Information injection-pump assembly
BOSCH
9 400 612 056
9400612056
ZEXEL
107692-5290
1076925290
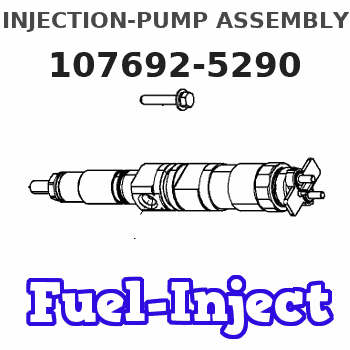
Rating:
Service parts 107692-5290 INJECTION-PUMP ASSEMBLY:
1.
_
5.
AUTOM. ADVANCE MECHANIS
9.
_
11.
Nozzle and Holder
16600-Z5673
12.
Open Pre:MPa(Kqf/cm2)
19.6{200}
15.
NOZZLE SET
Include in #1:
107692-5290
as INJECTION-PUMP ASSEMBLY
Cross reference number
BOSCH
9 400 612 056
9400612056
ZEXEL
107692-5290
1076925290
Zexel num
Bosch num
Firm num
Name
Calibration Data:
Adjustment conditions
Test oil
1404 Test oil ISO4113 or {SAEJ967d}
1404 Test oil ISO4113 or {SAEJ967d}
Test oil temperature
degC
40
40
45
Nozzle and nozzle holder
105780-8250
Bosch type code
1 688 901 101
Nozzle
105780-0120
Bosch type code
1 688 901 990
Nozzle holder
105780-2190
Opening pressure
MPa
20.7
Opening pressure
kgf/cm2
211
Injection pipe
Outer diameter - inner diameter - length (mm) mm 8-3-600
Outer diameter - inner diameter - length (mm) mm 8-3-600
Overflow valve
131425-0520
Overflow valve opening pressure
kPa
255
221
289
Overflow valve opening pressure
kgf/cm2
2.6
2.25
2.95
Tester oil delivery pressure
kPa
255
255
255
Tester oil delivery pressure
kgf/cm2
2.6
2.6
2.6
PS/ACT control unit part no.
407910-3
03*
Selector switch no.
01
PS/ACT control unit part no.
407980-2
24*
Digi switch no.
15
Direction of rotation (viewed from drive side)
Right R
Right R
Injection timing adjustment
Direction of rotation (viewed from drive side)
Right R
Right R
Injection order
1-4-2-6-
3-5
Pre-stroke
mm
5.1
5.07
5.13
Beginning of injection position
Drive side NO.1
Drive side NO.1
Difference between angles 1
Cal 1-4 deg. 60 59.75 60.25
Cal 1-4 deg. 60 59.75 60.25
Difference between angles 2
Cyl.1-2 deg. 120 119.75 120.25
Cyl.1-2 deg. 120 119.75 120.25
Difference between angles 3
Cal 1-6 deg. 180 179.75 180.25
Cal 1-6 deg. 180 179.75 180.25
Difference between angles 4
Cal 1-3 deg. 240 239.75 240.25
Cal 1-3 deg. 240 239.75 240.25
Difference between angles 5
Cal 1-5 deg. 300 299.75 300.25
Cal 1-5 deg. 300 299.75 300.25
Injection quantity adjustment
Adjusting point
-
Rack position
14.5
Pump speed
r/min
1300
1300
1300
Average injection quantity
mm3/st.
110.5
108.5
112.5
Max. variation between cylinders
%
0
-4
4
Basic
*
Fixing the rack
*
PS407980-224*
V
2.25+-0.
01
PS407980-224*
mm
3.1+-0.0
5
PS407910-303*
V
2.25+-0.
01
PS407910-303*
mm
3.1+-0.0
5
Standard for adjustment of the maximum variation between cylinders
*
Injection quantity adjustment_02
Adjusting point
Z
Rack position
8.6+-0.5
Pump speed
r/min
530
530
530
Average injection quantity
mm3/st.
30
28.2
31.8
Max. variation between cylinders
%
0
-10
10
Fixing the rack
*
PS407980-224*
V
V1+0.05+
-0.01
PS407980-224*
mm
5+-0.03
PS407910-303*
V
V1+0.05+
-0.01
PS407910-303*
mm
5+-0.03
Standard for adjustment of the maximum variation between cylinders
*
Remarks
Refer to items regarding the pre-stroke actuator
Refer to items regarding the pre-stroke actuator
Injection quantity adjustment_03
Adjusting point
A
Rack position
R1(14.5)
Pump speed
r/min
1300
1300
1300
Average injection quantity
mm3/st.
