Information nozzle
BOSCH
9 432 610 931
9432610931
ZEXEL
105017-2360
1050172360
ISUZU
8972059730
8972059730
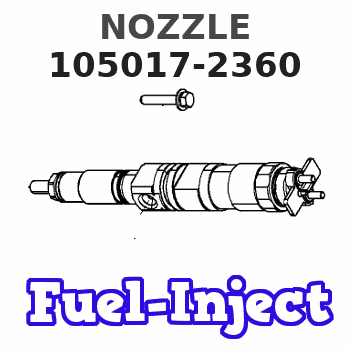
Rating:
Compare Prices: .
As an associate, we earn commssions on qualifying purchases through the links below
$44.99
25 Apr 2023
CN: lutong part plant
Diesel Fuel Injector Nozzles 105017-2360 DLLA158PN236 Fits for ISUZU TBR Panther 4JA1 4pcs/lot
DICSCL PARCS Diesel Fuel Injector Nozzles 105017-2360 DLLA158PN236 fits for ISUZU TBR Panther 4JA1 4pcs/lot. || Material: Made of high quality for longer durability and strength.100% quality inspection to ensure the high quality. Upgraded packaging to avoid damage. || Easy Installation:No further modification to direct replacement. || OEM Part Number:DLLA158PN236 || Estimated Time of Delivery from China: 5-10 working days.Customer satisfaction is always our top priority, we are standing by ready to provide you with reliable assistance with any questions you may have.
DICSCL PARCS Diesel Fuel Injector Nozzles 105017-2360 DLLA158PN236 fits for ISUZU TBR Panther 4JA1 4pcs/lot. || Material: Made of high quality for longer durability and strength.100% quality inspection to ensure the high quality. Upgraded packaging to avoid damage. || Easy Installation:No further modification to direct replacement. || OEM Part Number:DLLA158PN236 || Estimated Time of Delivery from China: 5-10 working days.Customer satisfaction is always our top priority, we are standing by ready to provide you with reliable assistance with any questions you may have.
Cross reference number
Zexel num
Bosch num
Firm num
Name
Information:
If the procedure did not correct the issue, contact your Cat dealer Technical Communicator (TC). For further assistance, your TC can confer with the Dealer Solutions Network (DSN).E1156(1) - Filter intake pressure greater than 10 kPa (1.50 psi) for more than 10 seconds. Refer to Table13 for troubleshooting.E1156(2) - Filter intake pressure greater than 15 kPa (2.25 psi) for more than 10 seconds. Refer to Table13 for troubleshooting.A faulty sensor may cause this diagnostic code. First determine that the sensor is not faulty.
Table 13
Troubleshooting Test Steps Values Results
1. Check for Associated Diagnostic Codes.
A. Establish communication between the Cat® Electronic Technician (ET) and the engine Electronic Control Module (ECM).
B. Troubleshoot any associated diagnostic codes that are present before continuing with this procedure.
Associated Diagnostic Codes
Result: An associated diagnostic code is not present.
Proceed to Test Step 2.
Result: An associated diagnostic code is active or logged.
1. Troubleshoot the associated diagnostic code before continuing with this procedure.
2. Service Maintenance.
A. Determine the most recent cleaning of the Wall Flow Filter (WFF).
Cleaning Interval
Result: The WFF was cleaned within the last 1000 hours.
Proceed to Test Step 3.
Result: The WFF was not cleaned within the last 1000 hours.
Proceed to Test Step 4.
3. Check for Contamination.
A. Reset all active codes and clear all logged codes.
B. Remove the WFF.
C. Check for contamination on the face of the WFF.
Contamination
Result: There is no sign of oil, fuel, or coolant on the WFF.
Proceed to Test Step 4.
Result: There is oil, fuel, or coolant on the WFF.
1. Diagnose the cause of the contamination.
2. The engine must be run with no load at 1400 rpm for at least 15 minutes, or until there is no white smoke.
3. If white smoke continues, or if the diagnostic code remains active, proceed to Test Step 5.
4. Clean the WFF.
A. Clean the WFF. Refer to "Wall Flow Diesel Particulate Filter - Clean".
B. Reset all active codes and clear all logged codes.
Clean was successful
Result: Cleaning the WFF was successful.
