Information injection-pump assembly
BOSCH
9 400 613 341
9400613341
ZEXEL
107692-1800
1076921800
ISUZU
8976024190
8976024190
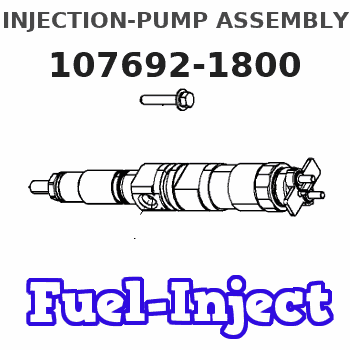
Rating:
Service parts 107692-1800 INJECTION-PUMP ASSEMBLY:
1.
_
5.
AUTOM. ADVANCE MECHANIS
7.
COUPLING PLATE
11.
Nozzle and Holder
8-94390-795-4
12.
Open Pre:MPa(Kqf/cm2)
18.1{185}/22.1{225}
14.
NOZZLE
Include in #1:
107692-1800
as INJECTION-PUMP ASSEMBLY
Cross reference number
BOSCH
9 400 613 341
9400613341
ZEXEL
107692-1800
1076921800
ISUZU
8976024190
8976024190
Zexel num
Bosch num
Firm num
Name
Calibration Data:
Adjustment conditions
Test oil
1404 Test oil ISO4113 or {SAEJ967d}
1404 Test oil ISO4113 or {SAEJ967d}
Test oil temperature
degC
40
40
45
Nozzle and nozzle holder
105780-8250
Bosch type code
1 688 901 101
Nozzle
105780-0120
Bosch type code
1 688 901 990
Nozzle holder
105780-2190
Opening pressure
MPa
20.7
Opening pressure
kgf/cm2
211
Injection pipe
Outer diameter - inner diameter - length (mm) mm 8-3-600
Outer diameter - inner diameter - length (mm) mm 8-3-600
Overflow valve
131425-1820
Overflow valve opening pressure
kPa
255
221
289
Overflow valve opening pressure
kgf/cm2
2.6
2.25
2.95
Tester oil delivery pressure
kPa
255
255
255
Tester oil delivery pressure
kgf/cm2
2.6
2.6
2.6
PS/ACT control unit part no.
407980-2
24*
Digi switch no.
17
Direction of rotation (viewed from drive side)
Left L
Left L
Injection timing adjustment
Direction of rotation (viewed from drive side)
Left L
Left L
Injection order
1-5-3-6-
2-4
Pre-stroke
mm
5.1
5.07
5.13
Beginning of injection position
Governor side NO.1
Governor side NO.1
Difference between angles 1
Cal 1-5 deg. 60 59.75 60.25
Cal 1-5 deg. 60 59.75 60.25
Difference between angles 2
Cal 1-3 deg. 120 119.75 120.25
Cal 1-3 deg. 120 119.75 120.25
Difference between angles 3
Cal 1-6 deg. 180 179.75 180.25
Cal 1-6 deg. 180 179.75 180.25
Difference between angles 4
Cyl.1-2 deg. 240 239.75 240.25
Cyl.1-2 deg. 240 239.75 240.25
Difference between angles 5
Cal 1-4 deg. 300 299.75 300.25
Cal 1-4 deg. 300 299.75 300.25
Injection quantity adjustment
Adjusting point
-
Rack position
14.2
Pump speed
r/min
850
850
850
Average injection quantity
mm3/st.
114
112.4
115.6
Max. variation between cylinders
%
0
-2.5
2.5
Basic
*
Fixing the rack
*
PS407980-224*
V
2.25+-0.
01
PS407980-224*
mm
3.1+-0.0
5
Standard for adjustment of the maximum variation between cylinders
*
Injection quantity adjustment_02
Adjusting point
Z
Rack position
8.5+-0.5
Pump speed
r/min
435
435
435
Average injection quantity
mm3/st.
9
7.7
10.3
Max. variation between cylinders
%
0
-14
14
Fixing the rack
*
PS407980-224*
V
V1+0.05+
-0.01
PS407980-224*
mm
5+-0.03
Standard for adjustment of the maximum variation between cylinders
*
Remarks
Refer to items regarding the pre-stroke actuator
Refer to items regarding the pre-stroke actuator
Injection quantity adjustment_03
Adjusting point
A
Rack position
R1(14.2)
Pump speed
r/min
850
850
850
Average injection quantity
mm3/st.
114
113
115
Basic
*
Fixing the lever
*
PS407980-224*
V
2.25+-0.
01
PS407980-224*
mm
3.1+-0.0
5
Injection quantity adjustment_04
Adjusting point
B
Rack position
R1+2
Pump speed
r/min
1450
1450
1450
Average injection quantity
mm3/st.