110.5
109.5
111.5
Basic
*
Fixing the lever
*
Boost pressure
kPa
24
24
Boost pressure
mmHg
180
180
PS407980-224*
V
2.25+-0.
01
PS407980-224*
mm
3.1+-0.0
5
PS407910-303*
V
2.25+-0.
01
PS407910-303*
mm
3.1+-0.0
5
Injection quantity adjustment_04
Adjusting point
B
Rack position
R1-2.25
Pump speed
r/min
800
800
800
Average injection quantity
mm3/st.
96.5
92.5
100.5
Fixing the lever
*
Boost pressure
kPa
24
24
Boost pressure
mmHg
180
180
PS407980-224*
V
2.25+-0.
01
PS407980-224*
mm
3.1+-0.0
5
PS407910-303*
V
2.25+-0.
01
PS407910-303*
mm
3.1+-0.0
5
Injection quantity adjustment_05
Adjusting point
C
Rack position
(R2-0.35
)+-0.2
Pump speed
r/min
350
350
350
Average injection quantity
mm3/st.
45
43
47
Fixing the lever
*
Boost pressure
kPa
0
0
0
Boost pressure
mmHg
0
0
0
PS407980-224*
V
2.25+-0.
01
PS407980-224*
mm
3.1+-0.0
5
PS407910-303*
V
2.25+-0.
01
PS407910-303*
mm
3.1+-0.0
5
Boost compensator adjustment
Pump speed
r/min
350
350
350
Rack position
(R2-0.35
)
Boost pressure
kPa
6.7
5.4
8
Boost pressure
mmHg
50
40
60
Boost compensator adjustment_02
Pump speed
r/min
350
350
350
Rack position
R2(R1-4.
35)
Boost pressure
kPa
10.7
10.7
10.7
Boost pressure
mmHg
80
80
80
0000001601
CU407980-224*
*
Actuator retarding type
*
Supply voltage
V
12
11.5
12.5
Ambient temperature
degC
23
18
28
Pre-stroke
mm
2
1.95
2.05
Output voltage
V
2.83
2.82
2.84
Adjustment
*
_02
CU407980-224*
*
Supply voltage
V
12
11.5
12.5
Ambient temperature
degC
23
18
28
Pre-stroke
mm
5.1
5.07
5.13
Output voltage
V
1.2
1
1.4
Confirmation
*
Remarks
Output voltage V1
Output voltage V1
_03
CU407980-224*
*
Supply voltage
V
12
11.5
12.5
Ambient temperature
degC
23
18
28
Output voltage
V
3.05
3.05
Confirmation of operating range
*
_04
CU407910-303*
*
Actuator retarding type
*
