Information injection-pump assembly
BOSCH
9 400 611 772
9400611772
ZEXEL
108622-1152
1086221152
ISUZU
1156032903
1156032903
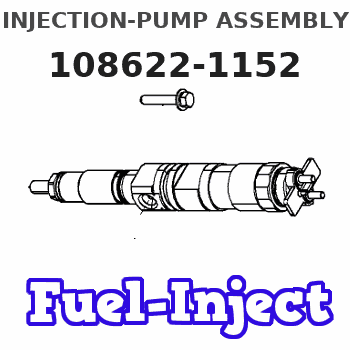
Rating:
Service parts 108622-1152 INJECTION-PUMP ASSEMBLY:
1.
_
5.
AUTOM. ADVANCE MECHANIS
7.
COUPLING PLATE
11.
Nozzle and Holder
1-15300-358-1
12.
Open Pre:MPa(Kqf/cm2)
22.1{225}
15.
NOZZLE SET
Include in #1:
108622-1152
as INJECTION-PUMP ASSEMBLY
Cross reference number
BOSCH
9 400 611 772
9400611772
ZEXEL
108622-1152
1086221152
ISUZU
1156032903
1156032903
Zexel num
Bosch num
Firm num
Name
9 400 611 772
1156032903 ISUZU
INJECTION-PUMP ASSEMBLY
6WA1-TC * K 14CJ TICS HD-TI6M TICS
6WA1-TC * K 14CJ TICS HD-TI6M TICS
Calibration Data:
Adjustment conditions
Test oil
1404 Test oil ISO4113 or {SAEJ967d}
1404 Test oil ISO4113 or {SAEJ967d}
Test oil temperature
degC
40
40
45
Nozzle and nozzle holder
105780-8250
Bosch type code
1 688 901 101
Nozzle
105780-0120
Bosch type code
1 688 901 990
Nozzle holder
105780-2190
Opening pressure
MPa
20.7
Opening pressure
kgf/cm2
211
Injection pipe
Outer diameter - inner diameter - length (mm) mm 8-3-600
Outer diameter - inner diameter - length (mm) mm 8-3-600
Overflow valve
131424-7120
Overflow valve opening pressure
kPa
255
221
289
Overflow valve opening pressure
kgf/cm2
2.6
2.25
2.95
Tester oil delivery pressure
kPa
255
255
255
Tester oil delivery pressure
kgf/cm2
2.6
2.6
2.6
PS/ACT control unit part no.
407980-2
24*
Digi switch no.
32
Direction of rotation (viewed from drive side)
Right R
Right R
Injection timing adjustment
Direction of rotation (viewed from drive side)
Right R
Right R
Injection order
1-5-3-6-
2-4
Pre-stroke
mm
6.4
6.37
6.43
Beginning of injection position
Drive side NO.1
Drive side NO.1
Difference between angles 1
Cal 1-5 deg. 60 59.75 60.25
Cal 1-5 deg. 60 59.75 60.25
Difference between angles 2
Cal 1-3 deg. 120 119.75 120.25
Cal 1-3 deg. 120 119.75 120.25
Difference between angles 3
Cal 1-6 deg. 180 179.75 180.25
Cal 1-6 deg. 180 179.75 180.25
Difference between angles 4
Cyl.1-2 deg. 240 239.75 240.25
Cyl.1-2 deg. 240 239.75 240.25
Difference between angles 5
Cal 1-4 deg. 300 299.75 300.25
Cal 1-4 deg. 300 299.75 300.25
Injection quantity adjustment
Adjusting point
-
Rack position
14.5
Pump speed
r/min
700
700
700
Average injection quantity
mm3/st.
216
214
218
Max. variation between cylinders
%
0
-3
3
Basic
*
Fixing the rack
*
PS407980-224*
V
2.45+-0.
01
PS407980-224*
mm
4+-0.05
Standard for adjustment of the maximum variation between cylinders
*
Injection quantity adjustment_02
Adjusting point
Z
Rack position
6.5+-0.5
Pump speed
r/min
370
370
370
Average injection quantity
mm3/st.
