Information injection-pump assembly
ZEXEL
108622-1230
1086221230
ISUZU
1156034090
1156034090
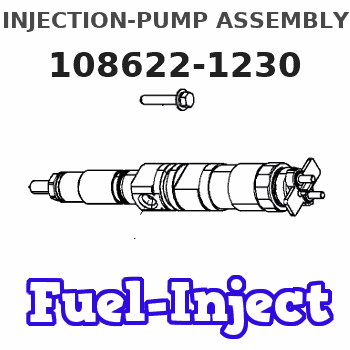
Rating:
Cross reference number
ZEXEL
108622-1230
1086221230
ISUZU
1156034090
1156034090
Zexel num
Bosch num
Firm num
Name
Calibration Data:
Adjustment conditions
Test oil
1404 Test oil ISO4113 or {SAEJ967d}
1404 Test oil ISO4113 or {SAEJ967d}
Test oil temperature
degC
40
40
45
Nozzle and nozzle holder
105780-8250
Bosch type code
1 688 901 101
Nozzle
105780-0120
Bosch type code
1 688 901 990
Nozzle holder
105780-2190
Opening pressure
MPa
20.7
Opening pressure
kgf/cm2
211
Injection pipe
Outer diameter - inner diameter - length (mm) mm 8-3-600
Outer diameter - inner diameter - length (mm) mm 8-3-600
Overflow valve
131424-7120
Overflow valve opening pressure
kPa
255
221
289
Overflow valve opening pressure
kgf/cm2
2.6
2.25
2.95
Tester oil delivery pressure
kPa
255
255
255
Tester oil delivery pressure
kgf/cm2
2.6
2.6
2.6
PS/ACT control unit part no.
407980-2
24*
Digi switch no.
32
Direction of rotation (viewed from drive side)
Left L
Left L
Injection timing adjustment
Direction of rotation (viewed from drive side)
Left L
Left L
Injection order
1-5-3-6-
2-4
Pre-stroke
mm
8.5
8.47
8.53
Beginning of injection position
Governor side NO.1
Governor side NO.1
Difference between angles 1
Cal 1-5 deg. 60 59.75 60.25
Cal 1-5 deg. 60 59.75 60.25
Difference between angles 2
Cal 1-3 deg. 120 119.75 120.25
Cal 1-3 deg. 120 119.75 120.25
Difference between angles 3
Cal 1-6 deg. 180 179.75 180.25
Cal 1-6 deg. 180 179.75 180.25
Difference between angles 4
Cyl.1-2 deg. 240 239.75 240.25
Cyl.1-2 deg. 240 239.75 240.25
Difference between angles 5
Cal 1-4 deg. 300 299.75 300.25
Cal 1-4 deg. 300 299.75 300.25
Injection quantity adjustment
Adjusting point
-
Rack position
12.9
Pump speed
r/min
720
720
720
Average injection quantity
mm3/st.
156.5
154.5
158.5
Max. variation between cylinders
%
0
-3
3
Basic
*
Fixing the rack
*
PS407980-224*
V
2.45+-0.
01
PS407980-224*
mm
6.1+-0.0
5
Standard for adjustment of the maximum variation between cylinders
*
Injection quantity adjustment_02
Adjusting point
Z
Rack position
6.7+-0.5
Pump speed
r/min
365
365
365
Average injection quantity
mm3/st.
14.5
11.3
17.7
Max. variation between cylinders
%
0
-13
13
Fixing the rack
*
PS407980-224*
V
V1+0.05+
-0.01
PS407980-224*
mm
8.4+-0.0
3
Standard for adjustment of the maximum variation between cylinders
*
Remarks
Refer to items regarding the pre-stroke actuator
Refer to items regarding the pre-stroke actuator
Injection quantity adjustment_03
Adjusting point
A
Rack position
R1(12.9)
Pump speed
r/min
720
720
720
Average injection quantity
mm3/st.
156.5
154.5
158.5
Basic
*
Fixing the lever
*
Boost pressure
kPa
53.3
53.3
Boost pressure
mmHg
400
400
PS407980-224*
V
2.45+-0.
01
PS407980-224*
mm
6.1+-0.0
5
Injection quantity adjustment_04
Adjusting point
B
Rack position
R1+1.1
Pump speed
r/min
1100
1100
1100
Average injection quantity
mm3/st.
141.5
131.5
151.5
Fixing the lever
*
Boost pressure
kPa
53.3
53.3
Boost pressure
mmHg
400
400
PS407980-224*
V
2.45+-0.
01
PS407980-224*
mm
6.1+-0.0
5
Boost compensator adjustment
Pump speed
r/min
500
500
500
Rack position
R2-1.7
Boost pressure
kPa
8
6.7
9.3
Boost pressure
mmHg
60
50
70
Boost compensator adjustment_02
Pump speed
r/min
500
500
500
Rack position
R2[R1-1.
