Information injection-pump assembly
BOSCH
9 400 614 055
9400614055
ZEXEL
101405-3141
1014053141
KOMATSU
3863880
3863880
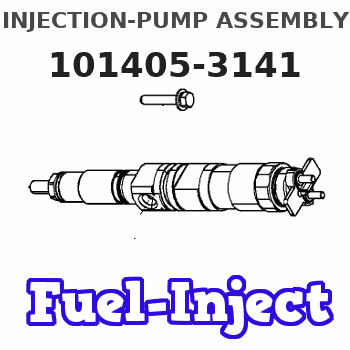
Rating:
Service parts 101405-3141 INJECTION-PUMP ASSEMBLY:
1.
_
5.
AUTOM. ADVANCE MECHANIS
6.
COUPLING PLATE
7.
COUPLING PLATE
8.
_
9.
_
10.
NOZZLE AND HOLDER ASSY
11.
Nozzle and Holder
12.
Open Pre:MPa(Kqf/cm2)
21.6{220}
13.
NOZZLE-HOLDER
14.
NOZZLE
15.
NOZZLE SET
Cross reference number
BOSCH
9 400 614 055
9400614055
ZEXEL
101405-3141
1014053141
KOMATSU
3863880
3863880
Zexel num
Bosch num
Firm num
Name
Calibration Data:
Adjustment conditions
Test oil
1404 Test oil ISO4113 or {SAEJ967d}
1404 Test oil ISO4113 or {SAEJ967d}
Test oil temperature
degC
40
40
45
Nozzle and nozzle holder
105780-8140
Bosch type code
EF8511/9A
Nozzle
105780-0000
Bosch type code
DN12SD12T
Nozzle holder
105780-2080
Bosch type code
EF8511/9
Opening pressure
MPa
17.2
Opening pressure
kgf/cm2
175
Injection pipe
Outer diameter - inner diameter - length (mm) mm 6-2-600
Outer diameter - inner diameter - length (mm) mm 6-2-600
Overflow valve
131424-3420
Overflow valve opening pressure
kPa
255
221
289
Overflow valve opening pressure
kgf/cm2
2.6
2.25
2.95
Tester oil delivery pressure
kPa
157
157
157
Tester oil delivery pressure
kgf/cm2
1.6
1.6
1.6
Direction of rotation (viewed from drive side)
Right R
Right R
Injection timing adjustment
Direction of rotation (viewed from drive side)
Right R
Right R
Injection order
1-3-4-2
Pre-stroke
mm
2.5
2.45
2.55
Beginning of injection position
Drive side NO.1
Drive side NO.1
Difference between angles 1
Cal 1-3 deg. 90 89.5 90.5
Cal 1-3 deg. 90 89.5 90.5
Difference between angles 2
Cal 1-4 deg. 180 179.5 180.5
Cal 1-4 deg. 180 179.5 180.5
Difference between angles 3
Cyl.1-2 deg. 270 269.5 270.5
Cyl.1-2 deg. 270 269.5 270.5
Injection quantity adjustment
Adjusting point
A
Rack position
9.7
Pump speed
r/min
1100
1100
1100
Average injection quantity
mm3/st.
93.5
92.5
94.5
Max. variation between cylinders
%
0
-2.5
2.5
Basic
*
Fixing the lever
*
Injection quantity adjustment_02
Adjusting point
-
Rack position
7+-0.5
Pump speed
r/min
465
465
465
Average injection quantity
mm3/st.
11.5
10.5
12.5
Max. variation between cylinders
%
0
-15
15
Fixing the rack
*
Remarks
Adjust only variation between cylinders; adjust governor according to governor specifications.
Adjust only variation between cylinders; adjust governor according to governor specifications.
Injection quantity adjustment_03
Adjusting point
D
Rack position
-
Pump speed
r/min
100
100
100
Average injection quantity
mm3/st.
