Information injection-pump assembly
BOSCH
F 019 Z10 945
f019z10945
ZEXEL
101405-3271
1014053271
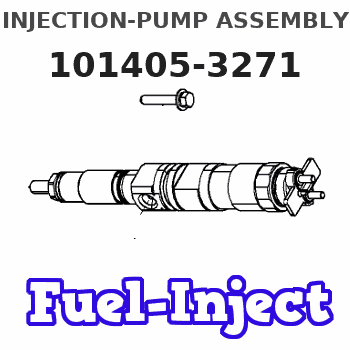
Rating:
Service parts 101405-3271 INJECTION-PUMP ASSEMBLY:
1.
_
5.
AUTOM. ADVANCE MECHANIS
6.
COUPLING PLATE
7.
COUPLING PLATE
8.
_
9.
_
11.
Nozzle and Holder
4063269
12.
Open Pre:MPa(Kqf/cm2)
22.0{224}
15.
NOZZLE SET
Cross reference number
BOSCH
F 019 Z10 945
f019z10945
ZEXEL
101405-3271
1014053271
Zexel num
Bosch num
Firm num
Name
101405-3271
F 019 Z10 945
INJECTION-PUMP ASSEMBLY
14BC INJECTION PUMP ASSY PE4A,5A, PE
14BC INJECTION PUMP ASSY PE4A,5A, PE
101405-3271
F 019 Z10 945
4063535 KOMATSU
INJECTION-PUMP ASSEMBLY
K 14BC INJECTION PUMP ASSY PE4A,5A, PE
K 14BC INJECTION PUMP ASSY PE4A,5A, PE
101405-3271
F 019 Z10 945
6737711130 KOMATSU
INJECTION-PUMP ASSEMBLY
K 14BC INJECTION PUMP ASSY PE4A,5A, PE
K 14BC INJECTION PUMP ASSY PE4A,5A, PE
Calibration Data:
Adjustment conditions
Test oil
1404 Test oil ISO4113 or {SAEJ967d}
1404 Test oil ISO4113 or {SAEJ967d}
Test oil temperature
degC
40
40
45
Nozzle and nozzle holder
105780-8140
Bosch type code
EF8511/9A
Nozzle
105780-0000
Bosch type code
DN12SD12T
Nozzle holder
105780-2080
Bosch type code
EF8511/9
Opening pressure
MPa
17.2
Opening pressure
kgf/cm2
175
Injection pipe
Outer diameter - inner diameter - length (mm) mm 6-2-600
Outer diameter - inner diameter - length (mm) mm 6-2-600
Overflow valve
131424-3420
Overflow valve opening pressure
kPa
255
221
289
Overflow valve opening pressure
kgf/cm2
2.6
2.25
2.95
Tester oil delivery pressure
kPa
255
255
255
Tester oil delivery pressure
kgf/cm2
2.6
2.6
2.6
Direction of rotation (viewed from drive side)
Right R
Right R
Injection timing adjustment
Direction of rotation (viewed from drive side)
Right R
Right R
Injection order
1-3-4-2
Pre-stroke
mm
2.5
2.45
2.55
Rack position
Point A R=A
Point A R=A
Beginning of injection position
Drive side NO.1
Drive side NO.1
Difference between angles 1
Cal 1-3 deg. 90 89.5 90.5
Cal 1-3 deg. 90 89.5 90.5
Difference between angles 2
Cal 1-4 deg. 180 179.5 180.5
Cal 1-4 deg. 180 179.5 180.5
Difference between angles 3
Cyl.1-2 deg. 270 269.5 270.5
Cyl.1-2 deg. 270 269.5 270.5
Injection quantity adjustment
Adjusting point
A
Rack position
9.7
Pump speed
r/min
1000
1000
1000
Average injection quantity
mm3/st.
93
92
94
Max. variation between cylinders
%
0
-2.5
2.5
Basic
*
Fixing the lever
*
Boost pressure
kPa
53.3
53.3
Boost pressure
mmHg
400
400
Hydraulic cylinder ON
*
Injection quantity adjustment_02
Adjusting point
-
Rack position
7.2+-0.5
Pump speed
r/min
420
420
420
Average injection quantity
mm3/st.