113.5
103.5
123.5
Fixing the lever
*
PS407980-224*
V
2.25+-0.
01
PS407980-224*
mm
3.1+-0.0
5
0000001601
CU407980-224*
*
Actuator retarding type
*
Supply voltage
V
24
23.5
24.5
Ambient temperature
degC
23
18
28
Pre-stroke
mm
2
1.95
2.05
Output voltage
V
2.83
2.82
2.84
Adjustment
*
_02
CU407980-224*
*
Supply voltage
V
24
23.5
24.5
Ambient temperature
degC
23
18
28
Pre-stroke
mm
5.1
5.07
5.13
Output voltage
V
1.2
1
1.4
Confirmation
*
Remarks
Output voltage V1
Output voltage V1
_03
CU407980-224*
*
Supply voltage
V
24
23.5
24.5
Ambient temperature
degC
23
18
28
Output voltage
V
3.05
3.05
Confirmation of operating range
*
Test data Ex:
Governor adjustment
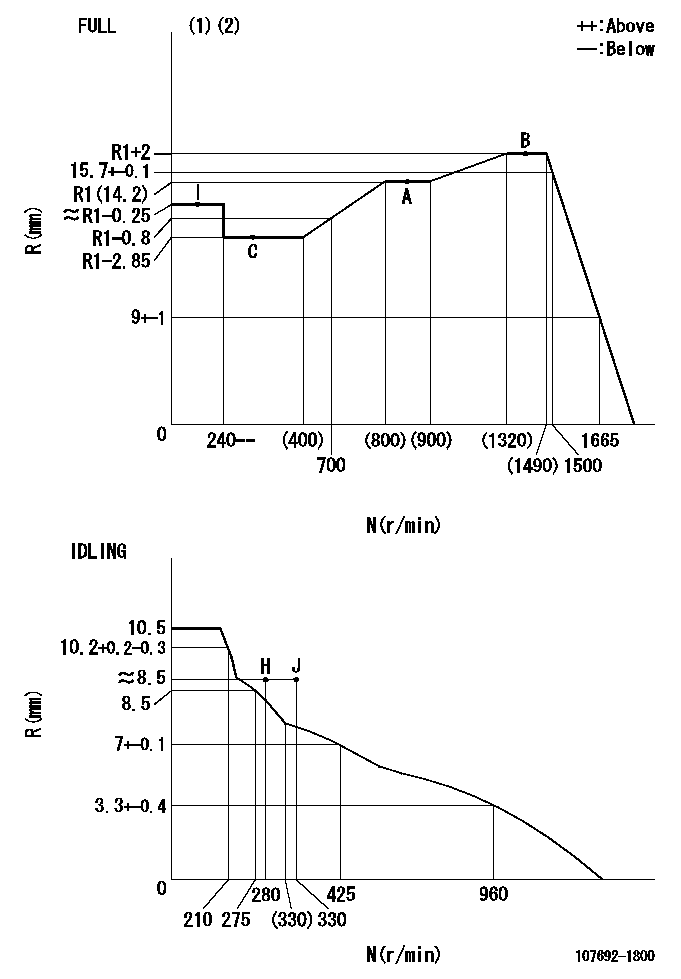
N:Pump speed
R:Rack position (mm)
(1)Torque cam stamping: T1
(2)Tolerance for racks not indicated: +-0.05mm.
----------
T1=AH10
----------
----------
T1=AH10
----------
Speed control lever angle

F:Full speed
I:Idle
(1)Use the pin at R = aa
(2)Stopper bolt set position 'H'
----------
aa=35mm
----------
a=1deg+-5deg b=36deg+-3deg
----------
aa=35mm
----------
a=1deg+-5deg b=36deg+-3deg
Stop lever angle
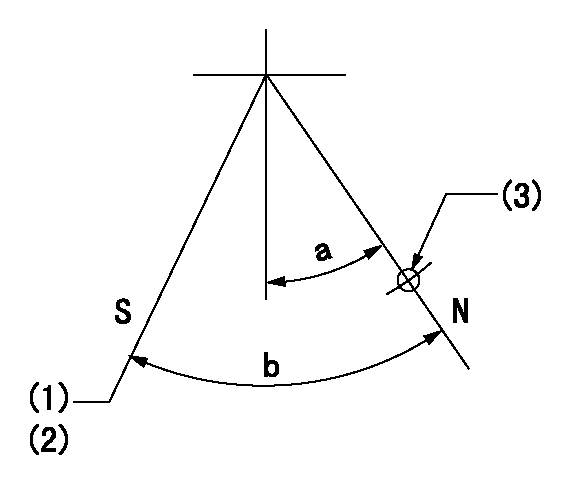
N:Pump normal
S:Stop the pump.
