Information injection-pump assembly
ZEXEL
107692-5090
1076925090
NISSAN-DIESEL
16714Z5578
16714z5578
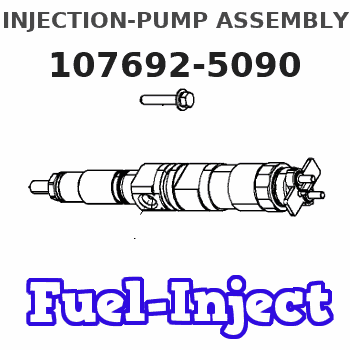
Rating:
Cross reference number
ZEXEL
107692-5090
1076925090
NISSAN-DIESEL
16714Z5578
16714z5578
Zexel num
Bosch num
Firm num
Name
Calibration Data:
Adjustment conditions
Test oil
1404 Test oil ISO4113 or {SAEJ967d}
1404 Test oil ISO4113 or {SAEJ967d}
Test oil temperature
degC
40
40
45
Nozzle and nozzle holder
105780-8250
Bosch type code
1 688 901 101
Nozzle
105780-0120
Bosch type code
1 688 901 990
Nozzle holder
105780-2190
Opening pressure
MPa
20.7
Opening pressure
kgf/cm2
211
Injection pipe
Outer diameter - inner diameter - length (mm) mm 8-3-600
Outer diameter - inner diameter - length (mm) mm 8-3-600
Overflow valve
131425-0520
Overflow valve opening pressure
kPa
255
221
289
Overflow valve opening pressure
kgf/cm2
2.6
2.25
2.95
Tester oil delivery pressure
kPa
255
255
255
Tester oil delivery pressure
kgf/cm2
2.6
2.6
2.6
PS/ACT control unit part no.
407980-2
24*
Digi switch no.
14
Direction of rotation (viewed from drive side)
Right R
Right R
Injection timing adjustment
Direction of rotation (viewed from drive side)
Right R
Right R
Injection order
1-4-2-6-
3-5
Pre-stroke
mm
5.6
5.57
5.63
Beginning of injection position
Drive side NO.1
Drive side NO.1
Difference between angles 1
Cal 1-4 deg. 60 59.75 60.25
Cal 1-4 deg. 60 59.75 60.25
Difference between angles 2
Cyl.1-2 deg. 120 119.75 120.25
Cyl.1-2 deg. 120 119.75 120.25
Difference between angles 3
Cal 1-6 deg. 180 179.75 180.25
Cal 1-6 deg. 180 179.75 180.25
Difference between angles 4
Cal 1-3 deg. 240 239.75 240.25
Cal 1-3 deg. 240 239.75 240.25
Difference between angles 5
Cal 1-5 deg. 300 299.75 300.25
Cal 1-5 deg. 300 299.75 300.25
Injection quantity adjustment
Adjusting point
-
Rack position
13.8
Pump speed
r/min
1400
1400
1400
Average injection quantity
mm3/st.
112
110
114
Max. variation between cylinders
%
0
-4
4
Basic
*
Fixing the rack
*
PS407980-224*
V
2.25+-0.
01
PS407980-224*
mm
3.6+-0.0
5
Standard for adjustment of the maximum variation between cylinders
*
Injection quantity adjustment_02
Adjusting point
Z
Rack position
8+-0.5
Pump speed
r/min
465
465
465
Average injection quantity
mm3/st.
10.6
8.8
12.4
Max. variation between cylinders
%
0
-10
10
Fixing the rack
*
PS407980-224*
V
V1+0.05+
-0.01
PS407980-224*
mm
5.5+-0.0
3
Standard for adjustment of the maximum variation between cylinders
*
Remarks
Refer to items regarding the pre-stroke actuator
Refer to items regarding the pre-stroke actuator
Injection quantity adjustment_03
Adjusting point
A
Rack position
R1(13.8)
Pump speed
r/min
1400
1400
1400
Average injection quantity
mm3/st.
112
111
113
Basic
*
Fixing the lever
*
Boost pressure
kPa
26.7
26.7
Boost pressure
mmHg
200
200
PS407980-224*
V
2.25+-0.
01
PS407980-224*
mm
3.6+-0.0
5
Injection quantity adjustment_04
Adjusting point
B
Rack position
R1-1.7
Pump speed
r/min
900
900
900
Average injection quantity
mm3/st.