4]
Boost pressure
kPa
40
40
40
Boost pressure
mmHg
300
300
300
0000001601
Pre-stroke
mm
8.5
8.47
8.53
Remarks
When the timing sleeve is pushed up
When the timing sleeve is pushed up
_02
Connector angle
deg.
8.5
8
9
Remarks
When the eccentric pin is tightened
When the eccentric pin is tightened
_03
Supply voltage
V
24
23.5
24.5
Ambient temperature
degC
23
18
28
Pre-stroke
mm
6.1
6.05
6.15
Output voltage
V
2.45
2.44
2.46
Adjustment
*
_04
Supply voltage
V
24
23.5
24.5
Ambient temperature
degC
23
18
28
Pre-stroke
mm
8.5
8.47
8.53
Output voltage
V
1.2
1
1.4
Confirmation
*
Remarks
Output voltage V1
Output voltage V1
_05
Supply voltage
V
24
23.5
24.5
Ambient temperature
degC
23
18
28
Pre-stroke
mm
5.5
Output voltage
V
3
2.98
3
Confirmation
*
_06
Supply voltage
V
24
23.5
24.5
Ambient temperature
degC
23
18
28
Output voltage
V
3.05
3.05
Confirmation of operating range
*
Test data Ex:
Governor adjustment
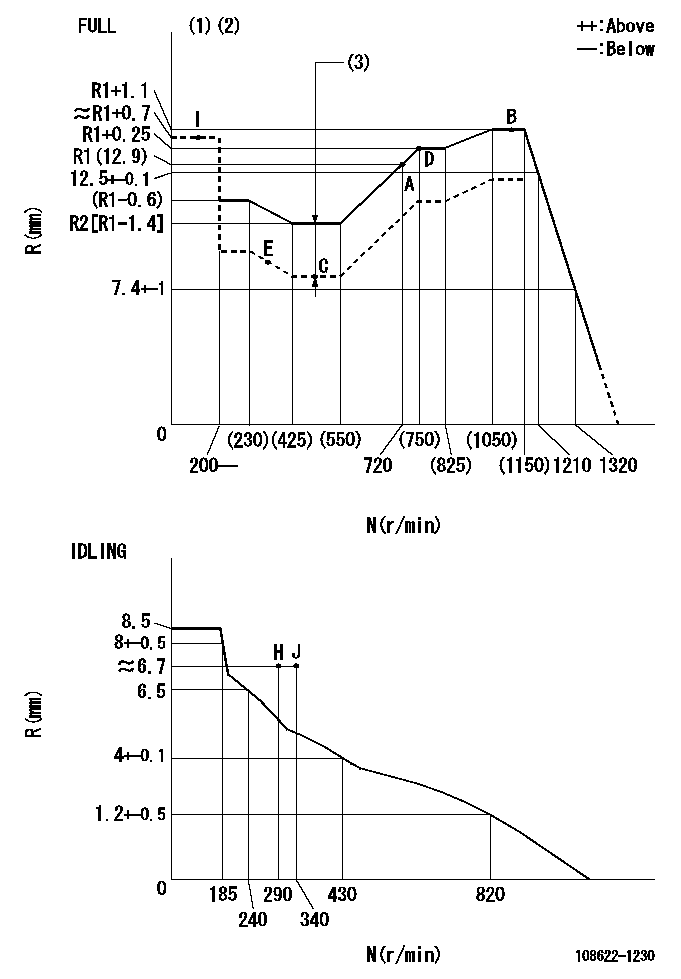
N:Pump speed
R:Rack position (mm)
(1)Torque cam stamping: T1
(2)Tolerance for racks not indicated: +-0.05mm.
