Information nozzle and holder assy.
BOSCH
9 430 613 945
9430613945
ZEXEL
105118-7721
1051187721
ISUZU
8972176420
8972176420
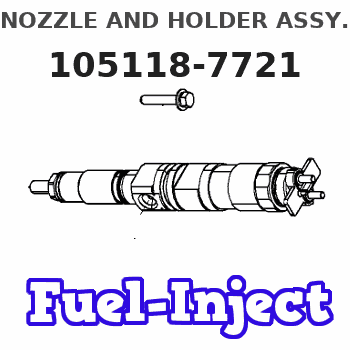
Rating:
Cross reference number
Zexel num
Bosch num
Firm num
Name
8972176420 ISUZU
NOZZLE AND HOLDER ASSY.
4JA1L * K 53KW N&NH
4JA1L * K 53KW N&NH
Information:
Belts, Hoses and Clamps
Inspect/Replace Accessory Drive Belts
Inspect the condition and adjustment of alternator drive belts. Examine belts for wear and replace if any signs of wear are present. Loose or worn pulley grooves cause belt slippage and low accessory drive speed.If belts are too loose, they vibrate enough to cause unnecessary wear on the belts and pulleys and possibly slip enough to cause overheating. If belts are too tight, unnecessary stresses are placed upon the pulley bearings and belts which can shorten the life of both.If one belt in a set requires replacement, always install a new matched set of belts. Never replace just the worn belt. If only the worn belt is replaced, the new belt will carry all the load, as it will not be stretched as much as the older belts. All the belts will fail in rapid succession.Adjust
1. Remove belt guard. Inspect the condition and adjustment of alternator belts and accessory drive belts, if equipped.2. To check the belt tension, apply 110 Newton (25 lb) force, perpendicular to the belt, midway between the driving and driven pulley. Measure the belt deflection. Correctly adjusted belts will deflect 13 to 20 mm (1/2 to 7/8 inch). Adjust the belt tension as required.If belt does not require replacement or adjustment, install the belt guard. If belt requires adjustment or replacement, do not install the belt guard.3. Loosen the mounting pivot bolt (1). Loosen the adjustment nut(s) (2).4. Adjust the alternator in or out by either tightening or loosening adjustment nut(s) as required to obtain the correct adjustment.5. Tighten bolts (1) and (2). Check the belt tension. Install the belt guard.If new belts are installed, check belt adjustment again after 30 minutes of engine operation. Repeat belt tightening if required.Adjust Accessory Drive Belts
If engine is equipped with any other belt driven equipment, check and adjust them as required.Inspect/Replace Hoses and Clamps
Hose replacement prior to failure is a good preventive maintenance practice. Replacing a hose before it fails reduces the chances for unscheduled downtime. By replacing a hose that is cracked, soft or leaking, major repairs will be avoided that could result in a severe engine overheating problem.* Inspect all hoses for leaks due to cracking, softness and loose clamps.* Replace hoses that are cracked or soft and tighten loose clamps. See the Torque for Standard Hose Clamps chart in the Torque Specifications section of this publication for the appropriate torque. For constant torque hose clamps, see the Torque Specifications section in this publication.Engine Valve Lash
Check/Adjust
To prevent possible injury, do not use the starting motor to turn the flywheel. Be sure the starting motors are disabled and engine cannot be started while this maintenance is being performed.Hot engine components can cause burns. Allow additional time for the engine to cool before measuring valve lash.
Measure the valve lash with the engine stopped. To obtain an accurate measurement, allow at least 20 minutes for the valves to cool to engine cylinder head and block temperature.
Initial valve lash adjustment (At First Oil
Inspect/Replace Accessory Drive Belts
Inspect the condition and adjustment of alternator drive belts. Examine belts for wear and replace if any signs of wear are present. Loose or worn pulley grooves cause belt slippage and low accessory drive speed.If belts are too loose, they vibrate enough to cause unnecessary wear on the belts and pulleys and possibly slip enough to cause overheating. If belts are too tight, unnecessary stresses are placed upon the pulley bearings and belts which can shorten the life of both.If one belt in a set requires replacement, always install a new matched set of belts. Never replace just the worn belt. If only the worn belt is replaced, the new belt will carry all the load, as it will not be stretched as much as the older belts. All the belts will fail in rapid succession.Adjust
1. Remove belt guard. Inspect the condition and adjustment of alternator belts and accessory drive belts, if equipped.2. To check the belt tension, apply 110 Newton (25 lb) force, perpendicular to the belt, midway between the driving and driven pulley. Measure the belt deflection. Correctly adjusted belts will deflect 13 to 20 mm (1/2 to 7/8 inch). Adjust the belt tension as required.If belt does not require replacement or adjustment, install the belt guard. If belt requires adjustment or replacement, do not install the belt guard.3. Loosen the mounting pivot bolt (1). Loosen the adjustment nut(s) (2).4. Adjust the alternator in or out by either tightening or loosening adjustment nut(s) as required to obtain the correct adjustment.5. Tighten bolts (1) and (2). Check the belt tension. Install the belt guard.If new belts are installed, check belt adjustment again after 30 minutes of engine operation. Repeat belt tightening if required.Adjust Accessory Drive Belts
If engine is equipped with any other belt driven equipment, check and adjust them as required.Inspect/Replace Hoses and Clamps
Hose replacement prior to failure is a good preventive maintenance practice. Replacing a hose before it fails reduces the chances for unscheduled downtime. By replacing a hose that is cracked, soft or leaking, major repairs will be avoided that could result in a severe engine overheating problem.* Inspect all hoses for leaks due to cracking, softness and loose clamps.* Replace hoses that are cracked or soft and tighten loose clamps. See the Torque for Standard Hose Clamps chart in the Torque Specifications section of this publication for the appropriate torque. For constant torque hose clamps, see the Torque Specifications section in this publication.Engine Valve Lash
Check/Adjust
To prevent possible injury, do not use the starting motor to turn the flywheel. Be sure the starting motors are disabled and engine cannot be started while this maintenance is being performed.Hot engine components can cause burns. Allow additional time for the engine to cool before measuring valve lash.
Measure the valve lash with the engine stopped. To obtain an accurate measurement, allow at least 20 minutes for the valves to cool to engine cylinder head and block temperature.
Initial valve lash adjustment (At First Oil