Information injection-pump assembly
BOSCH
F 01G 09U 0FA
f01g09u0fa
ZEXEL
108622-3432
1086223432
HINO
220008862A
220008862a
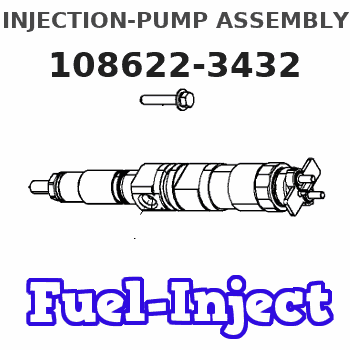
Rating:
Service parts 108622-3432 INJECTION-PUMP ASSEMBLY:
1.
_
5.
AUTOM. ADVANCE MECHANIS
9.
_
11.
Nozzle and Holder
23600-2800B
12.
Open Pre:MPa(Kqf/cm2)
14.7{150}/21.6{220}
14.
NOZZLE
Include in #1:
108622-3432
as INJECTION-PUMP ASSEMBLY
Cross reference number
BOSCH
F 01G 09U 0FA
f01g09u0fa
ZEXEL
108622-3432
1086223432
HINO
220008862A
220008862a
Zexel num
Bosch num
Firm num
Name
Calibration Data:
Adjustment conditions
Test oil
1404 Test oil ISO4113 or {SAEJ967d}
1404 Test oil ISO4113 or {SAEJ967d}
Test oil temperature
degC
40
40
45
Nozzle and nozzle holder
105780-8250
Bosch type code
1 688 901 101
Nozzle
105780-0120
Bosch type code
1 688 901 990
Nozzle holder
105780-2190
Opening pressure
MPa
20.7
Opening pressure
kgf/cm2
211
Injection pipe
Outer diameter - inner diameter - length (mm) mm 8-3-600
Outer diameter - inner diameter - length (mm) mm 8-3-600
Overflow valve
134424-4120
Overflow valve opening pressure
kPa
255
221
289
Overflow valve opening pressure
kgf/cm2
2.6
2.25
2.95
Tester oil delivery pressure
kPa
255
255
255
Tester oil delivery pressure
kgf/cm2
2.6
2.6
2.6
PS/ACT control unit part no.
407980-2
24*
Digi switch no.
33
Direction of rotation (viewed from drive side)
Left L
Left L
Injection timing adjustment
Direction of rotation (viewed from drive side)
Left L
Left L
Injection order
1-4-2-6-
3-5
Pre-stroke
mm
7.2
7.17
7.23
Beginning of injection position
Drive side NO.1
Drive side NO.1
Difference between angles 1
Cal 1-4 deg. 60 59.75 60.25
Cal 1-4 deg. 60 59.75 60.25
Difference between angles 2
Cyl.1-2 deg. 120 119.75 120.25
Cyl.1-2 deg. 120 119.75 120.25
Difference between angles 3
Cal 1-6 deg. 180 179.75 180.25
Cal 1-6 deg. 180 179.75 180.25
Difference between angles 4
Cal 1-3 deg. 240 239.75 240.25
Cal 1-3 deg. 240 239.75 240.25
Difference between angles 5
Cal 1-5 deg. 300 299.75 300.25
Cal 1-5 deg. 300 299.75 300.25
Injection quantity adjustment
Adjusting point
-
Rack position
12.4
Pump speed
r/min
700
700
700
Average injection quantity
mm3/st.
148
145
151
Max. variation between cylinders
%
0
-2
2
Basic
*
Fixing the rack
*
PS407980-224*
V
2.2+-0.0
1
PS407980-224*
mm
4.8+-0.0
5
Standard for adjustment of the maximum variation between cylinders
*
Injection quantity adjustment_02
Adjusting point
Z
Rack position
6.5+-0.5
Pump speed
r/min
350
350
350
Average injection quantity
mm3/st.
15
12
18
Max. variation between cylinders
%
0
-15
15
Fixing the rack
*
PS407980-224*
V
V1+0.05+
-0.01
PS407980-224*
mm
7.1+-0.0
3
Standard for adjustment of the maximum variation between cylinders
*
Remarks
Refer to items regarding the pre-stroke actuator
Refer to items regarding the pre-stroke actuator
Injection quantity adjustment_03
Adjusting point
A
Rack position
R1(12.4)
Pump speed
r/min
700
700
700
Average injection quantity
mm3/st.
