Information injection-pump assembly
BOSCH
9 400 619 229
9400619229
ZEXEL
108821-0060
1088210060
NISSAN-DIESEL
1680197605
1680197605

Rating:
Service parts 108821-0060 INJECTION-PUMP ASSEMBLY:
1.
_
7.
COUPLING PLATE
9.
_
11.
Nozzle and Holder
12.
Open Pre:MPa(Kqf/cm2)
13.7(140)/16.7(170)
15.
NOZZLE SET
Include in #1:
108821-0060
as INJECTION-PUMP ASSEMBLY
Cross reference number
BOSCH
9 400 619 229
9400619229
ZEXEL
108821-0060
1088210060
NISSAN-DIESEL
1680197605
1680197605
Zexel num
Bosch num
Firm num
Name
Calibration Data:
Adjustment conditions
Test oil
1404 Test oil ISO4113 or {SAEJ967d}
1404 Test oil ISO4113 or {SAEJ967d}
Test oil temperature
degC
40
40
45
Nozzle and nozzle holder
105780-8250
Bosch type code
1 688 901 101
Nozzle
105780-0120
Bosch type code
1 688 901 990
Nozzle holder
105780-2190
Opening pressure
MPa
20.7
Opening pressure
kgf/cm2
211
Injection pipe
Outer diameter - inner diameter - length (mm) mm 8-3-600
Outer diameter - inner diameter - length (mm) mm 8-3-600
Overflow valve
134424-4120
Overflow valve opening pressure
kPa
255
221
289
Overflow valve opening pressure
kgf/cm2
2.6
2.25
2.95
Tester oil delivery pressure
kPa
255
255
255
Tester oil delivery pressure
kgf/cm2
2.6
2.6
2.6
RED4 control unit part number
407915-0
590
RED4 rack sensor specifications
mm
19
PS/ACT control unit part no.
407980-2
24*
Digi switch no.
41
Direction of rotation (viewed from drive side)
Right R
Right R
Injection timing adjustment
Direction of rotation (viewed from drive side)
Right R
Right R
Injection order
1-8-7-5-
4-3-6-2
Pre-stroke
mm
6.4
6.37
6.43
Beginning of injection position
Governor side NO.1
Governor side NO.1
Difference between angles 1
Cal 1-8 deg. 45 44.75 45.25
Cal 1-8 deg. 45 44.75 45.25
Difference between angles 2
Cal 1-7 deg. 90 89.75 90.25
Cal 1-7 deg. 90 89.75 90.25
Difference between angles 3
Cal 1-5 deg. 135 134.75 135.25
Cal 1-5 deg. 135 134.75 135.25
Difference between angles 4
Cal 1-4 deg. 180 179.75 180.25
Cal 1-4 deg. 180 179.75 180.25
Difference between angles 5
Cal 1-3 deg. 225 224.75 225.25
Cal 1-3 deg. 225 224.75 225.25
Difference between angles 6
Cal 1-6 deg. 270 269.75 270.25
Cal 1-6 deg. 270 269.75 270.25
Difference between angles 7
Cyl.1-2 deg. 315 314.75 315.25
Cyl.1-2 deg. 315 314.75 315.25
Injection quantity adjustment
Rack position
(12.2)
PWM
%
56.8
Pump speed
r/min
600
600
600
Average injection quantity
mm3/st.
131
129
133
Max. variation between cylinders
%
0
-4
4
Basic
*
PS407980-224*
V
2.2+-0.0
1
PS407980-224*
mm
4+-0.05
Injection quantity adjustment_02
Rack position
(7.6)
PWM
%
30.9+-2.
8
Pump speed
r/min
295
295
295
Average injection quantity
mm3/st.
16.5
14.5
18.5
Max. variation between cylinders
%
0
-10
10
PS407980-224*
V
V1+0.05+
-0.01
PS407980-224*
mm
6.3+-0.0
3
Remarks
Refer to items regarding the pre-stroke actuator
Refer to items regarding the pre-stroke actuator
Governor adjustment
Pump speed
r/min
750--
Advance angle
deg.
0
0
0
Remarks
Start
Start
Governor adjustment_02
Pump speed
r/min
700
Advance angle
deg.
0.5
Governor adjustment_03
Pump speed
r/min
1000
Advance angle
deg.
3
2.5
3.5
Remarks
Finish
Finish
0000001201
Pre-stroke
mm
6.4
6.37
6.43
Remarks
When the timing sleeve is pushed up
When the timing sleeve is pushed up
_02
Connector angle
deg.
11.5
11
12
Remarks
When the eccentric pin is tightened
When the eccentric pin is tightened
_03
Supply voltage
V
24
23.5
24.5
Ambient temperature
degC
23
18
28
Pre-stroke
mm
2.4
2.35
2.45
Output voltage
V
2.95
2.94
2.96
Adjustment
*
_04
Supply voltage
V
24
23.5
24.5
Ambient temperature
degC
23
18
28
Pre-stroke
mm
6.4
6.37
6.43
Output voltage
V
1.2
1
1.4
Confirmation
*
Remarks
Output voltage V1
Output voltage V1
_05
Supply voltage
V
24
23.5
24.5
Ambient temperature
degC
23
18
28
Output voltage
V
3.05
3.05
Confirmation of operating range
*
Test data Ex:
Speed control lever angle

N:Pump normal
S:Stop the pump.