Return the machine to service.
Result: Cleaning the WFF was not successful.
1. Troubleshoot any diagnostic codes that are present, if no codes are present, proceed to Test Step 6.
5. Replace the WFF.
Replacement was successful
Result: Replacing the WFF was successful.
Return the machine to service.
If the procedure did not correct the issue, contact your Cat dealer Technical Communicator (TC). For further assistance, your TC can confer with the Dealer Solutions Network (DSN).Exhaust Temperature Is High
Certain operating conditions may cause the exhaust temperature to increase to a level that may damage engine components.Probable Causes
Boost Leak
Engine operating conditions
High altitude
Obstructed aftercooler
Table 14
Troubleshooting Test Steps Values Results
1. Check for Boost Leakage.
A. Apply a light load to the engine and check for boost leakage.
Boost Leaks
Result: Boost leakage was found.
Repair: Repair the leaks. Return the machine to service.
Result: Boost leakage was not found.
Proceed to Test Step 2.
2. Check the Engine Operating Conditions.
A. Check the histogram to determine if the high exhaust temperature was due to normal operation.
When possible, interview the operator. Determine if the engine is being operated under heavy load. Ensure that the engine is being operated at the
Table 13
Troubleshooting Test Steps Values Results
1. Check for Associated Diagnostic Codes.
A. Establish communication between the Cat® Electronic Technician (ET) and the engine Electronic Control Module (ECM).
B. Troubleshoot any associated diagnostic codes that are present before continuing with this procedure.
Associated Diagnostic Codes
Result: An associated diagnostic code is not present.
Proceed to Test Step 2.
Result: An associated diagnostic code is active or logged.
1. Troubleshoot the associated diagnostic code before continuing with this procedure.
2. Service Maintenance.
A. Determine the most recent cleaning of the Wall Flow Filter (WFF).
Cleaning Interval
Result: The WFF was cleaned within the last 1000 hours.
Proceed to Test Step 3.
Result: The WFF was not cleaned within the last 1000 hours.
Proceed to Test Step 4.
3. Check for Contamination.
A. Reset all active codes and clear all logged codes.
B. Remove the WFF.
C. Check for contamination on the face of the WFF.
Contamination
Result: There is no sign of oil, fuel, or coolant on the WFF.
Proceed to Test Step 4.
Result: There is oil, fuel, or coolant on the WFF.
1. Diagnose the cause of the contamination.
2. The engine must be run with no load at 1400 rpm for at least 15 minutes, or until there is no white smoke.
3. If white smoke continues, or if the diagnostic code remains active, proceed to Test Step 5.
4. Clean the WFF.
A. Clean the WFF. Refer to "Wall Flow Diesel Particulate Filter - Clean".
B. Reset all active codes and clear all logged codes.
Clean was successful
Result: Cleaning the WFF was successful.
Return the machine to service.
Result: Cleaning the WFF was not successful.
1. Troubleshoot any diagnostic codes that are present, if no codes are present, proceed to Test Step 6.
5. Replace the WFF.
Replacement was successful
Result: Replacing the WFF was successful.
Return the machine to service.
If the procedure did not correct the issue, contact your Cat dealer Technical Communicator (TC). For further assistance, your TC can confer with the Dealer Solutions Network (DSN).Exhaust Temperature Is High
Certain operating conditions may cause the exhaust temperature to increase to a level that may damage engine components.Probable Causes
Boost Leak
Engine operating conditions
High altitude
Obstructed aftercooler
Table 14
Troubleshooting Test Steps Values Results
1. Check for Boost Leakage.
A. Apply a light load to the engine and check for boost leakage.
Boost Leaks
Result: Boost leakage was found.
Repair: Repair the leaks. Return the machine to service.
Result: Boost leakage was not found.
Proceed to Test Step 2.
2. Check the Engine Operating Conditions.
A. Check the histogram to determine if the high exhaust temperature was due to normal operation.
When possible, interview the operator. Determine if the engine is being operated under heavy load. Ensure that the engine is being operated at the