Information injection-pump assembly
ZEXEL
108822-2680
1088222680
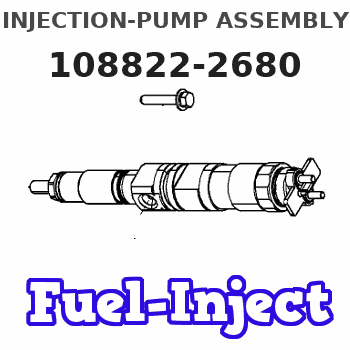
Rating:
Cross reference number
ZEXEL
108822-2680
1088222680
Zexel num
Bosch num
Firm num
Name
108822-2680
INJECTION-PUMP ASSEMBLY
Calibration Data:
Adjustment conditions
Test oil
1404 Test oil ISO4113 or {SAEJ967d}
1404 Test oil ISO4113 or {SAEJ967d}
Test oil temperature
degC
40
40
45
Nozzle and nozzle holder
105780-8250
Bosch type code
1 688 901 101
Nozzle
105780-0120
Bosch type code
1 688 901 990
Nozzle holder
105780-2190
Opening pressure
MPa
20.7
Opening pressure
kgf/cm2
211
Injection pipe
Outer diameter - inner diameter - length (mm) mm 8-3-600
Outer diameter - inner diameter - length (mm) mm 8-3-600
Overflow valve
131425-0220
Overflow valve opening pressure
kPa
157
123
191
Overflow valve opening pressure
kgf/cm2
1.6
1.25
1.95
Tester oil delivery pressure
kPa
255
255
255
Tester oil delivery pressure
kgf/cm2
2.6
2.6
2.6
PS/ACT control unit part no.
407980-2
24*
Digi switch no.
42
Direction of rotation (viewed from drive side)
Right R
Right R
Injection timing adjustment
Direction of rotation (viewed from drive side)
Right R
Right R
Injection order
1-2-7-3-
4-5-6-8
Pre-stroke
mm
8.5
8.47
8.53
Beginning of injection position
Governor side NO.1
Governor side NO.1
Difference between angles 1
Cyl.1-2 deg. 45 44.75 45.25
Cyl.1-2 deg. 45 44.75 45.25
Difference between angles 2
Cal 1-7 deg. 90 89.75 90.25
Cal 1-7 deg. 90 89.75 90.25
Difference between angles 3
Cal 1-3 deg. 135 134.75 135.25
Cal 1-3 deg. 135 134.75 135.25
Difference between angles 4
Cal 1-4 deg. 180 179.75 180.25
Cal 1-4 deg. 180 179.75 180.25
Difference between angles 5
Cal 1-5 deg. 225 224.75 225.25
Cal 1-5 deg. 225 224.75 225.25
Difference between angles 6
Cal 1-6 deg. 270 269.75 270.25
Cal 1-6 deg. 270 269.75 270.25
Difference between angles 7
Cal 1-8 deg. 315 314.75 315.25
Cal 1-8 deg. 315 314.75 315.25
Injection quantity adjustment
Adjusting point
-
Rack position
14.3
Pump speed
r/min
700
700
700
Average injection quantity
mm3/st.
148
146.4
149.6
Max. variation between cylinders
%
0
-3
3
Basic
*
Fixing the rack
*
PS407980-224*
V
2.45+-0.
01
PS407980-224*
mm
6.1+-0.0
5
Standard for adjustment of the maximum variation between cylinders
*
Injection quantity adjustment_02
Adjusting point
Z
Rack position
9+-0.5
Pump speed
r/min
355
355
355
Average injection quantity
mm3/st.
20.5
18.5
22.5
Max. variation between cylinders
%
0
-15
15
Fixing the rack
*
PS407980-224*
V
V1+0.05+
-0.01
PS407980-224*
mm
8.4+-0.0
3
Standard for adjustment of the maximum variation between cylinders
*
Remarks
Refer to items regarding the pre-stroke actuator
Refer to items regarding the pre-stroke actuator
Injection quantity adjustment_03
Adjusting point
A
Rack position
R1(14.3)
Pump speed
r/min
700
700
700
Average injection quantity
mm3/st.
148
147
149
Basic
*
Fixing the lever
*
PS407980-224*
V
2.45+-0.