Supply voltage
V
12
11.5
12.5
Ambient temperature
degC
23
18
28
Pre-stroke
mm
2
1.95
2.05
Output voltage
V
2.83
2.82
2.84
Adjustment
*
_05
CU407910-303*
*
Supply voltage
V
12
11.5
12.5
Ambient temperature
degC
23
18
28
Pre-stroke
mm
5.1
5.07
5.13
Output voltage
V
1.2
1
1.4
Confirmation
*
Remarks
Output voltage V1
Output voltage V1
_06
CU407910-303*
*
Supply voltage
V
12
11.5
12.5
Ambient temperature
degC
23
18
28
Output voltage
V
3.05
3.05
Confirmation of operating range
*
Test data Ex:
Governor adjustment
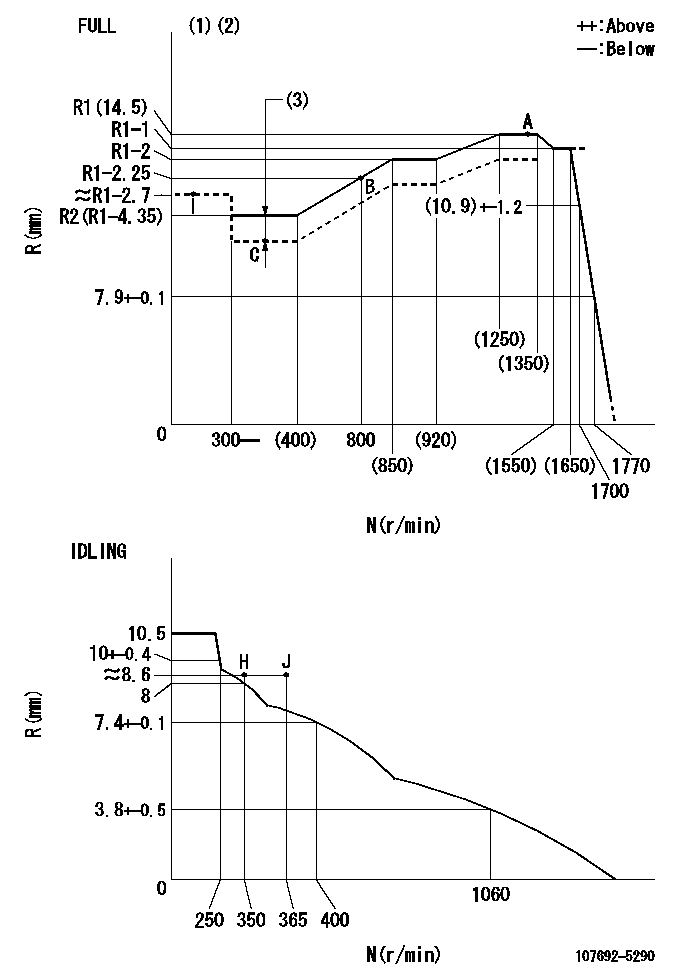
N:Pump speed
R:Rack position (mm)
(1)Torque cam stamping: T1
(2)Tolerance for racks not indicated: +-0.05mm.
(3)Boost compensator stroke: BCL
----------
T1=AG30 BCL=(0.35)mm
----------
----------
T1=AG30 BCL=(0.35)mm
----------
Speed control lever angle

F:Full speed
I:Idle
(1)Use the hole at R = aa
(2)Stopper bolt set position 'H'
----------
aa=93.5mm
----------
a=15deg+-5deg b=(35deg)+-3deg
----------
aa=93.5mm
----------
a=15deg+-5deg b=(35deg)+-3deg
Stop lever angle
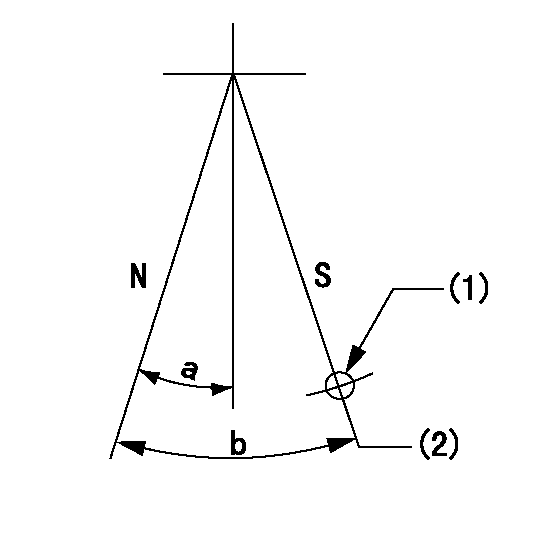
N:Pump normal
S:Stop the pump.
(1)Use the pin at R = aa
(2)Set the stopper bolt at rack position = bb (speed = cc).
----------
aa=37mm bb=1.5+-0.3mm cc=0r/min
----------
a=20deg+-5deg b=45deg+-5deg
----------
aa=37mm bb=1.5+-0.3mm cc=0r/min
----------
a=20deg+-5deg b=45deg+-5deg
0000001301

(1)Pump vertical direction
(2)Coupling's key groove position at No 1 cylinder's beginning of injection
(3)Pre-stroke: aa
(4)-
----------
aa=5.1+-0.03mm
----------
a=(20deg)
----------
aa=5.1+-0.03mm
----------
a=(20deg)
0000001401
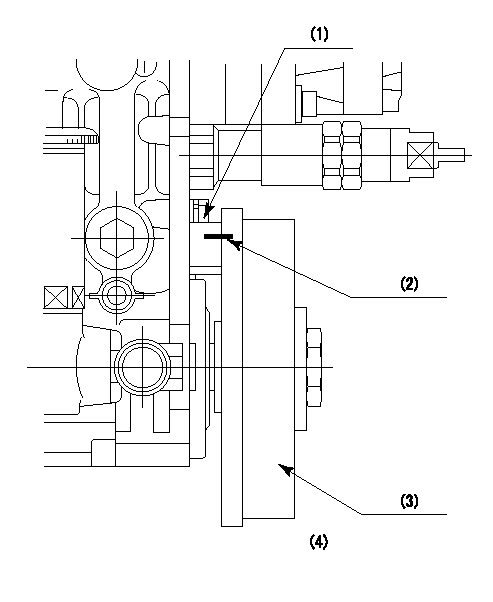
(1)Pointer
(2)Injection timing aligning mark
(3)Fly weight
(4)The actual shape and direction may be different from this illustration.
