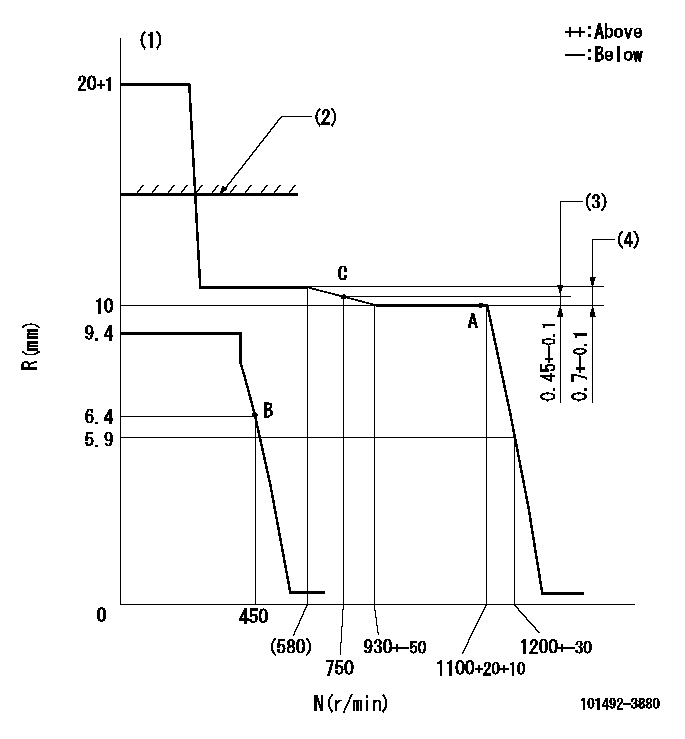
N:Pump speed
R:Rack position (mm)
(1)Target notch: K
(2)RACK LIMIT: RAL
(3)Rack difference from N = N1
(4)Rack difference between N = N2 and N = N3
----------
K=14 RAL=12.5+0.2mm N1=1100r/min N2=1100r/min N3=500r/min
----------
----------
K=14 RAL=12.5+0.2mm N1=1100r/min N2=1100r/min N3=500r/min
----------
Speed control lever angle
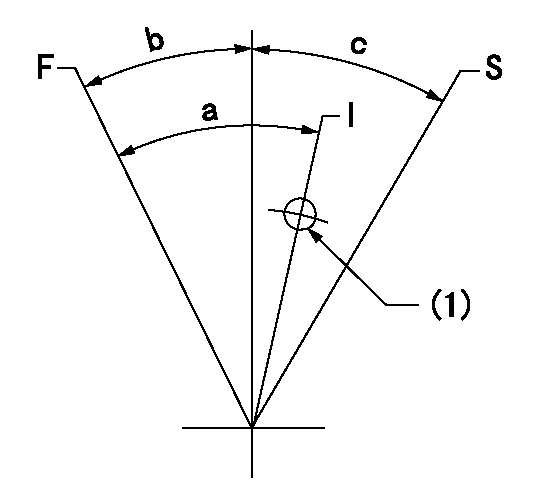
F:Full speed
I:Idle
S:Stop
(1)Use the hole at R = aa
----------
aa=80mm
----------
a=34deg+-5deg b=17deg+-3deg c=32deg+-3deg
----------
aa=80mm
----------
a=34deg+-5deg b=17deg+-3deg c=32deg+-3deg
Timing setting
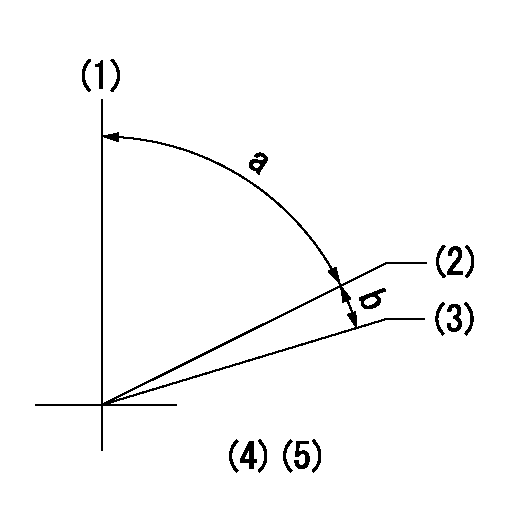
(1)Pump vertical direction
(2)Position of key groove at No 1 cylinder's beginning of injection
(3)Stamp aligning marks on the pump housing flange.