(1)Set the stopper bolt at speed = aa and rack position = bb.
(2)Non-injection rack position
(3)Use the pin above R = cc
----------
aa=0r/min bb=1.5+-0.3mm cc=40mm
----------
a=12deg+-5deg b=44deg+-5deg
----------
aa=0r/min bb=1.5+-0.3mm cc=40mm
----------
a=12deg+-5deg b=44deg+-5deg
0000001301
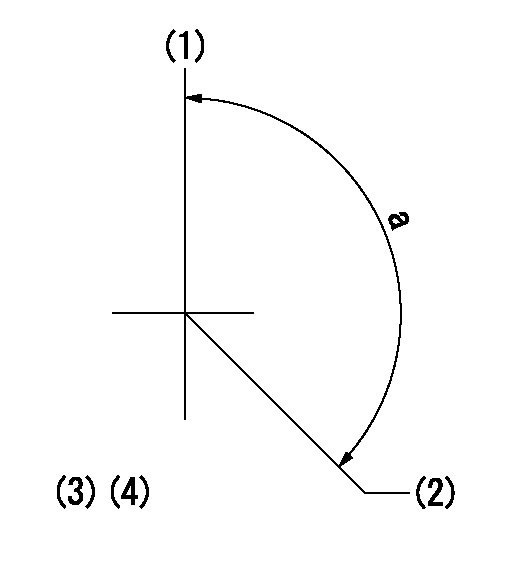
(1)Pump vertical direction
(2)Positions of coupling's threaded installation holes at No 1 cylinder's beginning of injection
(3)B.T.D.C.: aa
(4)Pre-stroke: bb
----------
aa=6deg bb=5.1+-0.03mm
----------
a=(140deg)
----------
aa=6deg bb=5.1+-0.03mm
----------
a=(140deg)
0000001401
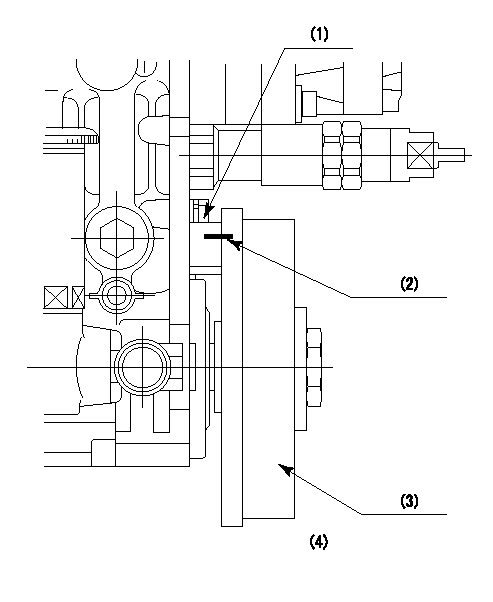
(1)Pointer
(2)Injection timing aligning mark
(3)Fly weight
(4)The actual shape and direction may be different from this illustration.
Operation sequence
1. Turn the prestroke actuator OFF.
2. Turn the camshaft as far as the No.1 cylinder's beginning of injection position.
3. Check that the pointer alignment mark of the injection pump and the alignment mark of the flywheel are matching.
4. If they are not matching, erase the alignment mark on the flywheel side, and stamp an alignment mark on the flywheel position that matches with the pointer side alignment mark.