01
PS407980-224*
mm
6.1+-0.0
5
Injection quantity adjustment_04
Adjusting point
B
Rack position
R1+1.35
Pump speed
r/min
1100
1100
1100
Average injection quantity
mm3/st.
143
139
147
Fixing the lever
*
PS407980-224*
V
2.45+-0.
01
PS407980-224*
mm
6.1+-0.0
5
0000001601
Pre-stroke
mm
8.5
8.47
8.53
Remarks
When the timing sleeve is pushed up
When the timing sleeve is pushed up
_02
Connector angle
deg.
8.5
8
9
Remarks
When the eccentric pin is tightened
When the eccentric pin is tightened
_03
Supply voltage
V
24
23.5
24.5
Ambient temperature
degC
23
18
28
Pre-stroke
mm
6.1
6.05
6.15
Output voltage
V
2.45
2.44
2.46
Adjustment
*
_04
Supply voltage
V
24
23.5
24.5
Ambient temperature
degC
23
18
28
Pre-stroke
mm
8.5
8.47
8.53
Output voltage
V
1.2
1
1.4
Confirmation
*
Remarks
Output voltage V1
Output voltage V1
_05
Supply voltage
V
24
23.5
24.5
Ambient temperature
degC
23
18
28
Pre-stroke
mm
5.5
Output voltage
V
3
2.98
3
Confirmation
*
_06
Supply voltage
V
24
23.5
24.5
Ambient temperature
degC
23
18
28
Output voltage
V
3.05
3.05
Confirmation of operating range
*
Test data Ex:
Governor adjustment
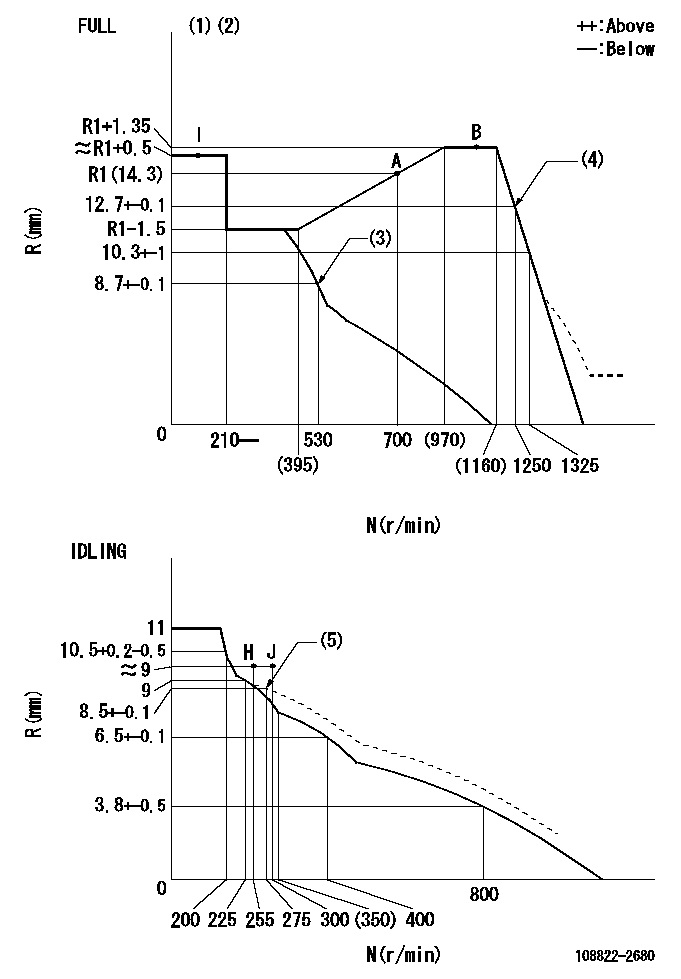
N:Pump speed
R:Rack position (mm)
(1)Torque cam stamping: T1
(2)Tolerance for racks not indicated: +-0.05mm.
