Information injection-pump assembly
ZEXEL
108622-1170
1086221170
ISUZU
1156033060
1156033060
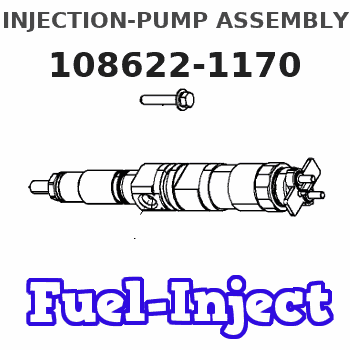
Rating:
Service parts 108622-1170 INJECTION-PUMP ASSEMBLY:
1.
_
5.
AUTOM. ADVANCE MECHANIS
7.
COUPLING PLATE
11.
Nozzle and Holder
1-15300-371-2
12.
Open Pre:MPa(Kqf/cm2)
17.7{180}/22.1{225}
14.
NOZZLE
Include in #1:
108622-1170
as INJECTION-PUMP ASSEMBLY
Cross reference number
ZEXEL
108622-1170
1086221170
ISUZU
1156033060
1156033060
Zexel num
Bosch num
Firm num
Name
Calibration Data:
Adjustment conditions
Test oil
1404 Test oil ISO4113 or {SAEJ967d}
1404 Test oil ISO4113 or {SAEJ967d}
Test oil temperature
degC
40
40
45
Nozzle and nozzle holder
105780-8250
Bosch type code
1 688 901 101
Nozzle
105780-0120
Bosch type code
1 688 901 990
Nozzle holder
105780-2190
Opening pressure
MPa
20.7
Opening pressure
kgf/cm2
211
Injection pipe
Outer diameter - inner diameter - length (mm) mm 8-3-600
Outer diameter - inner diameter - length (mm) mm 8-3-600
Overflow valve
134424-4320
Overflow valve opening pressure
kPa
255
221
289
Overflow valve opening pressure
kgf/cm2
2.6
2.25
2.95
Tester oil delivery pressure
kPa
255
255
255
Tester oil delivery pressure
kgf/cm2
2.6
2.6
2.6
RED4 control unit part number
407915-0
590
RED4 rack sensor specifications
mm
19
PS/ACT control unit part no.
407980-2
24*
Digi switch no.
33
Direction of rotation (viewed from drive side)
Right R
Right R
Injection timing adjustment
Direction of rotation (viewed from drive side)
Right R
Right R
Injection order
1-5-3-6-
2-4
Pre-stroke
mm
7
6.97
7.03
Beginning of injection position
Drive side NO.1
Drive side NO.1
Difference between angles 1
Cal 1-5 deg. 60 59.75 60.25
Cal 1-5 deg. 60 59.75 60.25
Difference between angles 2
Cal 1-3 deg. 120 119.75 120.25
Cal 1-3 deg. 120 119.75 120.25
Difference between angles 3
Cal 1-6 deg. 180 179.75 180.25
Cal 1-6 deg. 180 179.75 180.25
Difference between angles 4
Cyl.1-2 deg. 240 239.75 240.25
Cyl.1-2 deg. 240 239.75 240.25
Difference between angles 5
Cal 1-4 deg. 300 299.75 300.25
Cal 1-4 deg. 300 299.75 300.25
Injection quantity adjustment
Rack position
(15)
PWM
%
72.7
Pump speed
r/min
700
700
700
Average injection quantity
mm3/st.
224
222
226
Max. variation between cylinders
%
0
-3
3
Basic
*
PS407980-224*
V
2.2+-0.0
1
PS407980-224*
mm
4.6+-0.0
5
Injection quantity adjustment_02
Rack position
(6.8)
PWM
%
26.1+-2.
8
Pump speed
r/min
360
360
360
Average injection quantity
mm3/st.