(3)Boost compensator stroke: BCL
----------
T1=AF76 BCL=1.7+-0.1mm
----------
----------
T1=AF76 BCL=1.7+-0.1mm
----------
Speed control lever angle
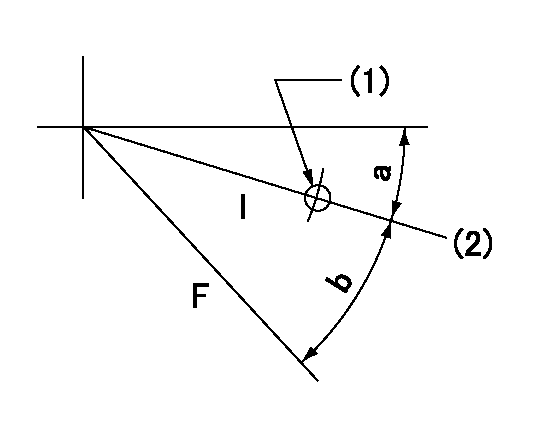
F:Full speed
I:Idle
(1)Use the pin at R = aa
(2)Stopper bolt setting
----------
aa=35mm
----------
a=22.5deg+-5deg b=30deg+-3deg
----------
aa=35mm
----------
a=22.5deg+-5deg b=30deg+-3deg
Stop lever angle
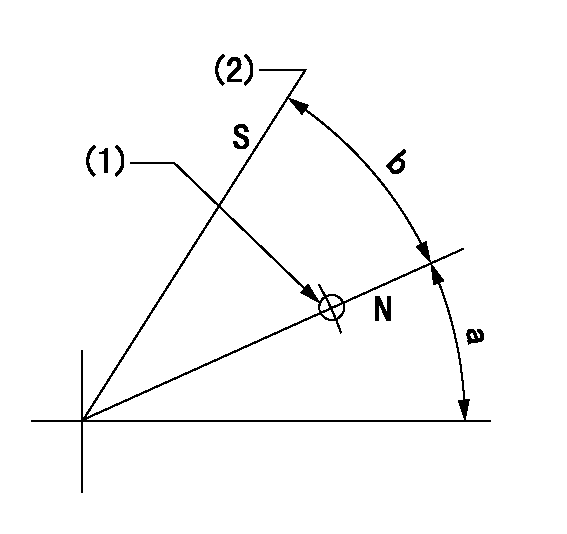
N:Pump normal
S:Stop the pump.
(1)Use the pin at R = aa
(2)Set the stopper bolt so that speed = bb and rack position = cc. (Confirm non-injection.)
----------
aa=40mm bb=0r/min cc=1.5+-0.3mm
----------
a=14deg+-5deg b=41deg+-5deg
----------
aa=40mm bb=0r/min cc=1.5+-0.3mm
----------
a=14deg+-5deg b=41deg+-5deg
0000001301
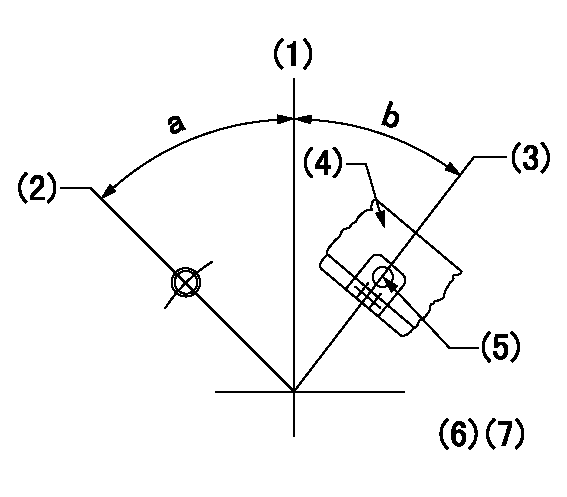
(1)Pump vertical direction
(2)Positions of coupling's threaded installation holes at No 1 cylinder's beginning of injection
(3)At the No 1 cylinder's beginning of injection position, stamp an aligning mark on the damper to align with the pointer's groove.
(4)Damper
(5)Pointer
(6)B.T.D.C.: aa
(7)Pre-stroke: bb
----------
aa=5deg bb=8.5+-0.03mm
----------
a=(50deg) b=(44deg)
----------
aa=5deg bb=8.5+-0.03mm
----------
a=(50deg) b=(44deg)
0000001901
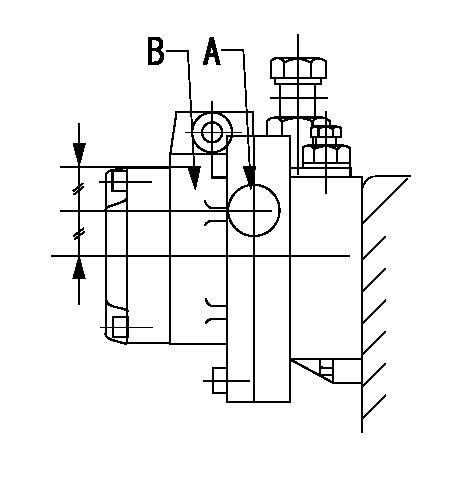
A:Sealing position
B:Pre-stroke actuator
1. When installing the pre-stroke actuator on the pump, first tighten the installation bolts loosely, then move the actuator fully counterclockwise (viewed from the drive side).
Temporary tightening torque: 1 - 1.5 N.m (0.1 - 0.15 kgf.m)
2. Move the actuator in the clockwise direction when viewed from the drive side, and adjust so that it becomes the adjustment point of the adjustment value. Then tighten it.