(3)Air cylinder ON
(4)Air cylinder OFF
(5)Damper spring setting
----------
T1=AD96
----------
----------
T1=AD96
----------
Speed control lever angle
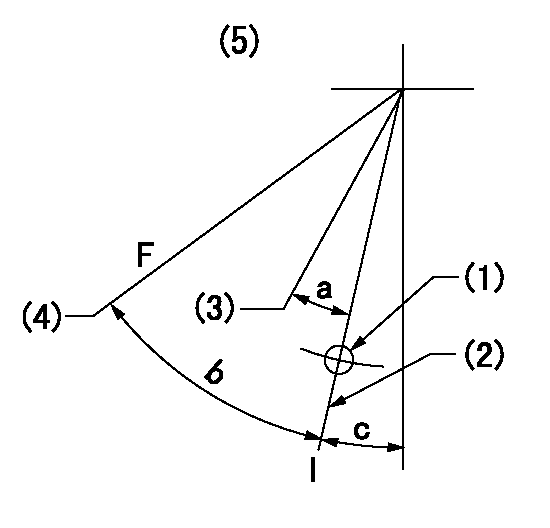
F:Full speed
I:Idle
(1)Use the hole at R = aa
(2)Stopper bolt setting
(3)When air cylinder ON.
(4)When air cylinder OFF.
(5)Viewed from feed pump side.
----------
aa=37.5mm
----------
a=(10deg) b=31deg+-3deg c=32deg+-5deg
----------
aa=37.5mm
----------
a=(10deg) b=31deg+-3deg c=32deg+-5deg
Stop lever angle
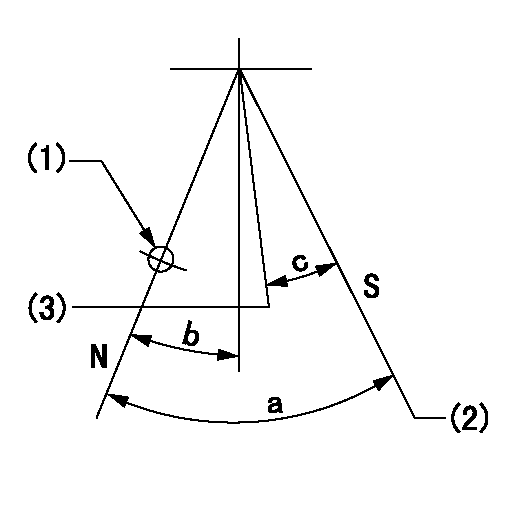
N:Pump normal
S:Stop the pump.
(1)Use the hole at R = aa
(2)Set the stopper bolt so that speed = bb and rack position = cc. (Confirm non-injection.)
(3)Normal engine position (equivalent to R = dd).
----------
aa=54mm bb=1100r/min cc=4+-0.3mm dd=18mm
----------
a=41deg+-5deg b=5.5deg+-5deg c=(31deg)
----------
aa=54mm bb=1100r/min cc=4+-0.3mm dd=18mm
----------
a=41deg+-5deg b=5.5deg+-5deg c=(31deg)
0000001301

(1)Pump vertical direction
(2)Coupling's key groove position at No 1 cylinder's beginning of injection
(3)At the No 1 cylinder's beginning of injection position, stamp an aligning mark on the damper to align with the pointer's groove.
(4)Damper
(5)Pointer
(6)B.T.D.C.: aa
(7)Pre-stroke: bb
----------
aa=6deg bb=8.5+-0.03mm
----------
a=45deg16min+-3deg b=(44deg)
----------
aa=6deg bb=8.5+-0.03mm
----------
a=45deg16min+-3deg b=(44deg)
0000001901
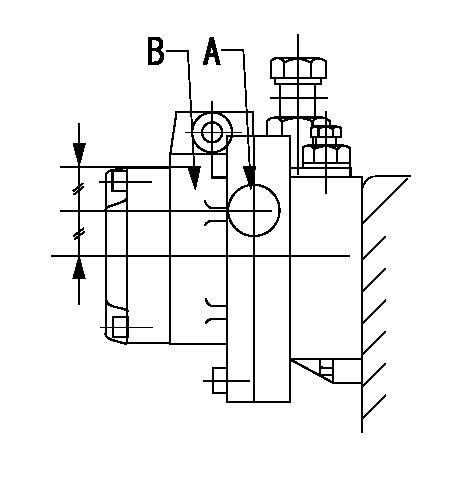
A:Sealing position
B:Pre-stroke actuator
1. When installing the pre-stroke actuator on the pump, first tighten the installation bolts loosely, then move the actuator fully counterclockwise (viewed from the drive side).
