Information injection-pump assembly
BOSCH
F 019 Z1D 030
f019z1d030
ZEXEL
109144-3050
1091443050
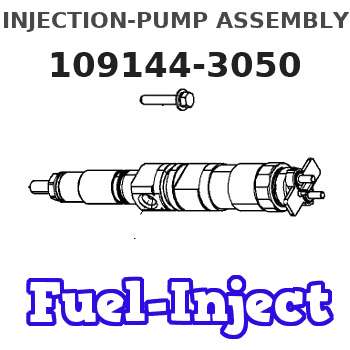
Rating:
Components :
0. | INJECTION-PUMP ASSEMBLY | 109144-3050 |
1. | _ | |
2. | FUEL INJECTION PUMP | 109044-3040 |
3. | NUMBER PLATE | |
4. | _ | |
5. | CAPSULE | |
6. | ADJUSTING DEVICE | |
7. | NOZZLE AND HOLDER ASSY | 105118-7833 |
8. | Nozzle and Holder | ME203961 |
9. | Open Pre:MPa(Kqf/cm2) | 17.6{179}/21.6{220} |
10. | NOZZLE-HOLDER | 105048-4410 |
11. | NOZZLE | 105019-1240 |
Scheme ###:
2. | [1] | 149520-0120 | BLEEDER SCREW |
3. | [1] | 149420-0001 | INTERMEDIATE PLATE |
5. | [1] | 149555-0000 | COVER |
6. | [1] | 149550-0020 | SUPPLY PUMP |
7. | [1] | 149911-0000 | O-RING |
8. | [1] | 149556-0000 | COVER |
9. | [1] | 149912-0200 | SEAL RING |
10. | [3] | 149916-0300 | TORX SCREW |
11. | [1] | 149916-0400 | TORX SCREW |
15. | [1] | 149600-0000 | DRIVE SHAFT |
16. | [1] | 149601-0000 | KEY |
17. | [1] | 149602-0000 | PLAIN WASHER |
17B. | [1] | 149602-0100 | PLAIN WASHER |
17C. | [1] | 149602-0200 | PLAIN WASHER |
17D. | [1] | 149602-0300 | PLAIN WASHER |
17E. | [1] | 149602-0400 | PLAIN WASHER |
17F. | [1] | 149602-0500 | PLAIN WASHER |
17G. | [1] | 149602-0600 | PLAIN WASHER |
17H. | [1] | 149602-0700 | PLAIN WASHER |
17I. | [1] | 149602-0800 | PLAIN WASHER |
17J. | [1] | 149602-0900 | PLAIN WASHER |
17K. | [1] | 149602-1000 | PLAIN WASHER |
18. | [1] | 149604-0000 | LOCKING WASHER |
20. | [1] | 149605-0000 | BEARING PLATE |
22. | [1] | 149606-0000 | COILED SPRING |
25. | [1] | 149610-0200 | CAM RING |
26. | [1] | 149615-0001 | PLATE |
26B. | [1] | 149615-0101 | PLATE |
26C. | [1] | 149615-0201 | PLATE |
26D. | [1] | 149615-0301 | PLATE |
26E. | [1] | 149615-0401 | PLATE |
26F. | [1] | 149615-0501 | PLATE |
26G. | [1] | 149615-0601 | PLATE |
26H. | [1] | 149615-0701 | PLATE |
26I. | [1] | 149615-0801 | PLATE |
26J. | [1] | 149615-0901 | PLATE |
26K. | [1] | 149615-1001 | PLATE |
26L. | [1] | 149615-1101 | PLATE |
26M. | [1] | 149615-1201 | PLATE |
27. | [2] | 149915-0000 | TORX BOLT |
31. | [1] | 149651-0000 | SLIDING PIECE |
32. | [1] | 149653-0300 | SHIM |
33. | [1] | 149652-0000 | COILED SPRING |
34. | [1] | 149653-0600 | SHIM |
35. | [2] | 149911-0100 | O-RING |
35. | [2] | 149911-0100 | O-RING |
36. | [1] | 149670-0000 | PLATE |
37. | [1] | 479765-6720 | TIMER PISTON SENSOR |
38. | [2] | 149917-1300 | BLEEDER SCREW |
40. | [1] | 149911-0200 | O-RING |
41. | [1] | 149911-0300 | O-RING |
42. | [1] | 149660-1020 | COVER |
43. | [4] | 149915-0600 | TORX BOLT |
45. | [2] | 149620-0000 | ROLLER |
46. | [2] | 149621-0000 | SHOE |
50. | [1] | 149701-0520 | HYDRAULIC HEAD |
50. | [1] | 149701-0520 | HYDRAULIC HEAD |
50. | [1] | 149701-0520 | HYDRAULIC HEAD |
50. | [1] | 149701-0520 | HYDRAULIC HEAD |
50. | [1] | 149701-0520 | HYDRAULIC HEAD |
