Information injection-pump assembly
BOSCH
9 400 619 886
9400619886
ZEXEL
107692-1610
1076921610
ISUZU
8976017170
8976017170
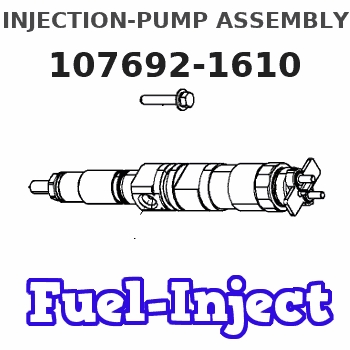
Rating:
Service parts 107692-1610 INJECTION-PUMP ASSEMBLY:
1.
_
5.
AUTOM. ADVANCE MECHANIS
9.
_
11.
Nozzle and Holder
8-97600-666-0
12.
Open Pre:MPa(Kqf/cm2)
21.6
15.
NOZZLE SET
Include in #1:
107692-1610
as INJECTION-PUMP ASSEMBLY
Cross reference number
BOSCH
9 400 619 886
9400619886
ZEXEL
107692-1610
1076921610
ISUZU
8976017170
8976017170
Zexel num
Bosch num
Firm num
Name
Calibration Data:
Adjustment conditions
Test oil
1404 Test oil ISO4113 or {SAEJ967d}
1404 Test oil ISO4113 or {SAEJ967d}
Test oil temperature
degC
40
40
45
Nozzle and nozzle holder
105780-8250
Bosch type code
1 688 901 101
Nozzle
105780-0120
Bosch type code
1 688 901 990
Nozzle holder
105780-2190
Opening pressure
MPa
20.7
Opening pressure
kgf/cm2
211
Injection pipe
Outer diameter - inner diameter - length (mm) mm 8-3-600
Outer diameter - inner diameter - length (mm) mm 8-3-600
Overflow valve
131425-1820
Overflow valve opening pressure
kPa
255
221
289
Overflow valve opening pressure
kgf/cm2
2.6
2.25
2.95
Tester oil delivery pressure
kPa
255
255
255
Tester oil delivery pressure
kgf/cm2
2.6
2.6
2.6
RED4 control unit part number
407915-0
590
RED4 rack sensor specifications
mm
19
PS/ACT control unit part no.
407980-2
24*
Digi switch no.
17
Direction of rotation (viewed from drive side)
Left L
Left L
Injection timing adjustment
Direction of rotation (viewed from drive side)
Left L
Left L
Injection order
1-5-3-6-
2-4
Pre-stroke
mm
5.1
5.07
5.13
Beginning of injection position
Governor side NO.1
Governor side NO.1
Difference between angles 1
Cal 1-5 deg. 60 59.75 60.25
Cal 1-5 deg. 60 59.75 60.25
Difference between angles 2
Cal 1-3 deg. 120 119.75 120.25
Cal 1-3 deg. 120 119.75 120.25
Difference between angles 3
Cal 1-6 deg. 180 179.75 180.25
Cal 1-6 deg. 180 179.75 180.25
Difference between angles 4
Cyl.1-2 deg. 240 239.75 240.25
Cyl.1-2 deg. 240 239.75 240.25
Difference between angles 5
Cal 1-4 deg. 300 299.75 300.25
Cal 1-4 deg. 300 299.75 300.25
Injection quantity adjustment
Rack position
(13.7)
PWM
%
65
Pump speed
r/min
750
750
750
Average injection quantity
mm3/st.
137.5
136.5
138.5
Max. variation between cylinders
%
0
-2.5
2.5
Basic
*
PS407980-224*
V
2.25+-0.
01
PS407980-224*
mm
3.1+-0.0
5
Injection quantity adjustment_02
Rack position
(6.9)
PWM
%
27.2+-2.
8
Pump speed
r/min
470
470
470
Average injection quantity
mm3/st.