Operation sequence
1. Turn the prestroke actuator OFF.
2. Turn the camshaft as far as the No.1 cylinder's beginning of injection position.
3. Check that the pointer alignment mark of the injection pump and the alignment mark of the flywheel are matching.
4. If they are not matching, erase the alignment mark on the flywheel side, and stamp an alignment mark on the flywheel position that matches with the pointer side alignment mark.
5. Check again that the coupling's key groove position is in the No.1 cylinder's beginning of injection position.
----------
----------
----------
----------
0000001701
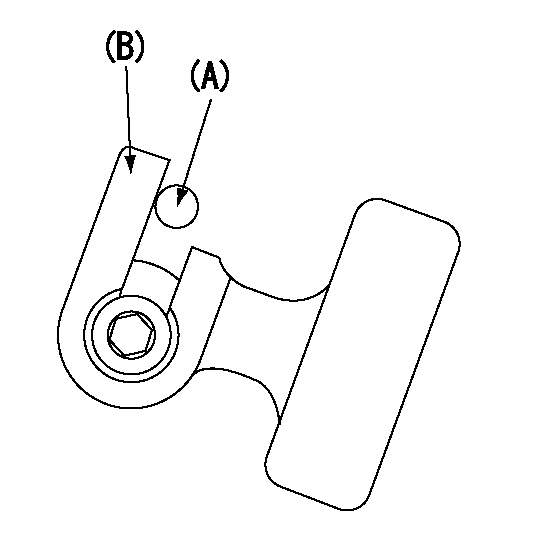
A : Stopper pin
B: Connector
----------
----------
----------
----------
0000001801
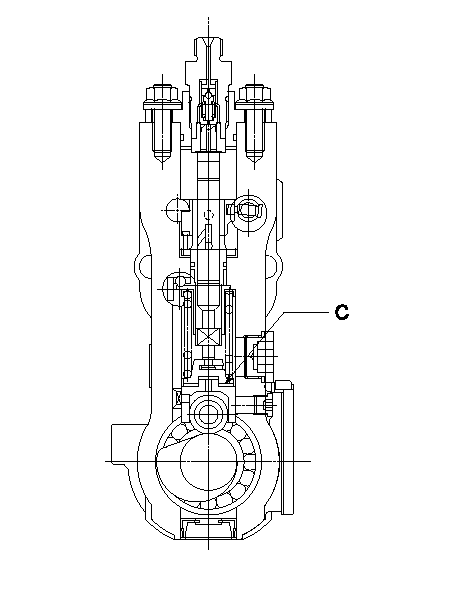
C:Shim
----------
----------
----------
----------
0000001901
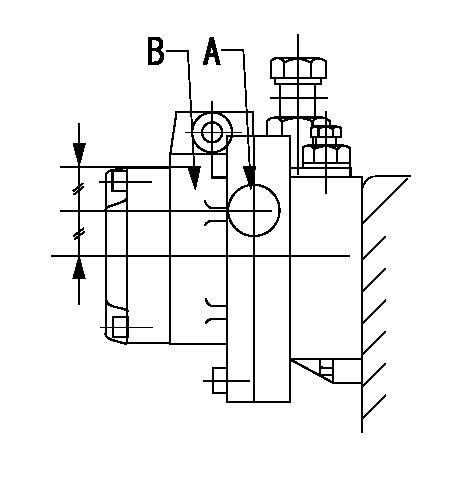
A:Sealing position
B:Pre-stroke actuator
1. When installing the pre-stroke actuator on the pump, first tighten the installation bolts loosely, then move the actuator fully counterclockwise (viewed from the drive side).
