Information supply pump
BOSCH
9 440 610 180
9440610180
ZEXEL
105210-6020
1052106020
MITSUBISHI
ME731601
me731601
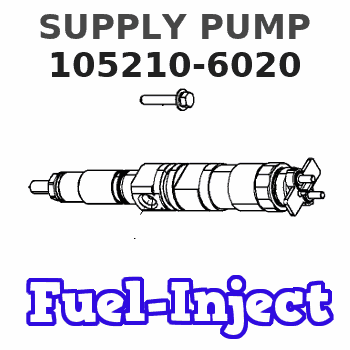
Rating:
Compare Prices: .
As an associate, we earn commssions on qualifying purchases through the links below
Scheme ###:
1. | [1] | 152061-0020 | PUMP HOUSING |
2. | [1] | 152030-0300 | STOP PIN |
5. | [1] | 152100-2301 | PUMP PLUNGER |
6. | [1] | 152102-0400 | COMPRESSION SPRING |
7. | [1] | 152105-1500 | CAPSULE |
8. | [1] | 139526-0000 | GASKET |
14. | [2] | 152115-0500 | VALVE BODY |
14. | [2] | 152115-0500 | VALVE BODY |
15. | [2] | 152116-0200 | COILED SPRING |
15. | [2] | 152116-0200 | COILED SPRING |
16. | [1] | 152117-0620 | CAPSULE |
18. | [2] | 029631-6060 | O-RING |
18. | [2] | 029631-6060 | O-RING |
25. | [1] | 152200-6720 | HAND PRIMER |
30. | [1] | 152300-6920 | EYE BOLT |
32. | [1] | 139814-0900 | EYE BOLT |
35. | [2] | 029341-4130 | GASKET D20&13.8T2* |
36. | [2] | 029341-4130 | GASKET D20&13.8T2* |
Include in #1:
101606-9850
as SUPPLY PUMP
Cross reference number
Zexel num
Bosch num
Firm num
Name
Information:
Unsolder the leads quickly to prevent heat from damaging the diodes.
(b) Remove the rectifiers mounting screws, then remove the rectifier.
Removing statorInspection
Key Points For Inspection(1) Inspection Rectifier
With each diode, measure the resistance between the diode terminal and the heat sink. Measure the resistance with the tester's (+) probe applied to the diode terminal and with the tester's (-) probe applied to the diode terminal. If the resistance is infinite in both cases, there is an open circuit. If the resistance is close to zero in both cases, there is a short circuit. An open circuit or short circuit indicates a diode fault. Replace the rectifiers if any diode is faulty.Next, measure the resistance between the terminals of the leads that connect the rectifier to the stator coil for each of the diodes. If any measurement reveals an open circuit (infinite resistance) or a short circuit (near-zero resistance), replace the rectifier.
Inspecting rectifier(2) Inspecting Field Coil
(a) Check whether continuity exists between the rotor's slip rings. If continuity does not exist, the field coil is open-circuited and the rotor must be replaced.
Field coil continuity test(b) Check whether continuity exists between each slip ring and the rotor shaft (or core). If continuity exists, the field coil is grounded and the rotor must be replaced.
Field coil ground test(3) Inspecting Stator Coils
(a) Check whether continuity exists between the leads at the ends of each stator coil. If continuity does not exist between any coil's leads, there is an open circuit and the stator must be replaced.
Stator coil continuity test(b) Check whether continuity exists between each stator coil lead and the stator core. If continuity exists, the stator coil is grounded and the stator must be replaced.
Stator coil ground test(4) Inspecting Brushes
(a) Replace the brush if it is worn down to the wear limit line.
Inspecting Brush(b) Disconnect the brush lead wires at the soldered sections to remove the brushes and springs.
Removing brushes and springs(c) To install new brushes, press them into the brush holders as shown in the diagram, then solder the lead wires.
Installing brushesAssembly
Follow the reverse of disassembly and use the procedure below:(1) The rear bearing has a groove for the snap ring. Install the snap ring in this groove. Make sure its tab is in the deep portion of the groove.(2) When installing the new rear bearing, place it in position with the side that has a groove toward the slip rings of the rotor.(3) To install the rear bearing in the rear bracket, heat the rear bracket.(4) Before installing the rotor in the rear bracket, insert a wire-shaped tooling into the hole in the rear bracket to lift the brushes of the slip rings. Remove the tooling after the rotor has been installed in position.
Assembling alternatorInstallation
Perform installation by following the removal sequence in reverse. Key Points For Installation(1) Install the fan belt on the alternator and mount the alternator on the engine. Temporarily tighten all the bolts.(2) Insert a bar between the alternator and crankcase. Using the bar as leverage, move the alternator