85
85
95
Fixing the lever
*
Rack limit
*
Test data Ex:
Governor adjustment
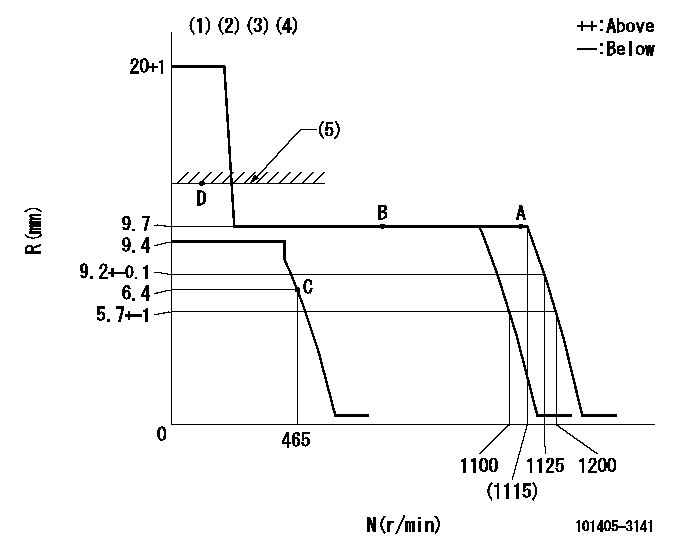
N:Pump speed
R:Rack position (mm)
(1)Target notch: K
(2)Tolerance for racks not indicated: +-0.05mm.
(3)The torque control spring does not operate.
(4)Adjust the secondary timing before adjusting the governor.
(5)RACK LIMIT
----------
K=15
----------
----------
K=15
----------
Speed control lever angle
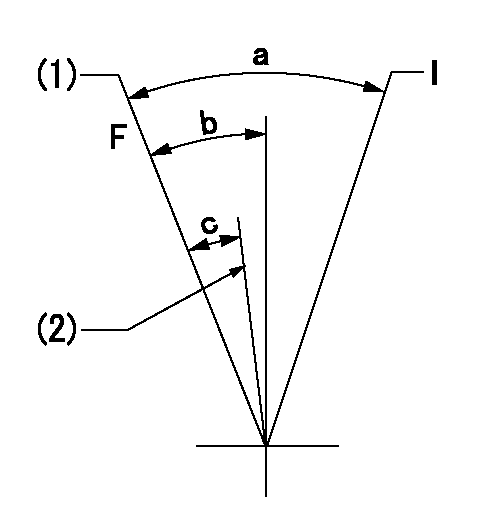
F:Full speed
I:Idle
(1)Speed = aa (active mode)
(2)Speed = bb (normal mode)
----------
aa=1125r/min bb=1100r/min
----------
a=35deg+-5deg b=18deg+-5deg c=5deg+-5deg
----------
aa=1125r/min bb=1100r/min
----------
a=35deg+-5deg b=18deg+-5deg c=5deg+-5deg
Stop lever angle

N:Pump normal
S:Stop the pump.
(1)No return spring
----------
----------
a=0deg+-5deg b=53deg+-5deg
----------
----------
a=0deg+-5deg b=53deg+-5deg
Timing setting

(1)Pump vertical direction
(2)Key groove position at No. 1 cylinder's beginning of injection position (at BTDC: aa).
(3)Position of the key groove of the No. 1 cylinder at B.T.D.C. bb (fix the governor flyweight at this position for delivery).
(4)B.T.D.C.: aa
(5)At second timing adjustment, set the camshaft at the * position and tighten the flyweight locknut.
(6)Align the flyweight's timing gear position with the lockpin groove and then fully tighten the flyweight to the camshaft.
(7)Remove the lock pin and adjust the governor. Reinstall the lock pin to fix the flyweight for delivery.
----------
aa=15deg bb=0deg
----------
a=54deg54min+-3deg b=7deg+-30min+-30min
----------
aa=15deg bb=0deg
----------
a=54deg54min+-3deg b=7deg+-30min+-30min
Information:
Crankcase Breather
Clean
1. Loosen hose clamp (1) and remove the hose from the cover.2. Loosen three breather cover bolts (2) and remove cover (3). 3. Remove breather element (4), and wash in clean, nonflammable solvent and allow to dry. 4. Install clean, dry breather element (4).5. Install cover (3) and bolts (2).5. Install hose and clamp (1). Tighten clamp (1), refer to topic "Torque Specifications" for the proper torque of hose clamp-worm drive band type. If the crankcase breather is not maintained on a regular basis, it will become plugged. A plugged crankcase breather would result in excessive crankcase pressure that may cause crankshaft seal leakage.Alternator, Fan and Accessory Drive Belts
Inspect/Replace
Inspect the condition and adjustment of alternator belts and fan drive belts.Inspect the drive belts for wear and replace if they show any signs of wear. If one belt in a set requires replacement, always install a new matched set of belts. Never replace just the worn belt. If only the worn belt is replaced, the new belt will carry all the load, as it will not be stretched as much as the older belts. All the belts will fail in rapid succession.Belt Adjustment
* To check the belt tension, apply 25 lbs (110 N) of force midway between the pulleys. Correctly adjusted belts will deflect 1/2 to 3/4 inch (13 to 19 mm).If belts are too loose, they vibrate enough to cause unnecessary wear on the belts and pulleys. If belts are too tight, unnecessary stresses are placed upon the pulley bearings and belts which might shorten the life of both.The engine is equipped with an automatic belt tensioner, adjustments should not be necessary.Hoses and Clamps
Inspect/Replace
Hose replacement prior to failure is a cost effective preventive maintenance practice. Replacing a hose before it fails saves money and reduces the chances for unscheduled downtime. By replacing a hose that is cracked, soft or leaking, you will avoid major repairs that could result in a severe engine overheating problem. * Inspect all hoses for leaks due to cracking, softness and loose clamps.* Replace hoses that are cracked or soft and tighten loose clamps.Before Replacing Hoses