5. Check again that the coupling's key groove position is in the No.1 cylinder's beginning of injection position.
----------
----------
----------
----------
0000001701
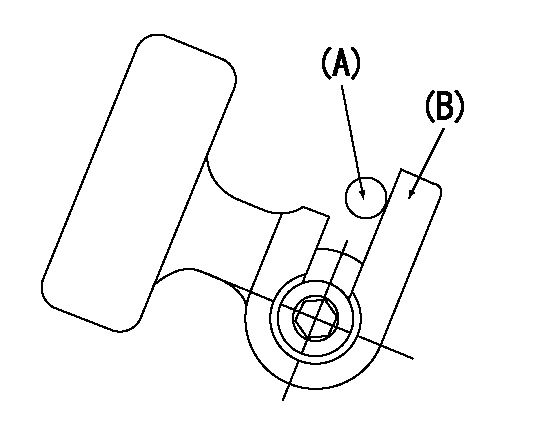
A : Stopper pin
B: Connector
----------
----------
----------
----------
0000001801
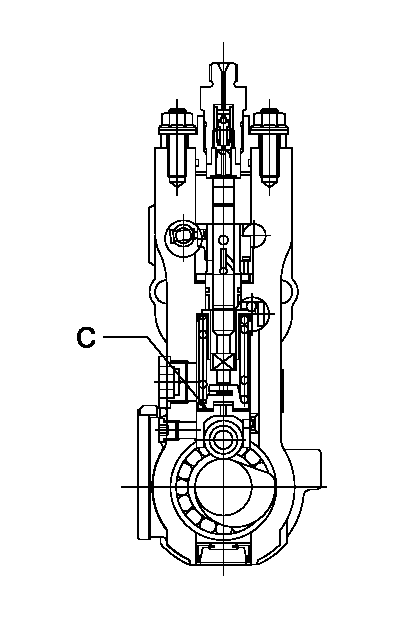
C:Shim
----------
----------
----------
----------
0000001901
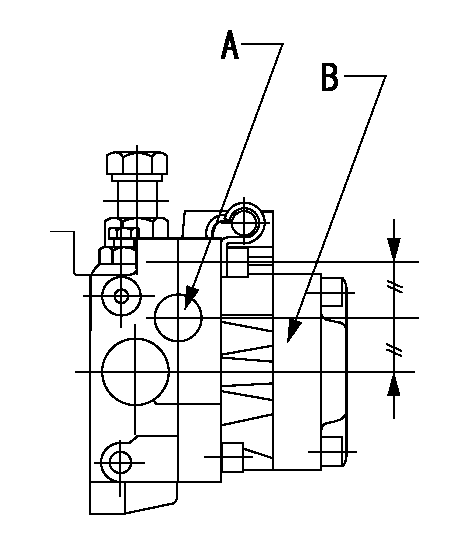
A:Sealing position
B:Pre-stroke actuator
1. When installing the pre-stroke actuator on the pump, first tighten the installation bolts loosely, then move the actuator fully clockwise (viewed from the drive side).
Temporary tightening torque: 1 - 1.5 N.m (0.1 - 0.15 kgf.m)
2. Move the actuator in the counterclockwise direction when viewed from the drive side, and adjust so that it becomes the adjustment point of the adjustment value. Then tighten it.
Tightening torque: 7^9 N.m (0.7^0.9 kgf.m)
3. After prestroke actuator installation adjustment, simultaneously stamp both the actuator side and housing side.
----------
----------
----------
----------
0000002201 RACK SENSOR

G:Red paint
H:Pump end face
P/N: part number of suitable shim
(1)Threaded type rack block
(2)Welded type rack block
Rack sensor adjustment
1. Threaded type rack sensor (-5*20, P type, no TICS rack limit).
(1)Screw in the bobbin (A) until it contacts the joint (B).
(2)Fix the pump lever.
(3)At speed N1 and rack position Ra, adjust the amount that the bobbin is screwed in so that the amp's output voltage is V1.
(4)Fix using the nut (F).
(5)Affix the caution plate to the upper part of the joint (B).
(6)Apply (G) at two places.
Connecting part between the joint (B) and the nut (F)
Connecting part between the end surface of the pump (H) and the joint (B)
2. Range for screw-in adjustment between the bobbin (A) and the joint (B) is 9 threads.
Screw in to the end from (the position where the bobbin (A) is rotated 9 turns).
