Information injection-pump assembly
BOSCH
9 400 611 855
9400611855
ZEXEL
108621-0050
1086210050
NISSAN-DIESEL
1680196701
1680196701

Rating:
Service parts 108621-0050 INJECTION-PUMP ASSEMBLY:
1.
_
7.
COUPLING PLATE
9.
_
11.
Nozzle and Holder
16600-96660
12.
Open Pre:MPa(Kqf/cm2)
22.6{230}
15.
NOZZLE SET
Include in #1:
108621-0050
as INJECTION-PUMP ASSEMBLY
Cross reference number
BOSCH
9 400 611 855
9400611855
ZEXEL
108621-0050
1086210050
NISSAN-DIESEL
1680196701
1680196701
Zexel num
Bosch num
Firm num
Name
Calibration Data:
Adjustment conditions
Test oil
1404 Test oil ISO4113 or {SAEJ967d}
1404 Test oil ISO4113 or {SAEJ967d}
Test oil temperature
degC
40
40
45
Nozzle and nozzle holder
105780-8250
Bosch type code
1 688 901 101
Nozzle
105780-0120
Bosch type code
1 688 901 990
Nozzle holder
105780-2190
Opening pressure
MPa
20.7
Opening pressure
kgf/cm2
211
Injection pipe
Outer diameter - inner diameter - length (mm) mm 8-3-600
Outer diameter - inner diameter - length (mm) mm 8-3-600
Overflow valve
134424-4120
Overflow valve opening pressure
kPa
255
221
289
Overflow valve opening pressure
kgf/cm2
2.6
2.25
2.95
Tester oil delivery pressure
kPa
255
255
255
Tester oil delivery pressure
kgf/cm2
2.6
2.6
2.6
RED3 control unit part number
407910-3
960
RED3 rack sensor specifications
mm
19
PS/ACT control unit part no.
407980-2
24*
Digi switch no.
31
Direction of rotation (viewed from drive side)
Right R
Right R
Injection timing adjustment
Direction of rotation (viewed from drive side)
Right R
Right R
Injection order
1-4-2-6-
3-5
Pre-stroke
mm
6.4
6.37
6.43
Beginning of injection position
Drive side NO.1
Drive side NO.1
Difference between angles 1
Cal 1-4 deg. 60 59.75 60.25
Cal 1-4 deg. 60 59.75 60.25
Difference between angles 2
Cyl.1-2 deg. 120 119.75 120.25
Cyl.1-2 deg. 120 119.75 120.25
Difference between angles 3
Cal 1-6 deg. 180 179.75 180.25
Cal 1-6 deg. 180 179.75 180.25
Difference between angles 4
Cal 1-3 deg. 240 239.75 240.25
Cal 1-3 deg. 240 239.75 240.25
Difference between angles 5
Cal 1-5 deg. 300 299.75 300.25
Cal 1-5 deg. 300 299.75 300.25
Injection quantity adjustment
Rack position
(16.2)
Vist
V
1.42
1.42
1.42
Pump speed
r/min
600
600
600
Average injection quantity
mm3/st.
189
187
191
Max. variation between cylinders
%
0
-4
4
Basic
*
PS407980-224*
V
2.45+-0.
01
PS407980-224*
mm
4+-0.05
Injection quantity adjustment_02
Rack position
(7.9)
Vist
V
2.7
2.6
2.8
Pump speed
r/min
280
280
280
Average injection quantity
mm3/st.
18.5
17.5
19.5
Max. variation between cylinders
%
0
-10
10
PS407980-224*
V
V1+0.05+
-0.01
PS407980-224*
mm
6.3+-0.0
3
Remarks
Refer to items regarding the pre-stroke actuator
Refer to items regarding the pre-stroke actuator
Governor adjustment
Pump speed
r/min
1150++
Advance angle
deg.
0
0
0
Remarks
Do not advance until starting N = 1155.
Do not advance until starting N = 1155.
Governor adjustment_02
Pump speed
r/min
1155
Advance angle
deg.
0.3
Governor adjustment_03
Pump speed
r/min
-
Advance angle
deg.
0.5
0.5
0.5
Remarks
Measure the actual speed, stop
Measure the actual speed, stop
0000001201
Pre-stroke
mm
6.4
6.37
6.43
Remarks
When the timing sleeve is pushed up
When the timing sleeve is pushed up
_02
Connector angle
deg.
