Information injection-pump assembly
ZEXEL
108622-3342
1086223342
HINO
220008722A
220008722a
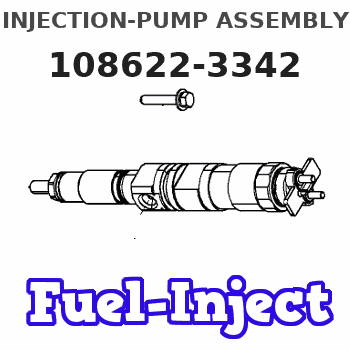
Rating:
Service parts 108622-3342 INJECTION-PUMP ASSEMBLY:
1.
_
5.
AUTOM. ADVANCE MECHANIS
9.
_
11.
Nozzle and Holder
23600-2800B
12.
Open Pre:MPa(Kqf/cm2)
14.7{150}/21.6{220}
14.
NOZZLE
Include in #1:
108622-3342
as INJECTION-PUMP ASSEMBLY
Cross reference number
ZEXEL
108622-3342
1086223342
HINO
220008722A
220008722a
Zexel num
Bosch num
Firm num
Name
Calibration Data:
Adjustment conditions
Test oil
1404 Test oil ISO4113 or {SAEJ967d}
1404 Test oil ISO4113 or {SAEJ967d}
Test oil temperature
degC
40
40
45
Nozzle and nozzle holder
105780-8250
Bosch type code
1 688 901 101
Nozzle
105780-0120
Bosch type code
1 688 901 990
Nozzle holder
105780-2190
Opening pressure
MPa
20.7
Opening pressure
kgf/cm2
211
Injection pipe
Outer diameter - inner diameter - length (mm) mm 8-3-600
Outer diameter - inner diameter - length (mm) mm 8-3-600
Overflow valve
134424-4120
Overflow valve opening pressure
kPa
255
221
289
Overflow valve opening pressure
kgf/cm2
2.6
2.25
2.95
Tester oil delivery pressure
kPa
255
255
255
Tester oil delivery pressure
kgf/cm2
2.6
2.6
2.6
PS/ACT control unit part no.
407980-2
24*
Digi switch no.
33
Direction of rotation (viewed from drive side)
Left L
Left L
Injection timing adjustment
Direction of rotation (viewed from drive side)
Left L
Left L
Injection order
1-4-2-6-
3-5
Pre-stroke
mm
7.2
7.17
7.23
Beginning of injection position
Drive side NO.1
Drive side NO.1
Difference between angles 1
Cal 1-4 deg. 60 59.75 60.25
Cal 1-4 deg. 60 59.75 60.25
Difference between angles 2
Cyl.1-2 deg. 120 119.75 120.25
Cyl.1-2 deg. 120 119.75 120.25
Difference between angles 3
Cal 1-6 deg. 180 179.75 180.25
Cal 1-6 deg. 180 179.75 180.25
Difference between angles 4
Cal 1-3 deg. 240 239.75 240.25
Cal 1-3 deg. 240 239.75 240.25
Difference between angles 5
Cal 1-5 deg. 300 299.75 300.25
Cal 1-5 deg. 300 299.75 300.25
Injection quantity adjustment
Adjusting point
-
Rack position
13.6
Pump speed
r/min
700
700
700
Average injection quantity
mm3/st.
161
158
164
Max. variation between cylinders
%
0
-2
2
Basic
*
Fixing the rack
*
PS407980-224*
V
2.2+-0.0
1
PS407980-224*
mm
4.8+-0.0
5
Standard for adjustment of the maximum variation between cylinders
*
Injection quantity adjustment_02
Adjusting point
Z
Rack position
7+-0.5
Pump speed
r/min
360
360
360
Average injection quantity
mm3/st.
15
12
18
Max. variation between cylinders
%
0
-15
15
Fixing the rack
*
PS407980-224*
V
V1+0.05+
-0.01
PS407980-224*
mm
7.1+-0.0
3
Standard for adjustment of the maximum variation between cylinders
*
Remarks
Refer to items regarding the pre-stroke actuator
Refer to items regarding the pre-stroke actuator
Injection quantity adjustment_03
Adjusting point
A
Rack position
R1(13.6)
Pump speed
r/min
700
700
700
Average injection quantity
mm3/st.