15
11.8
18.2
Max. variation between cylinders
%
0
-13
13
Fixing the rack
*
PS407980-224*
V
V1+0.05+
-0.01
PS407980-224*
mm
6.3+-0.0
3
Standard for adjustment of the maximum variation between cylinders
*
Remarks
Refer to items regarding the pre-stroke actuator
Refer to items regarding the pre-stroke actuator
Injection quantity adjustment_03
Adjusting point
A
Rack position
R1(14.5)
Pump speed
r/min
700
700
700
Average injection quantity
mm3/st.
216
214
218
Basic
*
Fixing the lever
*
Boost pressure
kPa
58.7
58.7
Boost pressure
mmHg
440
440
PS407980-224*
V
2.45+-0.
05
PS407980-224*
mm
4+-0.05
Boost compensator adjustment
Pump speed
r/min
800
800
800
Rack position
R2-2.2
Boost pressure
kPa
21.3
20
22.6
Boost pressure
mmHg
160
150
170
Boost compensator adjustment_02
Pump speed
r/min
800
800
800
Rack position
R2(R1+0.
15)
Boost pressure
kPa
45.3
45.3
45.3
Boost pressure
mmHg
340
340
340
0000001601
Pre-stroke
mm
6.4
6.37
6.43
Remarks
When the timing sleeve is pushed up
When the timing sleeve is pushed up
_02
Connector angle
deg.
8.5
8
9
Remarks
When the eccentric pin is tightened
When the eccentric pin is tightened
_03
Supply voltage
V
24
23.5
24.5
Ambient temperature
degC
23
18
28
Pre-stroke
mm
4
3.95
4.05
Output voltage
V
2.45
2.44
2.46
Adjustment
*
_04
Supply voltage
V
24
23.5
24.5
Ambient temperature
degC
23
18
28
Pre-stroke
mm
6.4
6.37
6.43
Output voltage
V
1.2
1
1.4
Confirmation
*
Remarks
Output voltage V1
Output voltage V1
_05
Supply voltage
V
24
23.5
24.5
Ambient temperature
degC
23
18
28
Pre-stroke
mm
3.4
Output voltage
V
3
2.98
3
Confirmation
*
_06
Supply voltage
V
24
23.5
24.5
Ambient temperature
degC
23
18
28
Output voltage
V
3.05
3.05
Confirmation of operating range
*
Test data Ex:
Governor adjustment
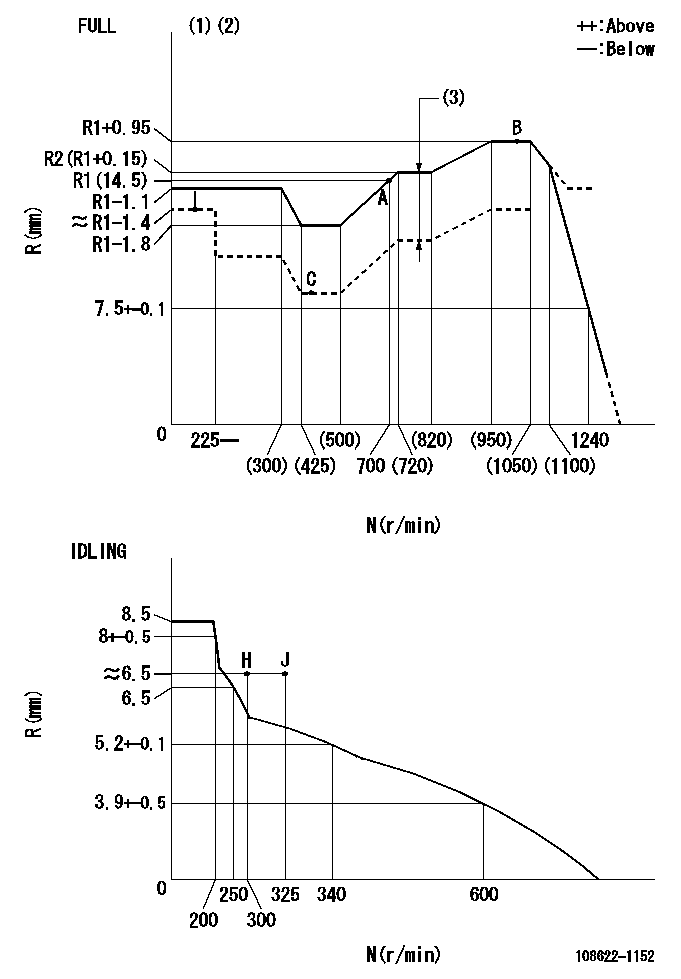
N:Pump speed
R:Rack position (mm)
(1)Torque cam stamping: T1
(2)Tolerance for racks not indicated: +-0.05mm.