105
101
109
Fixing the lever
*
Boost pressure
kPa
26.7
26.7
Boost pressure
mmHg
200
200
PS407980-224*
V
2.25+-0.
01
PS407980-224*
mm
3.6+-0.0
5
Injection quantity adjustment_05
Adjusting point
C
Rack position
R2-0.6
Pump speed
r/min
350
350
350
Average injection quantity
mm3/st.
25
21
29
Fixing the lever
*
Boost pressure
kPa
0
0
0
Boost pressure
mmHg
0
0
0
PS407980-224*
V
2.25+-0.
01
PS407980-224*
mm
3.6+-0.0
5
Boost compensator adjustment
Pump speed
r/min
350
350
350
Rack position
R2-0.6
Boost pressure
kPa
5.3
4
6.6
Boost pressure
mmHg
40
30
50
Boost compensator adjustment_02
Pump speed
r/min
350
350
350
Rack position
R2(R1-3.
35)
Boost pressure
kPa
13.3
13.3
13.3
Boost pressure
mmHg
100
100
100
0000001601
CU407980-224*
*
Actuator retarding type
*
Supply voltage
V
24
23.5
24.5
Ambient temperature
degC
23
18
28
Pre-stroke
mm
2.5
2.45
2.55
Output voltage
V
2.83
2.82
2.84
Adjustment
*
_02
CU407980-224*
*
Supply voltage
V
24
23.5
24.5
Ambient temperature
degC
23
18
28
Pre-stroke
mm
5.6
5.57
5.63
Output voltage
V
1.2
1
1.4
Confirmation
*
Remarks
Output voltage V1
Output voltage V1
_03
CU407980-224*
*
Supply voltage
V
24
23.5
24.5
Ambient temperature
degC
23
18
28
Output voltage
V
3.05
3.05
Confirmation of operating range
*
Test data Ex:
Governor adjustment
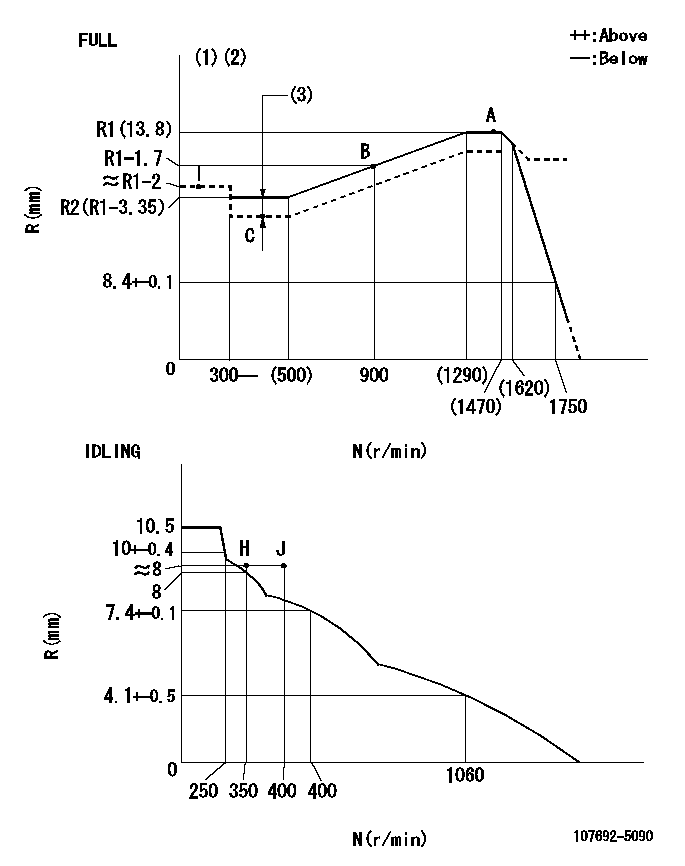
N:Pump speed
R:Rack position (mm)
(1)Torque cam stamping: T1
(2)Tolerance for racks not indicated: +-0.05mm.
