Information injection-pump assembly
BOSCH
F 019 Z10 756
f019z10756
ZEXEL
107692-1570
1076921570
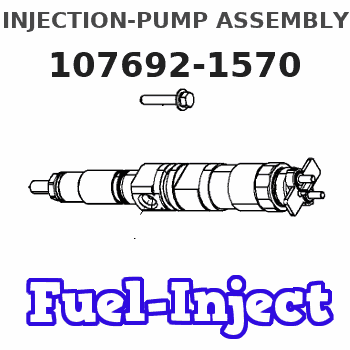
Rating:
Service parts 107692-1570 INJECTION-PUMP ASSEMBLY:
1.
_
5.
AUTOM. ADVANCE MECHANIS
7.
COUPLING PLATE
11.
Nozzle and Holder
12.
Open Pre:MPa(Kqf/cm2)
18.1(185)/22.1(225)
14.
NOZZLE
Include in #1:
107692-1570
as INJECTION-PUMP ASSEMBLY
Cross reference number
BOSCH
F 019 Z10 756
f019z10756
ZEXEL
107692-1570
1076921570
Zexel num
Bosch num
Firm num
Name
Calibration Data:
Adjustment conditions
Test oil
1404 Test oil ISO4113 or {SAEJ967d}
1404 Test oil ISO4113 or {SAEJ967d}
Test oil temperature
degC
40
40
45
Nozzle and nozzle holder
105780-8250
Bosch type code
1 688 901 101
Nozzle
105780-0120
Bosch type code
1 688 901 990
Nozzle holder
105780-2190
Opening pressure
MPa
20.7
Opening pressure
kgf/cm2
211
Injection pipe
Outer diameter - inner diameter - length (mm) mm 8-3-600
Outer diameter - inner diameter - length (mm) mm 8-3-600
Overflow valve
131425-1820
Overflow valve opening pressure
kPa
255
255
255
Overflow valve opening pressure
kgf/cm2
2.6
2.6
2.6
Tester oil delivery pressure
kPa
255
255
255
Tester oil delivery pressure
kgf/cm2
2.6
2.6
2.6
PS/ACT control unit part no.
407980-2
24*
Digi switch no.
17
Direction of rotation (viewed from drive side)
Left L
Left L
Injection timing adjustment
Direction of rotation (viewed from drive side)
Left L
Left L
Injection order
1-5-3-6-
2-4
Pre-stroke
mm
5.1
5.07
5.13
Beginning of injection position
Governor side NO.1
Governor side NO.1
Difference between angles 1
Cal 1-5 deg. 60 59.75 60.25
Cal 1-5 deg. 60 59.75 60.25
Difference between angles 2
Cal 1-3 deg. 120 119.75 120.25
Cal 1-3 deg. 120 119.75 120.25
Difference between angles 3
Cal 1-6 deg. 180 179.75 180.25
Cal 1-6 deg. 180 179.75 180.25
Difference between angles 4
Cyl.1-2 deg. 240 239.75 240.25
Cyl.1-2 deg. 240 239.75 240.25
Difference between angles 5
Cal 1-4 deg. 300 299.75 300.25
Cal 1-4 deg. 300 299.75 300.25
Injection quantity adjustment
Adjusting point
-
Rack position
13.8
Pump speed
r/min
850
850
850
Average injection quantity
mm3/st.
116
114.4
117.6
Max. variation between cylinders
%
0
-2.5
2.5
Basic
*
Fixing the rack
*
PS407980-224*
V
2.25+-0.
01
PS407980-224*
mm
3.1+-0.0
5
Standard for adjustment of the maximum variation between cylinders
*
Injection quantity adjustment_02
Adjusting point
Z
Rack position
8.5+-0.5
Pump speed
r/min
360
360
360
Average injection quantity
mm3/st.
12
10.7
13.3
Max. variation between cylinders
%
0
-14
14
Fixing the rack
*
PS407980-224*
V
V1+0.05+
-0.01
PS407980-224*
mm
5+-0.03
Standard for adjustment of the maximum variation between cylinders
*
Remarks
Refer to items regarding the pre-stroke actuator
Refer to items regarding the pre-stroke actuator
Injection quantity adjustment_03
Adjusting point
A
Rack position
R1(13.8)
Pump speed
r/min
850
850
850
Average injection quantity
mm3/st.