11.5
8.3
14.7
Max. variation between cylinders
%
0
-13
13
PS407980-224*
V
V1+0.05+
-0.01
PS407980-224*
mm
6.9+-0.0
3
Remarks
Refer to items regarding the pre-stroke actuator
Refer to items regarding the pre-stroke actuator
0000001201
Pre-stroke
mm
7
6.97
7.03
Remarks
When the timing sleeve is pushed up
When the timing sleeve is pushed up
_02
Connector angle
deg.
8.5
8
9
Remarks
When the eccentric pin is tightened
When the eccentric pin is tightened
_03
Supply voltage
V
24
23.5
24.5
Ambient temperature
degC
23
18
28
Pre-stroke
mm
3
2.95
3.05
Output voltage
V
2.95
2.94
2.96
Adjustment
*
_04
Supply voltage
V
24
23.5
24.5
Ambient temperature
degC
23
18
28
Pre-stroke
mm
7
6.97
7.03
Output voltage
V
1.2
1
1.4
Confirmation
*
Remarks
Output voltage V1
Output voltage V1
_05
Supply voltage
V
24
23.5
24.5
Ambient temperature
degC
23
18
28
Output voltage
V
3.05
3.05
Confirmation of operating range
*
Test data Ex:
Speed control lever angle
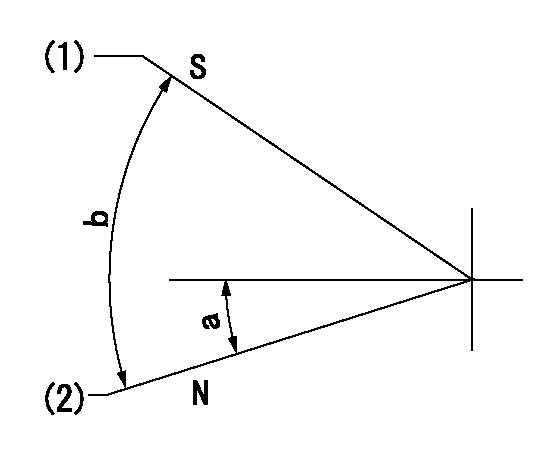
N:Pump normal
S:Stop the pump.
(1)Rack position = aa
(2)Rack position bb
----------
aa=1mm bb=20mm
----------
a=17deg+-5deg b=37deg+-5deg
----------
aa=1mm bb=20mm
----------
a=17deg+-5deg b=37deg+-5deg
0000000901

(1)Pump vertical direction
(2)Position of coupling's threaded hole at No 1 cylinder's beginning of injection
(3)B.T.D.C.: aa
(4)Pre-stroke: bb
----------
aa=4deg bb=7+-0.03mm
----------
a=(100deg)
----------
aa=4deg bb=7+-0.03mm
----------
a=(100deg)
0000001501
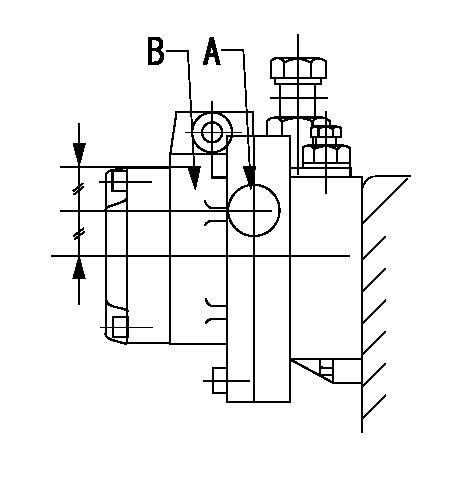
A:Sealing position
B:Pre-stroke actuator
1. When installing the pre-stroke actuator on the pump, first tighten the installation bolts loosely, then move the actuator fully counterclockwise (viewed from the drive side).
Temporary tightening torque: 1 - 1.5 N.m (0.1 - 0.15 kgf.m)
2. Move the actuator in the clockwise direction when viewed from the drive side, and adjust so that it becomes the adjustment point of the adjustment value. Then tighten it.
