Information injection-pump assembly
ZEXEL
108822-2080
1088222080
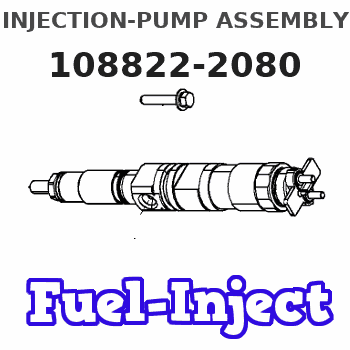
Rating:
Cross reference number
ZEXEL
108822-2080
1088222080
Zexel num
Bosch num
Firm num
Name
108822-2080
INJECTION-PUMP ASSEMBLY
14CQ TICS HD-TI8F TICS
14CQ TICS HD-TI8F TICS
Calibration Data:
Adjustment conditions
Test oil
1404 Test oil ISO4113 or {SAEJ967d}
1404 Test oil ISO4113 or {SAEJ967d}
Test oil temperature
degC
40
40
45
Nozzle and nozzle holder
105780-8250
Bosch type code
1 688 901 101
Nozzle
105780-0120
Bosch type code
1 688 901 990
Nozzle holder
105780-2190
Opening pressure
MPa
20.7
Opening pressure
kgf/cm2
211
Injection pipe
Outer diameter - inner diameter - length (mm) mm 8-3-600
Outer diameter - inner diameter - length (mm) mm 8-3-600
Overflow valve
131425-0220
Overflow valve opening pressure
kPa
157
123
191
Overflow valve opening pressure
kgf/cm2
1.6
1.25
1.95
Tester oil delivery pressure
kPa
255
255
255
Tester oil delivery pressure
kgf/cm2
2.6
2.6
2.6
RED3 control unit part number
407910-2
470
RED3 rack sensor specifications
mm
15
PS/ACT control unit part no.
407980-2
24*
Digi switch no.
42
Direction of rotation (viewed from drive side)
Right R
Right R
Injection timing adjustment
Direction of rotation (viewed from drive side)
Right R
Right R
Injection order
1-2-7-3-
4-5-6-8
Pre-stroke
mm
8.5
8.47
8.53
Beginning of injection position
Governor side NO.1
Governor side NO.1
Difference between angles 1
Cyl.1-2 deg. 45 44.75 45.25
Cyl.1-2 deg. 45 44.75 45.25
Difference between angles 2
Cal 1-7 deg. 90 89.75 90.25
Cal 1-7 deg. 90 89.75 90.25
Difference between angles 3
Cal 1-3 deg. 135 134.75 135.25
Cal 1-3 deg. 135 134.75 135.25
Difference between angles 4
Cal 1-4 deg. 180 179.75 180.25
Cal 1-4 deg. 180 179.75 180.25
Difference between angles 5
Cal 1-5 deg. 225 224.75 225.25
Cal 1-5 deg. 225 224.75 225.25
Difference between angles 6
Cal 1-6 deg. 270 269.75 270.25
Cal 1-6 deg. 270 269.75 270.25
Difference between angles 7
Cal 1-8 deg. 315 314.75 315.25
Cal 1-8 deg. 315 314.75 315.25
Injection quantity adjustment
Rack position
(11.5)
Vist
V
1.69
1.69
1.69
Pump speed
r/min
700
700
700
Average injection quantity
mm3/st.
127.5
126.5
128.5
Max. variation between cylinders
%
0
-3
3
Basic
*
PS407980-224*
V
2.45+-0.
01
PS407980-224*
mm
6.1+-0.0
5
Injection quantity adjustment_02
Rack position
(7.4)
Vist
V
2.5
2.4
2.6
Pump speed
r/min
340
340
340
Average injection quantity
mm3/st.
23.5
20.9
26.1
Max. variation between cylinders
%
0
-15
15
PS407980-224*
V
V1+0.05+
-0.01
PS407980-224*
mm
8.4+-0.0
3
Remarks
Refer to items regarding the pre-stroke actuator
Refer to items regarding the pre-stroke actuator
0000001201
Pre-stroke
mm
8.5
8.47
8.53
Remarks
When the timing sleeve is pushed up
When the timing sleeve is pushed up
_02
Connector angle
deg.
8.5
8
9
Remarks
When the eccentric pin is tightened
When the eccentric pin is tightened
_03
Supply voltage
V
24
23.5
24.5
Ambient temperature
degC
23
18
28
Pre-stroke
mm
6.1
6.05
6.15
Output voltage
V
2.45
2.44
2.46
Adjustment
*
_04
Supply voltage
V
24
23.5
24.5
Ambient temperature
degC
23
18
28
Pre-stroke
mm
8.5
8.47
8.53
Output voltage
V
1.2
1
1.4
Confirmation
*
Remarks
Output voltage V1
Output voltage V1
_05
Supply voltage
V
24
23.5
24.5
Ambient temperature
degC
23
18
28
Pre-stroke
mm
5.5
Output voltage
V
3
2.98
3
Confirmation
*
_06
Supply voltage
V
24
23.5
24.5
Ambient temperature
degC
23
18
28
Output voltage
V
3.05
3.05
Confirmation of operating range
*
Test data Ex:
Speed control lever angle

N:Pump normal
S:Stop the pump.
(1)Rack position = aa
(2)Rack position bb
----------
aa=16mm bb=1mm
----------
a=19deg+-5deg b=29deg+-5deg
----------
aa=16mm bb=1mm
----------
a=19deg+-5deg b=29deg+-5deg
0000000901