116
115
117
Basic
*
Fixing the lever
*
PS407980-224*
V
2.25+-0.
01
PS407980-224*
mm
3.1+-0.0
5
Injection quantity adjustment_04
Adjusting point
B
Rack position
R1+2.4
Pump speed
r/min
1450
1450
1450
Average injection quantity
mm3/st.
121
111
131
Fixing the lever
*
PS407980-224*
V
2.25+-0.
01
PS407980-224*
mm
3.1+-0.0
5
0000001601
CU407980-224*
*
Actuator retarding type
*
Supply voltage
V
24
23.5
24.5
Ambient temperature
degC
23
18
28
Pre-stroke
mm
2
1.95
2.05
Output voltage
V
2.83
2.82
2.84
Adjustment
*
_02
CU407980-224*
*
Supply voltage
V
24
23.5
24.5
Ambient temperature
degC
23
18
28
Pre-stroke
mm
5.1
5.07
5.13
Output voltage
V
1.2
1
1.4
Confirmation
*
Remarks
Output voltage V1
Output voltage V1
_03
CU407980-224*
*
Supply voltage
V
24
23.5
24.5
Ambient temperature
degC
23
18
28
Output voltage
V
3.05
3.05
Confirmation of operating range
*
Test data Ex:
Governor adjustment
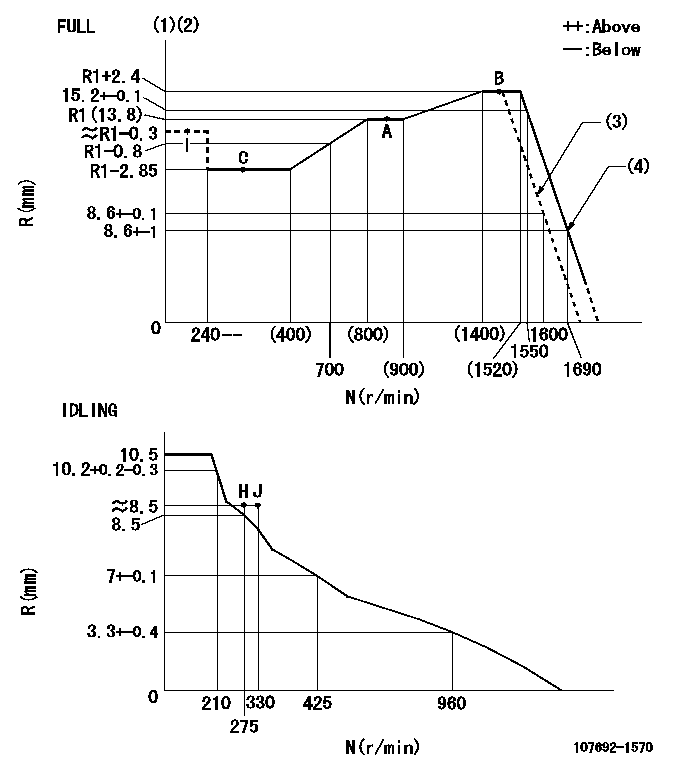
N:Pump speed
R:Rack position (mm)
(1)Torque cam stamping: T1
(2)Tolerance for racks not indicated: +-0.05mm.
(3)Air cylinder ON
(4)Air cylinder OFF
----------
T1=AF71
----------
----------
T1=AF71
----------
Speed control lever angle
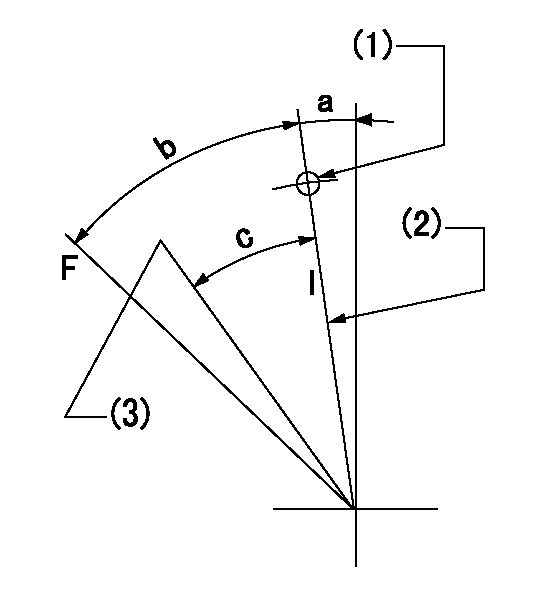
F:Full speed
I:Idle
(1)Use the pin at R = aa
(2)Stopper bolt setting
(3)When air cylinder ON.
