Information injection-pump assembly
BOSCH
9 400 611 865
9400611865
ZEXEL
108622-3785
1086223785
HINO
220401581G
220401581g
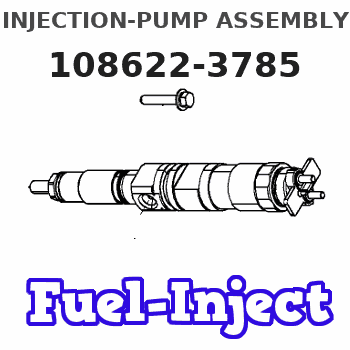
Rating:
Service parts 108622-3785 INJECTION-PUMP ASSEMBLY:
1.
_
5.
AUTOM. ADVANCE MECHANIS
9.
_
11.
Nozzle and Holder
23600-2181C
12.
Open Pre:MPa(Kqf/cm2)
16.7{170}/27.5{280}
14.
NOZZLE
Include in #1:
108622-3785
as INJECTION-PUMP ASSEMBLY
Cross reference number
BOSCH
9 400 611 865
9400611865
ZEXEL
108622-3785
1086223785
HINO
220401581G
220401581g
Zexel num
Bosch num
Firm num
Name
Calibration Data:
Adjustment conditions
Test oil
1404 Test oil ISO4113 or {SAEJ967d}
1404 Test oil ISO4113 or {SAEJ967d}
Test oil temperature
degC
40
40
45
Nozzle and nozzle holder
105780-8250
Bosch type code
1 688 901 101
Nozzle
105780-0120
Bosch type code
1 688 901 990
Nozzle holder
105780-2190
Opening pressure
MPa
20.7
Opening pressure
kgf/cm2
211
Injection pipe
Outer diameter - inner diameter - length (mm) mm 8-3-600
Outer diameter - inner diameter - length (mm) mm 8-3-600
Overflow valve
134424-4120
Overflow valve opening pressure
kPa
255
221
289
Overflow valve opening pressure
kgf/cm2
2.6
2.25
2.95
Tester oil delivery pressure
kPa
255
255
255
Tester oil delivery pressure
kgf/cm2
2.6
2.6
2.6
RED3 control unit part number
407910-3
960
RED3 rack sensor specifications
mm
19
PS/ACT control unit part no.
407980-2
24*
Digi switch no.
33
Direction of rotation (viewed from drive side)
Right R
Right R
Injection timing adjustment
Direction of rotation (viewed from drive side)
Right R
Right R
Injection order
1-4-2-6-
3-5
Pre-stroke
mm
6.4
6.37
6.43
Beginning of injection position
Drive side NO.1
Drive side NO.1
Difference between angles 1
Cal 1-4 deg. 60 59.75 60.25
Cal 1-4 deg. 60 59.75 60.25
Difference between angles 2
Cyl.1-2 deg. 120 119.75 120.25
Cyl.1-2 deg. 120 119.75 120.25
Difference between angles 3
Cal 1-6 deg. 180 179.75 180.25
Cal 1-6 deg. 180 179.75 180.25
Difference between angles 4
Cal 1-3 deg. 240 239.75 240.25
Cal 1-3 deg. 240 239.75 240.25
Difference between angles 5
Cal 1-5 deg. 300 299.75 300.25
Cal 1-5 deg. 300 299.75 300.25
Injection quantity adjustment
Rack position
(12.7)
Vist
V
1.94
1.94
1.94
Pump speed
r/min
700
700
700
Average injection quantity
mm3/st.
141.5
139.5
143.5
Max. variation between cylinders
%
0
-2
2
Basic
*
PS407980-224*
V
2.2+-0.0
1
PS407980-224*
mm
4+-0.05
Injection quantity adjustment_02
Rack position
(7.1)
Vist
V
2.8
2.7
2.9
Pump speed
r/min
300
300
300
Average injection quantity
mm3/st.