148
146
150
Basic
*
Fixing the lever
*
PS407980-224*
V
2.2+-0.0
1
PS407980-224*
mm
4.8+-0.0
5
Injection quantity adjustment_04
Adjusting point
B
Rack position
R1+0.8
Pump speed
r/min
1075
1075
1075
Average injection quantity
mm3/st.
133.5
127.5
139.5
Fixing the lever
*
PS407980-224*
V
2.2+-0.0
1
PS407980-224*
mm
4.8+-0.0
5
0000001601
Pre-stroke
mm
7.2
7.17
7.23
Remarks
When the timing sleeve is pushed up
When the timing sleeve is pushed up
_02
Connector angle
deg.
8.5
8
9
Remarks
When the eccentric pin is tightened
When the eccentric pin is tightened
_03
Supply voltage
V
24
23.5
24.5
Ambient temperature
degC
23
18
28
Pre-stroke
mm
3.2
3.15
3.25
Output voltage
V
2.95
2.94
2.96
Adjustment
*
_04
Supply voltage
V
24
23.5
24.5
Ambient temperature
degC
23
18
28
Pre-stroke
mm
7.2
7.17
7.23
Output voltage
V
1.2
1
1.4
Confirmation
*
Remarks
Output voltage V1
Output voltage V1
_05
Supply voltage
V
24
23.5
24.5
Ambient temperature
degC
23
18
28
Output voltage
V
3.05
3.05
Confirmation of operating range
*
Test data Ex:
Governor adjustment
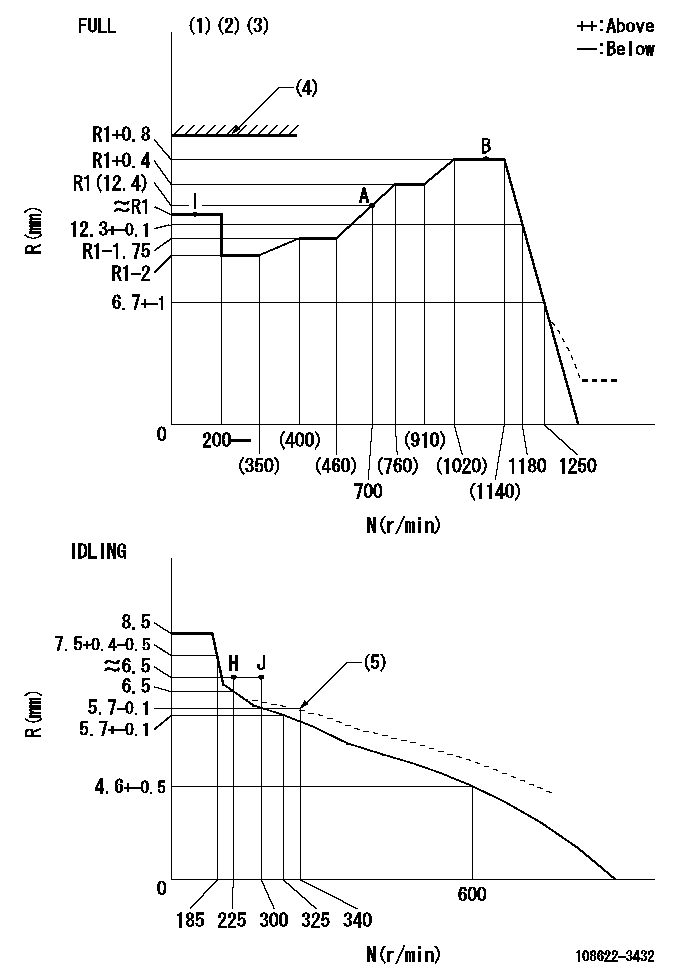
N:Pump speed
R:Rack position (mm)
(1)Torque cam stamping: T1
(2)Tolerance for racks not indicated: +-0.05mm.
(3)Set stop lever before governor adjustment. [When setting stop lever after governor adjustment, confirm that point B (Ra) can be obtained at full setting.]