----------
aa=35mm
----------
a=14deg+-5deg b=39.5deg+-3deg c=(29deg)
----------
aa=35mm
----------
a=14deg+-5deg b=39.5deg+-3deg c=(29deg)
Stop lever angle
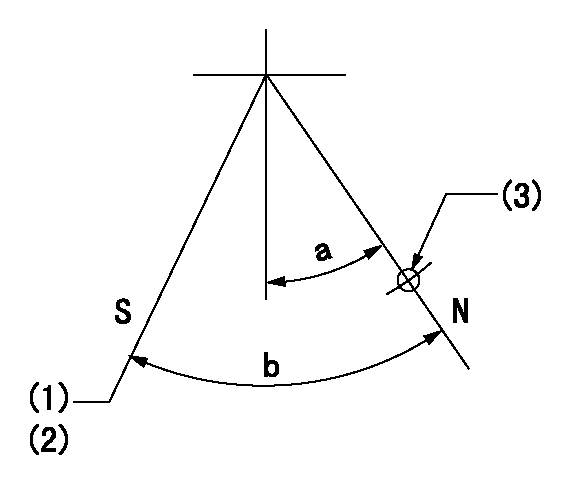
N:Pump normal
S:Stop the pump.
(1)Set the stopper bolt at speed = aa and rack position = bb (non-injection rack position).
(2)-
(3)Use the pin above R = cc
----------
aa=0r/min bb=1.5+-0.3mm cc=40mm
----------
a=12deg+-5deg b=44deg+-5deg
----------
aa=0r/min bb=1.5+-0.3mm cc=40mm
----------
a=12deg+-5deg b=44deg+-5deg
0000001301
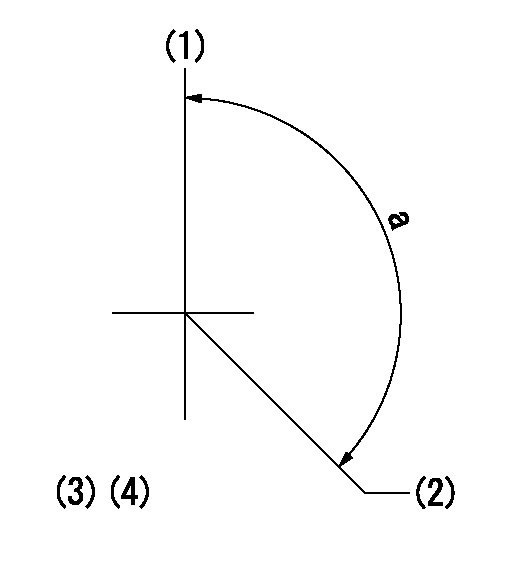
(1)Pump vertical direction
(2)Positions of coupling's threaded installation holes at No 1 cylinder's beginning of injection
(3)B.T.D.C.: aa
(4)Pre-stroke: bb
----------
aa=6deg bb=5.1+-0.03mm
----------
a=(140deg)
----------
aa=6deg bb=5.1+-0.03mm
----------
a=(140deg)
0000001401
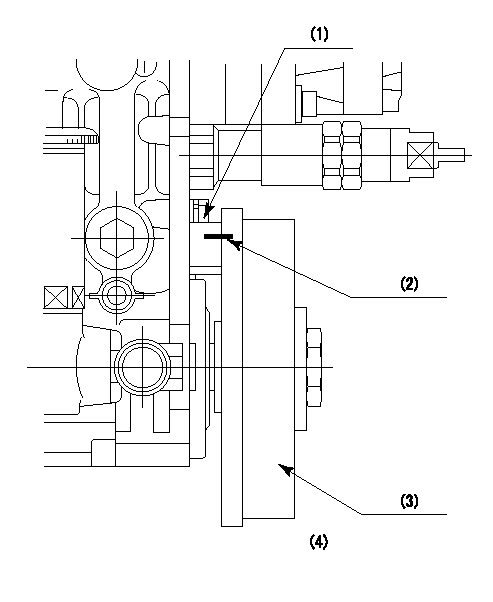
(1)Pointer
(2)Injection timing aligning mark
(3)Fly weight
(4)The actual shape and direction may be different from this illustration.
