Information injection-pump assembly
BOSCH
9 400 611 860
9400611860
ZEXEL
108622-1172
1086221172
ISUZU
1156033062
1156033062
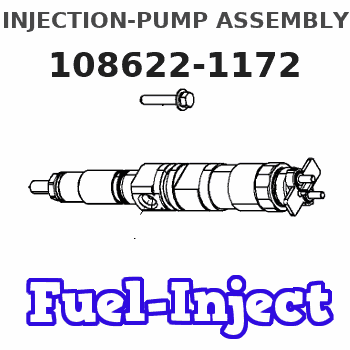
Rating:
Service parts 108622-1172 INJECTION-PUMP ASSEMBLY:
1.
_
5.
AUTOM. ADVANCE MECHANIS
7.
COUPLING PLATE
11.
Nozzle and Holder
1-15300-371-2
12.
Open Pre:MPa(Kqf/cm2)
17.7{180}/22.1{225}
14.
NOZZLE
Include in #1:
108622-1172
as INJECTION-PUMP ASSEMBLY
Cross reference number
BOSCH
9 400 611 860
9400611860
ZEXEL
108622-1172
1086221172
ISUZU
1156033062
1156033062
Zexel num
Bosch num
Firm num
Name
Calibration Data:
Adjustment conditions
Test oil
1404 Test oil ISO4113 or {SAEJ967d}
1404 Test oil ISO4113 or {SAEJ967d}
Test oil temperature
degC
40
40
45
Nozzle and nozzle holder
105780-8250
Bosch type code
1 688 901 101
Nozzle
105780-0120
Bosch type code
1 688 901 990
Nozzle holder
105780-2190
Opening pressure
MPa
20.7
Opening pressure
kgf/cm2
211
Injection pipe
Outer diameter - inner diameter - length (mm) mm 8-3-600
Outer diameter - inner diameter - length (mm) mm 8-3-600
Overflow valve
134424-4320
Overflow valve opening pressure
kPa
255
221
289
Overflow valve opening pressure
kgf/cm2
2.6
2.25
2.95
Tester oil delivery pressure
kPa
255
255
255
Tester oil delivery pressure
kgf/cm2
2.6
2.6
2.6
RED4 control unit part number
407915-0
590
RED4 rack sensor specifications
mm
19
PS/ACT control unit part no.
407980-2
24*
Digi switch no.
33
Direction of rotation (viewed from drive side)
Right R
Right R
Injection timing adjustment
Direction of rotation (viewed from drive side)
Right R
Right R
Injection order
1-5-3-6-
2-4
Pre-stroke
mm
7
6.97
7.03
Beginning of injection position
Drive side NO.1
Drive side NO.1
Difference between angles 1
Cal 1-5 deg. 60 59.75 60.25
Cal 1-5 deg. 60 59.75 60.25
Difference between angles 2
Cal 1-3 deg. 120 119.75 120.25
Cal 1-3 deg. 120 119.75 120.25
Difference between angles 3
Cal 1-6 deg. 180 179.75 180.25
Cal 1-6 deg. 180 179.75 180.25
Difference between angles 4
Cyl.1-2 deg. 240 239.75 240.25
Cyl.1-2 deg. 240 239.75 240.25
Difference between angles 5
Cal 1-4 deg. 300 299.75 300.25
Cal 1-4 deg. 300 299.75 300.25
Injection quantity adjustment
Rack position
(14.9)
PWM
%
71.9
Pump speed
r/min
700
700
700
Average injection quantity
mm3/st.
219
217
221
Max. variation between cylinders
%
0
-3
3
Basic
*
PS407980-224*
V
2.2+-0.0
1
PS407980-224*
mm
4.6+-0.0
5
Injection quantity adjustment_02
Rack position
(6.9)
PWM
%
26.9+-2.
8
Pump speed
r/min
390
390
390
Average injection quantity
mm3/st.
15
11.8
18.2
Max. variation between cylinders
%
0
-13
13
PS407980-224*
V
V1+0.05+
-0.01
PS407980-224*
mm
6.9+-0.0
3
Remarks
Refer to items regarding the pre-stroke actuator
Refer to items regarding the pre-stroke actuator
0000001201
Pre-stroke
mm
7
6.97
7.03
Remarks
When the timing sleeve is pushed up
When the timing sleeve is pushed up
_02
Connector angle
deg.