Temporary tightening torque: 1 - 1.5 N.m (0.1 - 0.15 kgf.m)
2. Move the actuator in the clockwise direction when viewed from the drive side, and adjust so that it becomes the adjustment point of the adjustment value. Then tighten it.
Tightening torque: 7^9 N.m (0.7^0.9 kgf.m)
3. After prestroke actuator installation adjustment, simultaneously stamp both the actuator side and housing side.
----------
----------
----------
----------
0000002201 RACK SENSOR
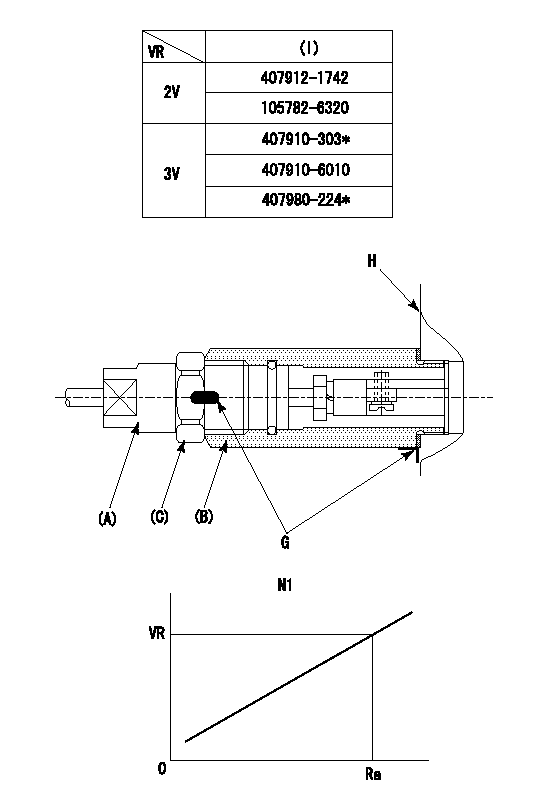
(VR) measurement voltage
(I) Part number of the control unit
(G) Apply red paint.
(H): End surface of the pump
1. Rack sensor adjustment (-0620)
(1)Fix the speed control lever at the full position
(2)Set the speed to N1 r/min.
(If the boost compensator is provided, apply boost pressure.)
(3)Adjust the bobbin (A) so that the rack sensor's output voltage is VR+-0.01.
(4)At that time, rack position must be Ra.
(5)Apply G at two places.
Connecting part between the joint (B) and the nut (F)
Connecting part between the joint (B) and the end surface of the pump (H)
----------
N1=1100r/min Ra=R1(14.3)+1.35mm
----------
----------
N1=1100r/min Ra=R1(14.3)+1.35mm
----------
0000002301 AIR CYLINDER
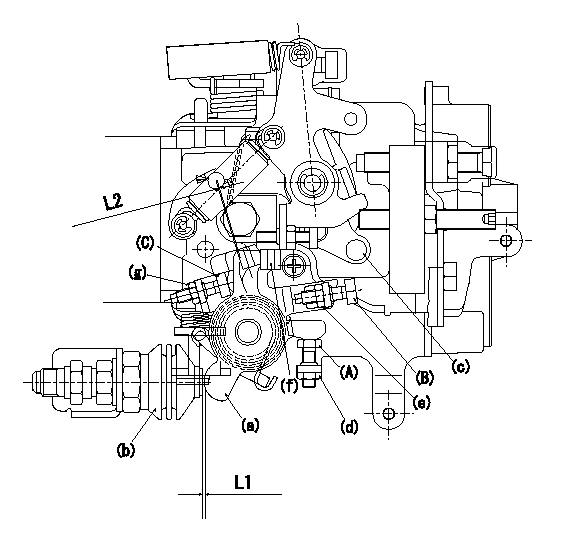
<A> stopper bolt
<B> stopper bolt
<C> stopper bolt
(a) lever
(b) air cylinder
(c) speed lever
(d) Nut
(e) nut
(f) lever
(g) nut
1. Stopper bolt <A> adjustment method
(1)When air cylinder pressure is P1, set the gap between the lever (a) and the air cylinder (b) to L1.