(1)Rack position = aa
(2)Rack position bb
----------
aa=20mm bb=1mm
----------
a=27deg+-5deg b=37deg+-5deg
----------
aa=20mm bb=1mm
----------
a=27deg+-5deg b=37deg+-5deg
0000000901
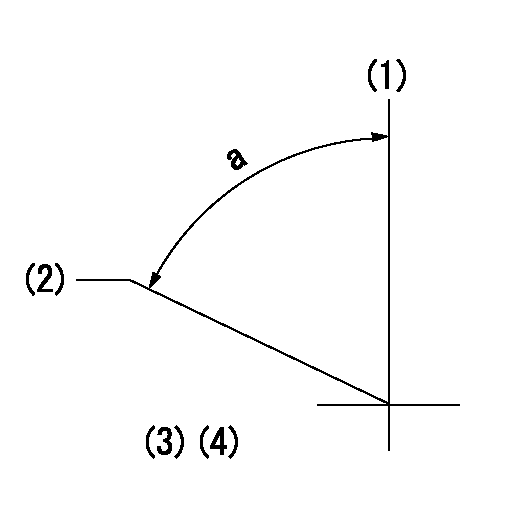
(1)Pump vertical direction
(2)Position of the coupling's key groove at the beginning of injection of the No. 8 cylinder.
(3)Pre-stroke: aa
(4)-
----------
aa=6.4+-0.03mm
----------
a=(80deg)
----------
aa=6.4+-0.03mm
----------
a=(80deg)
0000001501
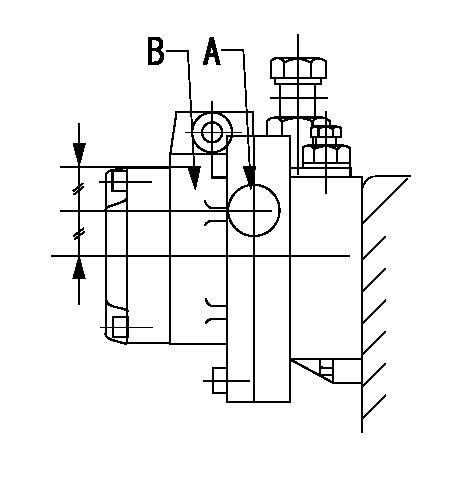
A:Sealing position
B:Pre-stroke actuator
1. When installing the pre-stroke actuator on the pump, first tighten the installation bolts loosely, then move the actuator fully counterclockwise (viewed from the drive side).
Temporary tightening torque: 1 - 1.5 N.m (0.1 - 0.15 kgf.m)
2. Move the actuator in the clockwise direction when viewed from the drive side, and adjust so that it becomes the adjustment point of the adjustment value. Then tighten it.
Tightening torque: 7^9 N.m (0.7^0.9 kgf.m)
3. After prestroke actuator installation adjustment, simultaneously stamp both the actuator side and housing side.
----------
----------
----------
----------
0000001701

(PWM) Pulse width modulation (%)
(R) Rack position (mm)
Rack sensor output characteristics
1. Rack limit adjustment
(1)Measure the rack position R2 for PWM a2%.
(2)Confirm that it is within the range R2 = 15+-1 mm.
(3)Measure the rack position R1 at PWM a %.
(4)Confirm that it is within the range R2 - R1 = 10+-0.1 mm.
2. Check the limp home operation.
(1)Move the switch box's limp home switch to the limp home side.
(2)Confirm rack position L1 (mm ) and L2 (mm) for PWM in the above table.
3. Check the pull down operation.
(1)Confirm that the rack position is 19 mm at PWM B%.
(2)In the conditions described in the above table, move the switch box's pull down switch to the pull down side and confirm that the rack position momentarily becomes 1 mm or less.