11.5
11
12
Remarks
When the eccentric pin is tightened
When the eccentric pin is tightened
_03
Supply voltage
V
24
23.5
24.5
Ambient temperature
degC
23
18
28
Pre-stroke
mm
3
2.95
3.05
Output voltage
V
2.95
2.94
2.96
Adjustment
*
_04
Supply voltage
V
24
23.5
24.5
Ambient temperature
degC
23
18
28
Pre-stroke
mm
7
6.97
7.03
Output voltage
V
1.2
1
1.4
Confirmation
*
Remarks
Output voltage V1
Output voltage V1
_05
Supply voltage
V
24
23.5
24.5
Ambient temperature
degC
23
18
28
Output voltage
V
3.05
3.05
Confirmation of operating range
*
Test data Ex:
Speed control lever angle
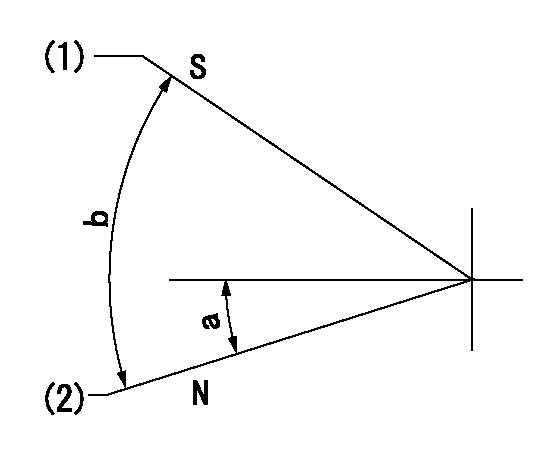
N:Pump normal
S:Stop the pump.
(1)Rack position = aa
(2)Rack position bb
----------
aa=1mm bb=20mm
----------
a=17deg+-5deg b=37deg+-5deg
----------
aa=1mm bb=20mm
----------
a=17deg+-5deg b=37deg+-5deg
0000000901

(1)Pump vertical direction
(2)Position of coupling's threaded hole at No 1 cylinder's beginning of injection
(3)B.T.D.C.: aa
(4)Pre-stroke: bb
----------
aa=4deg bb=7+-0.03mm
----------
a=(100deg)
----------
aa=4deg bb=7+-0.03mm
----------
a=(100deg)
0000001501
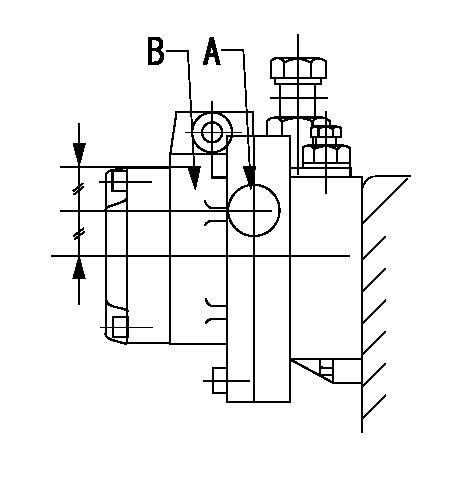
A:Sealing position
B:Pre-stroke actuator
1. When installing the pre-stroke actuator on the pump, first tighten the installation bolts loosely, then move the actuator fully counterclockwise (viewed from the drive side).
Temporary tightening torque: 1 - 1.5 N.m (0.1 - 0.15 kgf.m)
2. Move the actuator in the clockwise direction when viewed from the drive side, and adjust so that it becomes the adjustment point of the adjustment value. Then tighten it.
Tightening torque: 7^9 N.m (0.7^0.9 kgf.m)
3. After prestroke actuator installation adjustment, simultaneously stamp both the actuator side and housing side.
----------
----------
----------
----------
0000001701

(PWM) Pulse width modulation (%)
(R) Rack position (mm)
Rack sensor output characteristics
1. Rack limit adjustment
(1)Measure the rack position R2 for PWM a2%.
(2)Confirm that it is within the range R2 = 15+-1 mm.
(3)Measure the rack position R1 at PWM a %.
(4)Confirm that it is within the range R2 - R1 = 10+-0.1 mm.
2. Check the limp home operation.
(1)Move the switch box's limp home switch to the limp home side.
(2)Confirm rack position L1 (mm ) and L2 (mm) for PWM in the above table.
3. Check the pull down operation.
(1)Confirm that the rack position is 19 mm at PWM B%.
(2)In the conditions described in the above table, move the switch box's pull down switch to the pull down side and confirm that the rack position momentarily becomes 1 mm or less.
----------
a1=16.25 % a2=72.5 % L1=1-- mm L2=19++mm A=5 % B=95 %
----------
----------
a1=16.25 % a2=72.5 % L1=1-- mm L2=19++mm A=5 % B=95 %
----------
Information:
1. If necessary, remove the injector clamp bolt and clamp.
Illustration 1. Remove Clamp Bolt And Clamp.2. Remove jumper tube by removing two socket head cap screws on one end and loosening the tube nut on the other end. Refer to Illustrations 2 and 3.
Illustration 2. Remove Two Cap Screws.
Illustration 3. Loosen Tube Nut.
Make sure the small seat, shown in Illustration 4, is removed. Do not allow the seat to fall into any engine cavity, which could result in damage if unintentionally left inside the engine.Also, make sure the jumper tube is kept clean at all times. Dirt or other debris can get into the engine with this tube removed and cause possible damage.
