Information injection-pump assembly
BOSCH
9 400 612 855
9400612855
ZEXEL
108622-0140
1086220140
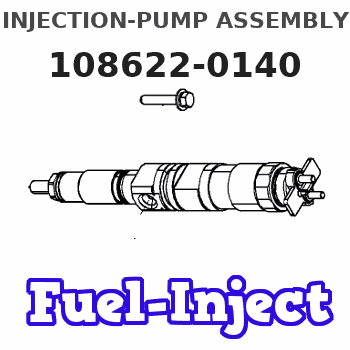
Rating:
Service parts 108622-0140 INJECTION-PUMP ASSEMBLY:
1.
_
5.
AUTOM. ADVANCE MECHANIS
9.
_
11.
Nozzle and Holder
16600-96611
12.
Open Pre:MPa(Kqf/cm2)
18.6{190}/22.6{230}
14.
NOZZLE
Include in #1:
108622-0140
as INJECTION-PUMP ASSEMBLY
Cross reference number
BOSCH
9 400 612 855
9400612855
ZEXEL
108622-0140
1086220140
Zexel num
Bosch num
Firm num
Name
Calibration Data:
Adjustment conditions
Test oil
1404 Test oil ISO4113 or {SAEJ967d}
1404 Test oil ISO4113 or {SAEJ967d}
Test oil temperature
degC
40
40
45
Nozzle and nozzle holder
105780-8250
Bosch type code
1 688 901 101
Nozzle
105780-0120
Bosch type code
1 688 901 990
Nozzle holder
105780-2190
Opening pressure
MPa
20.7
Opening pressure
kgf/cm2
211
Injection pipe
Outer diameter - inner diameter - length (mm) mm 8-3-600
Outer diameter - inner diameter - length (mm) mm 8-3-600
Overflow valve
134424-4120
Overflow valve opening pressure
kPa
255
221
289
Overflow valve opening pressure
kgf/cm2
2.6
2.25
2.95
Tester oil delivery pressure
kPa
255
255
255
Tester oil delivery pressure
kgf/cm2
2.6
2.6
2.6
RED3 control unit part number
407910-3
960
RED3 rack sensor specifications
mm
19
PS/ACT control unit part no.
407980-2
24*
Digi switch no.
31
Direction of rotation (viewed from drive side)
Right R
Right R
Injection timing adjustment
Direction of rotation (viewed from drive side)
Right R
Right R
Injection order
1-4-2-6-
3-5
Pre-stroke
mm
6.4
6.37
6.43
Beginning of injection position
Drive side NO.1
Drive side NO.1
Difference between angles 1
Cal 1-4 deg. 60 59.75 60.25
Cal 1-4 deg. 60 59.75 60.25
Difference between angles 2
Cyl.1-2 deg. 120 119.75 120.25
Cyl.1-2 deg. 120 119.75 120.25
Difference between angles 3
Cal 1-6 deg. 180 179.75 180.25
Cal 1-6 deg. 180 179.75 180.25
Difference between angles 4
Cal 1-3 deg. 240 239.75 240.25
Cal 1-3 deg. 240 239.75 240.25
Difference between angles 5
Cal 1-5 deg. 300 299.75 300.25
Cal 1-5 deg. 300 299.75 300.25
Injection quantity adjustment
Rack position
(16.1)
Vist
V
1.43
1.43
1.43
Pump speed
r/min
600
600
600
Average injection quantity
mm3/st.
195.5
193.5
197.5
Max. variation between cylinders
%
0
-4
4
Basic
*
PS407980-224*
V
2.45+-0.
01
PS407980-224*
mm
4+-0.05
Injection quantity adjustment_02
Rack position
(8.8)
Vist
V
2.5
2.4
2.6
Pump speed
r/min
275
275
275
Average injection quantity
mm3/st.
13.3
12.3
14.3
Max. variation between cylinders
%
0
-10
10
PS407980-224*
V
V1+0.05+
-0.01
PS407980-224*
mm
6.3+-0.0
3
Remarks
Refer to items regarding the pre-stroke actuator
Refer to items regarding the pre-stroke actuator
0000001201
Pre-stroke
mm
6.4
6.37
6.43
Remarks
When the timing sleeve is pushed up
When the timing sleeve is pushed up
_02
Connector angle
deg.