(3)Boost compensator stroke: BCL
----------
T1=AB57 BCL=0.6+-0.1mm
----------
----------
T1=AB57 BCL=0.6+-0.1mm
----------
Speed control lever angle

F:Full speed
I:Idle
(1)Use the hole at R = aa
(2)Stopper bolt set position 'H'
----------
aa=93.5mm
----------
a=18.5deg+-5deg b=34.5deg+-3deg
----------
aa=93.5mm
----------
a=18.5deg+-5deg b=34.5deg+-3deg
Stop lever angle
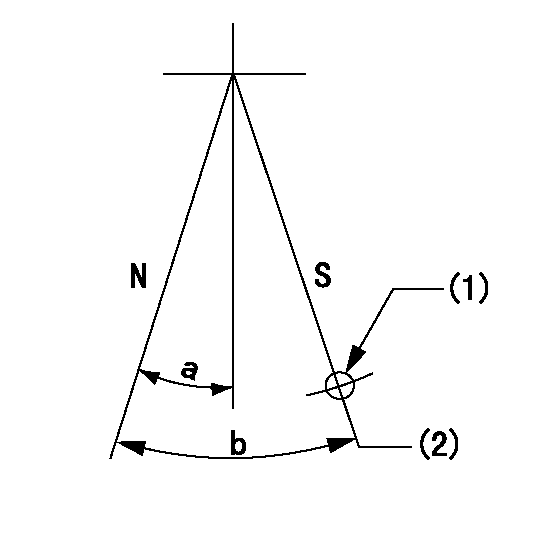
N:Pump normal
S:Stop the pump.
(1)Use the pin at R = aa
(2)Set the stopper bolt so that rack position = bb (speed = cc)
----------
aa=37mm bb=1.5+-0.3mm cc=0r/min
----------
a=20deg+-5deg b=45deg+-5deg
----------
aa=37mm bb=1.5+-0.3mm cc=0r/min
----------
a=20deg+-5deg b=45deg+-5deg
0000001301

(1)Pump vertical direction
(2)Coupling's key groove position at No 1 cylinder's beginning of injection
(3)Pre-stroke: aa
(4)-
----------
aa=5.6+-0.03mm
----------
a=(20deg)
----------
aa=5.6+-0.03mm
----------
a=(20deg)
0000001401
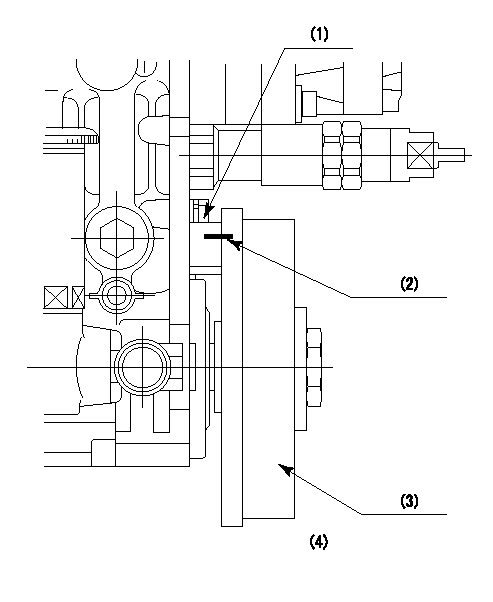
(1)Pointer
(2)Injection timing aligning mark
(3)Fly weight
(4)The actual shape and direction may be different from this illustration.
Operation sequence
1. Turn the prestroke actuator OFF.
2. Turn the camshaft as far as the No.1 cylinder's beginning of injection position.
3. Check that the pointer alignment mark of the injection pump and the alignment mark of the flywheel are matching.
4. If they are not matching, erase the alignment mark on the flywheel side, and stamp an alignment mark on the flywheel position that matches with the pointer side alignment mark.