----------
a1=16.25% a2=72.5% L1=1--mm L2=19++mm A=5% B=95%
----------
----------
a1=16.25% a2=72.5% L1=1--mm L2=19++mm A=5% B=95%
----------
Information:
789 Truck
On the 789 Truck, there are two mounting plates and two sets of ether nozzles, both of which are mounted on the frame cross tube in the engine compartment. 1. Install 8X0913 Tube (63) in the front nozzle, and 8W8177 Tube (65) in the rear nozzle of the front pair of turbocharger outlet adapters as shown.2. Use two 5P6314 Sleeves with 5P6313 Nuts to connect tubes (63) and (65) to 8C9006 Tee (64).3. Put 8X5015 Tube (60) in position along the cylinder block and frame cross tube (59). Use a 5P6314 Sleeve and a 5P6313 Nut to connect tube (60) to 8C9006 Tee (64) as shown.4. Connect one end of a 7N0140 Tube Assembly in the bottom of the shuttle valve on the right side mounting plate (62) to the free end of 8X5015 Tube (60).5. Use three 6V2686 Clips (61), with existing bolts on the engine cylinder block and truck frame cross tube (59), to secure 8X5015 Tube (60) as shown.6. Install 8W8179 Tube (66) in the front nozzle and 8W8180 Tube (67) in the rear nozzle of the rear pair of turbocharger outlet adapters as shown.7. Use two 5P6314 Sleeves with 5P6313 Nuts to connect tubes (66) and (67) to 8C9006 Tee (68).8. Use two 6V2686 Clips (61) with existing bolts to secure 8W8180 Tube (67) to the engine block as shown.9. Put 8W8178 Tube (69) in position along the cylinder block and connect it to 8C9006 Tee (68) as shown using a 5P6314 Sleeve and 5P6313 Nut.10. Connect one end of a 7N0140 Tube Assembly in the bottom connector of the shuttle valve on left side mounting plate (70) to the free end of the 8W8178 Tube (69).11. Use three 6V2686 Clips (61) with existing bolts on engine cylinder block to secure 8W8178 Tube (69) as shown.Installation of Ether Cylinders
1. Turn the disconnect switch to the ON position and put the start switch key in the OFF position. Make sure the two lamps on the console and the two yellow LEDs on the ECU are flashing.If they are flashing, it indicates that the control is functioning and recognizes that no ether cylinders are installed.2. Inspect the two digit, seven segment LED display on the ECU. It must read "00". This in an indication that there are no faults.If the display does not read "00", refer to the Service Manual, SENR4705, for a troubleshooting procedure of the system. 3. Remove protective caps (71) and (72) from 9X7137 Ether Solenoid Valves (73) and (74) (left side ether assembly mounting plate on 789 Truck when viewed from the rear of the engine). Install a new 9X7138 Filter Assembly in each solenoid valve inlet if one is not already in place.4. Install a 9X0147 Collar on the neck of each new 7X1062 Ether Cylinder.5. Remove the protective plug from the end of the new FULL ether cylinder, then install the new ether cylinder for ether
On the 789 Truck, there are two mounting plates and two sets of ether nozzles, both of which are mounted on the frame cross tube in the engine compartment. 1. Install 8X0913 Tube (63) in the front nozzle, and 8W8177 Tube (65) in the rear nozzle of the front pair of turbocharger outlet adapters as shown.2. Use two 5P6314 Sleeves with 5P6313 Nuts to connect tubes (63) and (65) to 8C9006 Tee (64).3. Put 8X5015 Tube (60) in position along the cylinder block and frame cross tube (59). Use a 5P6314 Sleeve and a 5P6313 Nut to connect tube (60) to 8C9006 Tee (64) as shown.4. Connect one end of a 7N0140 Tube Assembly in the bottom of the shuttle valve on the right side mounting plate (62) to the free end of 8X5015 Tube (60).5. Use three 6V2686 Clips (61), with existing bolts on the engine cylinder block and truck frame cross tube (59), to secure 8X5015 Tube (60) as shown.6. Install 8W8179 Tube (66) in the front nozzle and 8W8180 Tube (67) in the rear nozzle of the rear pair of turbocharger outlet adapters as shown.7. Use two 5P6314 Sleeves with 5P6313 Nuts to connect tubes (66) and (67) to 8C9006 Tee (68).8. Use two 6V2686 Clips (61) with existing bolts to secure 8W8180 Tube (67) to the engine block as shown.9. Put 8W8178 Tube (69) in position along the cylinder block and connect it to 8C9006 Tee (68) as shown using a 5P6314 Sleeve and 5P6313 Nut.10. Connect one end of a 7N0140 Tube Assembly in the bottom connector of the shuttle valve on left side mounting plate (70) to the free end of the 8W8178 Tube (69).11. Use three 6V2686 Clips (61) with existing bolts on engine cylinder block to secure 8W8178 Tube (69) as shown.Installation of Ether Cylinders
1. Turn the disconnect switch to the ON position and put the start switch key in the OFF position. Make sure the two lamps on the console and the two yellow LEDs on the ECU are flashing.If they are flashing, it indicates that the control is functioning and recognizes that no ether cylinders are installed.2. Inspect the two digit, seven segment LED display on the ECU. It must read "00". This in an indication that there are no faults.If the display does not read "00", refer to the Service Manual, SENR4705, for a troubleshooting procedure of the system. 3. Remove protective caps (71) and (72) from 9X7137 Ether Solenoid Valves (73) and (74) (left side ether assembly mounting plate on 789 Truck when viewed from the rear of the engine). Install a new 9X7138 Filter Assembly in each solenoid valve inlet if one is not already in place.4. Install a 9X0147 Collar on the neck of each new 7X1062 Ether Cylinder.5. Remove the protective plug from the end of the new FULL ether cylinder, then install the new ether cylinder for ether