Information injection-pump assembly
BOSCH
F 019 Z10 102
f019z10102
ZEXEL
101402-3840
1014023840
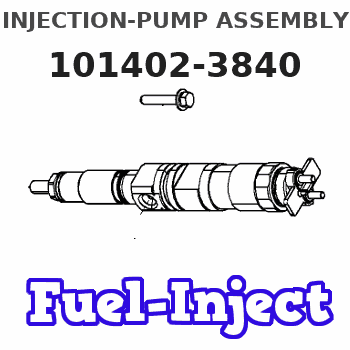
Rating:
Service parts 101402-3840 INJECTION-PUMP ASSEMBLY:
1.
_
5.
AUTOM. ADVANCE MECHANIS
6.
COUPLING PLATE
7.
COUPLING PLATE
8.
_
9.
_
10.
NOZZLE AND HOLDER ASSY
11.
Nozzle and Holder
12.
Open Pre:MPa(Kqf/cm2)
13.
NOZZLE-HOLDER
14.
NOZZLE
15.
NOZZLE SET
Cross reference number
BOSCH
F 019 Z10 102
f019z10102
ZEXEL
101402-3840
1014023840
Zexel num
Bosch num
Firm num
Name
Calibration Data:
Adjustment conditions
Test oil
1404 Test oil ISO4113 or {SAEJ967d}
1404 Test oil ISO4113 or {SAEJ967d}
Test oil temperature
degC
40
40
45
Nozzle and nozzle holder
105780-8140
Bosch type code
EF8511/9A
Nozzle
105780-0000
Bosch type code
DN12SD12T
Nozzle holder
105780-2080
Bosch type code
EF8511/9
Opening pressure
MPa
17.2
Opening pressure
kgf/cm2
175
Injection pipe
Outer diameter - inner diameter - length (mm) mm 6-2-600
Outer diameter - inner diameter - length (mm) mm 6-2-600
Overflow valve
131424-3420
Overflow valve opening pressure
kPa
255
221
289
Overflow valve opening pressure
kgf/cm2
2.6
2.25
2.95
Tester oil delivery pressure
kPa
157
157
157
Tester oil delivery pressure
kgf/cm2
1.6
1.6
1.6
Direction of rotation (viewed from drive side)
Right R
Right R
Injection timing adjustment
Direction of rotation (viewed from drive side)
Right R
Right R
Injection order
1-3-4-2
Pre-stroke
mm
2.5
2.45
2.55
Beginning of injection position
Drive side NO.1
Drive side NO.1
Difference between angles 1
Cal 1-3 deg. 90 89.5 90.5
Cal 1-3 deg. 90 89.5 90.5
Difference between angles 2
Cal 1-4 deg. 180 179.5 180.5
Cal 1-4 deg. 180 179.5 180.5
Difference between angles 3
Cyl.1-2 deg. 270 269.5 270.5
Cyl.1-2 deg. 270 269.5 270.5
Injection quantity adjustment
Adjusting point
A
Rack position
9.7
Pump speed
r/min
1000
1000
1000
Average injection quantity
mm3/st.
91.5
90.5
92.5
Max. variation between cylinders
%
0
-2.5
2.5
Basic
*
Fixing the lever
*
Boost pressure
kPa
44
44
Boost pressure
mmHg
330
330
Hydraulic cylinder ON
*
Injection quantity adjustment_02
Adjusting point
-
Rack position
7.1+-0.5
Pump speed
r/min
450
450
450
Average injection quantity
mm3/st.
10
9
11
Max. variation between cylinders
%
0
-15
15
Fixing the rack
*
Boost pressure
kPa
0
0
0
Boost pressure
mmHg
0
0
0
Hydraulic cylinder ON
*
Remarks
Adjust only variation between cylinders; adjust governor according to governor specifications.
Adjust only variation between cylinders; adjust governor according to governor specifications.
Injection quantity adjustment_03
Adjusting point
D
Rack position
-
Pump speed
r/min
100
100
100
Average injection quantity
mm3/st.
