Information injection-pump assembly
BOSCH
9 400 611 977
9400611977
ZEXEL
101405-3160
1014053160
KOMATSU
3863892
3863892
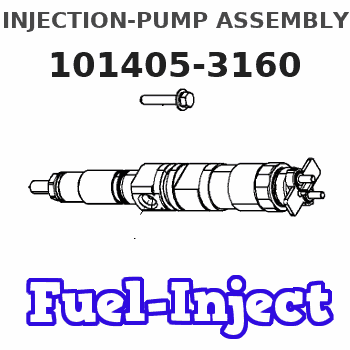
Rating:
Service parts 101405-3160 INJECTION-PUMP ASSEMBLY:
1.
_
5.
AUTOM. ADVANCE MECHANIS
6.
COUPLING PLATE
7.
COUPLING PLATE
8.
_
9.
_
10.
NOZZLE AND HOLDER ASSY
11.
Nozzle and Holder
12.
Open Pre:MPa(Kqf/cm2)
21.6{220}
13.
NOZZLE-HOLDER
14.
NOZZLE
15.
NOZZLE SET
Cross reference number
BOSCH
9 400 611 977
9400611977
ZEXEL
101405-3160
1014053160
KOMATSU
3863892
3863892
Zexel num
Bosch num
Firm num
Name
101405-3160
9 400 611 977
3863892 KOMATSU
INJECTION-PUMP ASSEMBLY
S4D102E K 14BC INJECTION PUMP ASSY PE4A,5A, PE
S4D102E K 14BC INJECTION PUMP ASSY PE4A,5A, PE
101405-3160
9 400 611 977
6732711361 KOMATSU
INJECTION-PUMP ASSEMBLY
S4D102E K 14BC INJECTION PUMP ASSY PE4A,5A, PE
S4D102E K 14BC INJECTION PUMP ASSY PE4A,5A, PE
Calibration Data:
Adjustment conditions
Test oil
1404 Test oil ISO4113 or {SAEJ967d}
1404 Test oil ISO4113 or {SAEJ967d}
Test oil temperature
degC
40
40
45
Nozzle and nozzle holder
105780-8140
Bosch type code
EF8511/9A
Nozzle
105780-0000
Bosch type code
DN12SD12T
Nozzle holder
105780-2080
Bosch type code
EF8511/9
Opening pressure
MPa
17.2
Opening pressure
kgf/cm2
175
Injection pipe
Outer diameter - inner diameter - length (mm) mm 6-2-600
Outer diameter - inner diameter - length (mm) mm 6-2-600
Overflow valve
131424-3420
Overflow valve opening pressure
kPa
255
221
289
Overflow valve opening pressure
kgf/cm2
2.6
2.25
2.95
Tester oil delivery pressure
kPa
157
157
157
Tester oil delivery pressure
kgf/cm2
1.6
1.6
1.6
Direction of rotation (viewed from drive side)
Right R
Right R
Injection timing adjustment
Direction of rotation (viewed from drive side)
Right R
Right R
Injection order
1-3-4-2
Pre-stroke
mm
2.5
2.45
2.55
Beginning of injection position
Drive side NO.1
Drive side NO.1
Difference between angles 1
Cal 1-3 deg. 90 89.5 90.5
Cal 1-3 deg. 90 89.5 90.5
Difference between angles 2
Cal 1-4 deg. 180 179.5 180.5
Cal 1-4 deg. 180 179.5 180.5
Difference between angles 3
Cyl.1-2 deg. 270 269.5 270.5
Cyl.1-2 deg. 270 269.5 270.5
Injection quantity adjustment
Adjusting point
A
Rack position
9.7
Pump speed
r/min
1100
1100
1100
Average injection quantity
mm3/st.
93.5
92.5
94.5
Max. variation between cylinders
%
0
-2.5
2.5
Basic
*
Fixing the lever
*
Injection quantity adjustment_02
Adjusting point
-
Rack position
6.8+-0.5
Pump speed
r/min
480
480
480
Average injection quantity
mm3/st.
11.5
10.5
12.5
Max. variation between cylinders
%
0
-15
15
Fixing the rack
*
Remarks
Adjust only variation between cylinders; adjust governor according to governor specifications.
Adjust only variation between cylinders; adjust governor according to governor specifications.
Injection quantity adjustment_03
Adjusting point
D
Rack position
-
Pump speed
r/min
100
100
100
Average injection quantity
mm3/st.