(1)Pump vertical direction
(2)Coupling's key groove position at No 1 cylinder's beginning of injection
(3)At the No 1 cylinder's beginning of injection position, stamp an aligning mark on the damper to align with the pointer's groove.
(4)Damper
(5)Pointer
(6)B.T.D.C.: aa
(7)Pre-stroke: bb
----------
aa=4deg bb=8.5+-0.03mm
----------
a=(45deg) b=(44deg)
----------
aa=4deg bb=8.5+-0.03mm
----------
a=(45deg) b=(44deg)
0000001501
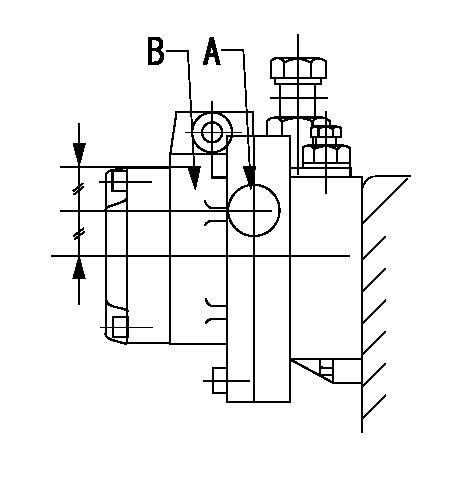
A:Sealing position
B:Pre-stroke actuator
1. When installing the pre-stroke actuator on the pump, first tighten the installation bolts loosely, then move the actuator fully counterclockwise (viewed from the drive side).
Temporary tightening torque: 1 - 1.5 N.m (0.1 - 0.15 kgf.m)
2. Move the actuator in the clockwise direction when viewed from the drive side, and adjust so that it becomes the adjustment point of the adjustment value. Then tighten it.
Tightening torque: 7^9 N.m (0.7^0.9 kgf.m)
3. After prestroke actuator installation adjustment, simultaneously stamp both the actuator side and housing side.
----------
----------
----------
----------
0000001701

(Rs) rack sensor specifications
(C/U) control unit part number
(V) Rack sensor output voltage
(R) Rack position (mm)
1. Confirming governor output characteristics (rack 15 mm, span 6 mm)
(1)When the output voltages of the rack sensor are V1 and V2, check that the rack positions R1 and R2 in the table above are satisfied.
----------
----------
----------
----------
0000001901 RACK SENSOR

(VR) measurement voltage
(I) Part number of the control unit
(G) Apply red paint.
(H): End surface of the pump
1. Rack sensor adjustment (154610-0620)
(1)At governor side rack sensor output voltage V1, adjust the bobbin (A) so that the drive side rack sensor output voltage is VR+-0.01.
(2)Apply G at two places.
Connecting part between the joint (B) and the nut (F)
Connecting part between the joint (B) and the end surface of the pump (H)
----------
V1=1V
----------
----------
V1=1V
----------
Information:
External LeaksPressurize the cooling system using the 9S8140 Cooling System Pressurizing Pump Group and check the following:1. Leaks In Hoses Or Connections Check all hoses and connections for visual signs of leakage. If no leaks are found, look for damage to hoses or loose hose clamps. Also, check for leaks in accessories such as fuel heaters and transmission oil coolers.2. Leaks In The Radiator3. Leaks In The Heater4. Leaks In The Water Pump Check the water pump for leaks before starting the engine, then start the engine and look for leaks. If there are leaks at the water pump, repair the pump or install a new pump.5. Cylinder Head Gasket Leaks Look for leaks along the surface of the cylinder head gasket. If leaks are found, remove the cylinder head and install a new head gasket. Coolant Leaks At The Overflow Tube6. Defective Pressure Cap Or Relief Valve Check the sealing surfaces of the pressure cap and the radiator to be sure the cap is sealing correctly. Check the opening pressure and sealing ability of the pressure cap or relief valve with the 9S8140 Cooling System Pressurizing Pump Group.7. Engine Runs Too Hot If coolant temperature is too high, pressure will be high enough to move the cap off of the sealing surface in the radiator and cause coolant loss through the overflow tube. If this occurs, refer to the portion, Overheating, of the topic, Abnormal Cooling System.8. Air/Combustion Gas In The Cooling System Air/Combustion Gas in the cooling system reduces the heat transfer from hot engine parts to the coolant and causes low coolant flow. The most common causes of air are: * Improper filling of the cooling system trapping air in the system.* Combustion gas leaking into the system. If air/combustion gas is present in the cooling system, the engine should be checked for internal cracks (cylinder head, injector sleeve, cylinder liner) or for a defective cylinder head gasket.The cooling system can be checked for air using the BOTTLE TEST. The equipment needed to do this test is a one pint bottle, a bucket of water, and a hose which will fit the end of the overflow pipe of the radiator. Before testing, be sure the cooling system is filled correctly. Use a wire to hold the relief valve in the radiator cap open. Put the hose over the end of the overflow pipe. Start the engine and operate it at high idle rpm for a minimum of five minutes after the engine is at normal operating temperature. After five or more minutes at operating temperature, place the loose end of the hose in the bottle filled with water. If the water gets out of the bottle in less than forty seconds, there is too much exhaust gas leakage into the cooling system. Find the cause of the air or gas getting into the cooling system and correct as necessary. Internal LeakageIf coolant is found in the engine oil check the following internal components
Have questions with 108822-2080?
Group cross 108822-2080 ZEXEL
Mitsubishi
Mitsubishi
Mitsubishi
Mitsubishi
Mitsubishi
Mitsubishi
108822-2080
INJECTION-PUMP ASSEMBLY