21
20
22
Max. variation between cylinders
%
0
-15
15
PS407980-224*
V
V1+0.05+
-0.01
PS407980-224*
mm
6.3+-0.0
3
Remarks
Refer to items regarding the pre-stroke actuator
Refer to items regarding the pre-stroke actuator
0000001201
Pre-stroke
mm
6.4
6.37
6.43
Remarks
When the timing sleeve is pushed up
When the timing sleeve is pushed up
_02
Connector angle
deg.
11.5
11
12
Remarks
When the eccentric pin is tightened
When the eccentric pin is tightened
_03
Supply voltage
V
24
23.5
24.5
Ambient temperature
degC
23
18
28
Pre-stroke
mm
2.4
2.35
2.45
Output voltage
V
2.95
2.94
2.96
Adjustment
*
_04
Supply voltage
V
24
23.5
24.5
Ambient temperature
degC
23
18
28
Pre-stroke
mm
6.4
6.37
6.43
Output voltage
V
1.2
1
1.4
Confirmation
*
Remarks
Output voltage V1
Output voltage V1
_05
Supply voltage
V
24
23.5
24.5
Ambient temperature
degC
23
18
28
Output voltage
V
3.05
3.05
Confirmation of operating range
*
Test data Ex:
Speed control lever angle

N:Pump normal
S:Stop the pump.
(1)Rack position = aa
(2)Rack position bb
----------
aa=20mm bb=1mm
----------
a=32.5deg+-5deg b=37deg+-5deg
----------
aa=20mm bb=1mm
----------
a=32.5deg+-5deg b=37deg+-5deg
0000000901
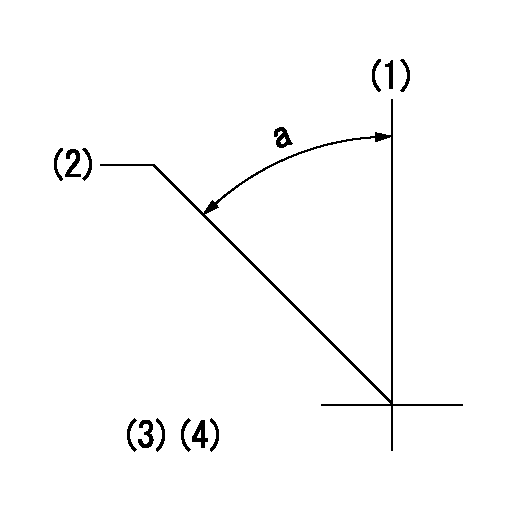
(1)Pump vertical direction
(2)Coupling's key groove position at No 1 cylinder's beginning of injection
(3)Pre-stroke: aa
(4)-
----------
aa=6.4+-0.03mm
----------
a=(40deg)
----------
aa=6.4+-0.03mm
----------
a=(40deg)
0000001501
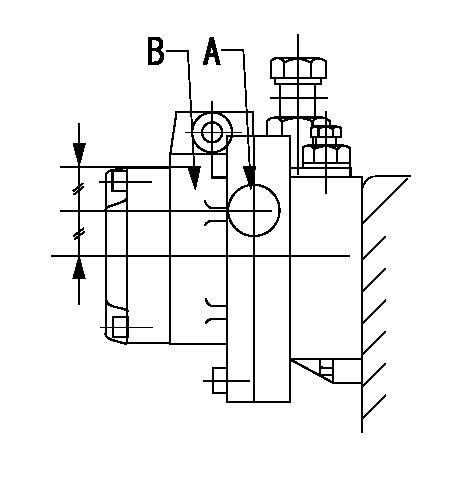
A:Sealing position
B:Pre-stroke actuator
1. When installing the pre-stroke actuator on the pump, first tighten the installation bolts loosely, then move the actuator fully counterclockwise (viewed from the drive side).
Temporary tightening torque: 1 - 1.5 N.m (0.1 - 0.15 kgf.m)
2. Move the actuator in the clockwise direction when viewed from the drive side, and adjust so that it becomes the adjustment point of the adjustment value. Then tighten it.