8.5
8
9
Remarks
When the eccentric pin is tightened
When the eccentric pin is tightened
_03
Supply voltage
V
24
23.5
24.5
Ambient temperature
degC
23
18
28
Pre-stroke
mm
4
3.95
4.05
Output voltage
V
2.45
2.44
2.46
Adjustment
*
_04
Supply voltage
V
24
23.5
24.5
Ambient temperature
degC
23
18
28
Pre-stroke
mm
6.4
6.37
6.43
Output voltage
V
1.2
1
1.4
Confirmation
*
Remarks
Output voltage V1
Output voltage V1
_05
Supply voltage
V
24
23.5
24.5
Ambient temperature
degC
23
18
28
Pre-stroke
mm
3.4
Output voltage
V
3
2.98
3
Confirmation
*
_06
Supply voltage
V
24
23.5
24.5
Ambient temperature
degC
23
18
28
Output voltage
V
3.05
3.05
Confirmation of operating range
*
Test data Ex:
Speed control lever angle
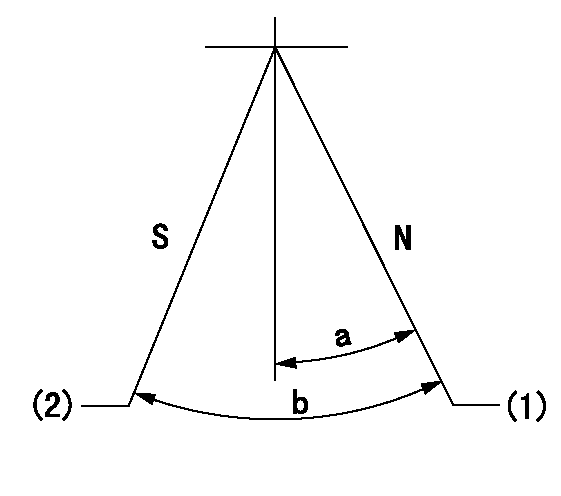
N:Pump normal
S:Stop the pump.
(1)Rack position = aa
(2)Rack position bb
----------
aa=20mm bb=1mm
----------
a=20deg+-5deg b=37deg+-5deg
----------
aa=20mm bb=1mm
----------
a=20deg+-5deg b=37deg+-5deg
0000000901

(1)Pump vertical direction
(2)Coupling's key groove position at No 1 cylinder's beginning of injection
(3)Pre-stroke: aa
(4)-
----------
aa=6.4+-0.03mm
----------
a=(30deg)
----------
aa=6.4+-0.03mm
----------
a=(30deg)
0000001501
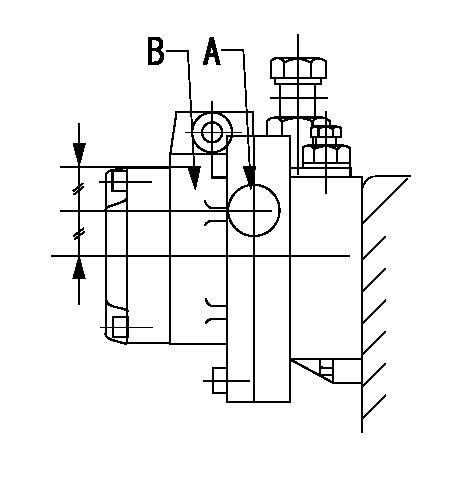
A:Sealing position
B:Pre-stroke actuator
1. When installing the pre-stroke actuator on the pump, first tighten the installation bolts loosely, then move the actuator fully counterclockwise (viewed from the drive side).
Temporary tightening torque: 1 - 1.5 N.m (0.1 - 0.15 kgf.m)
2. Move the actuator in the clockwise direction when viewed from the drive side, and adjust so that it becomes the adjustment point of the adjustment value. Then tighten it.
Tightening torque: 7^9 N.m (0.7^0.9 kgf.m)
3. After prestroke actuator installation adjustment, simultaneously stamp both the actuator side and housing side.
----------
----------
----------
----------
0000001701
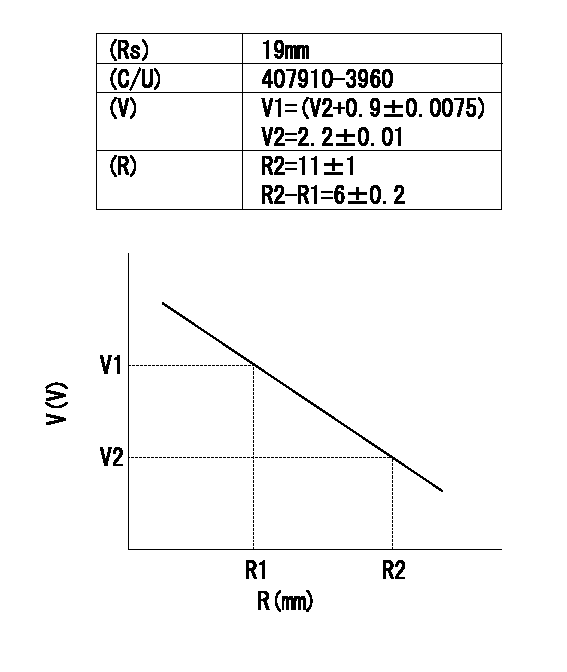
(Rs) rack sensor specifications
(C/U) control unit part number
(V) Rack sensor output voltage
(R) Rack position (mm)
1. Confirming governor output characteristics (rack 19 mm, span 6 mm)
(1)When the output voltages of the rack sensor are V1 and V2, check that the rack positions R1 and R2 in the table above are satisfied.