90
90
100
Fixing the lever
*
Boost pressure
kPa
0
0
0
Boost pressure
mmHg
0
0
0
Hydraulic cylinder OFF
*
Rack limit
*
Boost compensator adjustment
Pump speed
r/min
650
650
650
Rack position
R1-0.25
Boost pressure
kPa
26
23.3
28.7
Boost pressure
mmHg
195
175
215
Boost compensator adjustment_02
Pump speed
r/min
650
650
650
Rack position
R1(9.7)
Boost pressure
kPa
30.7
30.7
30.7
Boost pressure
mmHg
230
230
230
Test data Ex:
Governor adjustment
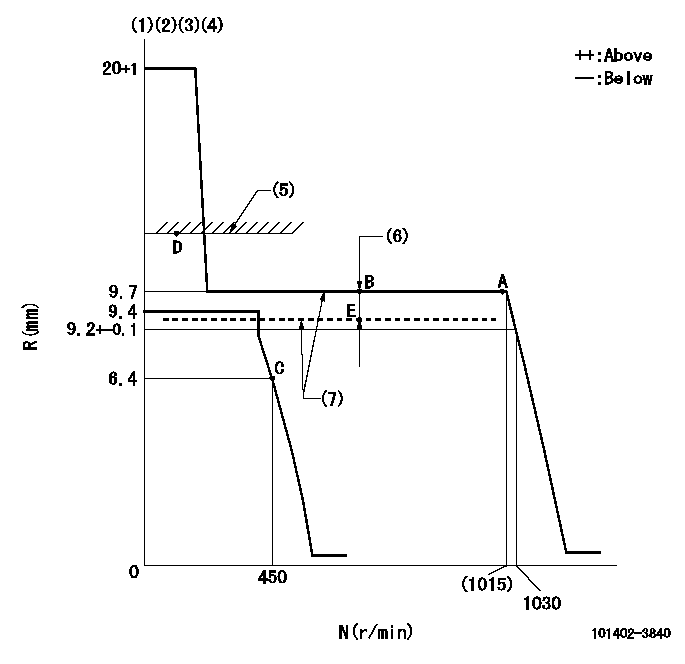
N:Pump speed
R:Rack position (mm)
(1)Target notch: K
(2)Tolerance for racks not indicated: +-0.05mm.
(3)The torque control spring does not operate.
(4)Adjust the secondary timing before adjusting the governor.
(5)RACK LIMIT (When hydraulic cylinder is OFF)
(6)Boost compensator stroke: BCL
(7)When hydraulic cylinder ON: P1
----------
K=15 BCL=0.25+-0.1mm P1=((392)kPa{(4)kgf/cm2})
----------
----------
K=15 BCL=0.25+-0.1mm P1=((392)kPa{(4)kgf/cm2})
----------
Speed control lever angle

F:Full speed
I:Idle
S:Stop
----------
----------
a=17deg+-3deg b=27deg+-5deg c=32deg+-3deg
----------
----------
a=17deg+-3deg b=27deg+-5deg c=32deg+-3deg
Stop lever angle
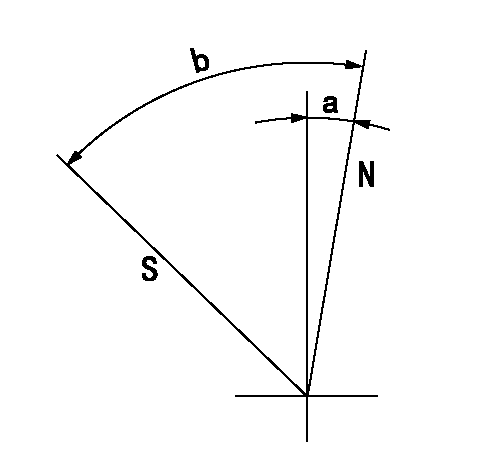
N:Pump normal
S:Stop the pump.
----------
----------
a=0deg+-5deg b=53deg+-5deg
----------
----------
a=0deg+-5deg b=53deg+-5deg
Timing setting

(1)Pump vertical direction
(2)Key groove position at No. 1 cylinder's beginning of injection position (at BTDC: aa).
(3)Position of the key groove of the No. 1 cylinder at B.T.D.C. bb (fix the governor flyweight at this position for delivery).
(4)B.T.D.C.: aa
(5)At second timing adjustment, set the camshaft at the * position and tighten the flyweight locknut.
(6)Align the flyweight's timing gear position with the lockpin groove and then fully tighten the flyweight to the camshaft.
(7)Remove the lock pin and adjust the governor. Reinstall the lock pin to fix the flyweight for delivery.
----------
aa=15deg bb=0deg
----------
a=54deg54min+-3deg b=7deg30min+-30min
----------
aa=15deg bb=0deg
----------
a=54deg54min+-3deg b=7deg30min+-30min
Information:
This Program can be administered either before or after a failure. In either case the decision whether to apply the Program is made by the dealer. When reporting the repair, use "PS9436" as the Part Number and "7755" as the Group Number. If administered before failure, use "56" as the Warranty Claim Description Code and use "T" as the SIMS Description Code. If administered after failure, use "96" as the Warranty Claim Description Code and use "Z" as the SIMS Description Code.