8.5
8
9
Remarks
When the eccentric pin is tightened
When the eccentric pin is tightened
_03
Supply voltage
V
24
23.5
24.5
Ambient temperature
degC
23
18
28
Pre-stroke
mm
4
3.95
4.05
Output voltage
V
2.45
2.44
2.46
Adjustment
*
_04
Supply voltage
V
24
23.5
24.5
Ambient temperature
degC
23
18
28
Pre-stroke
mm
6.4
6.37
6.43
Output voltage
V
1.2
1
1.4
Confirmation
*
Remarks
Output voltage V1
Output voltage V1
_05
Supply voltage
V
24
23.5
24.5
Ambient temperature
degC
23
18
28
Pre-stroke
mm
3.4
Output voltage
V
3
2.98
3
Confirmation
*
_06
Supply voltage
V
24
23.5
24.5
Ambient temperature
degC
23
18
28
Output voltage
V
3.05
3.05
Confirmation of operating range
*
Test data Ex:
Speed control lever angle
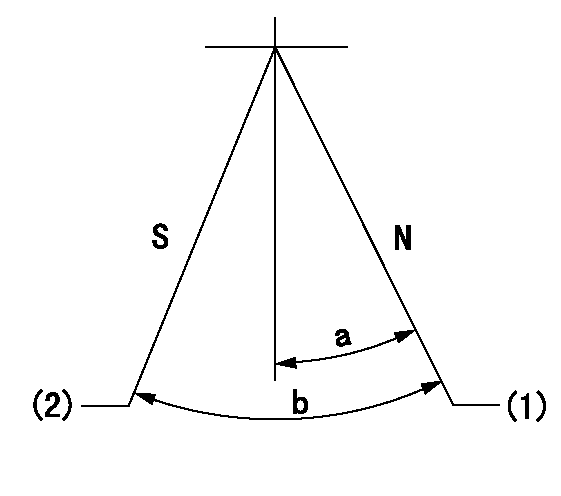
N:Pump normal
S:Stop the pump.
(1)Rack position = aa
(2)Rack position bb
----------
aa=20mm bb=1mm
----------
a=20deg+-5deg b=37deg+-5deg
----------
aa=20mm bb=1mm
----------
a=20deg+-5deg b=37deg+-5deg
0000000901

(1)Pump vertical direction
(2)Coupling's key groove position at No 1 cylinder's beginning of injection
(3)Pre-stroke: aa
(4)-
----------
aa=6.4+-0.03mm
----------
a=(30deg)
----------
aa=6.4+-0.03mm
----------
a=(30deg)
0000001501
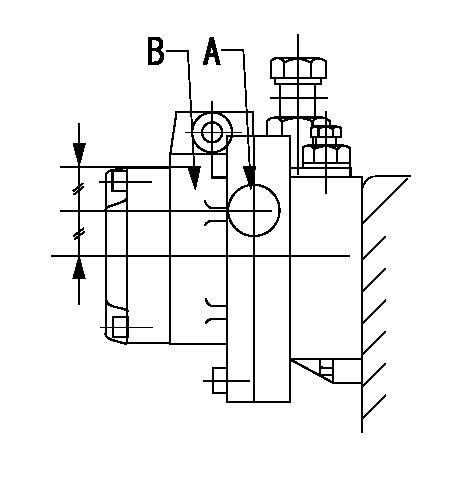
A:Sealing position
B:Pre-stroke actuator
1. When installing the pre-stroke actuator on the pump, first tighten the installation bolts loosely, then move the actuator fully counterclockwise (viewed from the drive side).
Temporary tightening torque: 1 - 1.5 N.m (0.1 - 0.15 kgf.m)
2. Move the actuator in the clockwise direction when viewed from the drive side, and adjust so that it becomes the adjustment point of the adjustment value. Then tighten it.
