Information injection-pump assembly
BOSCH
9 400 613 078
9400613078
ZEXEL
108922-2150
1089222150
MITSUBISHI
ME351919
me351919
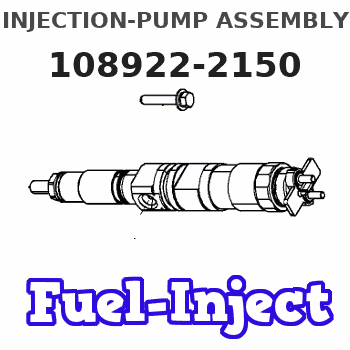
Rating:
Service parts 108922-2150 INJECTION-PUMP ASSEMBLY:
1.
_
5.
AUTOM. ADVANCE MECHANIS
7.
COUPLING PLATE
11.
Nozzle and Holder
ME072662
12.
Open Pre:MPa(Kqf/cm2)
17.7{180}/24.5{250}
14.
NOZZLE
Include in #1:
108922-2150
as INJECTION-PUMP ASSEMBLY
Cross reference number
Zexel num
Bosch num
Firm num
Name
9 400 613 078
ME351919 MITSUBISHI
INJECTION-PUMP ASSEMBLY
10M21 * 14CR TICS HD-TI10F TICS
10M21 * 14CR TICS HD-TI10F TICS
Information:
CHECKING FLYWHEEL FACE RUNOUT4. The difference between the lowest and highest readings taken at all four points should not exceed .006 in. (0.15 mm), which is the maximum permissible flywheel face runout.Checking Flywheel Bore Runout
CHECKING FLYWHEEL BORE RUNOUT
1. 7H1945 Holding Rod. 2. 7H1645 Holding Rod. 3. 7H1942 Indicator. 4. 7H1940 Universal Attachment.Make tool setup from parts of the 8S2328 Dial Test Indicator Group.1. Mount the dial indicator and adjust it so the universal attachment contacts the flywheel bore as shown.2. Adjust the dial indicator to read .000 in. (0.0 mm) then take readings every 90° around the flywheel.3. The difference between the lowest and highest readings taken at all four points should not exceed .006 in. (0.15 mm), which is the maximum permissible flywheel bore runout. Flywheel clutch pilot bearing bore runout should not exceed .005 in. (0.13 mm).
CHECKING FLYWHEEL CLUTCH PILOT BEARING BOREElectrical System
Most of the testing of the electrical system can be done on the engine. The wiring insulation must be in good condition, the wire and cable connections clean and tight and the battery fully charged. If on the engine test shows a defect in a component, remove the component for more testing. The wire size, color and recommendations of length are given in the WIRING DIAGRAMS in SYSTEMS OPERATION.Battery
9S1990 Battery Charger Tester.The battery circuit is an electrical load on the charging unit. The load is variable because of the condition of the charge in the battery. Damage to the charging unit will result, if the connections, (either positive or negative) between the battery and charging unit are broken while the charging unit is charging. This is because the battery load is lost and there is an increase in charging voltage.High voltage will damage, not only the charging unit but also the regulator and other electrical components.
9S1990 BATTERY CHARGER TESTER
Never disconnect any charging unit circuit or battery circuit cable from battery when the charging unit is charging.
Load test a battery that does not hold a charge when in use. To do this, put a resistance, across the battery main connections (terminals). For a 6 volt battery, put a resistance of two times the ampere/hour rating of the battery. For a 12 volt battery, put a resistance of three times the ampere/hour rating. Let the resistance remove the charge (discharge the battery) for 15 seconds. Immediately test the battery voltage. A 6 volt battery in good condition will test 4.5 volts; a 12 volt battery in good condition will test 9 volts.The Special Instruction (GEG00058) with the 9S1990 Charger Tester gives the battery testing procedure.Charging System
Battery
The condition of charge in the battery at each regular inspection will show if the charging system is operating correctly. An adjustment is necessary when the battery is always in a low condition of charge or a large amount of water is needed (one ounce per cell per week or every 50 service hours).Test the charging units and voltage regulators on the engine, when possible, using wiring and components that are