1. After engine is cool, loosen the radiator filler cap slowly to relieve any pressure and remove the cap.2. Drain the coolant from the cooling system to a level below the hose being replaced.3. Remove the hose clamps, disconnect the old hose and replace with a new hose.4. Install hose clamps. (See the Torque for Standard Hose Clamps-Worm Band Type chart in the Torque Specifications section of this publication for the appropriate torque.) For constant torque hose clamps, see the Torque Specifications section in this publication.After Replacing Hoses
Refer to the Cooling System Specifications and Cooling System-Test for Coolant Additive maintenance topics in this publication.5. Add coolant mixture to the cooling system. Bring it to the proper level by mixing a solution of acceptable water and Caterpillar Antifreeze. Test for supplemental additive (Conditioner) concentration. Add proper amount, or if equipped with a coolant additive element, install the appropriate element
Clean
1. Loosen hose clamp (1) and remove the hose from the cover.2. Loosen three breather cover bolts (2) and remove cover (3). 3. Remove breather element (4), and wash in clean, nonflammable solvent and allow to dry. 4. Install clean, dry breather element (4).5. Install cover (3) and bolts (2).5. Install hose and clamp (1). Tighten clamp (1), refer to topic "Torque Specifications" for the proper torque of hose clamp-worm drive band type. If the crankcase breather is not maintained on a regular basis, it will become plugged. A plugged crankcase breather would result in excessive crankcase pressure that may cause crankshaft seal leakage.Alternator, Fan and Accessory Drive Belts
Inspect/Replace
Inspect the condition and adjustment of alternator belts and fan drive belts.Inspect the drive belts for wear and replace if they show any signs of wear. If one belt in a set requires replacement, always install a new matched set of belts. Never replace just the worn belt. If only the worn belt is replaced, the new belt will carry all the load, as it will not be stretched as much as the older belts. All the belts will fail in rapid succession.Belt Adjustment
* To check the belt tension, apply 25 lbs (110 N) of force midway between the pulleys. Correctly adjusted belts will deflect 1/2 to 3/4 inch (13 to 19 mm).If belts are too loose, they vibrate enough to cause unnecessary wear on the belts and pulleys. If belts are too tight, unnecessary stresses are placed upon the pulley bearings and belts which might shorten the life of both.The engine is equipped with an automatic belt tensioner, adjustments should not be necessary.Hoses and Clamps
Inspect/Replace
Hose replacement prior to failure is a cost effective preventive maintenance practice. Replacing a hose before it fails saves money and reduces the chances for unscheduled downtime. By replacing a hose that is cracked, soft or leaking, you will avoid major repairs that could result in a severe engine overheating problem. * Inspect all hoses for leaks due to cracking, softness and loose clamps.* Replace hoses that are cracked or soft and tighten loose clamps.Before Replacing Hoses
1. After engine is cool, loosen the radiator filler cap slowly to relieve any pressure and remove the cap.2. Drain the coolant from the cooling system to a level below the hose being replaced.3. Remove the hose clamps, disconnect the old hose and replace with a new hose.4. Install hose clamps. (See the Torque for Standard Hose Clamps-Worm Band Type chart in the Torque Specifications section of this publication for the appropriate torque.) For constant torque hose clamps, see the Torque Specifications section in this publication.After Replacing Hoses
Refer to the Cooling System Specifications and Cooling System-Test for Coolant Additive maintenance topics in this publication.5. Add coolant mixture to the cooling system. Bring it to the proper level by mixing a solution of acceptable water and Caterpillar Antifreeze. Test for supplemental additive (Conditioner) concentration. Add proper amount, or if equipped with a coolant additive element, install the appropriate element