(3)Boost compensator stroke: BCL
----------
T1=AG18 BCL=2.2+-0.1mm
----------
----------
T1=AG18 BCL=2.2+-0.1mm
----------
Speed control lever angle
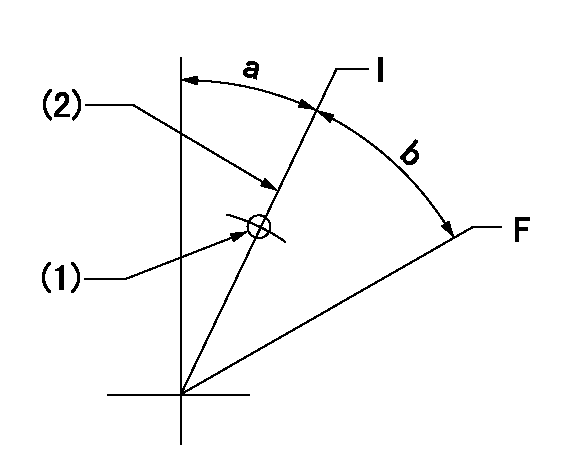
F:Full speed
I:Idle
(1)Use the pin at R = aa
(2)Stopper bolt set position 'H'
----------
aa=32mm
----------
a=1.5deg+-5deg b=35.5deg+-3deg
----------
aa=32mm
----------
a=1.5deg+-5deg b=35.5deg+-3deg
Stop lever angle
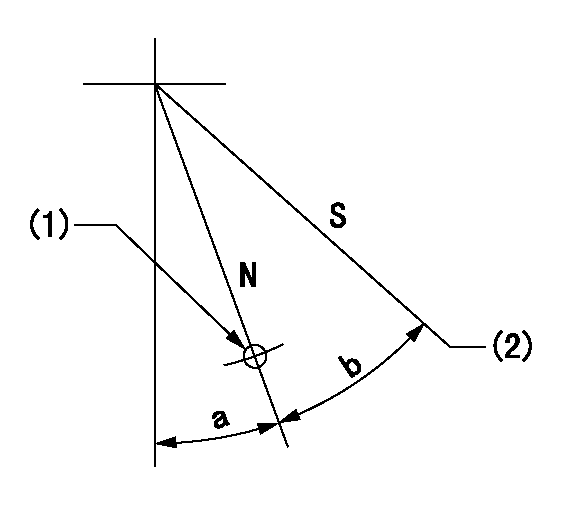
N:Pump normal
S:Stop the pump.
(1)Use the pin at R = aa
(2)Set the stopper bolt so that speed = bb and rack position = cc. (Confirm non-injection.)