(4)-
(5)-
----------
----------
a=58deg+-3deg b=2deg+-30min
----------
----------
a=58deg+-3deg b=2deg+-30min
Information:
If there has been a previous repair, part age/hours will apply. Retain a copy of the previous repair invoice in the dealer's records for audit purposes, and specify repair date and machine hours in the "Additional Comments" section of the warranty claim.
PARTS DISPOSITION
****Parts Stock****
Handle the parts in accordance with your Warranty Bulletin on warranty parts handling.
****Affected Product****
Handle the parts in accordance with your Warranty Bulletin on warranty parts handling.
Rework Procedure
Note: Ensure that all safety information, warnings, and instructions are read and understood before any operation or any maintenance procedures are performed. Refer to the Operation and Maintenance Manual "Safety Section".
C175 Injector Sleeve Re-Seal Process:
This Rework Procedure outlines how to correctly remove, inspect, and install a C175 injector sleeve into a cylinder head, with a new process designed to stop coolant leaks caused by injector sleeve seal failure.
Parts and Materials Needed:
8T-2223 Quill Tube Bolts/Cylinder - Qty 4
8T-0106 injector Hold Down Bolt/Cylinder - Qty 1
298-5347 Injector Sleeve/Cylinder - Qty 1
247-1074 Injector Sleeve O-Rings/Cylinder - Qty 2
8C-3132 Injector Tip O-Ring/Cylinder - Qty 1
339-9352 Injector System Cap Kit/Engine - Qty 1
- Battery powered screwdriver/impact
- Soft bristled brush (nylon or other non-metallic material), Cat part number 6V-7096 is an example. Refer to Image1.2.1.
- Injector sleeve torque tool (333-0759, or new tool provided by Lafayette)
- Vacuum attachment, for removing debris from inside cylinder
- Deep well socket, inverted
- Wrap a lint free shop towel around the socket, secure to the socket with an O-ring
- Brake clean or similar solvent
- Torque wrench capable of reaching 200 N.m
- Anti-seize (C5-A Loctite 51007)
- Clean engine oil
Image1.2.1
Removal of Valve Covers:
1. Remove four quill tube bolts and slide quill out of head. Refer to Image1.3.1.
2. Place quill tube into sealed plastic bag.
3. Place plugs into the quill tube hole and over fuel limiter in the fuel rail.
4. Remove the injectors.
5. Place injectors in plastic bag.
Image1.3.1
Removal of the Injector Sleeves:
1. Remove the injector sleeves. Refer to Image 1.4.1.
2. Vacuum out any loose debris.
3. Clean remaining Loctite debris from the injector sleeve seat using brake-clean or a similar solvent, a nylon bristled brush (Cat part number 6V-7096), and an inverted socket with a lint free rag or towel wrapped around it).
4. Use an O-ring to keep the rag around the socket.
5. Clean the threads in the head with the soft bristled brush. Refer to Image1.4.2.
6. Clean the seat surface with the inverted socket and a new rag until the rag no longer picks up debris or dirt from the seat. Refer to Image1.4.3 and 1.4.4.
Image1.4.1
Image1.4.2
Image1.4.3
Image1.4.4
Inspection of the Injector Sleeve Seat:
1. The seat and threads must be free of any debris.
2. The seat must not have any visible guttering around the surface.
3. There should be a continuous shiny band
Have questions with 101492-3880?
Group cross 101492-3880 ZEXEL
Komatsu
101492-3880
9 400 611 423
6205711243
INJECTION-PUMP ASSEMBLY
S4D95L
S4D95L