Termination Date
March 31, 1999Problem
Engines may experience ingress of coolant to the fuel system or vice versa due to the degradation of the sleeve seal-o-rings and the unit injector seal-o-rings. The contamination of coolant into the fuel system affects engine performance and can cause injector seizure. Contamination of fuel in the cooling system may reduce cooling performance.
Affected Product
Model & Identification Number
The work outlined in this program is to occur once only for the following engines with a minimum of 300,000 liters of fuel burned. In most applications this generally corresponds to:
*Every 300,000 kms of engine life for B-Triple and Triple Road Trains.*Every 450,000 kms of engine life for B-Double and Double Road Trains.*Every 600,000 kms of engine life for Single Trailers.3406E (5EK1-Up 6TS1-Up 1LW1-Up 5DS1-Up )
Parts Needed
6 - 9X7317 SEAL-O RING (Lower Seal-0-ring of unit Injector),6 - 9X7418 SEAL-O RING (Upper Seal-0-ring of Unit Injector),6 - 9X7419 SEAL-O RING (Mddle Seal-0-ring of Unit Injector),6 - 9X7430 SEAL-O-RING (Upper Seat-0-ring of unit Injector Sleeve),12- 9X7431 SEAL-O-RING (Lower Seal-0-ring of unit Injector Sleeve, two per sleeve),Action Required
See the attached procedure.
Service Claim Allowances
This job varies by cab type.
*See labor breakdowns. Labor Hours By Cab Type Parts Disposition
Please return seal-o-rings packaged in plastic bags, with relevant history of the truck and engine, to:
Steve Keenan,
Application and Service Engineer-
Caterpillar of Australia.
Private Mailbag 4.
Tuilamarine. 3043.
Handle all other parts in accordance with your Warranty Bulletin on warranty parts handling.
(1-Rework Procedure)Rework Procedure
1. Refer to attached parts book drawings.2. Obtain an ECM print-out from the Truck. Retain this print-out.3. Remove set of unit injectors. (Code 1290-010: refer p.109 of TRG for 3406E on highway truck engines;4. Drain and collect coolant.5. Remove and install set of unit injector sleeves (Code 1713-010: refer p. 111 of TRG).6. Replace injector body seals and sleeve seals. Return seals only as per parts disposition.7. Install set of unit injectors.8. Refill with coolant.9. Install set of unit injector sleeves.
Illustration 1.
Illustration 2.
Termination Date
March 31, 1999Problem
Engines may experience ingress of coolant to the fuel system or vice versa due to the degradation of the sleeve seal-o-rings and the unit injector seal-o-rings. The contamination of coolant into the fuel system affects engine performance and can cause injector seizure. Contamination of fuel in the cooling system may reduce cooling performance.
Affected Product
Model & Identification Number
The work outlined in this program is to occur once only for the following engines with a minimum of 300,000 liters of fuel burned. In most applications this generally corresponds to:
*Every 300,000 kms of engine life for B-Triple and Triple Road Trains.*Every 450,000 kms of engine life for B-Double and Double Road Trains.*Every 600,000 kms of engine life for Single Trailers.3406E (5EK1-Up 6TS1-Up 1LW1-Up 5DS1-Up )
Parts Needed
6 - 9X7317 SEAL-O RING (Lower Seal-0-ring of unit Injector),6 - 9X7418 SEAL-O RING (Upper Seal-0-ring of Unit Injector),6 - 9X7419 SEAL-O RING (Mddle Seal-0-ring of Unit Injector),6 - 9X7430 SEAL-O-RING (Upper Seat-0-ring of unit Injector Sleeve),12- 9X7431 SEAL-O-RING (Lower Seal-0-ring of unit Injector Sleeve, two per sleeve),Action Required
See the attached procedure.
Service Claim Allowances
This job varies by cab type.
*See labor breakdowns. Labor Hours By Cab Type Parts Disposition
Please return seal-o-rings packaged in plastic bags, with relevant history of the truck and engine, to:
Steve Keenan,
Application and Service Engineer-
Caterpillar of Australia.
Private Mailbag 4.
Tuilamarine. 3043.
Handle all other parts in accordance with your Warranty Bulletin on warranty parts handling.
(1-Rework Procedure)Rework Procedure
1. Refer to attached parts book drawings.2. Obtain an ECM print-out from the Truck. Retain this print-out.3. Remove set of unit injectors. (Code 1290-010: refer p.109 of TRG for 3406E on highway truck engines;4. Drain and collect coolant.5. Remove and install set of unit injector sleeves (Code 1713-010: refer p. 111 of TRG).6. Replace injector body seals and sleeve seals. Return seals only as per parts disposition.7. Install set of unit injectors.8. Refill with coolant.9. Install set of unit injector sleeves.
Illustration 1.
Illustration 2.