Operation sequence
1. Turn the prestroke actuator OFF.
2. Turn the camshaft as far as the No.1 cylinder's beginning of injection position.
3. Check that the pointer alignment mark of the injection pump and the alignment mark of the flywheel are matching.
4. If they are not matching, erase the alignment mark on the flywheel side, and stamp an alignment mark on the flywheel position that matches with the pointer side alignment mark.
5. Check again that the coupling's key groove position is in the No.1 cylinder's beginning of injection position.
----------
----------
----------
----------
0000001701
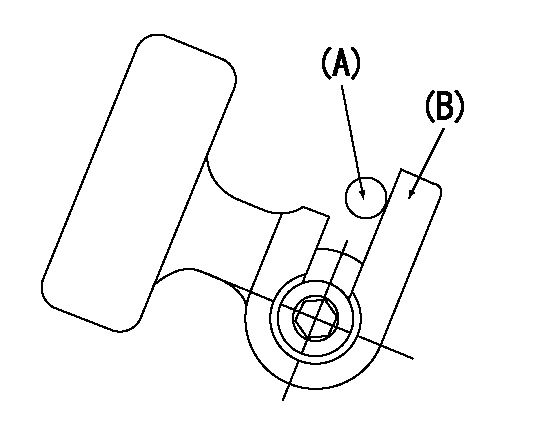
A : Stopper pin
B: Connector
----------
----------
----------
----------
0000001801
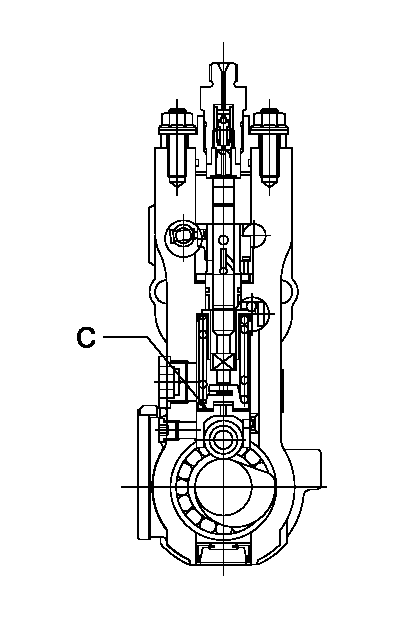
C:Shim
----------
----------
----------
----------
0000001901
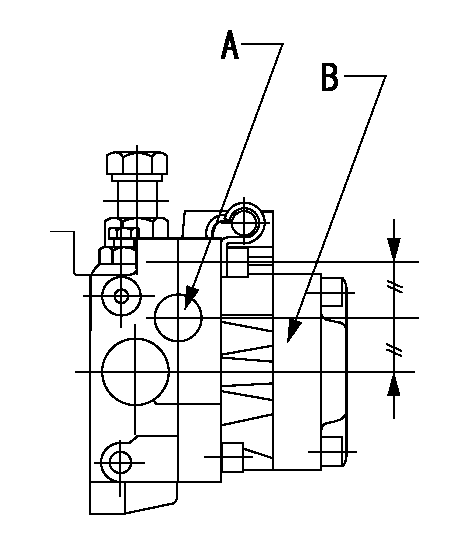
A:Sealing position
B:Pre-stroke actuator
1. When installing the pre-stroke actuator on the pump, first tighten the installation bolts loosely, then move the actuator fully clockwise (viewed from the drive side).
Temporary tightening torque: 1 - 1.5 N.m (0.1 - 0.15 kgf.m)
2. Move the actuator in the counterclockwise direction when viewed from the drive side, and adjust so that it becomes the adjustment point of the adjustment value. Then tighten it.
Tightening torque: 7^9 N.m (0.7^0.9 kgf.m)
3. After prestroke actuator installation adjustment, simultaneously stamp both the actuator side and housing side.
----------
----------
----------
----------
0000002201 RACK SENSOR

G:Red paint
H:Pump end face
P/N: part number of suitable shim
(1)Threaded type rack block
(2)Welded type rack block
Rack sensor adjustment
1. Threaded type rack sensor (-5*20, P type, no TICS rack limit).
(1)Screw in the bobbin (A) until it contacts the joint (B).