Temporary tightening torque: 1 - 1.5 N.m (0.1 - 0.15 kgf.m)
2. Move the actuator in the clockwise direction when viewed from the drive side, and adjust so that it becomes the adjustment point of the adjustment value. Then tighten it.
Tightening torque: 7^9 N.m (0.7^0.9 kgf.m)
3. After prestroke actuator installation adjustment, simultaneously stamp both the actuator side and housing side.
----------
----------
----------
----------
0000002201 RACK SENSOR
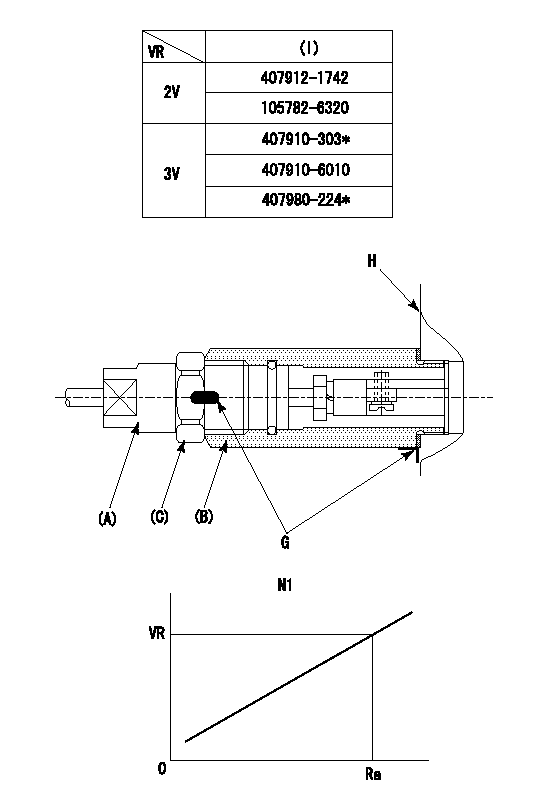
(VR) measurement voltage
(I) Part number of the control unit
(G) Apply red paint.
(H): End surface of the pump
1. Rack sensor adjustment (-0620)
(1)Fix the speed control lever at the full position
(2)Set the speed to N1 r/min.
(If the boost compensator is provided, apply boost pressure.)
(3)Adjust the bobbin (A) so that the rack sensor's output voltage is VR+-0.01.
(4)At that time, rack position must be Ra.
(5)Apply G at two places.
Connecting part between the joint (B) and the nut (F)
Connecting part between the joint (B) and the end surface of the pump (H)
----------
N1=1300r/min Ra=R1(14.5)mm
----------
----------
N1=1300r/min Ra=R1(14.5)mm
----------
0000002301 ACS

(A) Set screw
(B) Push rod 1
(C) Push rod 2
(D) Lever
1. Aneroid compensator unit adjustment
(1)Screw in (A) to obtain L1.
(2)Select C so that dimension L2 can be obtained.
2. Adjustment when mounting the governor.
(1)Set the speed of the pump to N1 r/min and fix the control lever at the full set position.
(2)Set to full boost.
(3)Screw in the aneroid compensator body to obtain the performance shown in the graph above.
(4)As there is hysterisis, measure when the absolute pressure drops.
(5)Hysterisis must not exceed rack position = h1.
