Information injection-pump assembly
BOSCH
9 400 619 060
9400619060
ZEXEL
107692-2280
1076922280
MITSUBISHI
ME170426
me170426
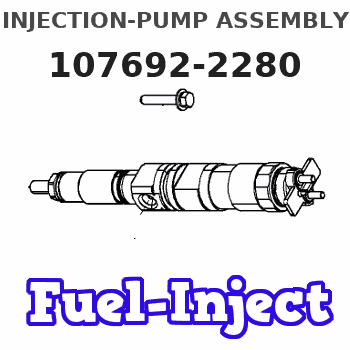
Rating:
Cross reference number
BOSCH
9 400 619 060
9400619060
ZEXEL
107692-2280
1076922280
MITSUBISHI
ME170426
me170426
Zexel num
Bosch num
Firm num
Name
107692-2280
9 400 619 060
ME170426 MITSUBISHI
INJECTION-PUMP ASSEMBLY
6D16T5 K 14CG INJECTION PUMP ASSY TICS MD-TI6 TICS
6D16T5 K 14CG INJECTION PUMP ASSY TICS MD-TI6 TICS
Calibration Data:
Adjustment conditions
Test oil
1404 Test oil ISO4113 or {SAEJ967d}
1404 Test oil ISO4113 or {SAEJ967d}
Test oil temperature
degC
40
40
45
Nozzle and nozzle holder
105780-8250
Bosch type code
1 688 901 101
Nozzle
105780-0120
Bosch type code
1 688 901 990
Nozzle holder
105780-2190
Opening pressure
MPa
20.7
Opening pressure
kgf/cm2
211
Injection pipe
Outer diameter - inner diameter - length (mm) mm 8-3-600
Outer diameter - inner diameter - length (mm) mm 8-3-600
Overflow valve
131424-8420
Overflow valve opening pressure
kPa
255
221
289
Overflow valve opening pressure
kgf/cm2
2.6
2.25
2.95
Tester oil delivery pressure
kPa
255
255
255
Tester oil delivery pressure
kgf/cm2
2.6
2.6
2.6
PS/ACT control unit part no.
407980-2
24*
Digi switch no.
17
Direction of rotation (viewed from drive side)
Left L
Left L
Injection timing adjustment
Direction of rotation (viewed from drive side)
Left L
Left L
Injection order
1-5-3-6-
2-4
Pre-stroke
mm
5.6
5.57
5.63
Beginning of injection position
Governor side NO.1
Governor side NO.1
Difference between angles 1
Cal 1-5 deg. 60 59.75 60.25
Cal 1-5 deg. 60 59.75 60.25
Difference between angles 2
Cal 1-3 deg. 120 119.75 120.25
Cal 1-3 deg. 120 119.75 120.25
Difference between angles 3
Cal 1-6 deg. 180 179.75 180.25
Cal 1-6 deg. 180 179.75 180.25
Difference between angles 4
Cyl.1-2 deg. 240 239.75 240.25
Cyl.1-2 deg. 240 239.75 240.25
Difference between angles 5
Cal 1-4 deg. 300 299.75 300.25
Cal 1-4 deg. 300 299.75 300.25
Injection quantity adjustment
Adjusting point
-
Rack position
13.4
Pump speed
r/min
700
700
700
Average injection quantity
mm3/st.
122
120
124
Max. variation between cylinders
%
0
-3
3
Basic
*
Fixing the rack
*
PS407980-224*
V
2.25+-0.
01
PS407980-224*
mm
3.6+-0.0
5
Standard for adjustment of the maximum variation between cylinders
*
Injection quantity adjustment_02
Adjusting point
Z
Rack position
7.7+-0.5
Pump speed
r/min
510
510
510
Average injection quantity
mm3/st.
10.5
8.7
12.3
Max. variation between cylinders
%
0
-15
15
Fixing the rack
*
PS407980-224*
V
V1+0.05+
-0.01
PS407980-224*
mm
5.5+-0.0
3
Standard for adjustment of the maximum variation between cylinders
*
Remarks
Refer to items regarding the pre-stroke actuator
Refer to items regarding the pre-stroke actuator
Injection quantity adjustment_03
Adjusting point
A
Rack position
R1(13.4)
Pump speed
r/min
700
700
700
Average injection quantity
mm3/st.