85
85
95
Fixing the lever
*
Rack limit
*
Test data Ex:
Governor adjustment
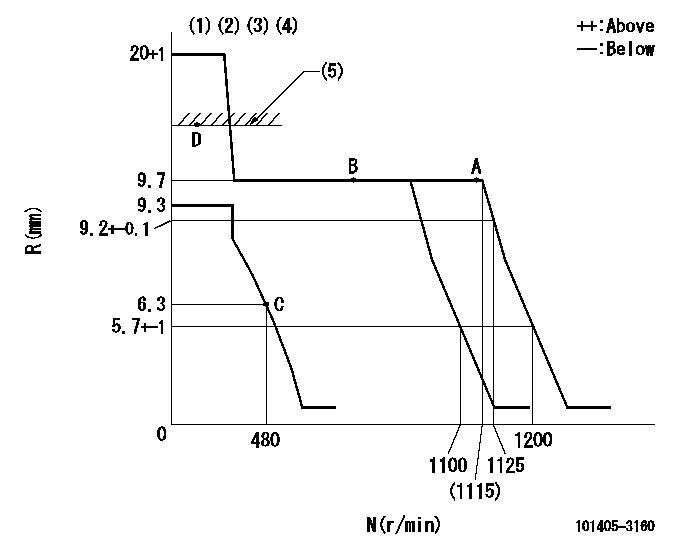
N:Pump speed
R:Rack position (mm)
(1)Target notch: K
(2)Tolerance for racks not indicated: +-0.05mm.
(3)Deliver without the torque control spring operating.
(4)Adjust the secondary timing before adjusting the governor.
(5)RACK LIMIT
----------
K=15
----------
----------
K=15
----------
Speed control lever angle
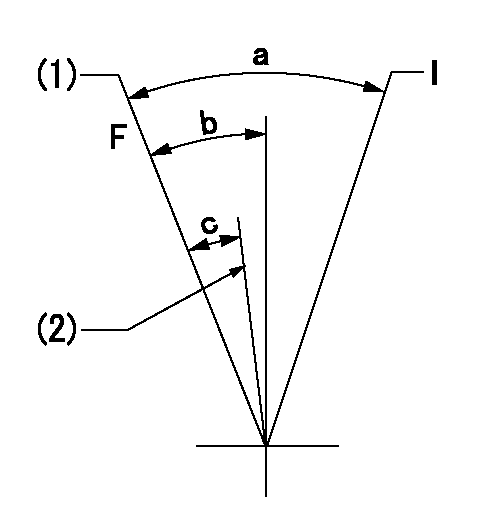
F:Full speed
I:Idle
(1)Set the speed at aa (active mode)
(2)Set the speed at bb (normal mode)
----------
aa=1125r/min bb=1100r/min
----------
a=34deg+-5deg b=19deg+-5deg c=5deg+-5deg
----------
aa=1125r/min bb=1100r/min
----------
a=34deg+-5deg b=19deg+-5deg c=5deg+-5deg
Stop lever angle

N:Pump normal
S:Stop the pump.
(1)No return spring
----------
----------
a=0deg+-5deg b=53deg+-5deg
----------
----------
a=0deg+-5deg b=53deg+-5deg
Timing setting

(1)Pump vertical direction
(2)Key groove position at No. 1 cylinder's beginning of injection position (at BTDC: aa).
(3)Position of the key groove of the No. 1 cylinder at B.T.D.C. bb (fix the governor flyweight at this position for delivery).
(4)B.T.D.C.: aa
(5)At second timing adjustment, set the camshaft at the * position and tighten the flyweight locknut.
(6)Align the flyweight's timing gear position with the lockpin groove and then fully tighten the flyweight to the camshaft.
(7)Remove the lock pin and adjust the governor. Reinstall the lock pin to fix the flyweight for delivery.