----------
aa=40mm bb=0r/min cc=1+-0.3mm
----------
a=18deg+-5deg b=44deg+-5deg
----------
aa=40mm bb=0r/min cc=1+-0.3mm
----------
a=18deg+-5deg b=44deg+-5deg
0000001301

(1)Pump vertical direction
(2)Position of flywheel's threaded hole at No 1 cylinder's beginning of injection
(3)B.T.D.C.: aa
(4)Pre-stroke: bb
----------
aa=5deg bb=6.4+-0.03mm
----------
a=(100deg)
----------
aa=5deg bb=6.4+-0.03mm
----------
a=(100deg)
0000001901
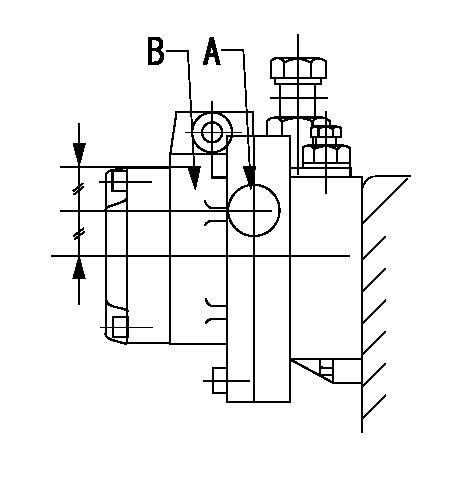
A:Sealing position
B:Pre-stroke actuator
1. When installing the pre-stroke actuator on the pump, first tighten the installation bolts loosely, then move the actuator fully counterclockwise (viewed from the drive side).
Temporary tightening torque: 1 - 1.5 N.m (0.1 - 0.15 kgf.m)
2. Move the actuator in the clockwise direction when viewed from the drive side, and adjust so that it becomes the adjustment point of the adjustment value. Then tighten it.
Tightening torque: 7^9 N.m (0.7^0.9 kgf.m)
3. After prestroke actuator installation adjustment, simultaneously stamp both the actuator side and housing side.
----------
----------
----------
----------
0000002201 RACK SENSOR

G:Red paint
H:Pump end face
P/N: part number of suitable shim
(1)Threaded type rack block
(2)Welded type rack block
Rack sensor adjustment
1. Threaded type rack sensor (-5*20, P type, no TICS rack limit).
(1)Screw in the bobbin (A) until it contacts the joint (B).
(2)Fix the pump lever.
(3)At speed N1 and rack position Ra, adjust the amount that the bobbin is screwed in so that the amp's output voltage is V1.
(4)Fix using the nut (F).
(5)Affix the caution plate to the upper part of the joint (B).
(6)Apply (G) at two places.
Connecting part between the joint (B) and the nut (F)
Connecting part between the end surface of the pump (H) and the joint (B)
2. Range for screw-in adjustment between the bobbin (A) and the joint (B) is 9 threads.
Screw in to the end from (the position where the bobbin (A) is rotated 9 turns).
Speed N1, rack position Ra, output voltage V1, rack sensor supply voltage 5+-0.01 (V)
----------
Ra=R1(14.5)+0.95mm N1=1000r/min V1=3+-0.01V
----------
----------
Ra=R1(14.5)+0.95mm N1=1000r/min V1=3+-0.01V
----------
Information:
* For the frequency and timing of cleaning, refer to the relevant instruction manual. More frequent cleaning than necessary could damage the element or cause dust and foreign matter to be sucked into the engine.* Do not strike the element or hit it against another object to remove dust.* Do not blow compressed air against outside surfaces of the element.
Inspection Procedure Inspection: Outer Element* Shine some electric light inside the element.* Replace the element if thin spots or broken parts are evident in the filter paper, or if the packing at the top of the element is damaged. Also replace the element if the dust on the element is damp with oily smoke or soot, regardless of the replacement schedule. Inspection: Operation of dust indicator under specific negative pressure * Perform the following inspection and, if faulty, replace the dust indicator.* With no vacuum applied to the dust indicator, take measurement between the terminals 1 and 2. There should be no continuity.* Gradually apply vacuum to the dust indicator. Measure the vacuum when the continuity is made between the terminals 1 and 2.Turbocharger
Removal Sequence1 Turbocharger coupler2 Gasket3 Turbocharger insulator B4 Turbocharger insulator A5 Oil return pipe6 Gasket7 Eyebolt8 Oil pipe9 Turbocharger (See later sections.)10 Gasket*a: Exhaust manifoldX: Non-reusable parts Installation SequenceFollow the removal sequence in reverse.Tightening torque (Unit: N m {kgf m} Lubricant and/or sealant Installation Procedure Installation: Turbocharger* When installing the turbocharger, pour an appropriate amount of engine oil from the oil port so that each part operates smoothly.Turbocharger Disassembly Sequence1 Hose2 Actuator3 Coupling4 Turbine housing5 Snap ring6 Compressor cover7 O-ring8 Cartridge assemblyX: Non-resusable parts Assembly SequenceFollow the disassembly sequence in reverse.Service standards (Unit: mm) Tightening torque (Unit: N m {kgf m} Lubricant and/or sealant Work Before Removal Mating Marks* Draw a line across the coupling, turbine housing, compressor cover, and cartridge assembly. This line will serve as mating marks in the installation procedure. Removal Procedure Removal: Turbine housing
* Tap all around the end of the turbine housing with a rubber hammer or a similar tool, being careful not to damage the turbine housing.* Do not let the blades of the cartridge assembly hit the turbine housing, as they are easily bent.