161
159
163
Basic
*
Fixing the lever
*
PS407980-224*
V
2.2+-0.0
1
PS407980-224*
mm
4.8+-0.0
5
Injection quantity adjustment_04
Adjusting point
B
Rack position
R1+0.5
Pump speed
r/min
1075
1075
1075
Average injection quantity
mm3/st.
140.5
134.5
146.5
Fixing the lever
*
PS407980-224*
V
2.2+-0.0
1
PS407980-224*
mm
4.8+-0.0
5
0000001601
Pre-stroke
mm
7.2
7.17
7.23
Remarks
When the timing sleeve is pushed up
When the timing sleeve is pushed up
_02
Connector angle
deg.
11.5
11
12
Remarks
When the eccentric pin is tightened
When the eccentric pin is tightened
_03
Supply voltage
V
24
23.5
24.5
Ambient temperature
degC
23
18
28
Pre-stroke
mm
3.2
3.15
3.25
Output voltage
V
2.95
2.94
2.96
Adjustment
*
_04
Supply voltage
V
24
23.5
24.5
Ambient temperature
degC
23
18
28
Pre-stroke
mm
7.2
7.17
7.23
Output voltage
V
1.2
1
1.4
Confirmation
*
Remarks
Output voltage V1
Output voltage V1
_05
Supply voltage
V
24
23.5
24.5
Ambient temperature
degC
23
18
28
Output voltage
V
3.05
3.05
Confirmation of operating range
*
Test data Ex:
Governor adjustment
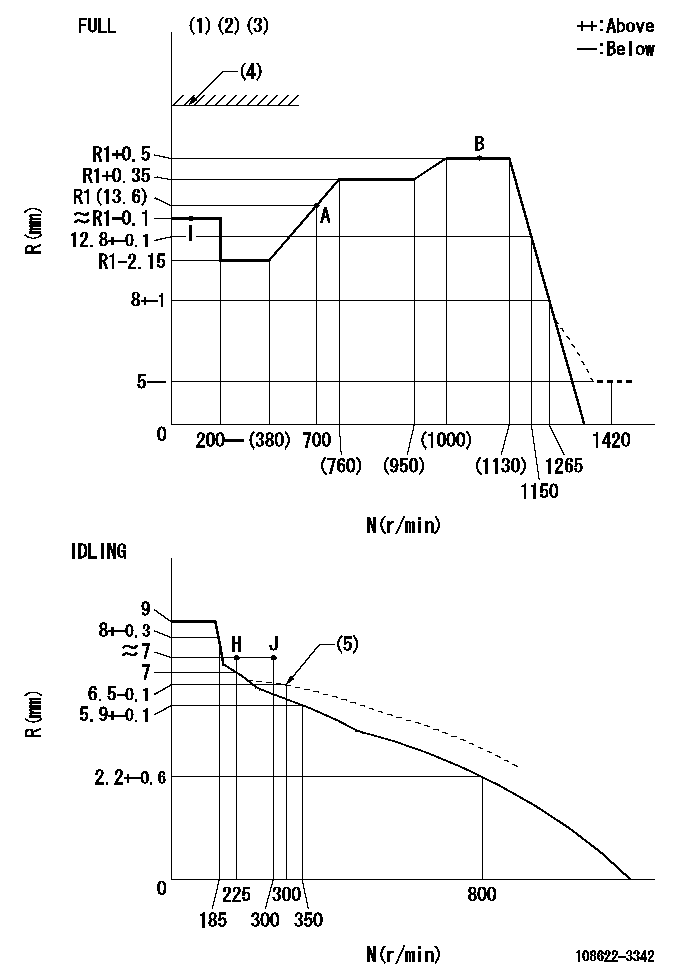
N:Pump speed
R:Rack position (mm)
(1)Torque cam stamping: T1
(2)Tolerance for racks not indicated: +-0.05mm.
(3)Set stop lever before governor adjustment. [When setting stop lever after governor adjustment, confirm that point B (Ra) can be obtained at full setting.]