51. | [2] | 146600-0000 | O-RING |
53. | [1] | 149720-0000 | SHIM |
53B. | [1] | 149720-0100 | SHIM |
53C. | [1] | 149720-0200 | SHIM |
53D. | [1] | 149720-0300 | SHIM |
54. | [1] | 016020-1410 | LOCKING WASHER |
55. | [4] | 146433-0100 | GASKET D12&6.4T1.00 |
56. | [4] | 149300-0420 | PRESSURE-CONTROL VALVE |
60. | [4] | 149915-0100 | TORX BOLT |
61. | [1] | 149722-0000 | CAPSULE |
62. | [1] | 146600-0500 | O-RING |
65. | [1] | 149805-0520 | GOVERNOR;ELECTRIC |
66. | [6] | 149915-0900 | TORX BOLT |
80. | [1] | 106144-1102 | TIMING CONTROL VALVE |
80/8. | [1] | 161440-3700 | O-RING |
81. | [1] | 149911-0400 | O-RING |
82. | [2] | 149913-0100 | BACKUP RING |
83. | [2] | 149915-0300 | TORX BOLT |
100. | [1] | 149571-0200 | EYE BOLT |
101. | [2] | 139512-0500 | GASKET |
102. | [1] | 149920-1620 | INLET UNION |
110. | [1] | 149570-0520 | OVER FLOW VALVE |
111. | [2] | 139512-0500 | GASKET |
112. | [1] | 149920-1720 | INLET UNION |
120. | [1] | 149570-0320 | OVER FLOW VALVE |
121. | [2] | 139512-0500 | GASKET |
122. | [1] | 149920-1520 | INLET UNION |
130. | [1] | 149560-0120 | CONTROL VALVE |
150. | [1] | 149900-0220 | PULLING ELECTROMAGNET |
150/9. | [1] | 149912-0500 | SEAL RING |
151. | [1] | 149575-0001 | FILTER |
152. | [1] | 149912-0500 | SEAL RING |
153. | [1] | 146621-1000 | UNION NUT |
160. | [1] | 479778-5620 | EEPROM ASSY |
161. | [4] | 149915-0500 | TORX BOLT |
205. | [1] | 149935-0000 | WOODRUFF KEY |
255. | [1] | 148650-0000 | BINDER |
256. | [2] | 148650-1500 | TUBE |
800S. | [1] | 149500-0420 | PUMP HOUSING |
905. | [1] | 149950-2400 | NAMEPLATE |
910. | [1] | 149930-0620 | BRACKET OEM:ME203139 |
911. | [1] | 149911-0600 | O-RING OEM:MF520407 |
912. | [3] | 149919-0100 | PLAIN WASHER OEM:MH005068 |
914. | [3] | 149918-0000 | UNION NUT OEM:MF434105 |
920. | [1] | 149931-1920 | TOOTHED GEAR OEM:ME204368 |
922. | [1] | 149918-0400 | UNION NUT OEM:ME204337 |
923. | [1] | 149931-0600 | PLATE OEM:ME203076 |
925. | [4] | 149917-1400 | BLEEDER SCREW OEM:MH001566 |
930. | [1] | 149925-0520 | BRACKET OEM:ME203989 |
931. | [3] | 149917-1000 | BLEEDER SCREW OEM:MF140227 |
948. | [1] | 149921-0200 | HOSE OEM:MS603003 |
949. | [2] | 149922-0000 | HOSE CLIP OEM:MS660164 |
949. | [2] | 149922-0000 | HOSE CLIP OEM:MS660164 |
955. | [2] | 149945-0220 | PULSE GENERATOR OEM:ME203180 |
956. | [2] | 149917-1100 | BLEEDER SCREW |
Include in #2:
109144-3050
as INJECTION-PUMP ASSEMBLY
Cross reference number
BOSCH
F 019 Z1D 030
f019z1d030
ZEXEL
109144-3050
1091443050
Zexel num
Bosch num
Firm num
Name
Calibration Data:
Adjustment conditions
Test oil
ISO4113
Nozzle and nozzle holder assembly
1 688 901 035
Opening pressure
bar
207
207
210
Injection pipe
157808-4720
Injection pipe
Inside diameter - outside diameter - length (mm) mm 1.6-6-45 0
Inside diameter - outside diameter - length (mm) mm 1.6-6-45 0
Cooling unit
1 687 010 130