(2)Fix the pump lever.
(3)At speed N1 and rack position Ra, adjust the amount that the bobbin is screwed in so that the amp's output voltage is V1.
(4)Fix using the nut (F).
(5)Affix the caution plate to the upper part of the joint (B).
(6)Apply (G) at two places.
Connecting part between the joint (B) and the nut (F)
Connecting part between the end surface of the pump (H) and the joint (B)
2. Range for screw-in adjustment between the bobbin (A) and the joint (B) is 9 threads.
Screw in to the end from (the position where the bobbin (A) is rotated 9 turns).
Speed N1, rack position Ra, output voltage V1, rack sensor supply voltage 5+-0.01 (V)
----------
Ra=R1(13.8)+2.4mm N1=1450r/min V1=3+-0.01V
----------
----------
Ra=R1(13.8)+2.4mm N1=1450r/min V1=3+-0.01V
----------
0000002301 AIR CYLINDER
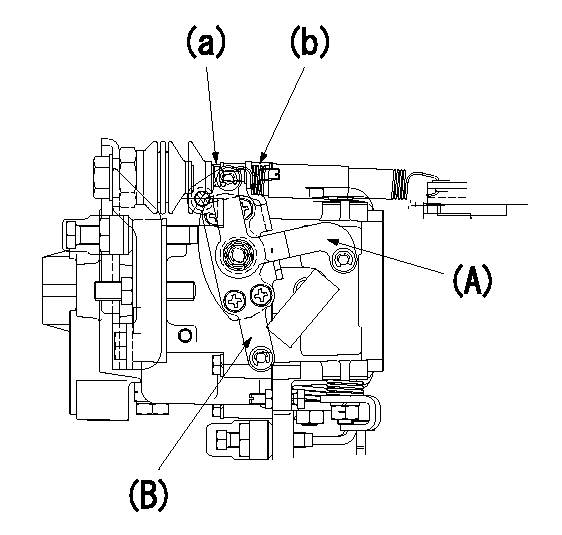
(A): Speed lever
(B): Speed lever
(a): Stopper bolt
(b): Nut
1. Air cylinder adjustment procedure
(1)Apply positive pressure P1 (ON) to the air cylinder.
(2)Operate the speed lever (A). (At this time speed lever (B) also moves together.)
(3)Set the speed lever (B) using the stopper bolt (a) so that rack position is Ra at speed N1. (Speed lever (A) is cancelled at this time.)
(4)Confirm that the speed lever (A)(B) turns to the full position at positive pressure (OFF) P2.
(5)After repeating the above several times, fix the stopper bolt (a) using the nut (b).
----------
P1=294kPa(3kgf/cm2) P2=0kPa(0kgf/cm2) N1=1600r/min Ra=8.6+-0.1mm
----------
----------
P1=294kPa(3kgf/cm2) P2=0kPa(0kgf/cm2) N1=1600r/min Ra=8.6+-0.1mm
----------
Information:
Air-to-air aftercooling systems are simple, reliable and easy to maintain and provide for one or more benefits.* Improved fuel consumption* Lower emissions* Increased powerOperation of ATAAC
Heated compressed air from the engine turbocharger is conveyed to an air-to-air aftercooler that is positioned in front of the engine radiator. The combined effect of the engine fan and ram air moves cooled air through the system to reduce the turbocharged air temperature before it enters the engine intake manifold.Lower intake air temperature allows more air to enter the cylinder, resulting in more complete fuel combustion and reduced exhaust emissions.Air-to-air aftercoolers can achieve charge air temperatures lower than water-to-air systems for additional efficiency.
To maintain an adequate water pump cavitation temperature for efficient water pump performance in an Air-to-Air aftercooled engine, Caterpillar recommends that the coolant mix contain a minimum of 30% Caterpillar Antifreeze, GM-6038M or equivalent. Only use a greater concentration (above 30%) of antifreeze as needed for anticipated outside temperatures.Ethylene glycol raises the boiling point of water.Do not exceed a coolant mixture of 60% ethylene glycol to water since a concentration above 60% ethylene glycol will reduce the engine's freeze protection and increase the possibility of deposit formation in the cooling system.Dowtherm 209 Full-Fill coolant cannot be substituted for ethylene glycol, due to its inability to raise the water pump cavitation temperature. Dowtherm 209 Full-Fill coolant lowers the boiling point of water.