----------
aa=15deg bb=0deg
----------
a=54deg54min+-3deg b=7deg30min+-30min
----------
aa=15deg bb=0deg
----------
a=54deg54min+-3deg b=7deg30min+-30min
Information:
All PM Level 3 maintenance is to be performed at the intervals specified in the Maintenance Management Schedule.Before proceeding with PM Level 3 maintenance, perform all PM Level 2, PM Level 1 and Daily maintenance requirements. You must read and understand the warnings and instructions contained in the Safety section of this manual before performing any operation or maintenance procedures.Air Compressor
Rebuild or Exchange
Visually check for fluid leaks.Our recommendation to maintain your air compressor before it fails will be less costly than repairing the air compressor after failure.If the engine is operated until the air compressor fails, additional damage to the engine could result. For example: A failed air compressor could contaminate the engine oil with particles of materials since engine oil also lubricates the air compressor. The circulation of these engine oil with particles of materials since engine oil also lubricates the air compressor. The circulation of these contaminates through the engine lubricating system could damage the engine's main and connecting rod bearings.Maintenance Options
Repair Kits - These useful kits can be obtained from your Caterpillar dealer. These kits include all the necessary parts, special tools and instructions to repair your air compressor in either your own maintenance shop or at your servicing dealer's facility. Repair kits simplify parts ordering, help speed repairs and reduce parts cost. Exchange - This is a cost cutting service that permits exchanging a worn air compressor for a dealer or OEM factory rebuilt air compressor on an over-the-counter basis. They are available when needed at a substantial savings in both time and money. New - Replace with a new air compressor.Caterpillar Recommendation
The most cost effective repair option is to rebuild the air compressor with a repair kit that can be obtained from your Caterpillar dealer.Refer to the Service Manual for your engine to remove and install the air compressor.Turbocharger
Rebuild or Exchange
The cost incurred to maintain your turbocharger before failure as recommended could be significantly less than if you wait until your turbocharger fails.By maintaining your turbocharger before failure, you will minimize unscheduled downtime and reduce the chances for potential damage to other engine parts. When you reduce the risk of unscheduled downtime and costly repairs, you conserve cash that can be budgeted for use more profitably elsewhere.If you choose to operate your engine until the turbocharger fails, your repair costs could be as much as twenty-five times or more compared to the repair before failure cost. This excessive cost is due to additional engine damage that could have been prevented.If the engine is operated until the turbocharger fails, severe damage to the turbocharger's compressor wheel and/or engine could result.For example: severe damage to the turbocharger compressor wheel could cause parts from the compressor wheel to enter the engine cylinder that could result in cracks in the cylinder head and cause additional damage to the piston, a piston seizure orother potential damage to valves and cylinder head.Our recommended maintenance intervals for performing preventive maintenance on your turbocharger are based on experience and gathered
Rebuild or Exchange
Visually check for fluid leaks.Our recommendation to maintain your air compressor before it fails will be less costly than repairing the air compressor after failure.If the engine is operated until the air compressor fails, additional damage to the engine could result. For example: A failed air compressor could contaminate the engine oil with particles of materials since engine oil also lubricates the air compressor. The circulation of these engine oil with particles of materials since engine oil also lubricates the air compressor. The circulation of these contaminates through the engine lubricating system could damage the engine's main and connecting rod bearings.Maintenance Options
Repair Kits - These useful kits can be obtained from your Caterpillar dealer. These kits include all the necessary parts, special tools and instructions to repair your air compressor in either your own maintenance shop or at your servicing dealer's facility. Repair kits simplify parts ordering, help speed repairs and reduce parts cost. Exchange - This is a cost cutting service that permits exchanging a worn air compressor for a dealer or OEM factory rebuilt air compressor on an over-the-counter basis. They are available when needed at a substantial savings in both time and money. New - Replace with a new air compressor.Caterpillar Recommendation
The most cost effective repair option is to rebuild the air compressor with a repair kit that can be obtained from your Caterpillar dealer.Refer to the Service Manual for your engine to remove and install the air compressor.Turbocharger
Rebuild or Exchange
The cost incurred to maintain your turbocharger before failure as recommended could be significantly less than if you wait until your turbocharger fails.By maintaining your turbocharger before failure, you will minimize unscheduled downtime and reduce the chances for potential damage to other engine parts. When you reduce the risk of unscheduled downtime and costly repairs, you conserve cash that can be budgeted for use more profitably elsewhere.If you choose to operate your engine until the turbocharger fails, your repair costs could be as much as twenty-five times or more compared to the repair before failure cost. This excessive cost is due to additional engine damage that could have been prevented.If the engine is operated until the turbocharger fails, severe damage to the turbocharger's compressor wheel and/or engine could result.For example: severe damage to the turbocharger compressor wheel could cause parts from the compressor wheel to enter the engine cylinder that could result in cracks in the cylinder head and cause additional damage to the piston, a piston seizure orother potential damage to valves and cylinder head.Our recommended maintenance intervals for performing preventive maintenance on your turbocharger are based on experience and gathered
Have questions with 101405-3160?
Group cross 101405-3160 ZEXEL
Komatsu
Komatsu
101405-3160
9 400 611 977
3863892
INJECTION-PUMP ASSEMBLY
S4D102E
S4D102E
101405-3160
9 400 611 977
6732711361
INJECTION-PUMP ASSEMBLY
S4D102E
S4D102E