Joint assembly
157641-6820
Transfer pump pressure
kPa
40
40
40
Transfer pump pressure
kgf/cm2
0.4
0.4
0.4
Direction of rotation (viewed from drive side)
Right R
Right R
Manual controller assembly
157966-4020
ECU assembly
157966-3820
Manual controller main harness
157966-4920
Manual controller intermediate harness
157966-5720
ROM harness
157966-5020
ROM intermediate harness
157966-2421
0000000201
Pre-stroke
deg.
2.5
2
3
Injection quantity adjustment
Max. applied voltage
V
8
8
8
Test voltage
V
13
12
14
Test data Ex:
Injection timing adjustment INJECTION PUMP PRE-STROKE
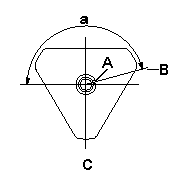
Key groove position at cylinder B's beginning of injection
A = key
B = B cylinder's beginning of static injection
C = when viewed from drive side
----------
----------
a=163.5deg
----------
----------
a=163.5deg
Information:
Problem
A failed sleeve or sleeve to head joint 3176 Truck Engines may cause fuel dilution of the cooling system, coolant entry into the injector cavity, or coolant entry into the cylinder.
Affected Product
Mode & Identification Number
3176 (2YG4902-9368*)
*If not previously reworked and stamped with "3S" next to Serial No. PlateParts Needed
4 - 7C2597 Gasket (water lines)5 - 8C3684 Antifreeze (gal) (if contaminated with fuel)6 - 3H2388 seal-O ring (spacer to head)6 - 4P7135 sleeve6 - 5P8066 O-ring (upper injector)1 - 1S7057 Gasket (turbo oil supply)1 - 7W2398 Gasket (turbo drain)6 - 9X7722 O-ring (lower injector)1 - 9Y7044 Gasket-Cylinder Head (only if head needs removal)Action Required
1. When it is necessary to replace a sleeve due to failure of the sleeve or the sleeve to head joint:a) Check for 3S stamped on the block next to the serial number plate. If block is stamped with 3S, change only the failed sleeve using 4P7135 sleeves. The 4C6730 Roller Expander and 4C6714 Swage must be used to install the new sleeves. See Special Instruction SEHS9246. Failure on engines marked 3S should be filed as normal warranty.b) If block is not stamped 3S replace all six sleeves using 4P7135 sleeves. The 4C6730 Roller Expander and 4C6714 Swage must be used to install the new sleeves. See Special Instruction SEHS9246.2. Ream all sleeves and check injector sleeve seating surface in head. Install the injector and check for good seat using blue dykem.3. Stamp 3S in the block next to the serial number plate after work is complete.Engine Disassembly
Cylinder Head Removal - It is possible to replace the sleeves without removing the cylinder head. See Special Instruction SEHS9246. However, in some applications it may be more efficient to remove the head. This decision is left to the dealer. Reason to remove the head must be explained in the claim story.
Off Engine Test
Test electronic unit injectors for leaks and VOP on test bench if milage is less than 150,000 mi. Replace as necessary.
