Information injection-pump assembly
BOSCH
9 400 619 402
9400619402
ZEXEL
108922-2050
1089222050
MITSUBISHI
ME094336
me094336
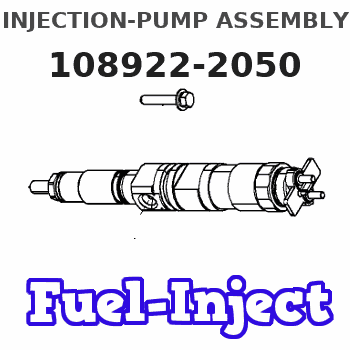
Rating:
Service parts 108922-2050 INJECTION-PUMP ASSEMBLY:
1.
_
5.
AUTOM. ADVANCE MECHANIS
7.
COUPLING PLATE
11.
Nozzle and Holder
ME093528
12.
Open Pre:MPa(Kqf/cm2)
14.
NOZZLE
Include in #1:
108922-2050
as INJECTION-PUMP ASSEMBLY
Cross reference number
BOSCH
9 400 619 402
9400619402
ZEXEL
108922-2050
1089222050
MITSUBISHI
ME094336
me094336
Zexel num
Bosch num
Firm num
Name
9 400 619 402
ME094336 MITSUBISHI
INJECTION-PUMP ASSEMBLY
10DC9T2 K 14CR INJECTION PUMP ASSY TICS HD-TI10F TICS
10DC9T2 K 14CR INJECTION PUMP ASSY TICS HD-TI10F TICS
Calibration Data:
Adjustment conditions
Test oil
1404 Test oil ISO4113 or {SAEJ967d}
1404 Test oil ISO4113 or {SAEJ967d}
Test oil temperature
degC
40
40
45
Nozzle and nozzle holder
105780-8250
Bosch type code
1 688 901 101
Nozzle
105780-0120
Bosch type code
1 688 901 990
Nozzle holder
105780-2190
Opening pressure
MPa
20.7
Opening pressure
kgf/cm2
211
Injection pipe
Outer diameter - inner diameter - length (mm) mm 8-3-600
Outer diameter - inner diameter - length (mm) mm 8-3-600
Overflow valve
131425-0220
Overflow valve opening pressure
kPa
157
123
191
Overflow valve opening pressure
kgf/cm2
1.6
1.25
1.95
Tester oil delivery pressure
kPa
255
255
255
Tester oil delivery pressure
kgf/cm2
2.6
2.6
2.6
RED3 control unit part number
407910-3
960
RED3 rack sensor specifications
mm
19
PS/ACT control unit part no.
407980-2
24*
Digi switch no.
52
Direction of rotation (viewed from drive side)
Right R
Right R
Injection timing adjustment
Direction of rotation (viewed from drive side)
Right R
Right R
Injection order
1-2-7-8-
5-6-3-4-
9-10
Pre-stroke
mm
8.5
8.47
8.53
Beginning of injection position
Governor side NO.1
Governor side NO.1
Difference between angles 1
Cyl.1-2 deg. 45 44.75 45.25
Cyl.1-2 deg. 45 44.75 45.25
Difference between angles 2
Cal 1-7 deg. 72 71.75 72.25
Cal 1-7 deg. 72 71.75 72.25
Difference between angles 3
Cal 1-8 deg. 117 116.75 117.25
Cal 1-8 deg. 117 116.75 117.25
Difference between angles 4
Cal 1-5 deg. 144 143.75 144.25
Cal 1-5 deg. 144 143.75 144.25
Difference between angles 5
Cal 1-6 deg. 189 188.75 189.25
Cal 1-6 deg. 189 188.75 189.25
Difference between angles 6
Cal 1-3 deg. 216 215.75 216.25
Cal 1-3 deg. 216 215.75 216.25
Difference between angles 7
Cal 1-4 deg. 261 260.75 261.25
Cal 1-4 deg. 261 260.75 261.25
Difference between angles 8
Cal 1-9 deg. 288 287.75 288.25
Cal 1-9 deg. 288 287.75 288.25
Difference between angles 9
Cal 1-10 deg. 333 332.75 333.25
Cal 1-10 deg. 333 332.75 333.25
Injection quantity adjustment
Rack position
(11.2)
Vist
V
2.18
2.18
2.18
Pump speed
r/min
650
650
650
Average injection quantity
mm3/st.
128.5
127.5
129.5
Max. variation between cylinders
%
0
-3
3
Basic
*
PS407980-224*
V
2.45+-0.