Tightening torque: 7^9 N.m (0.7^0.9 kgf.m)
3. After prestroke actuator installation adjustment, simultaneously stamp both the actuator side and housing side.
----------
----------
----------
----------
0000001701
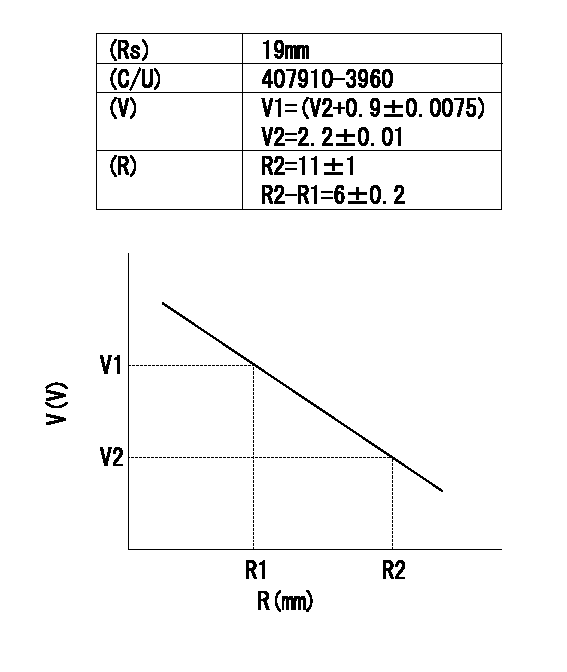
(Rs) rack sensor specifications
(C/U) control unit part number
(V) Rack sensor output voltage
(R) Rack position (mm)
1. Confirming governor output characteristics (rack 19 mm, span 6 mm)
(1)When the output voltages of the rack sensor are V1 and V2, check that the rack positions R1 and R2 in the table above are satisfied.
----------
----------
----------
----------
Information:
Illustration 7 g06347860
Injector male spade terminals
There are two options to build injector adapter harness for C3.3.If available, use the injector connector removed from C3.3 harness. Cut both 100 mm wires from the connector and attach bullet terminals that fit in the injector adapter harness C3.8 terminal from injector test kit.If no harness is available, build a harness with the following. Two female spade terminals for injector male spade terminal, two 16 gauge 100 mm wires, and two bullet terminals for injector adapter harness C3.8 terminal.
Illustration 8 g06345429
Injector adapter harness C2.4
Illustration 9 g06346223
Injector adapter harness C3.8
Illustration 10 g06346237
Injector male spade terminals
There are two options to build injector adapter harness for C2.4.If available, use the injector connector removed from C2.4 harness. Cut both 100 mm wires from the connector and attach bullet terminals that fit in the injector adapter harness C3.8 terminal from injector test kit.If no harness is available, build a harness with the following. Two female spade terminals for injector male spade terminal, two 16 gauge 100 mm wires, and two bullet terminals for injector adapter harness C3.8 terminal.Injector Test Set-up
Illustration 11 g06346391
Mounted nozzle test group
Find a suitable stable and surface to either mount or place the nozzle test group. Fill fuel container with #1 diesel and install high-pressure hose assembly. Use adaptors, if needed, based on nozzle tester. Tighten the fuel line adapter to (25 ft lbs). Install the fuel line adapter and tighten to (25 ft lbs) to allow connection to the injector.
Illustration 12 g06346423
Injector holder assembly
Take the injector test kit and remove all parts to assemble, as shown above. Take the injector holder and the clear fuel shield with screws from the kit and remove the screws using a 3mm alan wrench. Assemble the parts so the clear fuel shield with screws is on the bottom. While, the mounted injector holder is on top with the screws removed from before.
Illustration 13 g06346719
Fuel collector and injector holder
Place injector holder onto a fuel collector or another container to capture the injection spray.
Illustration 14 g06346839
Injector setup and harness connection
Install the injector that is needing to be tested into the opening at the top of injector holder. Attach the return fuel drain hose and run the drain hose to another fuel collector. Make the harness connection using the correct adapter for the C2.4, C3.3, and C3.8 engines. Connect the injector pulse tool and the injector adapter harness to the injector.
Illustration 15 g06346868
Complete setup of nozzle tester and injector test kit
Once injector test kit and nozzle test group are set up, connect fuel line adaptor on the high-pressure hose assembly to the injector, leave connection loose. Actuate the lever on the nozzle test group until fuel drips from connection allowing air to purge from setup. Tighten fuel line adaptor at injector to (25 ft lbs).Injector Test Procedure
Illustration 16 g06346881
Mounted nozzle test group (close-up)
Inspect the injector for any leaks. Using the lever on the nozzle tester group, build injection fuel pressure to (5000 psi). Turn the locking valve to insure there is no leakage back through the tester.
Let the nozzle test