(4)Stop lever's normal position setting: equivalent to RA
(5)Damper spring setting
----------
T1=AD16 Ra=R1+0.8mm RA=16mm
----------
----------
T1=AD16 Ra=R1+0.8mm RA=16mm
----------
Speed control lever angle
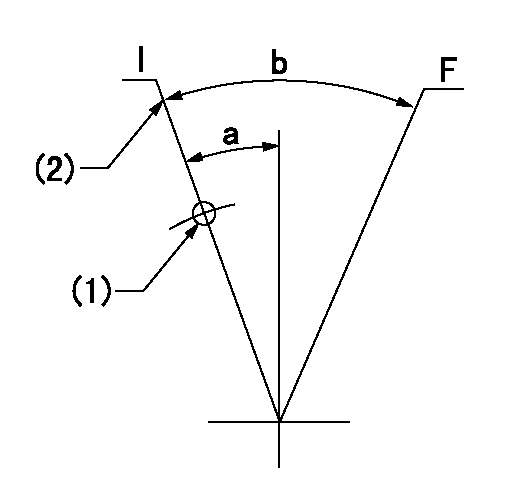
F:Full speed
I:Idle
(1)Use the hole at R = aa
(2)Stopper bolt set position 'H'
----------
aa=36.5mm
----------
a=18deg+-5deg b=(40deg)+-3deg
----------
aa=36.5mm
----------
a=18deg+-5deg b=(40deg)+-3deg
Stop lever angle
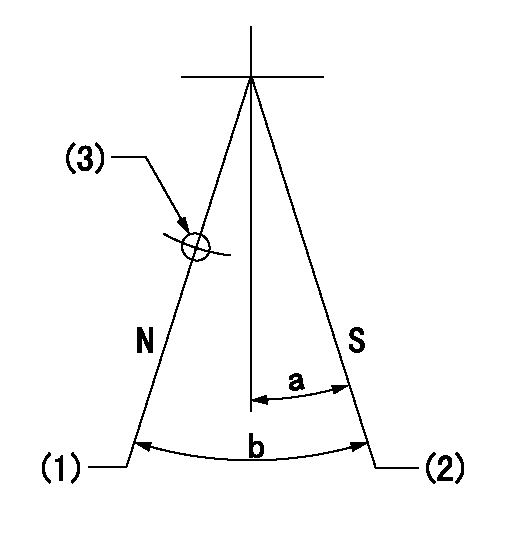
N:Pump normal
S:Stop the pump.
(1)Set the stopper bolt at rack position = approximately aa.
(2)At pump speed bb and rack position cc, set the stopper bolt. (Confirm non-injection at speed = dd.)
(3)Use the hole above R = ee
----------
aa=16mm bb=0r/min cc=1.5+-0.3mm dd=1250r/min ee=35mm
----------
a=11deg+-5deg b=31deg+-5deg
----------
aa=16mm bb=0r/min cc=1.5+-0.3mm dd=1250r/min ee=35mm
----------
a=11deg+-5deg b=31deg+-5deg
0000001301

(1)Pump vertical direction
(2)Coupling's key groove position at No 1 cylinder's beginning of injection
(3)Pre-stroke: aa
(4)-
----------
aa=7.2+-0.03mm
----------
a=(2deg)
----------
aa=7.2+-0.03mm
----------
a=(2deg)
0000001901
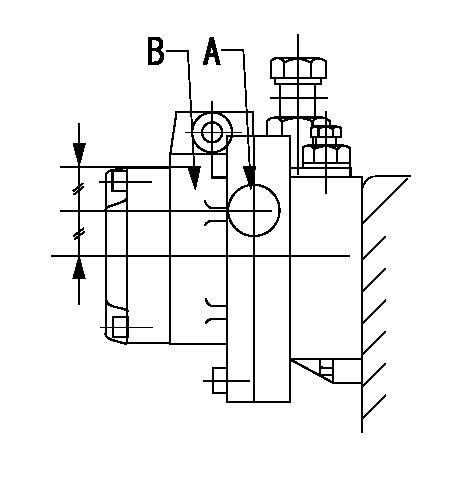
A:Sealing position
B:Pre-stroke actuator
1. When installing the pre-stroke actuator on the pump, first tighten the installation bolts loosely, then move the actuator fully counterclockwise (viewed from the drive side).
Temporary tightening torque: 1 - 1.5 N.m (0.1 - 0.15 kgf.m)
2. Move the actuator in the clockwise direction when viewed from the drive side, and adjust so that it becomes the adjustment point of the adjustment value. Then tighten it.