Illustration 4. Do Not Lose Or Misplace Tube Seat.3. Remove four bolts and rocker arm assembly.
Illustration 5. Remove Rocker Arm Assembly.4. Remove inlet manifold bolt, as shown in Illustration 6.
Illustration 6. Remove Manifold Bolt.5. Remove the unit injector.6. Install a new injector brass sleeve or inspect and ream the existing sleeves as outlined in Tool Operating Manual NEHS0675. It is not necessary to ream new sleeves when using this procedure.7. Install the unit injector.
Do not install the injectors "off-engine" because the injector tip will protrude from the head and be subject to damage. If the injectors are installed off-engine, make sure the bottom surface of the head is raised off the surface of the work bench.
8. Install the injector forcing cover (8). Make sure the extending portion (small dowel) is in the oil supply hole of the injector. Also make sure wear button (10) is in place.
Illustration 7. Install Injector Forcing Cover (8) With Wear Button (10).9. Place a small amount of 4C-5591 Thread Lubricant on top of the injector forcing cover's wear button (10) and on the threads of forcing bolt (4).
Complete lubrication of the wear button and forcing bolt must be maintained for each injector seating procedure. Failure to relubricate each part before seating the next injector may cause premature wear or tool damage. Also, make sure the forcing bolt turns freely and does not have any damaged threads.
Illustration 8. Put A Small Amount Of Thread Lubricant On Wear Button.10. Install the forcing bridge with three 7X-0457 Bolts (5) and three 9M-1974 Hard Washers (6). Put the two long legs of the forcing bridge in the two rocker arm shaft support holes closest to the injector. The short leg of the forcing bridge sits on the intake manifold bolt boss.
Illustration 9. Install Forcing Bridge.11. Tighten forcing bridge mounting bolts (5) to 28 7 N m, 2.9 0.7 meter kg, (21 5 lb. ft.).
Damage to the head could occur if bridge mounting bolts (5) are not tightened to the specified torque.
Illustration 10. Tighten Forcing Bridge Bolts.12. Tighten the forcing bolt finger tight.13. Use a 9U-5019 Torque Wrench and tighten the forcing bolts to 34 1.4 N m, 3.5
Illustration 1. Remove Clamp Bolt And Clamp.2. Remove jumper tube by removing two socket head cap screws on one end and loosening the tube nut on the other end. Refer to Illustrations 2 and 3.
Illustration 2. Remove Two Cap Screws.
Illustration 3. Loosen Tube Nut.
Make sure the small seat, shown in Illustration 4, is removed. Do not allow the seat to fall into any engine cavity, which could result in damage if unintentionally left inside the engine.Also, make sure the jumper tube is kept clean at all times. Dirt or other debris can get into the engine with this tube removed and cause possible damage.
Illustration 4. Do Not Lose Or Misplace Tube Seat.3. Remove four bolts and rocker arm assembly.
Illustration 5. Remove Rocker Arm Assembly.4. Remove inlet manifold bolt, as shown in Illustration 6.
Illustration 6. Remove Manifold Bolt.5. Remove the unit injector.6. Install a new injector brass sleeve or inspect and ream the existing sleeves as outlined in Tool Operating Manual NEHS0675. It is not necessary to ream new sleeves when using this procedure.7. Install the unit injector.
Do not install the injectors "off-engine" because the injector tip will protrude from the head and be subject to damage. If the injectors are installed off-engine, make sure the bottom surface of the head is raised off the surface of the work bench.
8. Install the injector forcing cover (8). Make sure the extending portion (small dowel) is in the oil supply hole of the injector. Also make sure wear button (10) is in place.
Illustration 7. Install Injector Forcing Cover (8) With Wear Button (10).9. Place a small amount of 4C-5591 Thread Lubricant on top of the injector forcing cover's wear button (10) and on the threads of forcing bolt (4).
Complete lubrication of the wear button and forcing bolt must be maintained for each injector seating procedure. Failure to relubricate each part before seating the next injector may cause premature wear or tool damage. Also, make sure the forcing bolt turns freely and does not have any damaged threads.
Illustration 8. Put A Small Amount Of Thread Lubricant On Wear Button.10. Install the forcing bridge with three 7X-0457 Bolts (5) and three 9M-1974 Hard Washers (6). Put the two long legs of the forcing bridge in the two rocker arm shaft support holes closest to the injector. The short leg of the forcing bridge sits on the intake manifold bolt boss.
Illustration 9. Install Forcing Bridge.11. Tighten forcing bridge mounting bolts (5) to 28 7 N m, 2.9 0.7 meter kg, (21 5 lb. ft.).
Damage to the head could occur if bridge mounting bolts (5) are not tightened to the specified torque.
Illustration 10. Tighten Forcing Bridge Bolts.12. Tighten the forcing bolt finger tight.13. Use a 9U-5019 Torque Wrench and tighten the forcing bolts to 34 1.4 N m, 3.5