(4)Stop lever's normal position setting: equivalent to RA
(5)Damper spring setting
----------
T1=AC97 Ra=(R1+0.5)mm RA=18mm
----------
----------
T1=AC97 Ra=(R1+0.5)mm RA=18mm
----------
Speed control lever angle
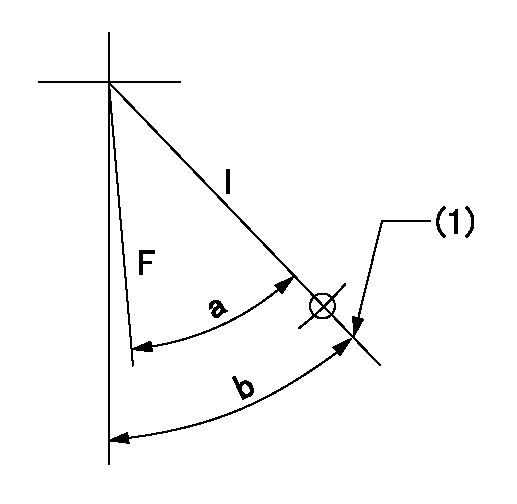
F:Full speed
I:Idle
(1)Stopper bolt set position 'H'
----------
----------
a=34deg+-3deg b=36deg+-5deg
----------
----------
a=34deg+-3deg b=36deg+-5deg
Stop lever angle
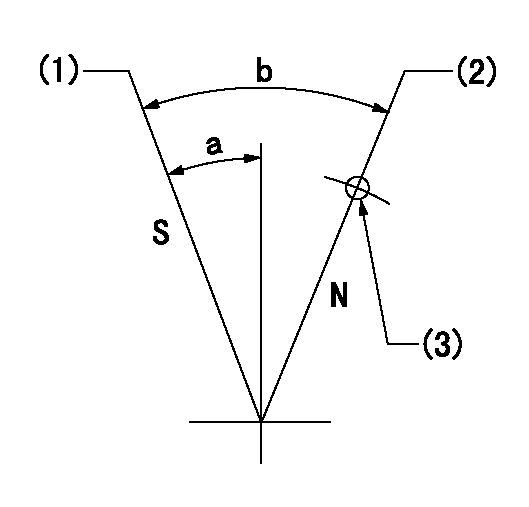
N:Pump normal
S:Stop the pump.
(1)At pump speed aa and rack position bb, set the stopper screw. (After setting, apply red paint.)
(2)Set the stopper screw at this lever angle.
(3)Use the hole above R = cc
----------
aa=0r/min bb=1.5+-0.3mm cc=30mm
----------
a=22deg+-5deg b=42deg+-5deg
----------
aa=0r/min bb=1.5+-0.3mm cc=30mm
----------
a=22deg+-5deg b=42deg+-5deg
0000001301

(1)Pump vertical direction
(2)Coupling's key groove position at No 1 cylinder's beginning of injection
(3)Pre-stroke: aa
(4)-
----------
aa=7.2+-0.03mm
----------
a=(10deg)
----------
aa=7.2+-0.03mm
----------
a=(10deg)
0000001901
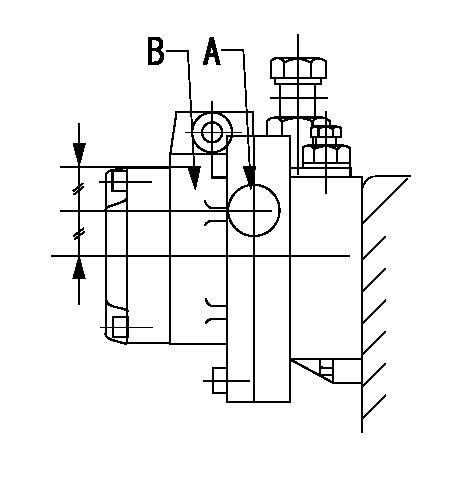
A:Sealing position
B:Pre-stroke actuator
1. When installing the pre-stroke actuator on the pump, first tighten the installation bolts loosely, then move the actuator fully counterclockwise (viewed from the drive side).
Temporary tightening torque: 1 - 1.5 N.m (0.1 - 0.15 kgf.m)
2. Move the actuator in the clockwise direction when viewed from the drive side, and adjust so that it becomes the adjustment point of the adjustment value. Then tighten it.
Tightening torque: 7^9 N.m (0.7^0.9 kgf.m)
3. After prestroke actuator installation adjustment, simultaneously stamp both the actuator side and housing side.
----------
----------
----------
----------
0000002201 RACK SENSOR

(VR) measurement voltage
(I) Part number of the control unit
(G) Apply red paint.
(H): End surface of the pump
1. Rack limit adjustment
(1)Mount the joint (B).
(2)Select the shim (D) so that the rack limit's rack position is obtained at that time.