Tightening torque: 7^9 N.m (0.7^0.9 kgf.m)
3. After prestroke actuator installation adjustment, simultaneously stamp both the actuator side and housing side.
----------
----------
----------
----------
0000002201 RACK SENSOR
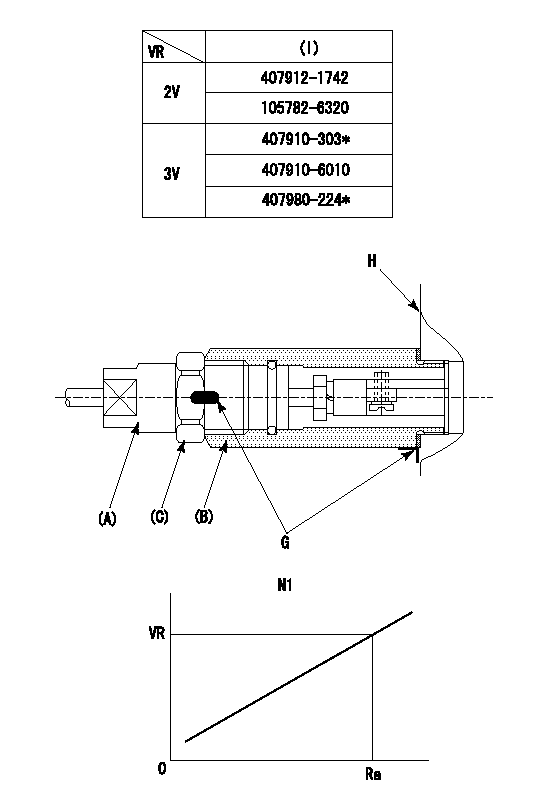
(VR) measurement voltage
(I) Part number of the control unit
(G) Apply red paint.
(H): End surface of the pump
1. Rack sensor adjustment (-0620)
(1)Fix the speed control lever at the full position
(2)Set the speed to N1 r/min.
(If the boost compensator is provided, apply boost pressure.)
(3)Adjust the bobbin (A) so that the rack sensor's output voltage is VR+-0.01.
(4)At that time, rack position must be Ra.
(5)Apply G at two places.
Connecting part between the joint (B) and the nut (F)
Connecting part between the joint (B) and the end surface of the pump (H)
----------
N1=1075r/min Ra=R1(12.4)+0.8mm
----------
----------
N1=1075r/min Ra=R1(12.4)+0.8mm
----------
0000002301 AIR CYLINDER
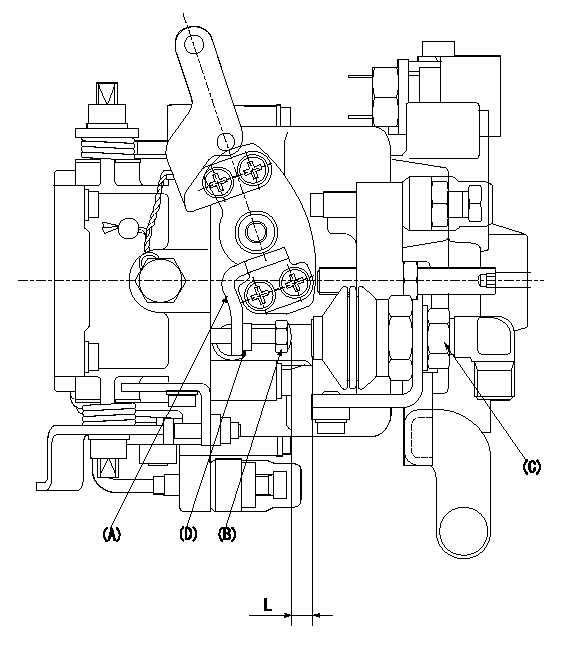
1. Air cylinder adjustment procedure
(1)Set the speed lever at idle.
(2)Temporarily set the clearance between the speed lever A and the set bolt B at L.
(3)Set the speed at N.
(4)Apply positive pressure P1 to the air cylinder.
(5)Gradually push out the set bolt (B).
(6)Tighten the nut (D) at the point where the rack position is Ra at speed N.
(7)Apply positive pressure P1 several times.