----------
N1=1300r/min L1=1.5+-0.5mm L2=37.5+-0.5mm h1=0.15mm
----------
Ra=R1(14.5)mm Rb=- Rc=(R1-0.65)mm P1=(86)+-2.7kPa((645)+-20mmHg) P2=- P3=57.7+-0.7kPa(433+-5mmHg) Q1=110.5+-1cm3/1000st Q2=- Q3=100.5+-2cm3/1000st
----------
N1=1300r/min L1=1.5+-0.5mm L2=37.5+-0.5mm h1=0.15mm
----------
Ra=R1(14.5)mm Rb=- Rc=(R1-0.65)mm P1=(86)+-2.7kPa((645)+-20mmHg) P2=- P3=57.7+-0.7kPa(433+-5mmHg) Q1=110.5+-1cm3/1000st Q2=- Q3=100.5+-2cm3/1000st
Information:
2. Loosen the fuel injection line nut at the fuel pump, one at a time, with the engine running. Use a cloth or similar material to prevent fuel from spraying on hot exhaust component. Be sure to tighten each fuel line nut after the test, before the next fuel line nut is loosened. 3. When a cylinder is found where the loosened fuel line nut does not make a difference in engine performance or smoking, have that cylinder injection nozzle tested. Purge the fuel lines of air. 4. Check for any fuel leaks. Stop the engine by following the procedure in the Engine Stopping topic in this manual and correct any fuel leaks that may occur. To Remove and Install Injection Nozzles
Special tooling is required. Refer to the Service Manual for your engine to remove and install injection nozzles or contact your Caterpillar dealer for assistance.Starting Motor and Alternator
Inspect for Proper Operation
Electric Starting Motor
AlternatorFor good life of the air starting motor, the air supply should be free of dirt and water. A lubricator should be used with the starting system. Use 10 weight non-detergent engine oil above 0°C (32°F) or diesel fuel at temperatures below 0°C (32°F). See the Lubricant Specifications for the proper oil to use.One unscheduled failure caused by any of these components will cost more in downtime than maintaining them before failure. The cost incurred to maintain these components before failure as recommended could be significantly less than if the component fails. By maintaining these components before failure, unscheduled downtime and potential damage to other engine parts are reduced. The prevention of unscheduled downtime saves money and lowers operating costs.Caterpillar recommends that the most cost effective method of operation and maintenance for these components is to inspect the unit before it fails and make the decision to rebuild or exchange the components.Before deciding which repair method is best, make sure all of the options and costs associated with repair have been considered. Some considerations are:* The costs associated with using separate parts from inventory versus the cost of a repair kit.* Downtime costs while the product is being rebuilt or repaired.* Total parts and labor costs for repairs versus the actual Remanufactured cost.* Remanufactured components from Caterpillar (if available) are covered by a standard, factory warranty.Caterpillar Recommendation
To minimize downtime, Caterpillar recommends that the use of Remanufactured components (subject to availability) is the most cost effective option.Removal and Installation
Refer to the established procedure in the Service Manual for this engine to Remove and Install these components or contact your Caterpillar dealer for assistance.Turbochargers
Rebuild or Exchange
The cost incurred to maintain your turbochargers before failure as recommended could be significantly less than if you wait until your turbocharger fails. By maintaining your turbochargers before failure, you will minimize unscheduled downtime and reduce the chances for potential damage to other engine parts. If you choose to operate your engine until the turbochargers fail, your repair costs could be as much as twenty-five times or more compared
Special tooling is required. Refer to the Service Manual for your engine to remove and install injection nozzles or contact your Caterpillar dealer for assistance.Starting Motor and Alternator
Inspect for Proper Operation
Electric Starting Motor
AlternatorFor good life of the air starting motor, the air supply should be free of dirt and water. A lubricator should be used with the starting system. Use 10 weight non-detergent engine oil above 0°C (32°F) or diesel fuel at temperatures below 0°C (32°F). See the Lubricant Specifications for the proper oil to use.One unscheduled failure caused by any of these components will cost more in downtime than maintaining them before failure. The cost incurred to maintain these components before failure as recommended could be significantly less than if the component fails. By maintaining these components before failure, unscheduled downtime and potential damage to other engine parts are reduced. The prevention of unscheduled downtime saves money and lowers operating costs.Caterpillar recommends that the most cost effective method of operation and maintenance for these components is to inspect the unit before it fails and make the decision to rebuild or exchange the components.Before deciding which repair method is best, make sure all of the options and costs associated with repair have been considered. Some considerations are:* The costs associated with using separate parts from inventory versus the cost of a repair kit.* Downtime costs while the product is being rebuilt or repaired.* Total parts and labor costs for repairs versus the actual Remanufactured cost.* Remanufactured components from Caterpillar (if available) are covered by a standard, factory warranty.Caterpillar Recommendation
To minimize downtime, Caterpillar recommends that the use of Remanufactured components (subject to availability) is the most cost effective option.Removal and Installation
Refer to the established procedure in the Service Manual for this engine to Remove and Install these components or contact your Caterpillar dealer for assistance.Turbochargers
Rebuild or Exchange
The cost incurred to maintain your turbochargers before failure as recommended could be significantly less than if you wait until your turbocharger fails. By maintaining your turbochargers before failure, you will minimize unscheduled downtime and reduce the chances for potential damage to other engine parts. If you choose to operate your engine until the turbochargers fail, your repair costs could be as much as twenty-five times or more compared