5. Check again that the coupling's key groove position is in the No.1 cylinder's beginning of injection position.
----------
----------
----------
----------
0000001701
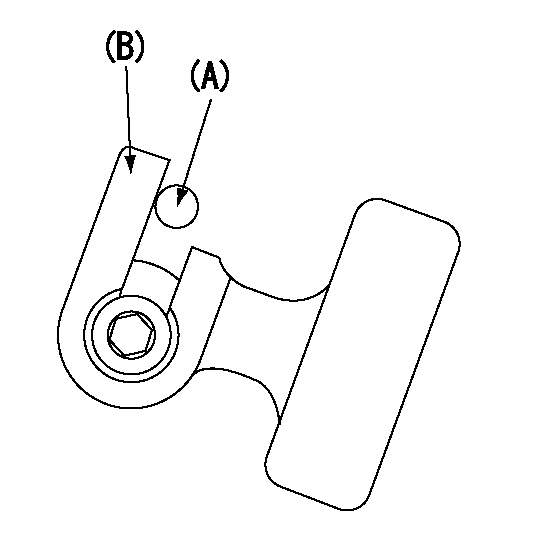
A : Stopper pin
B: Connector
----------
----------
----------
----------
0000001801
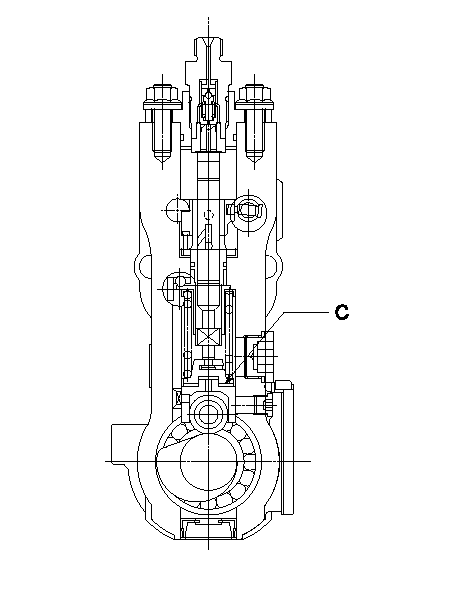
C:Shim
----------
----------
----------
----------
0000001901
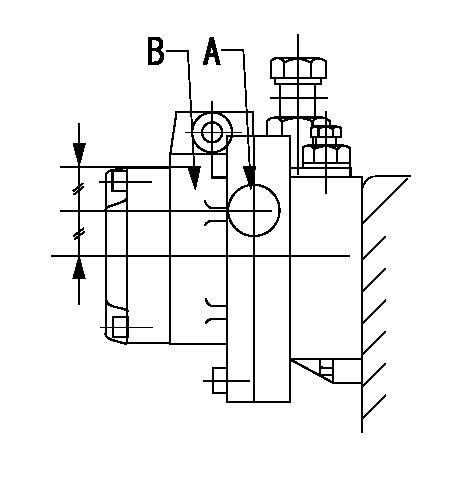
A:Sealing position
B:Pre-stroke actuator
1. When installing the pre-stroke actuator on the pump, first tighten the installation bolts loosely, then move the actuator fully counterclockwise (viewed from the drive side).
Temporary tightening torque: 1 - 1.5 N.m (0.1 - 0.15 kgf.m)
2. Move the actuator in the clockwise direction when viewed from the drive side, and adjust so that it becomes the adjustment point of the adjustment value. Then tighten it.
Tightening torque: 7^9 N.m (0.7^0.9 kgf.m)
3. After prestroke actuator installation adjustment, simultaneously stamp both the actuator side and housing side.
----------
----------
----------
----------
0000002201 RACK SENSOR
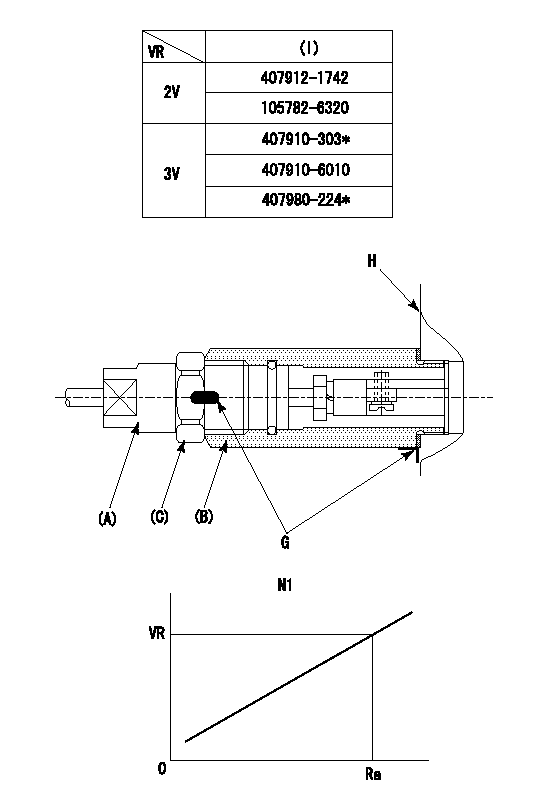
(VR) measurement voltage
(I) Part number of the control unit
(G) Apply red paint.