01
PS407980-224*
mm
6.1+-0.0
5
Injection quantity adjustment_02
Rack position
(6.8)
Vist
V
2.8
2.7
2.9
Pump speed
r/min
375
375
375
Average injection quantity
mm3/st.
19
17
21
Max. variation between cylinders
%
0
-15
15
PS407980-224*
V
V1+0.05+
-0.01
PS407980-224*
mm
8.4+-0.0
3
Remarks
Refer to items regarding the pre-stroke actuator
Refer to items regarding the pre-stroke actuator
0000001201
Pre-stroke
mm
8.5
8.47
8.53
Remarks
When the timing sleeve is pushed up
When the timing sleeve is pushed up
_02
Connector angle
deg.
8.5
8
9
Remarks
When the eccentric pin is tightened
When the eccentric pin is tightened
_03
Supply voltage
V
24
23.5
24.5
Ambient temperature
degC
23
18
28
Pre-stroke
mm
6.1
6.05
6.15
Output voltage
V
2.45
2.44
2.46
Adjustment
*
_04
Supply voltage
V
24
23.5
24.5
Ambient temperature
degC
23
18
28
Pre-stroke
mm
8.5
8.47
8.53
Output voltage
V
1.2
1
1.4
Confirmation
*
Remarks
Output voltage V1
Output voltage V1
_05
Supply voltage
V
24
23.5
24.5
Ambient temperature
degC
23
18
28
Pre-stroke
mm
5.5
Output voltage
V
3
2.98
3
Confirmation
*
_06
Supply voltage
V
24
23.5
24.5
Ambient temperature
degC
23
18
28
Output voltage
V
3.05
3.05
Confirmation of operating range
*
Test data Ex:
Speed control lever angle

N:Pump normal
S:Stop the pump.
(1)Rack position = aa
(2)Rack position bb
----------
aa=20mm bb=1mm
----------
a=35deg+-5deg b=37deg+-5deg
----------
aa=20mm bb=1mm
----------
a=35deg+-5deg b=37deg+-5deg
0000000901

(1)Pump vertical direction
(2)Coupling's key groove position at No 1 cylinder's beginning of injection
(3)At the No 1 cylinder's beginning of injection position, stamp an aligning mark on the damper to align with the pointer's groove.
(4)Damper
(5)Pointer
(6)B.T.D.C.: aa
(7)Pre-stroke: bb
----------
aa=6deg bb=8.5+-0.03mm
----------
a=44deg30min+-3deg b=(44deg)
----------
aa=6deg bb=8.5+-0.03mm
----------
a=44deg30min+-3deg b=(44deg)
0000001501
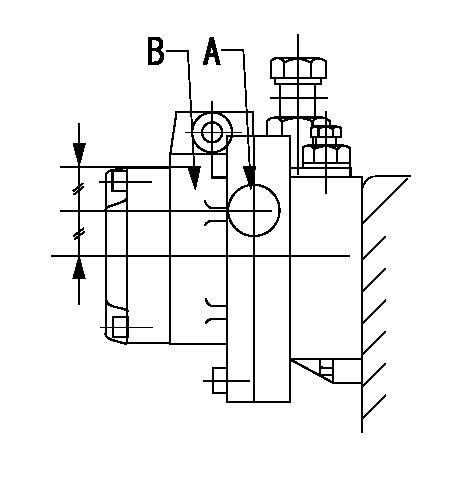
A:Sealing position
B:Pre-stroke actuator
1. When installing the pre-stroke actuator on the pump, first tighten the installation bolts loosely, then move the actuator fully counterclockwise (viewed from the drive side).
Temporary tightening torque: 1 - 1.5 N.m (0.1 - 0.15 kgf.m)
2. Move the actuator in the clockwise direction when viewed from the drive side, and adjust so that it becomes the adjustment point of the adjustment value. Then tighten it.
Tightening torque: 7^9 N.m (0.7^0.9 kgf.m)