----------
----------
----------
----------
Information:
Introduction
The problem that is identified below does not have a known permanent solution. Until a permanent solution is found, use the solution that is identified below.Problem
Fuel injectors in certain C175 Machine Engines have been experiencing -7 and -12 fault codes which have resulted in replacement of the injectors.Solution
As Caterpillar® tries to determine the root cause for the fuel injector failures, documentation is needed. Fill out the form below and send it to the following email address:unes_john_w
Table 1
Background Information Information / Action Requested Responses / Comments
1 Truck Serial Number
2 Engine Serial Number
3 Truck Hours at Time of Failure
4 Engine Hours at Time of Failure
5 Date of Failure
6 Mine Site
7 Servicing Dealer and Dealer Code (For generating SIB Request)
8 Service/Workorder (For generating SIB Request)
9 Affected Cylinder / Cylinders of Engine
Fuel System Information
10 Injector Part Number Removed
11 Injector Serial Number Removed
12 Hours on Failed Injector
13 Replacement Injector Part Number Installed
14 Replacement Injector Serial Number Installed
15 CFM Install - Yes or No?
If Yes, provide SMH at Time of Installation
16 Low-Pressure Fuel System Configuration? (New Trans Pump per M0064904?)
If Yes, at PCR or Provide SMH at Time of Installation
17 Fuel Filter make / part number
18 Previous Maintenance on Fuel System Past Tertiary Filter
19 History of HPFP Replacement (most recent replacement hrs, symptoms)
20 SIB Issued for Injectors on Failed Cylinders
Software
21 Engine Software at Time of Failure
22 Software History on Engine - If Available
23 SC2 Installed? If No, is VIMS Data Available?
24 PSR at Time of Failure
25 ECM Replacement File at Time of Failure
Wiring
26 Any Wiring Issues on the Engine Harness?
27 Any By-Pass Wiring Installed on Engine Harness?
Service History
28 Any History of Head Bolt Failures on the Engine or Affected Cylinder?
29 Pressure Check / Evaluate Health of Injector Sleeve on Affected Cylinder
30 Any History of Fluid in the Engine (Turbocharger Failure, Coolant Leaks, ATAAC Issues)
Other
31 Submit DSN to Document Failure
The problem that is identified below does not have a known permanent solution. Until a permanent solution is found, use the solution that is identified below.Problem
Fuel injectors in certain C175 Machine Engines have been experiencing -7 and -12 fault codes which have resulted in replacement of the injectors.Solution
As Caterpillar® tries to determine the root cause for the fuel injector failures, documentation is needed. Fill out the form below and send it to the following email address:unes_john_w
Table 1
Background Information Information / Action Requested Responses / Comments
1 Truck Serial Number
2 Engine Serial Number
3 Truck Hours at Time of Failure
4 Engine Hours at Time of Failure
5 Date of Failure
6 Mine Site
7 Servicing Dealer and Dealer Code (For generating SIB Request)
8 Service/Workorder (For generating SIB Request)
9 Affected Cylinder / Cylinders of Engine
Fuel System Information
10 Injector Part Number Removed
11 Injector Serial Number Removed
12 Hours on Failed Injector
13 Replacement Injector Part Number Installed
14 Replacement Injector Serial Number Installed
15 CFM Install - Yes or No?
If Yes, provide SMH at Time of Installation
16 Low-Pressure Fuel System Configuration? (New Trans Pump per M0064904?)
If Yes, at PCR or Provide SMH at Time of Installation
17 Fuel Filter make / part number
18 Previous Maintenance on Fuel System Past Tertiary Filter
19 History of HPFP Replacement (most recent replacement hrs, symptoms)
20 SIB Issued for Injectors on Failed Cylinders
Software
21 Engine Software at Time of Failure
22 Software History on Engine - If Available
23 SC2 Installed? If No, is VIMS Data Available?
24 PSR at Time of Failure
25 ECM Replacement File at Time of Failure
Wiring
26 Any Wiring Issues on the Engine Harness?
27 Any By-Pass Wiring Installed on Engine Harness?
Service History
28 Any History of Head Bolt Failures on the Engine or Affected Cylinder?
29 Pressure Check / Evaluate Health of Injector Sleeve on Affected Cylinder
30 Any History of Fluid in the Engine (Turbocharger Failure, Coolant Leaks, ATAAC Issues)
Other
31 Submit DSN to Document Failure