Tightening torque: 7^9 N.m (0.7^0.9 kgf.m)
3. After prestroke actuator installation adjustment, simultaneously stamp both the actuator side and housing side.
----------
----------
----------
----------
0000001701

(PWM) Pulse width modulation (%)
(R) Rack position (mm)
Rack sensor output characteristics
1. Rack limit adjustment
(1)Measure the rack position R2 for PWM a2%.
(2)Confirm that it is within the range R2 = 15+-1 mm.
(3)Measure the rack position R1 at PWM a %.
(4)Confirm that it is within the range R2 - R1 = 10+-0.1 mm.
2. Check the limp home operation.
(1)Move the switch box's limp home switch to the limp home side.
(2)Confirm rack position L1 (mm ) and L2 (mm) for PWM in the above table.
3. Check the pull down operation.
(1)Confirm that the rack position is 19 mm at PWM B%.
(2)In the conditions described in the above table, move the switch box's pull down switch to the pull down side and confirm that the rack position momentarily becomes 1 mm or less.
----------
a1=16.25% a2=72.5% L1=1--mm L2=19++mm A=5% B=95%
----------
----------
a1=16.25% a2=72.5% L1=1--mm L2=19++mm A=5% B=95%
----------
Information:
3406B and 3406C Non-Peec Engines
Steps 4 through 7 do not apply to PEEC engines.
Illustration 16. Install Lever Assembly
(1) 6N-3646 Lever. (2) 5P-0537 Washer. (3) 6V-8918 Bolt. (4) 9M-3858 Rack Preload Spring. (5) 1B-7182 Bolt.4. Install lever (1) with washer (2) and bolt (3).5. Install bolt (5) into hole as shown.6. Hook spring (4) between bolt (5) and lever (1).
Illustration 17. Install Rack Positioning Assembly
(1) 9U-5296 Rack Assembly. (2) Original cover mounting bolts or 4F-7957 Bolt.7. Install rack positioning assembly (1) with bolts (2). Use rack positioning assembly (1) as a "fuel ON" and "fuel OFF" control. Position the assembly to the full "fuel ON" position for all tests. Use the positioning assembly for rack adjustment.3406 Peec Engines
Steps 8 and 9 do not apply to Non-PEEC engines.
Illustration 18. Installing testing hardware for 3406 PEEC Engines
(1) 9U-5292 Rack Preload Assembly. (2) 9U-5120 Spanner Wrench. (3) 9U-5295 Positioning Assembly.8. Remove the BTM from the injection pump and install the 9U-5292 Rack Preload Assembly (1). Make sure the pin is properly located in the slot of the servo shaft. After installing the rack preload assembly, finger tighten the bolts.9. Remove the shut-off solenoid with a 9U-5120 Spanner Wrench (2) and install 9U-5295 Positioning Assembly (3). Use rack preload assembly (1) as a "fuel ON" and "fuel OFF" control. Position the assembly to the full "fuel ON" position for all tests. Use the positioning assembly for rack adjustment.Connect Hoses and Lines
Illustration 19. Connect Lube Oil Supply and Drain Hose
(1) 7G-7105 Hose. (2) 5P-6661 Fitting. (3) 9U-7709 Oil Drain Tube and two 5D-1026 Hose Clamps.
Illustration 20. Connect Fuel Supply and Return Lines
(4) 030-7947 Fitting, 3J-1907 O-ring Seal, and 7G-7105 Hose. (5) 8T-2160 Orifice Fitting, 3J-1907 O-ring Seal, and 7G-7105 Hose. (6) 9U-5298 Fuel Injection Line Tube Assembly (verify fuel line part number in TMI).1. Attach one end of hose (1) to the Lube Oil Supply fitting on the test stand. Attach the other end to the 5P-6661 Fitting on the rear support.2. Connect the oil drain tube (2) to the rear support and the test stand's stand-pipe with two hose clamps. On the AVM20-12C, the drain hose can be routed to the lube oil drain pan.3. Install fitting, O-ring, and hose (4) onto the fuel injection pump. Connect the other end of the hose to the "Test Oil Supply" connection on the test stand.4. Install fitting, O-ring, and hose (5) onto the fuel injection pump. Connect the other end of the hose to the "Test Oil Return" connection on the test stand.