10
9
11
Max. variation between cylinders
%
0
-15
15
Fixing the rack
*
Boost pressure
kPa
0
0
0
Boost pressure
mmHg
0
0
0
Hydraulic cylinder ON
*
Remarks
Adjust only variation between cylinders; adjust governor according to governor specifications.
Adjust only variation between cylinders; adjust governor according to governor specifications.
Boost compensator adjustment
Pump speed
r/min
650
650
650
Rack position
8.75
Boost pressure
kPa
14.7
12
17.4
Boost pressure
mmHg
110
90
130
Boost compensator adjustment_02
Pump speed
r/min
650
650
650
Rack position
10.35
Boost pressure
kPa
40
40
40
Boost pressure
mmHg
300
300
300
Test data Ex:
Governor adjustment
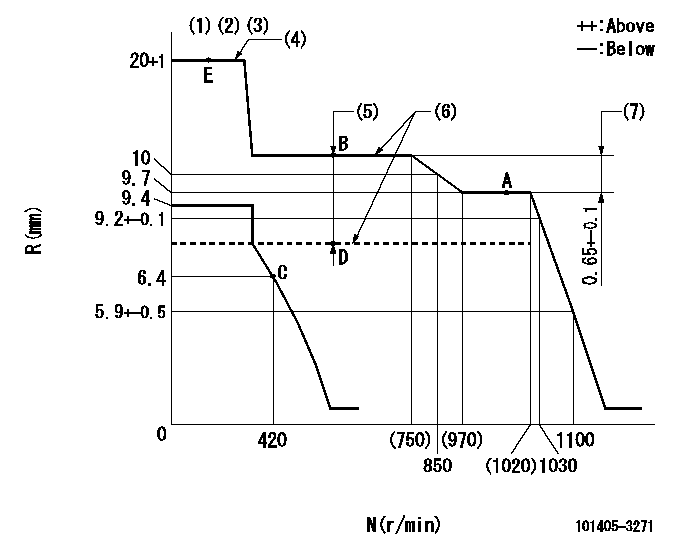
N:Pump speed
R:Rack position (mm)
(1)Target notch: K
(2)Tolerance for racks not indicated: +-0.05mm.
(3)Adjust the secondary timing before adjusting the governor.
(4)When the hydraulic cylinder is OFF
(5)Boost compensator stroke: BCL
(6)When hydraulic cylinder ON: P1
(7)Rack difference between N = N1 and N = N2
----------
K=18 BCL=1.6+-0.1mm P1=127+-10kPa{1.3+-0.1kgf/cm2} N1=1000r/min N2=650r/min
----------
----------
K=18 BCL=1.6+-0.1mm P1=127+-10kPa{1.3+-0.1kgf/cm2} N1=1000r/min N2=650r/min
----------
Speed control lever angle

F:Full speed
I:Idle
(1)Use the hole at R = aa
(2)Stopper bolt setting
----------
aa=60mm
----------
a=16deg+-5deg b=30deg+-5deg
----------
aa=60mm
----------
a=16deg+-5deg b=30deg+-5deg
Stop lever angle

N:Pump normal
S:Stop the pump.
(1)No return spring
----------
----------
a=0deg+-5deg b=53deg+-5deg
----------
----------
a=0deg+-5deg b=53deg+-5deg
0000001501 TAMPER PROOF
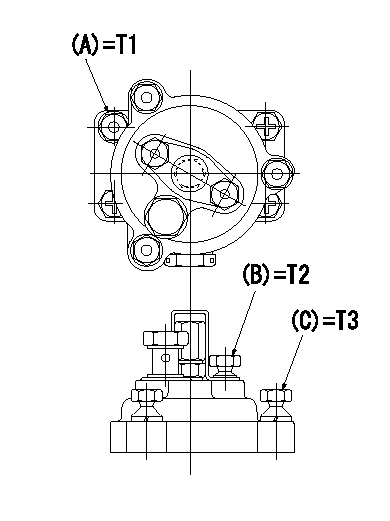
Tamperproofing-equipped boost compensator cover installation procedure
(1)After adjusting the governor and the boost compensator, tighten to the specified torque to break off the bolt heads.
(Tightening torque T = T1 maximum)
(2)After adjusting the governor and the boost compensator, tighten to the specified torque to break off the bolt heads.
(Tightening torque T = T2)
(3)After adjusting the governor and the boost compensator, tighten to the specified torque to break off the bolt heads.