(H): End surface of the pump
1. Rack sensor adjustment (-0620)
(1)Fix the speed control lever at the full position
(2)Set the speed to N1 r/min.
(If the boost compensator is provided, apply boost pressure.)
(3)Adjust the bobbin (A) so that the rack sensor's output voltage is VR+-0.01.
(4)At that time, rack position must be Ra.
(5)Apply G at two places.
Connecting part between the joint (B) and the nut (F)
Connecting part between the joint (B) and the end surface of the pump (H)
----------
N1=1400r/min Ra=R1(13.8)mm
----------
----------
N1=1400r/min Ra=R1(13.8)mm
----------
0000002301 ACS
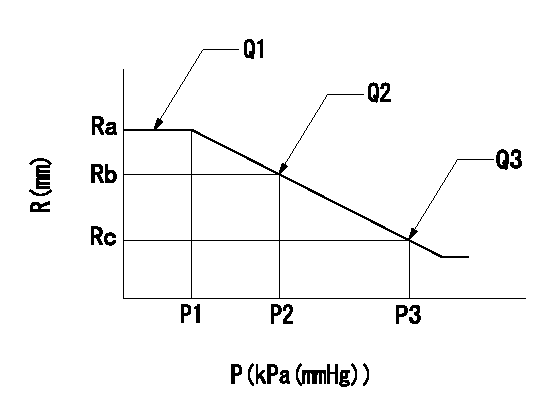
(P) Absolute pressure
(R) Rack position (mm)
1. Adjustment of the aneroid compensator
(1)Screw in the aneroid compensator body and attach the pushrod to the compensator lever so that the performance in the above graph can be obtained. The control lever must be at the full set position N = N1.
----------
N1=1400r/min
----------
Ra=R1(13.8)mm Rb=- Rc=(R1-0.7)mm P1=(94)+-2.7kPa((705)+-20mmHg) P2=- P3=74.6+-0.7kPa(560+-5mmHg) Q1=112+-1cm3/1000st Q2=- Q3=102+-2cm3/1000st
----------
N1=1400r/min
----------
Ra=R1(13.8)mm Rb=- Rc=(R1-0.7)mm P1=(94)+-2.7kPa((705)+-20mmHg) P2=- P3=74.6+-0.7kPa(560+-5mmHg) Q1=112+-1cm3/1000st Q2=- Q3=102+-2cm3/1000st
Information:
ELC cooling systems can withstand contamination of up to ten percent of conventional HD coolant/antifreeze. If the contamination exceeds ten percent of the total system capacity, perform either one of the following two procedures:* Drain the cooling system. Flush the system with clean water. Refill the system with ELC.* Maintain the cooling system as if the system is filled with conventional HD coolant/antifreeze.Commercial Extended Life Coolant
If Caterpillar extended life coolant is not used, select a commercial extended life coolant that meets the Caterpillar EC-1 specification. Do not use a product that is labeled as an extended life coolant but does not meet the Caterpillar EC-1 specification. Follow the coolant maintenance guidelines of the commercial extended life coolant supplier. In all cases, use distilled or deionized water or use water that has the properties listed in the Caterpillar Water Quality Limits chart.Caterpillar Diesel Engine Antifreeze/Coolant (DEAC)
For cooling systems using conventional HD coolant, Caterpillar recommends the use of Caterpillar Diesel Engine Antifreeze/Coolant (DEAC). DEAC is an alkaline type, single-phase, ethylene glycol-based antifreeze/coolant. DEAC contains inorganic corrosion inhibitors and anti-foaming agents.Contact your Caterpillar dealer for part numbers and available container sizes.Caterpillar DEAC is available premixed with distilled water in a 50/50 concentration. If DEAC concentrate is used, Caterpillar recommends mixing the concentrate with distilled or deionized water. If distilled or deionized water is not available, use water that has the properties listed in the Caterpillar Water Quality Limits chart.Caterpillar Supplemental Coolant Additive (SCA)
Caterpillar Supplemental Coolant Additive (SCA) is effective in preventing corrosion on all metals. Caterpillar SCA also prevents the formation of mineral deposits, prevents liner cavitation, and eliminates coolant foaming.Caterpillar DEAC is formulated with the correct level of Caterpillar SCA. Additional SCA is NOT needed when the cooling system is initially filled with DEAC.Contact your Caterpillar dealer for part numbers and available container sizes.Commercial Heavy Duty (HD) Coolant/Antifreeze and SCA
If Caterpillar DEAC is not used, select a low silicate commercial HD coolant/antifreeze that meets ASTM D5345 or D4985 specifications.When a commercial HD coolant/antifreeze is used, the cooling system should be treated with three to six percent Caterpillar SCA by volume. Refer to the Caterpillar SCA Requirements for Heavy Duty Coolant/Antifreeze chart. If Caterpillar SCA is not used, select a commercial SCA. The commercial SCA must provide a minimum of 1200 mg/L or 1200 ppm (70 grains/US gal) nitrites in the final coolant mixture. Follow the coolant maintenance guidelines of the commercial SCA supplier.HD coolant/antifreezes that meet ASTM D5345 or D4985 specifications DO require SCA treatment at initial fill, and on a maintenance basis.When mixing concentrated coolants, use distilled or deionized water or use water that has the properties listed in the Caterpillar Water Quality Limits chart.Heavy Duty Coolant/Antifreeze Cooling System Maintenance
Never operate an engine without thermostats in the cooling system. Thermostats maintain the engine coolant at the proper operating temperature. Cooling system problems can develop without thermostats.
