Information slotted washer
BOSCH
9 411 617 113
9411617113
ZEXEL
140217-2200
1402172200
ISUZU
8941289210
8941289210
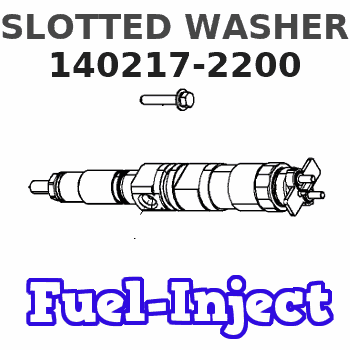
Rating:
Compare Prices: .
As an associate, we earn commssions on qualifying purchases through the links below
$29.95
24 Apr 2021
US: Hartville Hardware
John Deere Original Equipment Valve Seat #8941289210
John Deere
John Deere
Include in ###:
Cross reference number
Zexel num
Bosch num
Firm num
Name
140217-2200
9 411 617 113
8941289210 ISUZU
SLOTTED WASHER
C 23XX SPRING SEAT PFR- parts PFR
C 23XX SPRING SEAT PFR- parts PFR
140217-2200
9 411 617 113
131296531 ISHIKAWAJIMA-H
SLOTTED WASHER
C 23XX SPRING SEAT PFR- parts PFR
C 23XX SPRING SEAT PFR- parts PFR
140217-2200
9 411 617 113
62156390090 ISEKI
SLOTTED WASHER
C 23XX SPRING SEAT PFR- parts PFR
C 23XX SPRING SEAT PFR- parts PFR
140217-2200
9 411 617 113
2286310908 FUJI-HEAVY
SLOTTED WASHER
C 23XX SPRING SEAT PFR- parts PFR
C 23XX SPRING SEAT PFR- parts PFR
140217-2200
9 411 617 113
131296531 ISHIKAWAJIMA-S
SLOTTED WASHER
C 23XX SPRING SEAT PFR- parts PFR
C 23XX SPRING SEAT PFR- parts PFR
140217-2200
9 411 617 113
16328ZG3A0000 HONDA
SLOTTED WASHER
C 23XX SPRING SEAT PFR- parts PFR
C 23XX SPRING SEAT PFR- parts PFR
140217-2200
9 411 617 113
16328ZG30030 HONDA
SLOTTED WASHER
A C 23XX SPRING SEAT PFR- parts PFR
A C 23XX SPRING SEAT PFR- parts PFR
140217-2200
9 411 617 113
1533151291 KUBOTA
SLOTTED WASHER
C 23XX SPRING SEAT PFR- parts PFR
C 23XX SPRING SEAT PFR- parts PFR
140217-2200
9 411 617 113
3521016334B KAWASAKI-HEAVY
SLOTTED WASHER
C 23XX SPRING SEAT PFR- parts PFR
C 23XX SPRING SEAT PFR- parts PFR
140217-2200
9 411 617 113
160072004 KAWASAKI-HEAVY
SLOTTED WASHER
A C 23XX SPRING SEAT PFR- parts PFR
A C 23XX SPRING SEAT PFR- parts PFR
140217-2200
9 411 617 113
81185013010 TOYO-SHA
SLOTTED WASHER
C 23XX SPRING SEAT PFR- parts PFR
C 23XX SPRING SEAT PFR- parts PFR
140217-2200
9 411 617 113
1533151291 KUBOTA
SLOTTED WASHER
C 23XX SPRING SEAT PFR- parts PFR
C 23XX SPRING SEAT PFR- parts PFR
Information:
Fuel Tank Drain
Fuel tank drains are used to drain water and sediment from the fuel tank daily. The drain must be located on the lowest part of the fuel tank where the containments collect.Note: Daily draining of water and sediment from the fuel tank has been a standard maintenance requirement for decades.Advanced Tank Breather Filter
Preventing short fuel system life by keeping dust from entering the fuel tank.Water Separators
Water separators are required to remove large quantities of latent water from the fuel.Primary Fuel Filters
Primary fuel filters are required to remove large abrasives from the fuel supply and prevent premature clogging of the 4-micron secondary filters from excessive debris.Secondary Fuel Filters
Series filtration more than doubles wear life over single filtration.Electronic Unit Injectors (EUI)
An adequate fuel supply pressure is essential to prevent cavitation of internal injector components due to incomplete fuel fill.Major Factors Which Negatively Affect Fuel System Wear
Abrasive Contaminants
Increased injection pressure acting on the same level of abrasive contaminants in the fuel results in accelerated injector abrasive wear. This abrasive wear cannot be eliminated by using improved materials or processes. Abrasive wear only can be reduced by removing abrasives from the fuel. Solution
Single or series High Efficiency fuel filters and/or bulk fuel filter/water coalescer.Water in Fuel
An excessive amount of latent water in the fuel is a key cause of injector failure. Water has inadequate film strength to prevent metal-to-metal contact between the plunger and barrel, resulting in plunger scuffing or seizure. Water can be effectively by the use and regular maintenance of a water separator or bulk fuel filter/water coalescer. Removal of excess latent water is essential to prevent scuffing with the upcoming injection pressure increases and subsequent hydraulic loading of internal injector parts.Solution
Proper maintenance of fuel tank drains, water separators and/or use of a bulk fuel filter/water coalescer.Excessive Fuel Temperature
Increasing fuel temperatures reduces fuel viscosity and resultant fuel film strength. Reduced film strength increases the probability of injector plunger and barrel scuffing or seizure. Limiting the maximum fuel temperature will become even more critical with the increase of use if low sulfur fuel which has a lower film strength and common rail fuel systems which run elevated fuel temperatures. Fuel temperatures also play in diesel and biodiesel fuel degradation.Solution
Properly maintain fuel filters and fuel coolers where needed. Ensure proper consideration for materials used in fuel coolers as zinc, copper, lead, and tin can have adverse effects on fuel degradation.Customer Maintenance Practices