9.5
8.2
10.8
Max. variation between cylinders
%
0
-14
14
PS407980-224*
V
V1+0.05+
-0.01
PS407980-224*
mm
5+-0.03
Remarks
Refer to items regarding the pre-stroke actuator
Refer to items regarding the pre-stroke actuator
0000001201
CU407980-224*
*
Actuator retarding type
*
Supply voltage
V
24
23.5
24.5
Ambient temperature
degC
23
18
28
Pre-stroke
mm
2
1.95
2.05
Output voltage
V
2.83
2.82
2.84
Adjustment
*
_02
CU407980-224*
*
Supply voltage
V
24
23.5
24.5
Ambient temperature
degC
23
18
28
Pre-stroke
mm
5.1
5.07
5.13
Output voltage
V
1.2
1
1.4
Confirmation
*
Remarks
Output voltage V1
Output voltage V1
_03
CU407980-224*
*
Supply voltage
V
24
23.5
24.5
Ambient temperature
degC
23
18
28
Output voltage
V
3.05
3.05
Confirmation of operating range
*
Test data Ex:
Speed control lever angle
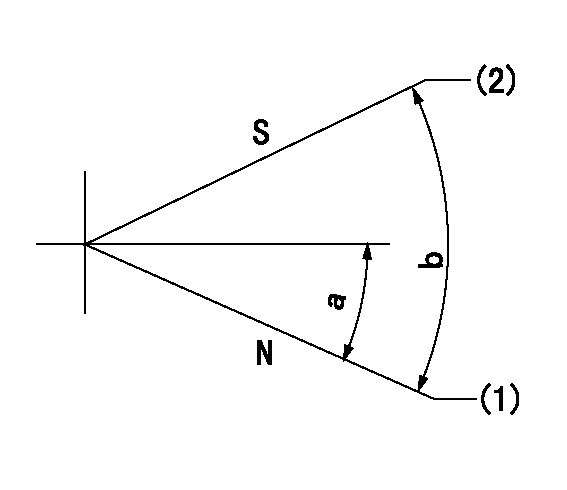
N:Pump normal
S:Stop the pump.
(1)Rack position = aa
(2)Rack position bb
----------
aa=20mm bb=1mm
----------
a=16deg+-5deg b=37deg+-5deg
----------
aa=20mm bb=1mm
----------
a=16deg+-5deg b=37deg+-5deg
0000000901
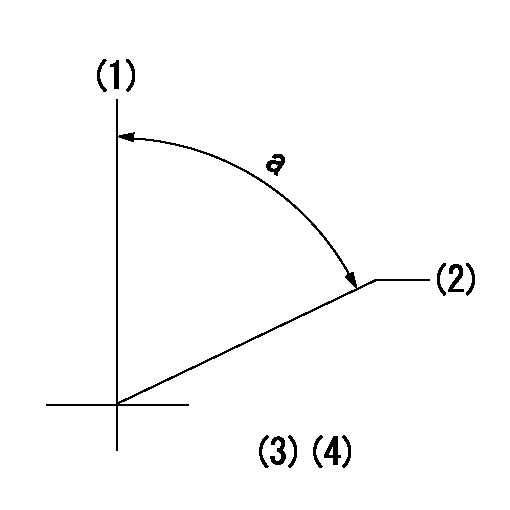
(1)Pump vertical direction
(2)Position of coupling's threaded hole at No 1 cylinder's beginning of injection
(3)B.T.D.C.: aa
(4)Pre-stroke: bb
----------
aa=2deg bb=5.1+-0.03mm
----------
a=(50deg)
----------
aa=2deg bb=5.1+-0.03mm
----------
a=(50deg)
Stop lever angle
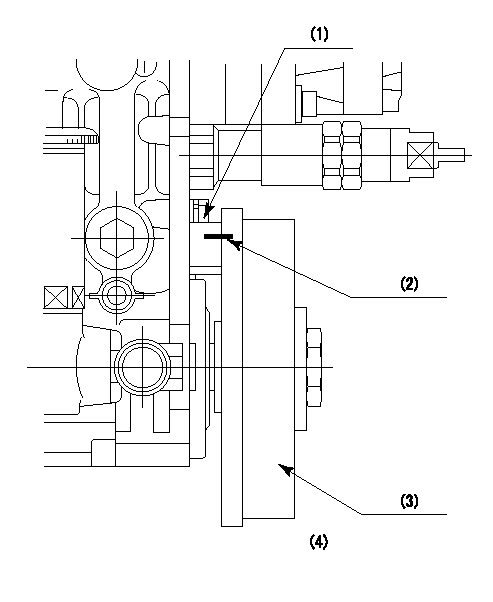
(1)Pointer
(2)Injection timing aligning mark
(3)Fly weight
(4)The actual shape and direction may be different from this illustration.
Operation sequence
1. Turn the prestroke actuator OFF.
2. Turn the camshaft as far as the No.1 cylinder's beginning of injection position.
3. Check that the pointer alignment mark of the injection pump and the alignment mark of the flywheel are matching.
4. If they are not matching, erase the alignment mark on the flywheel side, and stamp an alignment mark on the flywheel position that matches with the pointer side alignment mark.