(3)Install the rod (E) to the block (C).
The distance between the pump end face and the rod (E) at rack limit must be L.
2. Rack sensor adjustment (-0020)
(1)Screw in the bobbin (A) until it contacts the joint (B).
(2)Fix the speed control lever at the full side.
(3)Set at speed N.
(4)Adjust the depth that the bobbin (A) is screwed in so that the control unit's rack sensor output voltage is VR+-0.01 (V), then tighten the nut (F). (If equipped with a boost compensator, perform with boost pressure applied.)
(5)Adjust the bobbin (A) so that the rack sensor's output voltage is VR+-0.01.
(6)Apply G at two places.
Connecting part between the joint (B) and the nut (F)
Connecting part between the joint (B) and the end surface of the pump (H)
----------
L=38-0.2mm N=1075r/min Ra=R1(13.6)+0.5mm
----------
----------
L=38-0.2mm N=1075r/min Ra=R1(13.6)+0.5mm
----------
Information:
ACTION REQUIRED
Refer to the attached Rework Procedure.
OWNER NOTIFICATION
U.S. and Canadian owners will receive the attached Owner Notification.
SERVICE CLAIM ALLOWANCES
Caterpillar Dealer Suggested Customer Suggested
Parts % Labor Hrs% Parts % Labor Hrs% Parts % Labor Hrs%
100% 100% 0% 0% 0% 0%
This is a 4.0-hour job
PARTS DISPOSITION
Handle the parts in accordance with your Warranty Bulletin on warranty parts handling.
MAKE EVERY EFFORT TO COMPLETE THIS PROGRAM AS SOON AS POSSIBLE.
COPY OF OWNER NOTIFICATION FOR U.S. AND CANADIAN OWNERS
XYZ Corporation
3240 Arrow Drive
Anywhere, YZ 99999
PRIORITY - PRODUCT IMPROVEMENT PROGRAM FOR REPLACING THE DIESEL PARTICULATE FILTER ON CERTAIN SKID STEER LOADERS AND COMPACT TRACK LOADERS
MODELS INVOLVED - 272D Skid Steer Loaders and 299D Compact Track Loaders
Dear Cat Product Owner:
The diesel particulate filter needs to be replaced on certain 272D Skid Steer Loaders and 299D Compact Track Loaders. The existing diesel particulate filter has been installed incorrectly which can result in decreased performance of the filter. You will not be charged for the service performed.
Contact your local Cat dealer immediately to schedule this service. The dealer will advise you of the time required to complete this service.
Please refer the dealer to their Service Letter dated 06Aug2012 when scheduling this service.
We regret the inconvenience this may cause you, but urge you to have this service performed as soon as possible to prevent unscheduled downtime.
Caterpillar Inc.
Identification #(s)
Attached to 06Aug2012 Service Letter
Rework Procedure
1. Remove the cooling package. Refer UENR2328, Disassembly and Assembly, "Radiator and Hydraulic Oil Cooler - Removal Procedure".
2. Record the diesel particulate filter serial number prior to installing. The serial number is etched into the diesel particulate filter housing in the location shown in Image1.1.1. It is the lower set of digits. Send the new diesel particulate filter serial number and machine serial number to Rob McHardy (MCHARDY_ROBERT_W).
Image1.1.1
Image1.1.2
3. Replace the 389-5370 Diesel Particulate Filter section. Refer to UENR0129, Disassembly and Assembly, "Diesel Particulate Filter - Remove and Install" and "Diesel Particulate Filter - Disassemble".
4. When performing this work, replace the three 389-5373 Gaskets (metal) for the diesel particulate filter section and the 345-3579 Gasket between the turbo flange and the DOC inlet.
5. Ensure the diesel particulate filter is installed with the exhaust flowing in the direction of the arrow that is on the diesel particulate filter. Refer to Image1.2.1.
6. Cover both ends of the diesel particulate filter to ensure the ash and soot remain within the diesel particulate filter. Package the diesel particulate filter according to REHS3827, "Procedure to Handle and Ship Diesel Particulate Filters (DPF) and Catalytic Converter Mufflers (CCM)".
7. Connect Caterpillar Electronic Technician (ET). Version 2012A is acceptable but version 2012B is recommended. Go to Service Tab and select "DPF Soot Load Reset". At the next two screens select the "Reset" button in the bottom left corner.
Image1.2.1