Fuel system performance, sophistication, and complexity continue to increase at a rapid pace. It is more important than ever for the user to maintain fuel filters in order to prevent filter restriction and the problems caused by low fuel pressure. It is also important to use quality Advanced Efficiency filters in order to trap and hold microscopic abrasive debris, which causes accelerated wear in modern fuel systems.C7 and C9 HEUI Fuel System Diagram
Note: The following illustration identifies components that may be included in many different arrangements. Refer to the Service Information System (SIS) for the correct components for the
Fuel tank drains are used to drain water and sediment from the fuel tank daily. The drain must be located on the lowest part of the fuel tank where the containments collect.Note: Daily draining of water and sediment from the fuel tank has been a standard maintenance requirement for decades.Advanced Tank Breather Filter
Preventing short fuel system life by keeping dust from entering the fuel tank.Water Separators
Water separators are required to remove large quantities of latent water from the fuel.Primary Fuel Filters
Primary fuel filters are required to remove large abrasives from the fuel supply and prevent premature clogging of the 4-micron secondary filters from excessive debris.Secondary Fuel Filters
Series filtration more than doubles wear life over single filtration.Electronic Unit Injectors (EUI)
An adequate fuel supply pressure is essential to prevent cavitation of internal injector components due to incomplete fuel fill.Major Factors Which Negatively Affect Fuel System Wear
Abrasive Contaminants
Increased injection pressure acting on the same level of abrasive contaminants in the fuel results in accelerated injector abrasive wear. This abrasive wear cannot be eliminated by using improved materials or processes. Abrasive wear only can be reduced by removing abrasives from the fuel. Solution
Single or series High Efficiency fuel filters and/or bulk fuel filter/water coalescer.Water in Fuel
An excessive amount of latent water in the fuel is a key cause of injector failure. Water has inadequate film strength to prevent metal-to-metal contact between the plunger and barrel, resulting in plunger scuffing or seizure. Water can be effectively by the use and regular maintenance of a water separator or bulk fuel filter/water coalescer. Removal of excess latent water is essential to prevent scuffing with the upcoming injection pressure increases and subsequent hydraulic loading of internal injector parts.Solution
Proper maintenance of fuel tank drains, water separators and/or use of a bulk fuel filter/water coalescer.Excessive Fuel Temperature
Increasing fuel temperatures reduces fuel viscosity and resultant fuel film strength. Reduced film strength increases the probability of injector plunger and barrel scuffing or seizure. Limiting the maximum fuel temperature will become even more critical with the increase of use if low sulfur fuel which has a lower film strength and common rail fuel systems which run elevated fuel temperatures. Fuel temperatures also play in diesel and biodiesel fuel degradation.Solution
Properly maintain fuel filters and fuel coolers where needed. Ensure proper consideration for materials used in fuel coolers as zinc, copper, lead, and tin can have adverse effects on fuel degradation.Customer Maintenance Practices
Fuel system performance, sophistication, and complexity continue to increase at a rapid pace. It is more important than ever for the user to maintain fuel filters in order to prevent filter restriction and the problems caused by low fuel pressure. It is also important to use quality Advanced Efficiency filters in order to trap and hold microscopic abrasive debris, which causes accelerated wear in modern fuel systems.C7 and C9 HEUI Fuel System Diagram
Note: The following illustration identifies components that may be included in many different arrangements. Refer to the Service Information System (SIS) for the correct components for the
Have questions with 140217-2200?
Group cross 140217-2200 ZEXEL
Isuzu
140217-2200
9 411 617 113
8941289210
SLOTTED WASHER
Ishikawajima-H
140217-2200
9 411 617 113
131296531
SLOTTED WASHER
Iseki
140217-2200
9 411 617 113
62156390090
SLOTTED WASHER
Fuji-Heavy
140217-2200
9 411 617 113
2286310908
SLOTTED WASHER
Ishikawajima-S
140217-2200
9 411 617 113
131296531
SLOTTED WASHER
Honda
140217-2200
9 411 617 113
16328ZG3A0000
SLOTTED WASHER
140217-2200
9 411 617 113
16328ZG30030
SLOTTED WASHER
Kubota
140217-2200
9 411 617 113
1533151291
SLOTTED WASHER
Kawasaki-Heavy
140217-2200
9 411 617 113
3521016334B
SLOTTED WASHER
140217-2200
9 411 617 113
160072004
SLOTTED WASHER
Toyo-Sha
140217-2200
9 411 617 113
81185013010
SLOTTED WASHER
Kubota
140217-2200
9 411 617 113
1533151291
SLOTTED WASHER