122
121
123
Basic
*
Fixing the lever
*
Boost pressure
kPa
36
36
Boost pressure
mmHg
270
270
PS407980-224*
V
2.25+-0.
01
PS407980-224*
mm
3.6+-0.0
5
Injection quantity adjustment_04
Adjusting point
B
Rack position
R1+1.55
Pump speed
r/min
1350
1350
1350
Average injection quantity
mm3/st.
113
109
117
Fixing the lever
*
Boost pressure
kPa
36
36
Boost pressure
mmHg
270
270
PS407980-224*
V
2.25+-0.
01
PS407980-224*
mm
3.6+-0.0
5
Injection quantity adjustment_05
Adjusting point
C
Rack position
(R2-1.4)
Pump speed
r/min
250
250
250
Average injection quantity
mm3/st.
69
67
71
Fixing the lever
*
Boost pressure
kPa
0
0
0
Boost pressure
mmHg
0
0
0
PS407980-224*
V
2.25+-0.
01
PS407980-224*
mm
3.6+-0.0
5
Injection quantity adjustment_06
Adjusting point
D
Rack position
(R1-0.55
)
Pump speed
r/min
550
550
550
Average injection quantity
mm3/st.
118.5
114.5
122.5
Fixing the lever
*
Boost pressure
kPa
36
36
Boost pressure
mmHg
270
270
PS407980-224*
V
2.25+-0.
01
PS407980-224*
mm
3.6+-0.0
5
Boost compensator adjustment
Pump speed
r/min
250
250
250
Rack position
(R2-1.4)
Boost pressure
kPa
8
6.7
9.3
Boost pressure
mmHg
60
50
70
Boost compensator adjustment_02
Pump speed
r/min
250
250
250
Rack position
R2(R1-1.
3)
Boost pressure
kPa
22.7
22.7
22.7
Boost pressure
mmHg
170
170
170
0000001601
CU407980-224*
*
Actuator retarding type
*
Supply voltage
V
24
23.5
24.5
Ambient temperature
degC
23
18
28
Pre-stroke
mm
2.5
2.45
2.55
Output voltage
V
2.83
2.82
2.84
Adjustment
*
_02
CU407980-224*
*
Supply voltage
V
24
23.5
24.5
Ambient temperature
degC
23
18
28
Pre-stroke
mm
5.6
5.57
5.63
Output voltage
V
1.2
1
1.4
Confirmation
*
Remarks
Output voltage V1
Output voltage V1
_03
CU407980-224*
*
Supply voltage
V
24
23.5
24.5
Ambient temperature
degC
23
18
28
Output voltage
V
3.05
3.05
Confirmation of operating range
*
Test data Ex:
Governor adjustment

N:Pump speed
R:Rack position (mm)
(1)Torque cam stamping: T1
(2)Tolerance for racks not indicated: +-0.05mm.