5. Check again that the coupling's key groove position is in the No.1 cylinder's beginning of injection position.
----------
----------
----------
----------
0000001301
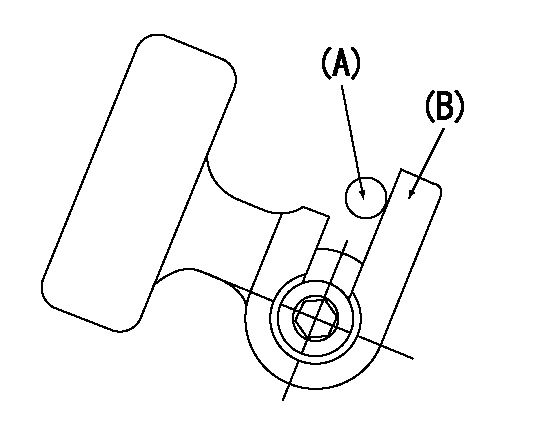
A : Stopper pin
B: Connector
----------
----------
----------
----------
0000001401
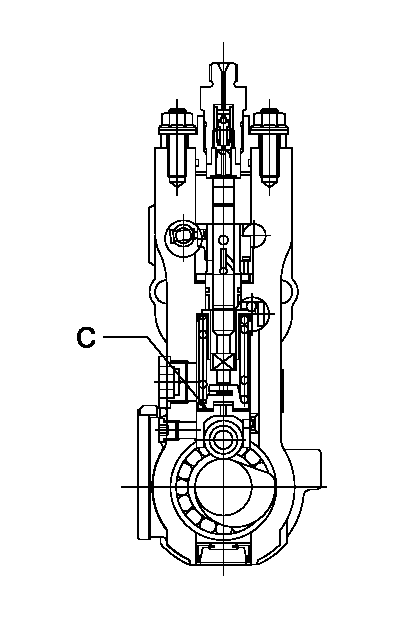
C:Shim
----------
----------
----------
----------
0000001501
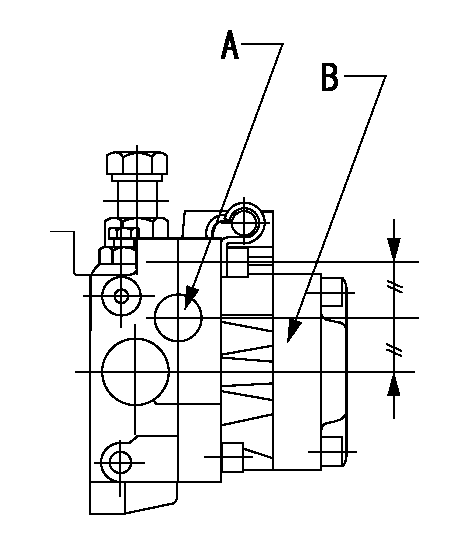
A:Sealing position
B:Pre-stroke actuator
1. When installing the pre-stroke actuator on the pump, first tighten the installation bolts loosely, then move the actuator fully clockwise (viewed from the drive side).
Temporary tightening torque: 1 - 1.5 N.m (0.1 - 0.15 kgf.m)
2. Move the actuator in the counterclockwise direction when viewed from the drive side, and adjust so that it becomes the adjustment point of the adjustment value. Then tighten it.
Tightening torque: 7^9 N.m (0.7^0.9 kgf.m)
3. After prestroke actuator installation adjustment, simultaneously stamp both the actuator side and housing side.
----------
----------
----------
----------
0000001701

(PWM) Pulse width modulation (%)
(R) Rack position (mm)
Rack sensor output characteristics
1. Rack limit adjustment
(1)Measure the rack position R2 for PWM a2%.
(2)Confirm that it is within the range R2 = 15+-1 mm.
(3)Measure the rack position R1 at PWM a %.
(4)Confirm that it is within the range R2 - R1 = 10+-0.1 mm.
2. Check the limp home operation.
(1)Move the switch box's limp home switch to the limp home side.
(2)Confirm rack position L1 (mm ) and L2 (mm) for PWM in the above table.
3. Check the pull down operation.
(1)Confirm that the rack position is 19 mm at PWM B%.
(2)In the conditions described in the above table, move the switch box's pull down switch to the pull down side and confirm that the rack position momentarily becomes 1 mm or less.