Air Intake System
Never run the engine without an air cleaner installed or with a damaged air cleaner. Dirt will enter the engine and cause premature wear and damage to engine components.Service the air cleaner at regular intervals as determined by the operating environmental dust conditions. Check the air cleaner service indicator (if equipped) daily.As the air cleaner element becomes plugged, the difference of air pressure between the inlet side (dirty side) and the engine side (clean side) will increase. Service the air cleaners regularly or when the air cleaner service indicator diaphragm enters the red zone or the red piston locks in the visible position.Inspect the air intake hoses, elbows and gaskets for cracks or damage, replace as needed. Check for loose clamps, tighten as needed.Check the precleaner (if equipped) daily for accumulation of dust and debris.The Caterpillar air cleaner element may be cleaned up to six times, but must be replaced annually. The element when cleaned, should be thoroughly checked for rips and tears in the filter material and for gasket damage.Winter Fronts
Caterpillar discourages the use of winter fronts or other air flow restriction devices mounted in front of radiators with air-to-air aftercooled engines. Air flow restriction can cause higher exhaust temperatures, power loss, excessive fan usage, a reduction in fuel economy and possible engine damage.If a winter front must be used, then it should have a permanent circular or diamond-shaped opening directly in line with the fan hub and must have a minimum opening dimension of at least 120 sq. in. (770 sq. cm).A centered opening, versus a side or edge winter front opening is specified to provide
Heated compressed air from the engine turbocharger is conveyed to an air-to-air aftercooler that is positioned in front of the engine radiator. The combined effect of the engine fan and ram air moves cooled air through the system to reduce the turbocharged air temperature before it enters the engine intake manifold.Lower intake air temperature allows more air to enter the cylinder, resulting in more complete fuel combustion and reduced exhaust emissions.Air-to-air aftercoolers can achieve charge air temperatures lower than water-to-air systems for additional efficiency.
To maintain an adequate water pump cavitation temperature for efficient water pump performance in an Air-to-Air aftercooled engine, Caterpillar recommends that the coolant mix contain a minimum of 30% Caterpillar Antifreeze, GM-6038M or equivalent. Only use a greater concentration (above 30%) of antifreeze as needed for anticipated outside temperatures.Ethylene glycol raises the boiling point of water.Do not exceed a coolant mixture of 60% ethylene glycol to water since a concentration above 60% ethylene glycol will reduce the engine's freeze protection and increase the possibility of deposit formation in the cooling system.Dowtherm 209 Full-Fill coolant cannot be substituted for ethylene glycol, due to its inability to raise the water pump cavitation temperature. Dowtherm 209 Full-Fill coolant lowers the boiling point of water.
Air Intake System
Never run the engine without an air cleaner installed or with a damaged air cleaner. Dirt will enter the engine and cause premature wear and damage to engine components.Service the air cleaner at regular intervals as determined by the operating environmental dust conditions. Check the air cleaner service indicator (if equipped) daily.As the air cleaner element becomes plugged, the difference of air pressure between the inlet side (dirty side) and the engine side (clean side) will increase. Service the air cleaners regularly or when the air cleaner service indicator diaphragm enters the red zone or the red piston locks in the visible position.Inspect the air intake hoses, elbows and gaskets for cracks or damage, replace as needed. Check for loose clamps, tighten as needed.Check the precleaner (if equipped) daily for accumulation of dust and debris.The Caterpillar air cleaner element may be cleaned up to six times, but must be replaced annually. The element when cleaned, should be thoroughly checked for rips and tears in the filter material and for gasket damage.Winter Fronts
Caterpillar discourages the use of winter fronts or other air flow restriction devices mounted in front of radiators with air-to-air aftercooled engines. Air flow restriction can cause higher exhaust temperatures, power loss, excessive fan usage, a reduction in fuel economy and possible engine damage.If a winter front must be used, then it should have a permanent circular or diamond-shaped opening directly in line with the fan hub and must have a minimum opening dimension of at least 120 sq. in. (770 sq. cm).A centered opening, versus a side or edge winter front opening is specified to provide