(2)Confirm that the speed lever (c) operates between idling and full speed.
(3)Fix stopper bolt <A> using nut (d).
2. Stopper bolt <B> adjustment method.
(1)At air cylinder pressure P2, pump speed N1 and rack position is R1, adjust stopper bolt (B) so that the speed lever (c) is in the stop position.
(2)Turn the stopper bolt (c) so that the clearance between lever (a) and lever (f) is L2, then fix using nut (g).
(3)Move the lever (a) several times and fix stopper bolt <B> using the nut (e).
(4)Tightening torque T1 for nuts (d), (e) and (g)
----------
L1=0.2++mm L2=0~1.5mm P1=0kPa(0kgf/cm2) P2=686+98kpa(7+1kgf/cm2) N1=530r/min R1=8.7+-0.1mm T1=4.9~6.86N-m(0.5~0.7kgf-m)
----------
----------
L1=0.2++mm L2=0~1.5mm P1=0kPa(0kgf/cm2) P2=686+98kpa(7+1kgf/cm2) N1=530r/min R1=8.7+-0.1mm T1=4.9~6.86N-m(0.5~0.7kgf-m)
----------
Information:
(1) Remove the plug in the dash and install 3T306 Starting Aid Switch (1). Connect two purple wires (2), from the wiring harness, to switch (1).(2) On machines with a bulldozer, remove two nuts (3), washers and bolts. Remove two bolts (4) and washers. Remove bracket (5) from bracket (6). (3) Put 7G6359 Box Assembly (7) in position and install two 5F4899 Bolts (8) and 5M2894 Washers. Install two S1594 Bolts (9), 5P1075 Washers and 1D4717 Nuts to hold box assembly (7) to bracket (6). Install 4M7470 Grommet in hole (A).(4) Put the wires of 6N7674 Valve Assembly (10) through hole (A) and install valve assembly (10) on box assembly (7) with two S1617 Bolts (11), 5P4116 Washers and 1D4716 Nuts. Install 7N2059 Clamp Assembly (12) with two S1617 Bolts, 5P4116 Washers and 1D4716 Nuts. Install 63801 Washer (13) on 6D1746 Bolt (14). Put bolt (14) in position in cover (15) and install L1365 Washer (16) on bolt (14). Install 3B4610 Cotter Pin (17) in bolt (14). (5) Remove the plug from the manifold and install 6N9995 Atomizer Assembly (18) as shown. The orifices of the atomizer must be toward each end of the manifold. Install 5P7907 Connector (19) in valve assembly (10). Connect 9G941 Tube (20) to atomizer assembly (18). Use 5P6314 Sleeve (21) and 5P6313 Nut (22) to connect tube (20) to connector (19). Remove the plug from the bypass elbow of the water lines group and install 6N5899 Switch (23). Connect 9G6560 Wire Assembly (24) to switch (23) and to valve assembly (10). Connect 9G6561 Wire Assembly (25) to valve assembly (10) and to the purple wire, from the starting aid switch, at the rear of the engine. Use former clips (26) to hold wire assemblies (24) and (25) in position.(6) Remove cap (27) from valve assembly (10) and install a 7N296 Cylinder Assembly. (7) For machines without bulldozer lines, remove the two bolts from the cylinder head and put 7G6359 Box Assembly (7) in position. Install two 5F4899 Bolts (8) and 5M2894 Washers. Remove the bolt from the exhaust manifold and put 3T1685 Bracket (27) in position. Install L2070 Bolt (28), 5M2894 Washer and 1D4717 Nut. Install two S1594 Bolts (9), 5P1075 Washers and 1D4717 Nuts. Install the 4M7470 Grommet in hole (A), see Step 3. Follow Steps 1, 4, 5 and 6 for installation of the group.
Have questions with 108822-2680?
Group cross 108822-2680 ZEXEL
Mitsubishi
Mitsubishi
Mitsubishi
Mitsubishi
Mitsubishi
Mitsubishi
Mitsubishi
Mitsubishi
108822-2680
INJECTION-PUMP ASSEMBLY