(3)Boost compensator stroke: BCL
----------
T1=AC34 BCL=(1.4)+-0.1mm
----------
----------
T1=AC34 BCL=(1.4)+-0.1mm
----------
Speed control lever angle
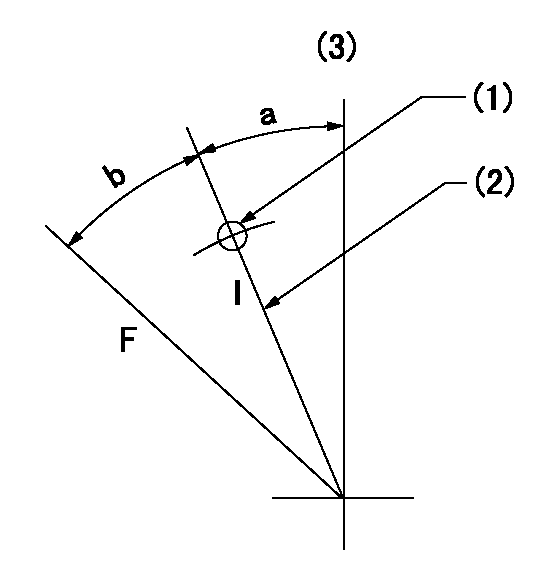
F:Full speed
I:Idle
(1)Use the hole at R = aa
(2)Stopper bolt set position 'H'
(3)Accelerator lever
----------
aa=38mm
----------
a=30deg+-5deg b=39.5deg+-3deg
----------
aa=38mm
----------
a=30deg+-5deg b=39.5deg+-3deg
Stop lever angle
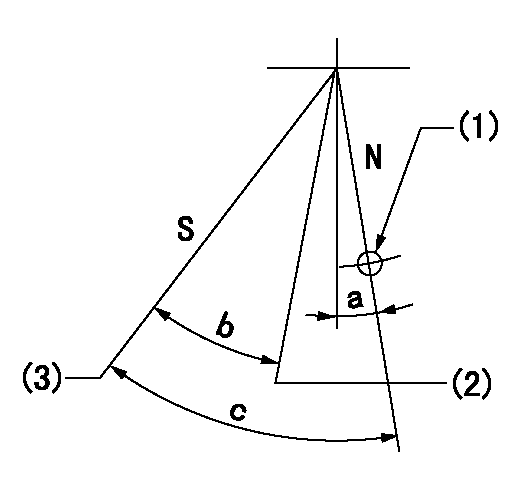
N:Pump normal
S:Stop the pump.
(1)Use the hole at R = aa
(2)Normal engine position (Rack position corresponding to bb)
(3)Set the stopper bolt at rack position = cc and speed = dd and confirm non-injection
----------
aa=47mm bb=17.4mm cc=3.5+-0.3mm dd=0r/min
----------
a=4deg+-5deg b=(31deg) c=41deg+-5deg
----------
aa=47mm bb=17.4mm cc=3.5+-0.3mm dd=0r/min
----------
a=4deg+-5deg b=(31deg) c=41deg+-5deg
0000001301
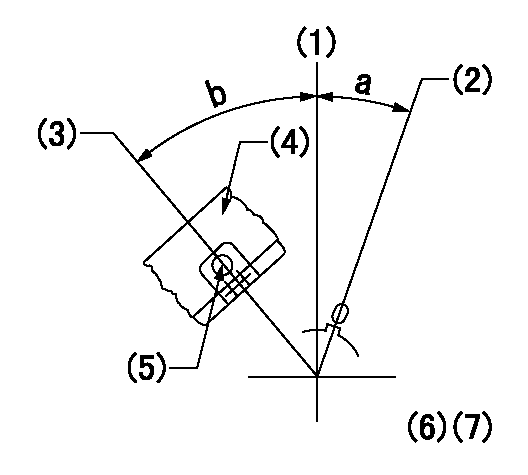
(1)Pump vertical direction
(2)Coupling's key groove position at No 1 cylinder's beginning of injection
(3)At the No 1 cylinder's beginning of injection position, stamp an aligning mark on the damper to align with the pointer's groove.
(4)Damper
(5)Pointer
(6)B.T.D.C.: aa
(7)Pre-stroke: bb
----------
aa=2deg bb=5.6+-0.03mm
----------
a=(0deg) b=(40deg)
----------
aa=2deg bb=5.6+-0.03mm
----------
a=(0deg) b=(40deg)
0000001401
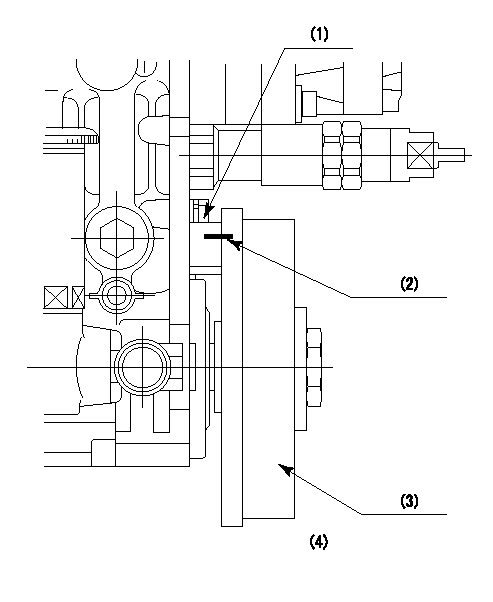
(1)Pointer
(2)Injection timing aligning mark
(3)Fly weight
(4)The actual shape and direction may be different from this illustration.