Removal: Compressor Cover
* Tap all around the end of the turbine housing with a rubber hammer or a similar tool, being careful not damage the turbine housing.* Do not let the blades of the cartridge assembly hit the turbine housing, as they are easily bent.
Work after Disassembly Cleaning* Before cleaning the parts, carry out a visual inspection for any marks of burns or wear that may become difficult to find after the cleaning. If any defects are evident, replace the part(s).* Immerse the disassembled parts in an inflammable solvent (a 5 to 10 aqueous solution of Oil Clean from New Hope Co., Ltd.). Take out the parts from the solvent and dry them with compressed air. If there is any solid matter remaining on the parts, remove them with a plastic scraper or a bristle brush.
*
Inspection Procedure Inspection: Outer Element* Shine some electric light inside the element.* Replace the element if thin spots or broken parts are evident in the filter paper, or if the packing at the top of the element is damaged. Also replace the element if the dust on the element is damp with oily smoke or soot, regardless of the replacement schedule. Inspection: Operation of dust indicator under specific negative pressure * Perform the following inspection and, if faulty, replace the dust indicator.* With no vacuum applied to the dust indicator, take measurement between the terminals 1 and 2. There should be no continuity.* Gradually apply vacuum to the dust indicator. Measure the vacuum when the continuity is made between the terminals 1 and 2.Turbocharger
Removal Sequence1 Turbocharger coupler2 Gasket3 Turbocharger insulator B4 Turbocharger insulator A5 Oil return pipe6 Gasket7 Eyebolt8 Oil pipe9 Turbocharger (See later sections.)10 Gasket*a: Exhaust manifoldX: Non-reusable parts Installation SequenceFollow the removal sequence in reverse.Tightening torque (Unit: N m {kgf m} Lubricant and/or sealant Installation Procedure Installation: Turbocharger* When installing the turbocharger, pour an appropriate amount of engine oil from the oil port so that each part operates smoothly.Turbocharger Disassembly Sequence1 Hose2 Actuator3 Coupling4 Turbine housing5 Snap ring6 Compressor cover7 O-ring8 Cartridge assemblyX: Non-resusable parts Assembly SequenceFollow the disassembly sequence in reverse.Service standards (Unit: mm) Tightening torque (Unit: N m {kgf m} Lubricant and/or sealant Work Before Removal Mating Marks* Draw a line across the coupling, turbine housing, compressor cover, and cartridge assembly. This line will serve as mating marks in the installation procedure. Removal Procedure Removal: Turbine housing
* Tap all around the end of the turbine housing with a rubber hammer or a similar tool, being careful not to damage the turbine housing.* Do not let the blades of the cartridge assembly hit the turbine housing, as they are easily bent.
Removal: Compressor Cover
* Tap all around the end of the turbine housing with a rubber hammer or a similar tool, being careful not damage the turbine housing.* Do not let the blades of the cartridge assembly hit the turbine housing, as they are easily bent.
Work after Disassembly Cleaning* Before cleaning the parts, carry out a visual inspection for any marks of burns or wear that may become difficult to find after the cleaning. If any defects are evident, replace the part(s).* Immerse the disassembled parts in an inflammable solvent (a 5 to 10 aqueous solution of Oil Clean from New Hope Co., Ltd.). Take out the parts from the solvent and dry them with compressed air. If there is any solid matter remaining on the parts, remove them with a plastic scraper or a bristle brush.
*