Tightening torque: 7^9 N.m (0.7^0.9 kgf.m)
3. After prestroke actuator installation adjustment, simultaneously stamp both the actuator side and housing side.
----------
----------
----------
----------
0000001701
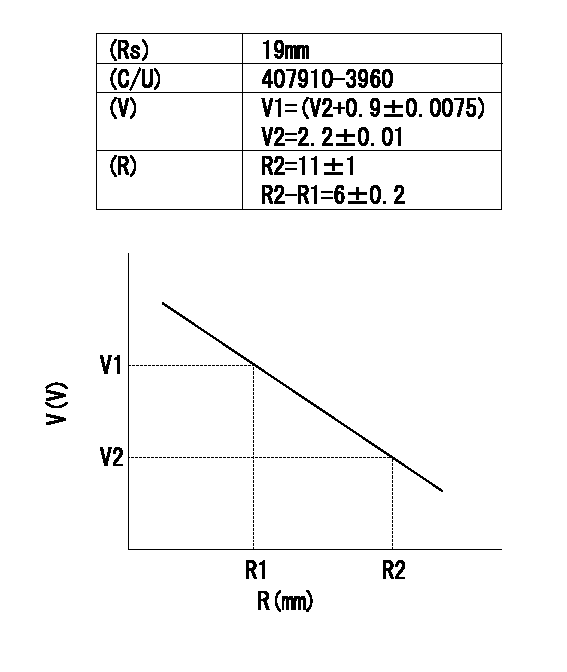
(Rs) rack sensor specifications
(C/U) control unit part number
(V) Rack sensor output voltage
(R) Rack position (mm)
1. Confirming governor output characteristics (rack 19 mm, span 6 mm)
(1)When the output voltages of the rack sensor are V1 and V2, check that the rack positions R1 and R2 in the table above are satisfied.
----------
----------
----------
----------
Information:
Regular service intervals, along with close daily visual inspection and the adherence to the instructions and schedules, will assure many hours of trouble-free service. If correction steps are taken immediately on discovery of any abnormal condition, fewer forced stops and more economical operation will result.The Lubrication and Maintenance Chart is intended as a guide and adjustments in the schedule may be necessary, depending on conditions under which the engine is operating. A thorough analysis should be made before adjusting the maintenance schedule.Some items to consider in establishing a new schedule are: Severe dust or dirty conditions, fuel consumption (a good measurement to establish intervals as it indicates the amount of work performed). As a guideline, the 3408 Engine with a 12 gal. (45 litre) (10 imp. gal.) capacity crankcase will use approximately 4000 gal. (15,000 litre) (3332 imp. gal.) between oil changes.* The 3412 Engine with a 16 gal. (60.5 litre) (13 imp. gal.) capacity crankcase will use approximately 5100 gal. (19,200 litre) (4248 imp. gal.) between oil changes. *Reducing or extending the maintenance intervals should be done only after complete study and enough time to gain adequate experience to meet specific operations.*With 0.5% or less fuel sulphur content.Caterpillar scheduled oil sampling: Scheduled oil sampling is a program which analyzes oil samples taken from an engine at regular intervals (usually at oil change periods). This oil analysis does not indicate the condition of the oil; but rather, it is a scheduled procedure to determine engine condition at regular intervals by analyzing lubricating oil for foreign and wear particles.The scheduled oil sampling will give the following benefits:It assures the owner that maintenance has been performed.It will show the first signs of excessive wear, meaning a possible upcoming failure, allowing time for a scheduled repair.It will warm maintenance personnel of improper or lack of maintenance and presence of fuel dilution or antifreeze in oil.It is particularly helpful in preventing wear due to dirt entry from air cleaner or inlet piping.Regular sampling is especially advantageous for new engines to establish wear trends from the beginning. The results of the oil analysis are interpreted by experienced, highly trained personnel. Contact your Caterpillar dealer for detailed information.