Operation sequence
1. Turn the prestroke actuator OFF.
2. Turn the camshaft as far as the No.1 cylinder's beginning of injection position.
3. Check that the pointer alignment mark of the injection pump and the alignment mark of the flywheel are matching.
4. If they are not matching, erase the alignment mark on the flywheel side, and stamp an alignment mark on the flywheel position that matches with the pointer side alignment mark.
5. Check again that the coupling's key groove position is in the No.1 cylinder's beginning of injection position.
----------
----------
----------
----------
0000001701
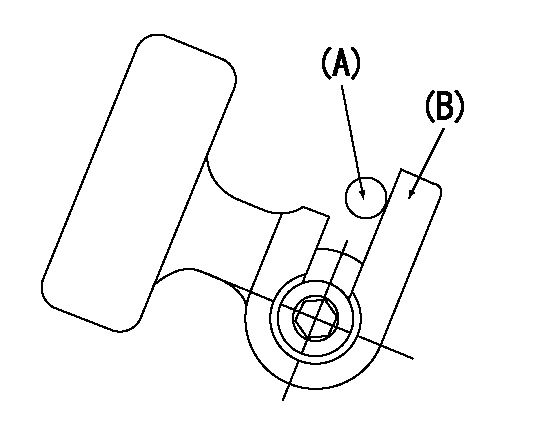
A : Stopper pin
B: Connector
----------
----------
----------
----------
0000001801
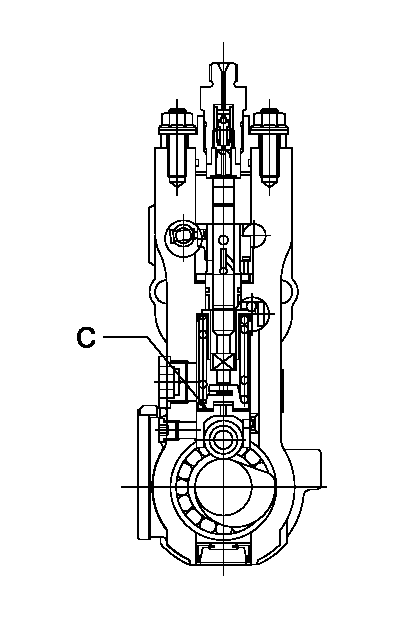
C:Shim
----------
----------
----------
----------
0000001901
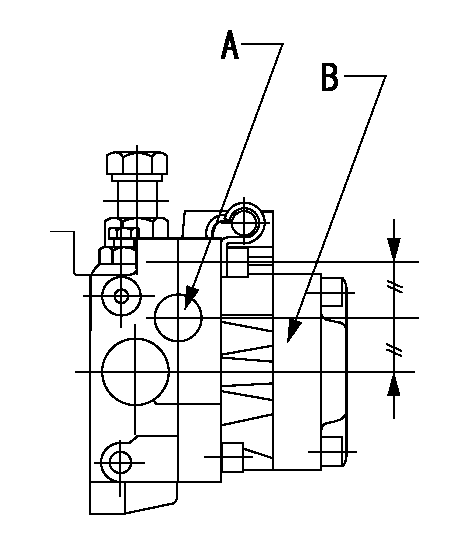
A:Sealing position
B:Pre-stroke actuator
1. When installing the pre-stroke actuator on the pump, first tighten the installation bolts loosely, then move the actuator fully clockwise (viewed from the drive side).
Temporary tightening torque: 1 - 1.5 N.m (0.1 - 0.15 kgf.m)
2. Move the actuator in the counterclockwise direction when viewed from the drive side, and adjust so that it becomes the adjustment point of the adjustment value. Then tighten it.