Tightening torque: 7^9 N.m (0.7^0.9 kgf.m)
3. After prestroke actuator installation adjustment, simultaneously stamp both the actuator side and housing side.
----------
----------
----------
----------
0000002201 RACK SENSOR

G:Red paint
H:Pump end face
P/N: part number of suitable shim
(1)Threaded type rack block
(2)Welded type rack block
Rack sensor adjustment
1. Threaded type rack sensor (-5*20, P type, no TICS rack limit).
(1)Screw in the bobbin (A) until it contacts the joint (B).
(2)Fix the pump lever.
(3)At speed N1 and rack position Ra, adjust the amount that the bobbin is screwed in so that the amp's output voltage is V1.
(4)Fix using the nut (F).
(5)Affix the caution plate to the upper part of the joint (B).
(6)Apply (G) at two places.
Connecting part between the joint (B) and the nut (F)
Connecting part between the end surface of the pump (H) and the joint (B)
2. Range for screw-in adjustment between the bobbin (A) and the joint (B) is 9 threads.
Screw in to the end from (the position where the bobbin (A) is rotated 9 turns).
Speed N1, rack position Ra, output voltage V1, rack sensor supply voltage 5+-0.01 (V)
----------
Ra=R1(12.9)+1.1mm N1=1100r/min V1=3+-0.01V
----------
----------
Ra=R1(12.9)+1.1mm N1=1100r/min V1=3+-0.01V
----------
Information:
Features
Benefits
All critical engineering changes and updates included
Improved reliability and performance
Worldwide availability through Cat parts distribution system
Customer access regardless of location
Off-the-shelf availability
Downtime reduced through exchange product
Same-as-new Caterpillar warranty
Consistent support
Coverage Chart
Reman PN
New PN
Part Name
20R1298
3594090
INJECTOR GP - FUEL
20R1299
3494080
INJECTOR GP - FUEL
20R1301
3594020
INJECTOR GP - FUEL
20R1302
3594040
INJECTOR GP - FUEL
20R1303
3594070
INJECTOR GP - FUEL
20R1304
3597434
INJECTOR GP - FUEL
20R1308
3594050
INJECTOR GP - FUEL
20R1302
3594040
INJECTOR GP - FUEL
20R1317
3809889
INJECTOR GP - FUEL
20R1318
3674293
INJECTOR GP - FUEL
20R3247
3920225
INJECTOR GP - FUEL
20R3607
3820709
INJECTOR GP - FUEL
20R3608
3820745
INJECTOR GP – FUEL
20R3815
3689171
PUMP GP – FUEL INJ
20R3816
3689172
PUMP GP – FUEL INJ
20R3817
3689173
PUMP GP – FUEL INJ
Core Acceptance
The following Core Acceptance Criteria are available supporting these products. All the latest Core Acceptance Criteria guidelines can be found on the Reman Dealer Extranet at https://catreman.cat.com/cac
SELD0226 Unit Injectors Electronic
SELD0023 Fuel Pump & Governor Groups
Warranty
Please consult the appropriate warranty statement for your area by going to warranty.cat.com.
Core Management
Please refer to the Caterpillar Core Management Information System (CMIS 2) related to the parts information application that describes all Reman part/Core Acceptability Family (CAF) and other related information. Also, refer to other CMIS 2 inquiry applications such as: Dealer Customer Profile, Inspection Reason Codes, Inspection Line Inquiry, Dealer Add Charges, Dealer Entitlement Activity, Dealer CCR Inquiry, Dealer CCR Entry, Dealer Shipment Processing, Dealer Process Packaging Grief and Reporting. This information is available to all dealers worldwide that have been converted to CMIS 2.
Please go to the Reman web site https://catreman.cat.com for the latest policy and procedural updates that are available to all dealers worldwide explaining policy and procedural information such as “Policy and Core Management” -SELD0122; “Core Management Systems and Operations Procedures” -SELD0040; “Reman Core Return Packaging Instructions And Guidelines” -SELD0300; and “Shipping Instructions” SELD0039.
If you have any questions regarding Reman Core Management or Core Management Systems (CMIS2), feel free to call your Corinth Dealer Service Representative toll free at (800) 537-2928.
Contact Information:
For assistance with technical questions, call the Reman Technical Hot Line also toll free at (888) 88-REMAN or use our e-mail address--Reman_Help.
Global Dealer Solutions Network Parts Technical Support Team Toll Free -North America: 1-877-228-2420 International: +1-309-266-4421 Electronic Requests: Send via Microsoft Customer Relationship Management (MSCRM). For access and tutorial information: https://gdsn.cat.com/mscrm
, CATERPILLAR, BUILT FOR IT, their respective logos, “Caterpillar Yellow” and the ”Power Edge” trade dress, as well as corporate and product identity used herein, are trademarks of Caterpillar and may not be used without permission.
The information contained herein is intended for circulation only to Caterpillar and dealer employees whose duties require knowledge of such reports and is intended exclusively for their information and