Information locking washer
BOSCH
9 423 610 434
9423610434
ZEXEL
156322-0000
1563220000
ISUZU
1157491160
1157491160
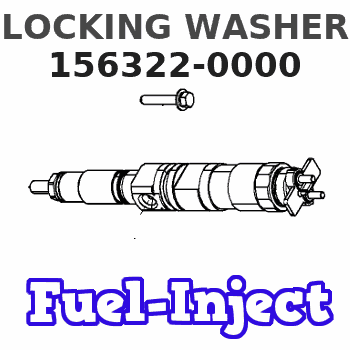
Rating:
Include in ###:
Cross reference number
Zexel num
Bosch num
Firm num
Name
156322-0000
9 423 610 434
1157491160 ISUZU
LOCKING WASHER
C 14GQ SPRING WASHER TIMER
C 14GQ SPRING WASHER TIMER
156322-0000
9 423 610 434
228731750A HINO
LOCKING WASHER
C 14GQ SPRING WASHER TIMER
C 14GQ SPRING WASHER TIMER
156322-0000
9 423 610 434
S228731750A HINO
LOCKING WASHER
A C 14GQ SPRING WASHER TIMER
A C 14GQ SPRING WASHER TIMER
156322-0000
9 423 610 434
ME716643 MITSUBISHI
LOCKING WASHER
C 14GQ SPRING WASHER TIMER
C 14GQ SPRING WASHER TIMER
156322-0000
9 423 610 434
16874Z9000 NISSAN-DIESEL
LOCKING WASHER
C 14GQ SPRING WASHER TIMER
C 14GQ SPRING WASHER TIMER
Information:
* Remove any carbon deposits from the injection nozzles before disassembling, assembling, or adjusting the injection nozzle assembly. Before disassembling, check the pressure and shape of the spray and inspect the assembly for fuel leakage. Do not disassemble if no defects are evident.* Do not change the needle valve and nozzle combination on each cylinder.
* Assembly sequenceFollow the disassembly sequence in reverse.Service standards Tightening torque (Unit: N m {kgf m}) Special tools (Unit: mm) Inspection before removal
Inspection: Injection nozzle* Connect the injection nozzle to the nozzle tester and carry out the following inspections.
* Before starting the inspections, operate the lever on the nozzle tester two or three times to bleed out all the air.
(1) Checking the valve opening pressure* Push down the lever on the nozzle tester at a rate of one to two seconds per stroke. This will cause the pressure gauge reading to rise gradually, and the needle will suddenly deflect. Note the pressure at which the needle starts to deflect. * If the measurement is out of the standard value range, disassemble the nozzle, clean it, and then adjust it using an adjusting shim.* Available adjusting shims (thickness): 1.2 mm to 1.7 mm (11 different thicknesses in increments of 0.05 mm)* If the valve opening pressure is still incorrect after the adjustment, replace the injection nozzle assembly.
* Do not touch the spray that comes out of the nozzle.
(2) Inspecting the spray condition * Pump the lever on the nozzle at a rate of about one to two seconds per stroke and keep it spraying continuously.A Spray in the form of straight line (Good: spray angle at 10° or less)B Spray angle too large (Bad)C Spray deviates from centerline (Bad)D Irregular spray (Bad)
* Do not touch the spray that comes out of the nozzle.
* Check that no fuel drips from the nozzle after the spray is complete.* If defects are evident, disassemble and clean the injection nozzle, and then inspect its spray condition once again.* If defects persist after reinspection, replace the injection nozzle assembly.(3) Checking for leakage * Decrease the nozzle pressure to a pressure 1960 kPa {20 kgf/cm2} lower than the first valve opening pressure. Maintain this pressure for 10 seconds and check that no fuel drips from the end of the nozzle.* If fuel drips are evident, disassemble and clean the injection nozzle, and then perform a leakage test once again.* If leakage is detected during the reinspection, replace the injection nozzle assembly.Removal procedure
Removal: Injection nozzle
* Do not touch the sliding surfaces of the needle valve. If you accidentally touch it, clean it with a cleaning fluid (such as gas oil).* Do not change the needle valve and nozzle combination on each cylinder.
Cleaning procedure
Cleaning: Injection nozzle* Wash the needle valve and nozzle in a cleaning fluid (such as gas oil), then use
to remove any carbon deposits according to the following procedure. * Remove carbon deposits from the tip of the needle valve using the clean bar of
.
* Do not use a wire brush
* Assembly sequenceFollow the disassembly sequence in reverse.Service standards Tightening torque (Unit: N m {kgf m}) Special tools (Unit: mm) Inspection before removal
Inspection: Injection nozzle* Connect the injection nozzle to the nozzle tester and carry out the following inspections.
* Before starting the inspections, operate the lever on the nozzle tester two or three times to bleed out all the air.
(1) Checking the valve opening pressure* Push down the lever on the nozzle tester at a rate of one to two seconds per stroke. This will cause the pressure gauge reading to rise gradually, and the needle will suddenly deflect. Note the pressure at which the needle starts to deflect. * If the measurement is out of the standard value range, disassemble the nozzle, clean it, and then adjust it using an adjusting shim.* Available adjusting shims (thickness): 1.2 mm to 1.7 mm (11 different thicknesses in increments of 0.05 mm)* If the valve opening pressure is still incorrect after the adjustment, replace the injection nozzle assembly.
* Do not touch the spray that comes out of the nozzle.
(2) Inspecting the spray condition * Pump the lever on the nozzle at a rate of about one to two seconds per stroke and keep it spraying continuously.A Spray in the form of straight line (Good: spray angle at 10° or less)B Spray angle too large (Bad)C Spray deviates from centerline (Bad)D Irregular spray (Bad)
* Do not touch the spray that comes out of the nozzle.
* Check that no fuel drips from the nozzle after the spray is complete.* If defects are evident, disassemble and clean the injection nozzle, and then inspect its spray condition once again.* If defects persist after reinspection, replace the injection nozzle assembly.(3) Checking for leakage * Decrease the nozzle pressure to a pressure 1960 kPa {20 kgf/cm2} lower than the first valve opening pressure. Maintain this pressure for 10 seconds and check that no fuel drips from the end of the nozzle.* If fuel drips are evident, disassemble and clean the injection nozzle, and then perform a leakage test once again.* If leakage is detected during the reinspection, replace the injection nozzle assembly.Removal procedure
Removal: Injection nozzle
* Do not touch the sliding surfaces of the needle valve. If you accidentally touch it, clean it with a cleaning fluid (such as gas oil).* Do not change the needle valve and nozzle combination on each cylinder.
Cleaning procedure
Cleaning: Injection nozzle* Wash the needle valve and nozzle in a cleaning fluid (such as gas oil), then use
to remove any carbon deposits according to the following procedure. * Remove carbon deposits from the tip of the needle valve using the clean bar of
.
* Do not use a wire brush
Have questions with 156322-0000?
Group cross 156322-0000 ZEXEL
Isuzu
156322-0000
9 423 610 434
1157491160
LOCKING WASHER
Hino
156322-0000
9 423 610 434
228731750A
LOCKING WASHER
156322-0000
9 423 610 434
S228731750A
LOCKING WASHER
Mitsubishi
156322-0000
9 423 610 434
ME716643
LOCKING WASHER
Nissan-Diesel
156322-0000
9 423 610 434
16874Z9000
LOCKING WASHER