(8)Confirm that the lever returns to the idle position at positive pressure P2.
----------
L=(6)mm N=320r/min P1=392+98kPa(4+1kgf/cm2) P2=0kPa(0kgf/cm2) Ra=6.5+-0.1mm
----------
----------
L=(6)mm N=320r/min P1=392+98kPa(4+1kgf/cm2) P2=0kPa(0kgf/cm2) Ra=6.5+-0.1mm
----------
Information:
Start By:a. remove fuel injection linesb. remove fuel filter and basec. remove fuel transfer pump The following illustrations are of a 3304 Engine. 1. Disconnect the governor control linkage from the governor.2. On 3304 Engines only: remove oil supply line (1), oil drain line (2) and heat shield (3). Remove the O-ring seal from oil drain line (2) if it is damaged. Remove the gaskets and screen from the top of the turbocharger.3. Disconnect fuel drain lines (4) and (5) from the fuel injection pump housing and governor. 4. Remove the nuts, washers and cover from the timing gear housing. Remove studs (6) if they are damaged or loose.5. Loosen bolt (7) enough to leave a gap of 3.18 mm (.125 in) between washer (8) and the fuel pump drive gear.6. Install Tool (A) as shown. Tighten the stud to pull the fuel pump drive gear loose from the taper on the fuel injection pump camshaft.7. Remove Tool (A), bolt (7) and washer (8) from the engine. 8. Fasten a nylon strap and hoist to the fuel injection pump housing and governor. The 3304 fuel injection pump housing and governor weighs 24 kg (53 lb). The 3306 fuel injection pump housing and governor weighs 29 kg (64 lb).9. Remove bolt (9), bolt (10), three nuts (11) and the fuel injection pump housing and governor. Remove the two O-ring seals from the bottom and the two O-ring seals from the front of the fuel injection pump housing and governor.Install Fuel Injection Pump Housing & Governor
The following illustrations are of a 3304 Engine. 1. Put clean engine oil on the O-ring seals. Install O-ring seals (1) in the bottom and O-ring seals (2) in the front of the fuel injection pump housing and governor. 2. Make sure O-ring seals (1) and (2) stay in position in the fuel injection pump housing and governor. Fasten a hoist to the fuel injection pump housing and governor, and put it in position on the engine. Install the two bolts at location (5) and the three nuts on studs (3) to hold the fuel injection pump housing and governor in position.3. Remove the bolts that hold cover (4) in position. Remove cover (4) and the gasket. 4. Put Tool (A) in position as shown. Install the bolt that holds the fuel pump drive gear to the fuel injection pump camshaft without the washer. This will allow the camshaft in the fuel system to be turned.5. Put pressure on the end of Tool (A) and turn the camshaft slowly until the Tool drops into the groove (slot) in the camshaft. Leave Tool (A) in position in the groove (slot). Remove the bolt from the end of the camshaft. 6. Install washer (6) with the large diameter toward the front of the engine. Install bolt (7) and tighten it to a torque of 6.8 N m (60 lb in).7. Install Tool (B) as shown in the flywheel housing. Make sure bolt (7) does not loosen as
The following illustrations are of a 3304 Engine. 1. Put clean engine oil on the O-ring seals. Install O-ring seals (1) in the bottom and O-ring seals (2) in the front of the fuel injection pump housing and governor. 2. Make sure O-ring seals (1) and (2) stay in position in the fuel injection pump housing and governor. Fasten a hoist to the fuel injection pump housing and governor, and put it in position on the engine. Install the two bolts at location (5) and the three nuts on studs (3) to hold the fuel injection pump housing and governor in position.3. Remove the bolts that hold cover (4) in position. Remove cover (4) and the gasket. 4. Put Tool (A) in position as shown. Install the bolt that holds the fuel pump drive gear to the fuel injection pump camshaft without the washer. This will allow the camshaft in the fuel system to be turned.5. Put pressure on the end of Tool (A) and turn the camshaft slowly until the Tool drops into the groove (slot) in the camshaft. Leave Tool (A) in position in the groove (slot). Remove the bolt from the end of the camshaft. 6. Install washer (6) with the large diameter toward the front of the engine. Install bolt (7) and tighten it to a torque of 6.8 N m (60 lb in).7. Install Tool (B) as shown in the flywheel housing. Make sure bolt (7) does not loosen as