Tightening torque: 7^9 N.m (0.7^0.9 kgf.m)
3. After prestroke actuator installation adjustment, simultaneously stamp both the actuator side and housing side.
----------
----------
----------
----------
0000002201 RACK SENSOR
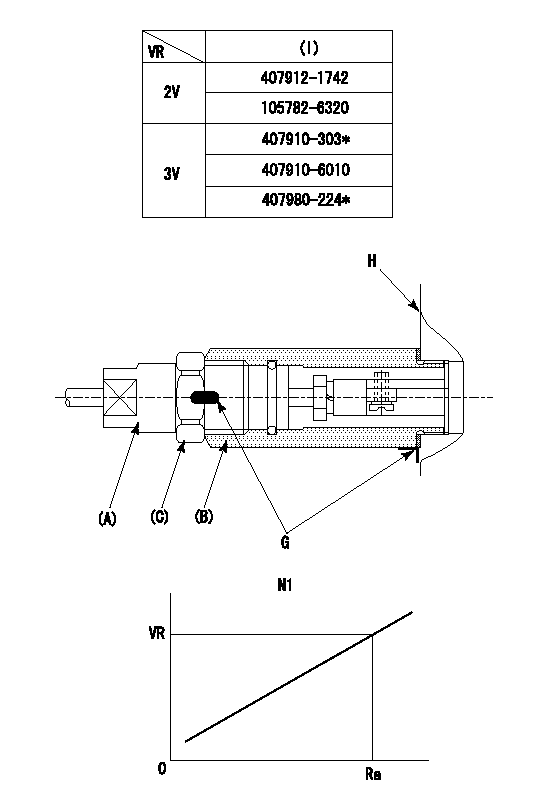
(VR) measurement voltage
(I) Part number of the control unit
(G) Apply red paint.
(H): End surface of the pump
1. Rack sensor adjustment (-0620)
(1)Fix the speed control lever at the full position
(2)Set the speed to N1 r/min.
(If the boost compensator is provided, apply boost pressure.)
(3)Adjust the bobbin (A) so that the rack sensor's output voltage is VR+-0.01.
(4)At that time, rack position must be Ra.
(5)Apply G at two places.
Connecting part between the joint (B) and the nut (F)
Connecting part between the joint (B) and the end surface of the pump (H)
----------
N1=1350r/min Ra=R1(13.4)+1.55mm
----------
----------
N1=1350r/min Ra=R1(13.4)+1.55mm
----------
0000002301 SPEED SENSOR

(A) Flyweight projection
(B) Pickup sensor
(c) Lock nut
Speed sensor installation
(1)Install the speed sensor so that the clearance between the sensor and the flyweight projection is L.
(This gap is the gap when the pickup sensor is returned 1 turn from where it contacts the flyweight tooth.)
----------
L=0.8~1mm
----------
----------
L=0.8~1mm
----------
Information:
Under the Hood Inspection
For maximum service life of your truck engine, make a thorough under the hood inspection before starting the engine. Look for such items as oil or coolant leaks, loose bolts, worn belts and trash build-up. Remove trash build-up and have repairs made as needed.Perform required Daily maintenance before starting the engine.
Each time any significant quantity of oil (or other fluid) is spilled on or near the engine it should be cleaned up. Accumulated grease and oil on an engine is a fire hazard. Remove this debris with steam cleaning or high pressure water at PM Level 2 or every 6000 hours.Wipe clean all fittings, caps and plugs before servicing.
Starting the Engine
Do not store starting fluid containers in the cab. Failure to do so, could result in an explosion and/or fire and possible personal injury.If equipped with an electrically or fuel ignited manifold heater, DO NOT use ether.
Startability will be improved at temperatures below +32°F (0°C) by the use of a starting aid (ether) or use of a cylinder block coolant heater or other means to heat the crankcase oil. This will help alleviate white smoke and misfire during cold weather start-up.Use ether when temperatures are below 32°F (0°C) for cold weather starting purposes only.
When using starting fluid, follow the manufacturer's instructions carefully, use it sparingly and spray it ONLY WHILE CRANKING THE ENGINE. Excessive ether can cause piston and ring damage.Use ether for cold starting purposes only.