(Tightening torque T = T3)
----------
T1=7.16~9.12N-m(0.73~0.93kgf-m) T2=2.9~4.4N-m(0.3~0.45kgf-m) T3=2.9~4.4N-m(0.3~0.45kgf-m)
----------
----------
T1=7.16~9.12N-m(0.73~0.93kgf-m) T2=2.9~4.4N-m(0.3~0.45kgf-m) T3=2.9~4.4N-m(0.3~0.45kgf-m)
----------
Timing setting

(1)Pump vertical direction
(2)Key groove position at No. 1 cylinder's beginning of injection position (at BTDC: aa).
(3)Position of the key groove of the No. 1 cylinder at B.T.D.C. bb (fix the governor flyweight at this position for delivery).
(4)B.T.D.C.: aa
(5)At second timing adjustment, set the camshaft at the * position and tighten the flyweight locknut.
(6)Align the flyweight's timing gear position with the lockpin groove and then fully tighten the flyweight to the camshaft.
(7)Remove the lock pin and adjust the governor. Reinstall the lock pin to fix the flyweight for delivery.
----------
aa=12deg bb=0deg
----------
a=54deg54min+-3deg b=6deg+-30min
----------
aa=12deg bb=0deg
----------
a=54deg54min+-3deg b=6deg+-30min
Information:
Your engine may not have the same or all of the gauges as shown in the illustrations. The illustrations shown are of typical gauges.Gauges provide a "look" inside the engine. Be sure they are in good working order. You can determine what is the "normal" operating range by observing your gauges over a period of time.Noticeable changes in gauge readings are an indication of potential gauge or engine problems. This also applies to gauge readings that have changed significantly but are still within specifications. The cause of any sudden or significant change in the readings should be determined and corrected. Contact your Caterpillar dealer for assistance as needed. Oil Pressure - Indicates engine oil pressure. Normal oil pressure should read 275 to 606 kPa (40 to 88 psi) when the engine is running at rated engine rpm, with SAE 10W30 oil, at 110°C (230°F) operating oil temperature.If the gauge reading fluctuates after the load is stable:1. Remove the load.2. Reduce engine speed to low idle.The DIAGNOSTIC lamp will come on and a fault logged in the ECM system if oil pressure drops below 69 kPa (10 psi) at low idle rpm. If no pressure is indicated, stop the engine. Jacket Water Temperature - Indicates engine coolant temperature. The gauge should normally indicate between 87 and 98°C (189 and 208°F). Somewhat higher temperatures may occur under certain conditions. Maximum allowable operating temperature is 104°C (220°F) with the cooling system pressurized. If the engine is operating above this range and steam becomes apparent:1. Reduce the load and engine rpm.2. Inspect for coolant leaks.3. Determine if the engine must be shutdown immediately; or if the engine can be cooled by reducing the load.A DIAGNOSTIC lamp will come on and a fault logged in the ECM if jacket water temperature is above 104°C (220°F). Fuel Pressure - Indicates fuel pressure to the injection pump. The indicator should register in the NORMAL (green) range. Normal fuel pressure at LOW IDLE is 205 35 kPa (30 5 psi). Normal fuel pressure at Top Engine Limit (TEL) or rated rpm is 240 kPa (35 psi).If the indicator moves to the OUT position or registers below 160 kPa (23 psi) when equipped with a numerical gauge, the engine will not operate properly. A drop in fuel pressure usually indicates a dirty or plugged fuel filter. Tachometer - Indicates engine rpm. The engine can be operated at top engine limit (2300 rpm max) without damage, but should never be allowed to exceed 2450 rpm. Overspeeding can result in serious damage to your engine.
To prevent engine damage, never exceed 2450 rpm.
Service Hour Meter - Indicates the total number of clock hours the engine has operated if used. ECM Hours are also available via ECAP.
To prevent engine damage, never exceed 2450 rpm.
Service Hour Meter - Indicates the total number of clock hours the engine has operated if used. ECM Hours are also available via ECAP.
Have questions with 101405-3271?
Group cross 101405-3271 ZEXEL
101405-3271
F 019 Z10 945
INJECTION-PUMP ASSEMBLY
Komatsu
101405-3271
F 019 Z10 945
4063535
INJECTION-PUMP ASSEMBLY
101405-3271
F 019 Z10 945
6737711130
INJECTION-PUMP ASSEMBLY