Speed N1, rack position Ra, output voltage V1, rack sensor supply voltage 5+-0.01 (V)
----------
Ra=R1(14.2)+2mm N1=1450r/min V1=3+-0.01V
----------
----------
Ra=R1(14.2)+2mm N1=1450r/min V1=3+-0.01V
----------
Information:
Literature Information
This manual contains information and instructions concerning engine safety, operation, lubrication, and maintenance. Read, study, and keep it available with other literature and engine information.Some photographs or illustrations in this publication show details or attachments that may differ from your engine. Guards and covers may have been removed for illustrative purposes. Continuing improvement and advancement of product design may have caused changes to your engine which are not included in this publication.Whenever a question arises regarding your engine, or this publication, please consult your Caterpillar dealer for the latest available information.Safety
The safety section lists basic safety precautions. In addition, this section identifies hazardous, warning situations. Read and understand the basic precautions listed in the safety section before operating or performing lubrication, maintenance and/or repair on this product.Operation
Engine operation outlined in this publication is basic. Engine operators gain knowledge of the engine through experience, developing operation skills and techniques which enhance efficient and economical engine operation.The operation section is a reference for operators. Photographs and illustrations guide operators through correct procedures of inspecting, starting, operating and stopping the engine. Discussion of gauges and engine control information is included.Maintenance
The maintenance section is a guide to engine care. The illustrated instructions are grouped by maintenance service intervals. The actual operating environment of the engine also governs the maintenance schedule. Under extremely severe, dusty, or frigid operating conditions, lubrication and maintenance checks more frequent than those specified in the Maintenance Schedule may be necessary.Maintenance Intervals
Use the service hour meter to determine service intervals. Calendar intervals shown (daily, weekly, monthly, etc.) can be used instead of service hour meter intervals, if they provide more convenient servicing schedules and approximate the indicated service hour meter reading. Recommended service should always be performed at the interval that occurs first.We recommend that the maintenance schedules be reproduced for ease of inspection. We also recommend that ongoing maintenance records be kept to document engine service.See the Maintenance Records section of this publication for information regarding documents that are generally accepted as proof of maintenance or repair. Your Caterpillar dealer can assist you in tailoring your Maintenance Schedule to meet the needs of your operating environment.Overhaul
Major engine repair details are not covered in this manual. Major repairs are best left to trained personnel or an authorized Caterpillar dealer.If a major engine failure requiring removal of the engine occurs, numerous after-failure overhaul options available from your Caterpillar dealer. Contact your dealer for information regarding these options.Engine Description
The engines described in this publication are 3304B and 3306B Industrial and EPG diesel engines.They are designed primarily for agricultural, prime power and standby electrical power generation, petroleum and auxiliary industrial applications.Engine Storage
For general information, refer to the Engine Lifting & Storage topic. For complete engine storage information refer to Special Instruction SEHS9031, Storage Procedure for Caterpillar Products.California
Proposition 65 WarningDiesel engine exhaust and some of its constituents are known to the state of California to cause cancer, birth defects, and other reproductive harm.
Illustration 1
EPA/EU Emissions Certification Film (typical example)
Illustration 2
EPA/EU Emissions Certification
This manual contains information and instructions concerning engine safety, operation, lubrication, and maintenance. Read, study, and keep it available with other literature and engine information.Some photographs or illustrations in this publication show details or attachments that may differ from your engine. Guards and covers may have been removed for illustrative purposes. Continuing improvement and advancement of product design may have caused changes to your engine which are not included in this publication.Whenever a question arises regarding your engine, or this publication, please consult your Caterpillar dealer for the latest available information.Safety
The safety section lists basic safety precautions. In addition, this section identifies hazardous, warning situations. Read and understand the basic precautions listed in the safety section before operating or performing lubrication, maintenance and/or repair on this product.Operation
Engine operation outlined in this publication is basic. Engine operators gain knowledge of the engine through experience, developing operation skills and techniques which enhance efficient and economical engine operation.The operation section is a reference for operators. Photographs and illustrations guide operators through correct procedures of inspecting, starting, operating and stopping the engine. Discussion of gauges and engine control information is included.Maintenance
The maintenance section is a guide to engine care. The illustrated instructions are grouped by maintenance service intervals. The actual operating environment of the engine also governs the maintenance schedule. Under extremely severe, dusty, or frigid operating conditions, lubrication and maintenance checks more frequent than those specified in the Maintenance Schedule may be necessary.Maintenance Intervals
Use the service hour meter to determine service intervals. Calendar intervals shown (daily, weekly, monthly, etc.) can be used instead of service hour meter intervals, if they provide more convenient servicing schedules and approximate the indicated service hour meter reading. Recommended service should always be performed at the interval that occurs first.We recommend that the maintenance schedules be reproduced for ease of inspection. We also recommend that ongoing maintenance records be kept to document engine service.See the Maintenance Records section of this publication for information regarding documents that are generally accepted as proof of maintenance or repair. Your Caterpillar dealer can assist you in tailoring your Maintenance Schedule to meet the needs of your operating environment.Overhaul
Major engine repair details are not covered in this manual. Major repairs are best left to trained personnel or an authorized Caterpillar dealer.If a major engine failure requiring removal of the engine occurs, numerous after-failure overhaul options available from your Caterpillar dealer. Contact your dealer for information regarding these options.Engine Description
The engines described in this publication are 3304B and 3306B Industrial and EPG diesel engines.They are designed primarily for agricultural, prime power and standby electrical power generation, petroleum and auxiliary industrial applications.Engine Storage
For general information, refer to the Engine Lifting & Storage topic. For complete engine storage information refer to Special Instruction SEHS9031, Storage Procedure for Caterpillar Products.California
Proposition 65 WarningDiesel engine exhaust and some of its constituents are known to the state of California to cause cancer, birth defects, and other reproductive harm.
Illustration 1
EPA/EU Emissions Certification Film (typical example)
Illustration 2
EPA/EU Emissions Certification