Check the coolant/antifreeze solution (glycol content) frequently to ensure adequate anti-boil and anti-freeze protection. Caterpillar recommends the use of a refractometer for checking the
If Caterpillar extended life coolant is not used, select a commercial extended life coolant that meets the Caterpillar EC-1 specification. Do not use a product that is labeled as an extended life coolant but does not meet the Caterpillar EC-1 specification. Follow the coolant maintenance guidelines of the commercial extended life coolant supplier. In all cases, use distilled or deionized water or use water that has the properties listed in the Caterpillar Water Quality Limits chart.Caterpillar Diesel Engine Antifreeze/Coolant (DEAC)
For cooling systems using conventional HD coolant, Caterpillar recommends the use of Caterpillar Diesel Engine Antifreeze/Coolant (DEAC). DEAC is an alkaline type, single-phase, ethylene glycol-based antifreeze/coolant. DEAC contains inorganic corrosion inhibitors and anti-foaming agents.Contact your Caterpillar dealer for part numbers and available container sizes.Caterpillar DEAC is available premixed with distilled water in a 50/50 concentration. If DEAC concentrate is used, Caterpillar recommends mixing the concentrate with distilled or deionized water. If distilled or deionized water is not available, use water that has the properties listed in the Caterpillar Water Quality Limits chart.Caterpillar Supplemental Coolant Additive (SCA)
Caterpillar Supplemental Coolant Additive (SCA) is effective in preventing corrosion on all metals. Caterpillar SCA also prevents the formation of mineral deposits, prevents liner cavitation, and eliminates coolant foaming.Caterpillar DEAC is formulated with the correct level of Caterpillar SCA. Additional SCA is NOT needed when the cooling system is initially filled with DEAC.Contact your Caterpillar dealer for part numbers and available container sizes.Commercial Heavy Duty (HD) Coolant/Antifreeze and SCA
If Caterpillar DEAC is not used, select a low silicate commercial HD coolant/antifreeze that meets ASTM D5345 or D4985 specifications.When a commercial HD coolant/antifreeze is used, the cooling system should be treated with three to six percent Caterpillar SCA by volume. Refer to the Caterpillar SCA Requirements for Heavy Duty Coolant/Antifreeze chart. If Caterpillar SCA is not used, select a commercial SCA. The commercial SCA must provide a minimum of 1200 mg/L or 1200 ppm (70 grains/US gal) nitrites in the final coolant mixture. Follow the coolant maintenance guidelines of the commercial SCA supplier.HD coolant/antifreezes that meet ASTM D5345 or D4985 specifications DO require SCA treatment at initial fill, and on a maintenance basis.When mixing concentrated coolants, use distilled or deionized water or use water that has the properties listed in the Caterpillar Water Quality Limits chart.Heavy Duty Coolant/Antifreeze Cooling System Maintenance
Never operate an engine without thermostats in the cooling system. Thermostats maintain the engine coolant at the proper operating temperature. Cooling system problems can develop without thermostats.
Check the coolant/antifreeze solution (glycol content) frequently to ensure adequate anti-boil and anti-freeze protection. Caterpillar recommends the use of a refractometer for checking the