Hold nut on 9U-6705 Master Nozzle when tightening fuel injection line tube assemblies (6). If the nut is not held in place during tightening, the master nozzle can be damaged.
5. Install six fuel injection line tube assemblies (6).Pre-Test Checks
1. Remove the lock-out on the electrical box, if installed.2. Release the Emergency Stop button.3. Start the bench and visually check for oil leaks from covers, hoses, etc.4. Check for oil flow through the drain tube. Also, check for oil flowing out of the oil
Steps 4 through 7 do not apply to PEEC engines.
Illustration 16. Install Lever Assembly
(1) 6N-3646 Lever. (2) 5P-0537 Washer. (3) 6V-8918 Bolt. (4) 9M-3858 Rack Preload Spring. (5) 1B-7182 Bolt.4. Install lever (1) with washer (2) and bolt (3).5. Install bolt (5) into hole as shown.6. Hook spring (4) between bolt (5) and lever (1).
Illustration 17. Install Rack Positioning Assembly
(1) 9U-5296 Rack Assembly. (2) Original cover mounting bolts or 4F-7957 Bolt.7. Install rack positioning assembly (1) with bolts (2). Use rack positioning assembly (1) as a "fuel ON" and "fuel OFF" control. Position the assembly to the full "fuel ON" position for all tests. Use the positioning assembly for rack adjustment.3406 Peec Engines
Steps 8 and 9 do not apply to Non-PEEC engines.
Illustration 18. Installing testing hardware for 3406 PEEC Engines
(1) 9U-5292 Rack Preload Assembly. (2) 9U-5120 Spanner Wrench. (3) 9U-5295 Positioning Assembly.8. Remove the BTM from the injection pump and install the 9U-5292 Rack Preload Assembly (1). Make sure the pin is properly located in the slot of the servo shaft. After installing the rack preload assembly, finger tighten the bolts.9. Remove the shut-off solenoid with a 9U-5120 Spanner Wrench (2) and install 9U-5295 Positioning Assembly (3). Use rack preload assembly (1) as a "fuel ON" and "fuel OFF" control. Position the assembly to the full "fuel ON" position for all tests. Use the positioning assembly for rack adjustment.Connect Hoses and Lines
Illustration 19. Connect Lube Oil Supply and Drain Hose
(1) 7G-7105 Hose. (2) 5P-6661 Fitting. (3) 9U-7709 Oil Drain Tube and two 5D-1026 Hose Clamps.
Illustration 20. Connect Fuel Supply and Return Lines
(4) 030-7947 Fitting, 3J-1907 O-ring Seal, and 7G-7105 Hose. (5) 8T-2160 Orifice Fitting, 3J-1907 O-ring Seal, and 7G-7105 Hose. (6) 9U-5298 Fuel Injection Line Tube Assembly (verify fuel line part number in TMI).1. Attach one end of hose (1) to the Lube Oil Supply fitting on the test stand. Attach the other end to the 5P-6661 Fitting on the rear support.2. Connect the oil drain tube (2) to the rear support and the test stand's stand-pipe with two hose clamps. On the AVM20-12C, the drain hose can be routed to the lube oil drain pan.3. Install fitting, O-ring, and hose (4) onto the fuel injection pump. Connect the other end of the hose to the "Test Oil Supply" connection on the test stand.4. Install fitting, O-ring, and hose (5) onto the fuel injection pump. Connect the other end of the hose to the "Test Oil Return" connection on the test stand.
Hold nut on 9U-6705 Master Nozzle when tightening fuel injection line tube assemblies (6). If the nut is not held in place during tightening, the master nozzle can be damaged.
5. Install six fuel injection line tube assemblies (6).Pre-Test Checks
1. Remove the lock-out on the electrical box, if installed.2. Release the Emergency Stop button.3. Start the bench and visually check for oil leaks from covers, hoses, etc.4. Check for oil flow through the drain tube. Also, check for oil flowing out of the oil