----------
a1=16.25% a2=72.5% L1=1--mm L2=19++mm A=5% B=95%
----------
----------
a1=16.25% a2=72.5% L1=1--mm L2=19++mm A=5% B=95%
----------
Information:
Overhaul General
If you elect to perform an in-frame overhaul yourself, without having a Caterpillar dealer perform the overhaul for you or without using an overhaul kit, then you should be aware of the following:Rebuild Or Exchange
Cylinder Head Assembly, Cylinder Packs, Oil Pump and Fuel Transfer PumpYour cylinder head assembly, cylinder packs, oil pump and fuel transfer pump should be inspected according to the instructions found in various Caterpillar reusability publications. Refer to the Index Of Publications On Reusability Or Salvage Of Used Parts section of the Guideline For Reusable Parts and Salvage Operations, form SEBF8029 to determine the reusability publications needed for inspecting your parts.The Guideline For Reusable Parts and Salvage Operations is part of an established Caterpillar parts reusability program. These guidelines were developed to assist Caterpillar dealers and customers reduce costs by avoiding unnecessary expenditures for new parts when existing parts can be used as is, repaired or salvaged. Parts complying with the specifications outlined in the reusable parts guideline will give an additional service life.If your parts comply with the established visual, dimensional, functional, etc., inspection specifications expressed in the reusable parts guideline, then they should be reused.If your parts are not within specification, then they should be salvaged, repaired or replaced. Failure to salvage, repair or replace out-of-spec parts will result in unscheduled downtime and could result in costly repairs caused by potential damage to other engine parts.Furthermore, the use of out-of-spec parts can reduce your engine's efficiency and increase fuel consumption. Reduced engine efficiency and increased fuel consumption translates into higher operating costs. Therefore, Caterpillar recommends that you salvage, repair or replace your out-of-spec parts.Replace
Main and Connecting Rod BearingsIn most probability, your main and connecting rod bearings will not last until your second overhaul. Therefore, Caterpillar recommends the installation of new main and connecting rod bearings at each overhaul period.Inspect
Crankshaft, Camshaft, Camshaft Followers, Damper, Spacer Plate, Fuel Pump Camshaft and Fuel RackThe ideal time for inspecting your crankshaft, camshaft, camshaft followers, damper, spacer plate, fuel pump camshaft and fuel rack is while your engine is disassembled for overhaul. Inspect each component for potential damage as follows: * Crankshaft - Inspect for bend, journal damage and bearing material seized to the journal. At the same time, check the taper and profile of the crankshaft journals by interpreting your main and connecting rod bearing wear patterns. In case of an out-of-frame overhaul, use the magnetic particle inspection process to check the crankshaft for cracks.*
If you elect to perform an in-frame overhaul yourself, without having a Caterpillar dealer perform the overhaul for you or without using an overhaul kit, then you should be aware of the following:Rebuild Or Exchange
Cylinder Head Assembly, Cylinder Packs, Oil Pump and Fuel Transfer PumpYour cylinder head assembly, cylinder packs, oil pump and fuel transfer pump should be inspected according to the instructions found in various Caterpillar reusability publications. Refer to the Index Of Publications On Reusability Or Salvage Of Used Parts section of the Guideline For Reusable Parts and Salvage Operations, form SEBF8029 to determine the reusability publications needed for inspecting your parts.The Guideline For Reusable Parts and Salvage Operations is part of an established Caterpillar parts reusability program. These guidelines were developed to assist Caterpillar dealers and customers reduce costs by avoiding unnecessary expenditures for new parts when existing parts can be used as is, repaired or salvaged. Parts complying with the specifications outlined in the reusable parts guideline will give an additional service life.If your parts comply with the established visual, dimensional, functional, etc., inspection specifications expressed in the reusable parts guideline, then they should be reused.If your parts are not within specification, then they should be salvaged, repaired or replaced. Failure to salvage, repair or replace out-of-spec parts will result in unscheduled downtime and could result in costly repairs caused by potential damage to other engine parts.Furthermore, the use of out-of-spec parts can reduce your engine's efficiency and increase fuel consumption. Reduced engine efficiency and increased fuel consumption translates into higher operating costs. Therefore, Caterpillar recommends that you salvage, repair or replace your out-of-spec parts.Replace
Main and Connecting Rod BearingsIn most probability, your main and connecting rod bearings will not last until your second overhaul. Therefore, Caterpillar recommends the installation of new main and connecting rod bearings at each overhaul period.Inspect
Crankshaft, Camshaft, Camshaft Followers, Damper, Spacer Plate, Fuel Pump Camshaft and Fuel RackThe ideal time for inspecting your crankshaft, camshaft, camshaft followers, damper, spacer plate, fuel pump camshaft and fuel rack is while your engine is disassembled for overhaul. Inspect each component for potential damage as follows: * Crankshaft - Inspect for bend, journal damage and bearing material seized to the journal. At the same time, check the taper and profile of the crankshaft journals by interpreting your main and connecting rod bearing wear patterns. In case of an out-of-frame overhaul, use the magnetic particle inspection process to check the crankshaft for cracks.*