3. After prestroke actuator installation adjustment, simultaneously stamp both the actuator side and housing side.
----------
----------
----------
----------
0000001701
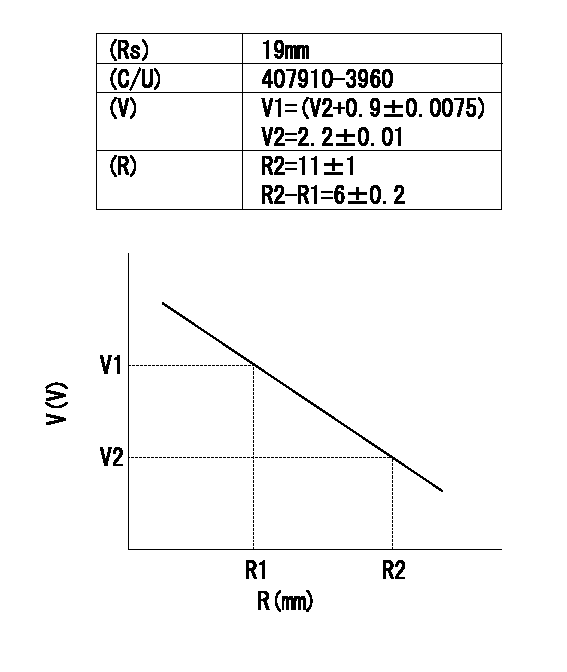
(Rs) rack sensor specifications
(C/U) control unit part number
(V) Rack sensor output voltage
(R) Rack position (mm)
1. Confirming governor output characteristics (rack 19 mm, span 6 mm)
(1)When the output voltages of the rack sensor are V1 and V2, check that the rack positions R1 and R2 in the table above are satisfied.
----------
----------
----------
----------
0000001901 RACK SENSOR

(VR) measurement voltage
(I) Part number of the control unit
(G) Apply red paint.
(H): End surface of the pump
1. Rack sensor adjustment (154610-0620)
(1)At governor side rack sensor output voltage V1, adjust the bobbin (A) so that the drive side rack sensor output voltage is VR+-0.01.
(2)Apply G at two places.
Connecting part between the joint (B) and the nut (F)
Connecting part between the joint (B) and the end surface of the pump (H)
----------
V1=1.6V
----------
----------
V1=1.6V
----------
Information:
This Revised Service Letter replaces the 25May2010 Service Letter. Changes have been made to Termination Date.
TERMINATION DATE
31Jul2010
PROBLEM
The fuel inlet check valves, on the fuel injection pump, may fail on certain C6.6 Industrial Engines that are installed in specific OEM Applications. A failure of the inlet check valves could result in any of the following symptoms: failure to start, prevention of the engine from achieving full power, or a de-rate of the engine.
Before any repair is carried out, ensure the appropriate trouble shooting steps have been followed and carried out.
AFFECTED PRODUCT
Model Identification Number
C6.6 TIER 3 66605372, 5675-5704, 5718, 5720-5726, 5728-5731, 5733, 5735-5749, 5751-5771, 6005-6024, 6438, 7207-7215, 7221-7232, 7234-7240, 7268-7277, 7279-7288, 7428, 9732, 9746-9747, 9749-9754, 9756-9760, 9765, 9790-9809, 9823-9826, 9828-9839, 9841-9842, 9877-9894, 9896-9902, 9931-9937, 9939-9950, 9952-9955, 9959-9961, 10000, 10003-10005, 10007-10023, 10116, 10118-10149, 10438
PARTS NEEDED
Qty
Part Number Description
1 1113423 WASHER
1 2258019 GASKET-PUMP-HSG
3 2323149 WASHER-SEALING
1 2784138 PROTECTION KT
1 3368180 TUBE FUEL-INJ
1 3495736 PUMP GP-FUEL
In order to allow equitable parts availability to all participating dealers, please limit your initial parts order to not exceed 32% of dealership population. This is an initial order recommendation only, and the ultimate responsibility for ordering the total number of parts needed to satisfy the program lies with the dealer.
ACTION REQUIRED
Replace the existing fuel injection pump group with a new 349-5736 fuel injection pump group.
Refer to appropriate service manuals as necessary.
Rework Procedure:
1. Remove machine parts as necessary to gain sufficient access to the engine.
2. Remove existing fuel injection pump and replace it with a new 349-5736 fuel injection pump group. Refer to the Disassembly & Assembly Instruction RENR9722 Fuel Injection Pump - Remove and Install.
3. Ensure that all the warnings and notices are adhered to and safety practices are followed. Ensure that the protection caps are used during this operation to prevent issues with contamination.
4. Install all parts that were removed to gain access to the engine.
5. Check for leaks and repair as necessary.
SERVICE CLAIM ALLOWANCES
Product smu/age whichever comes first Caterpillar Dealer Suggested Customer Suggested
Parts % Labor Hrs% Parts % Labor Hrs% Parts % Labor Hrs%
0-3000 hrs,
0-36 mo 100.0% 100.0% 0.0% 0.0% 0.0% 0.0%
This is a 8.0-hour job
PARTS DISPOSITION
Handle the parts in accordance with your Warranty Bulletin on warranty parts handling.