If the engine fails to start within 30 seconds, release the starter switch and wait two minutes to allow the starter motor to cool before using it again.Start the engine using the following procedure:1. Place the transmission in NEUTRAL and disengage the flywheel clutch (if equipped) to remove the transmission drag and prevent movement of the truck.Depressing the clutch in cold weather can mean the difference between starting and not starting. Depressing the clutch in warm weather produces faster starts and reduces battery drain.2. Turn the ignition switch to the ON position and push the crank button or turn the ignition switch to the START position.3. Crank the engine. If the engine fails to start in 30 seconds, release the starting (ignition) switch and wait two minutes to allow the starter motor to cool before using it again.
Do not increase engine speed until the oil pressure gauge indicates normal. Oil pressure should raise within 15 seconds after the engine starts.If oil pressure is not indicated on gauge within 15 seconds, do not drive the truck. Stop the engine, investigate and correct the cause.
4. Allow the engine to idle three to five minutes, or until the water temperature gauge has begun to rise. Check all gauges during the warm-up period.5. Check fuel level gauge. Do not fill fuel tank to top. Fuel expands as it gets warm and may overflow.Starting With Jumper Cables
When boost starting an engine, follow the instructions to properly start the engine. This engine may be equipped with a 12 or 24 volt starting system. Use only
For maximum service life of your truck engine, make a thorough under the hood inspection before starting the engine. Look for such items as oil or coolant leaks, loose bolts, worn belts and trash build-up. Remove trash build-up and have repairs made as needed.Perform required Daily maintenance before starting the engine.
Each time any significant quantity of oil (or other fluid) is spilled on or near the engine it should be cleaned up. Accumulated grease and oil on an engine is a fire hazard. Remove this debris with steam cleaning or high pressure water at PM Level 2 or every 6000 hours.Wipe clean all fittings, caps and plugs before servicing.
Starting the Engine
Do not store starting fluid containers in the cab. Failure to do so, could result in an explosion and/or fire and possible personal injury.If equipped with an electrically or fuel ignited manifold heater, DO NOT use ether.
Startability will be improved at temperatures below +32°F (0°C) by the use of a starting aid (ether) or use of a cylinder block coolant heater or other means to heat the crankcase oil. This will help alleviate white smoke and misfire during cold weather start-up.Use ether when temperatures are below 32°F (0°C) for cold weather starting purposes only.
When using starting fluid, follow the manufacturer's instructions carefully, use it sparingly and spray it ONLY WHILE CRANKING THE ENGINE. Excessive ether can cause piston and ring damage.Use ether for cold starting purposes only.
If the engine fails to start within 30 seconds, release the starter switch and wait two minutes to allow the starter motor to cool before using it again.Start the engine using the following procedure:1. Place the transmission in NEUTRAL and disengage the flywheel clutch (if equipped) to remove the transmission drag and prevent movement of the truck.Depressing the clutch in cold weather can mean the difference between starting and not starting. Depressing the clutch in warm weather produces faster starts and reduces battery drain.2. Turn the ignition switch to the ON position and push the crank button or turn the ignition switch to the START position.3. Crank the engine. If the engine fails to start in 30 seconds, release the starting (ignition) switch and wait two minutes to allow the starter motor to cool before using it again.
Do not increase engine speed until the oil pressure gauge indicates normal. Oil pressure should raise within 15 seconds after the engine starts.If oil pressure is not indicated on gauge within 15 seconds, do not drive the truck. Stop the engine, investigate and correct the cause.
4. Allow the engine to idle three to five minutes, or until the water temperature gauge has begun to rise. Check all gauges during the warm-up period.5. Check fuel level gauge. Do not fill fuel tank to top. Fuel expands as it gets warm and may overflow.Starting With Jumper Cables
When boost starting an engine, follow the instructions to properly start the engine. This engine may be equipped with a 12 or 24 volt starting system. Use only
Have questions with 107692-2280?
Group cross 107692-2280 ZEXEL
Mitsubishi
Mitsubishi
107692-2280
9 400 619 060
ME170426
INJECTION-PUMP ASSEMBLY
6D16T5
6D16T5