Engine Assembly
1) Pressurize the cooling system to 15 psi. Look for leakage in and around sleeve cavity to check installation process. Replace any leaking sleeves.2) Test for fuel leaks past the upper injector O-rings by blocking the fuel return line and pressurizing to 100 psi. (observe for 3 minutes)3) Install the remainder of the parts to complete assembly of the engine.4) If failure resulted in fuel in the coolant, flush and fill cooling system. Flush the system for a minimum of 30 minutes using 4C4609/4C4613 Cleaner (may use 6V4511 as a substitute). Fill the cooling system using a 50% mixture of low silicate antifreeze and distilled water. If Caterpillar antifreeze is not used, add 6% cooling system conditioner.Service Claim Allowances
This a labor breakdown for in-frame repair when the block has been stamped 3S.
This is a labor breakdown (when the block has not been stamped 3S) if removal of the cylinder is needed. Head removal must be justified in the claim story.
Additional Labor segments can be claimed if necessary.
Parts Disposition
Handle the parts in accordance with your Warranty
A failed sleeve or sleeve to head joint 3176 Truck Engines may cause fuel dilution of the cooling system, coolant entry into the injector cavity, or coolant entry into the cylinder.
Affected Product
Mode & Identification Number
3176 (2YG4902-9368*)
*If not previously reworked and stamped with "3S" next to Serial No. PlateParts Needed
4 - 7C2597 Gasket (water lines)5 - 8C3684 Antifreeze (gal) (if contaminated with fuel)6 - 3H2388 seal-O ring (spacer to head)6 - 4P7135 sleeve6 - 5P8066 O-ring (upper injector)1 - 1S7057 Gasket (turbo oil supply)1 - 7W2398 Gasket (turbo drain)6 - 9X7722 O-ring (lower injector)1 - 9Y7044 Gasket-Cylinder Head (only if head needs removal)Action Required
1. When it is necessary to replace a sleeve due to failure of the sleeve or the sleeve to head joint:a) Check for 3S stamped on the block next to the serial number plate. If block is stamped with 3S, change only the failed sleeve using 4P7135 sleeves. The 4C6730 Roller Expander and 4C6714 Swage must be used to install the new sleeves. See Special Instruction SEHS9246. Failure on engines marked 3S should be filed as normal warranty.b) If block is not stamped 3S replace all six sleeves using 4P7135 sleeves. The 4C6730 Roller Expander and 4C6714 Swage must be used to install the new sleeves. See Special Instruction SEHS9246.2. Ream all sleeves and check injector sleeve seating surface in head. Install the injector and check for good seat using blue dykem.3. Stamp 3S in the block next to the serial number plate after work is complete.Engine Disassembly
Cylinder Head Removal - It is possible to replace the sleeves without removing the cylinder head. See Special Instruction SEHS9246. However, in some applications it may be more efficient to remove the head. This decision is left to the dealer. Reason to remove the head must be explained in the claim story.
Off Engine Test
Test electronic unit injectors for leaks and VOP on test bench if milage is less than 150,000 mi. Replace as necessary.
Engine Assembly
1) Pressurize the cooling system to 15 psi. Look for leakage in and around sleeve cavity to check installation process. Replace any leaking sleeves.2) Test for fuel leaks past the upper injector O-rings by blocking the fuel return line and pressurizing to 100 psi. (observe for 3 minutes)3) Install the remainder of the parts to complete assembly of the engine.4) If failure resulted in fuel in the coolant, flush and fill cooling system. Flush the system for a minimum of 30 minutes using 4C4609/4C4613 Cleaner (may use 6V4511 as a substitute). Fill the cooling system using a 50% mixture of low silicate antifreeze and distilled water. If Caterpillar antifreeze is not used, add 6% cooling system conditioner.Service Claim Allowances
This a labor breakdown for in-frame repair when the block has been stamped 3S.
This is a labor breakdown (when the block has not been stamped 3S) if removal of the cylinder is needed. Head removal must be justified in the claim story.
Additional Labor segments can be claimed if necessary.
Parts Disposition
Handle the parts in accordance with your Warranty