Information injection-pump assembly
BOSCH
9 400 619 011
9400619011
ZEXEL
107692-1370
1076921370
ISUZU
8943924390
8943924390

Rating:
Service parts 107692-1370 INJECTION-PUMP ASSEMBLY:
1.
_
5.
AUTOM. ADVANCE MECHANIS
6.
COUPLING PLATE
9.
_
11.
Nozzle and Holder
8-94394-606-5
12.
Open Pre:MPa(Kqf/cm2)
21.6{220}
15.
NOZZLE SET
Include in #1:
107692-1370
as INJECTION-PUMP ASSEMBLY
Cross reference number
BOSCH
9 400 619 011
9400619011
ZEXEL
107692-1370
1076921370
ISUZU
8943924390
8943924390
Zexel num
Bosch num
Firm num
Name
107692-1370
9 400 619 011
8943924390 ISUZU
INJECTION-PUMP ASSEMBLY
6HE1-TC K 14CG INJECTION PUMP ASSY TICS MD-TI6 TICS
6HE1-TC K 14CG INJECTION PUMP ASSY TICS MD-TI6 TICS
Calibration Data:
Adjustment conditions
Test oil
1404 Test oil ISO4113 or {SAEJ967d}
1404 Test oil ISO4113 or {SAEJ967d}
Test oil temperature
degC
40
40
45
Nozzle and nozzle holder
105780-8250
Bosch type code
1 688 901 101
Nozzle
105780-0120
Bosch type code
1 688 901 990
Nozzle holder
105780-2190
Opening pressure
MPa
20.7
Opening pressure
kgf/cm2
211
Injection pipe
Outer diameter - inner diameter - length (mm) mm 8-3-600
Outer diameter - inner diameter - length (mm) mm 8-3-600
Overflow valve
131425-0520
Overflow valve opening pressure
kPa
255
221
289
Overflow valve opening pressure
kgf/cm2
2.6
2.25
2.95
Tester oil delivery pressure
kPa
255
255
255
Tester oil delivery pressure
kgf/cm2
2.6
2.6
2.6
PS/ACT control unit part no.
407980-2
24*
Digi switch no.
13
Direction of rotation (viewed from drive side)
Left L
Left L
Injection timing adjustment
Direction of rotation (viewed from drive side)
Left L
Left L
Injection order
1-5-3-6-
2-4
Pre-stroke
mm
1.9
1.87
1.93
Beginning of injection position
Governor side NO.1
Governor side NO.1
Difference between angles 1
Cal 1-5 deg. 60 59.75 60.25
Cal 1-5 deg. 60 59.75 60.25
Difference between angles 2
Cal 1-3 deg. 120 119.75 120.25
Cal 1-3 deg. 120 119.75 120.25
Difference between angles 3
Cal 1-6 deg. 180 179.75 180.25
Cal 1-6 deg. 180 179.75 180.25
Difference between angles 4
Cyl.1-2 deg. 240 239.75 240.25
Cyl.1-2 deg. 240 239.75 240.25
Difference between angles 5
Cal 1-4 deg. 300 299.75 300.25
Cal 1-4 deg. 300 299.75 300.25
Injection quantity adjustment
Adjusting point
-
Rack position
14.4
Pump speed
r/min
750
750
750
Average injection quantity
mm3/st.
120
118.4
121.6
Max. variation between cylinders
%
0
-2.5
2.5
Basic
*
Fixing the rack
*
PS407980-224*
V
1.88+-0.
01
PS407980-224*
mm
3.1+-0.0
5
Standard for adjustment of the maximum variation between cylinders
*
Injection quantity adjustment_02
Adjusting point
Z
Rack position
9+-0.5
Pump speed
r/min
425
425
425
Average injection quantity
mm3/st.
19
17.7
20.3
Max. variation between cylinders
%
0
-14
14
Fixing the rack
*
PS407980-224*
V
2.83+-0.
01
PS407980-224*
mm
5+-0.03
Standard for adjustment of the maximum variation between cylinders
*
Injection quantity adjustment_03
Adjusting point
A
Rack position
R1(14.4)
Pump speed
r/min
750
750
750
Average injection quantity
mm3/st.
120
119
121
Basic
*
Fixing the lever
*
Boost pressure
kPa
61.3
61.3
Boost pressure
mmHg
460
460
PS407980-224*
V
1.88+-0.
01
PS407980-224*
mm
3.1+-0.0
5
Boost compensator adjustment
Pump speed
r/min
300
300
300
Rack position
R2-2.7
Boost pressure
kPa
17.3
16
18.6
Boost pressure
mmHg
130
120
140
Boost compensator adjustment_02
Pump speed
r/min
300
300
300
Rack position
R2(R1-0.
55)
Boost pressure
kPa
48
48
48
Boost pressure
mmHg
360
360
360
0000001601
CU407980-224*
*
Actuator advancing type
*
Supply voltage
V
24
23.5
24.5
Ambient temperature
degC
23
18
28
Pre-stroke
mm
5
4.95
5.05
Output voltage
V
2.83
2.82
2.84
Adjustment
*
_02
CU407980-224*
*
Supply voltage
V
24
23.5
24.5
Ambient temperature
degC
23
18
28
Pre-stroke
mm
1.9
1.87
1.93
Output voltage
V
1.2
1
1.4
Confirmation
*
_03
CU407980-224*
*
Supply voltage
V
24
23.5
24.5
Ambient temperature
degC
23
18
28
Output voltage
V
3.05
3.05
Confirmation of operating range
*
Test data Ex:
Governor adjustment
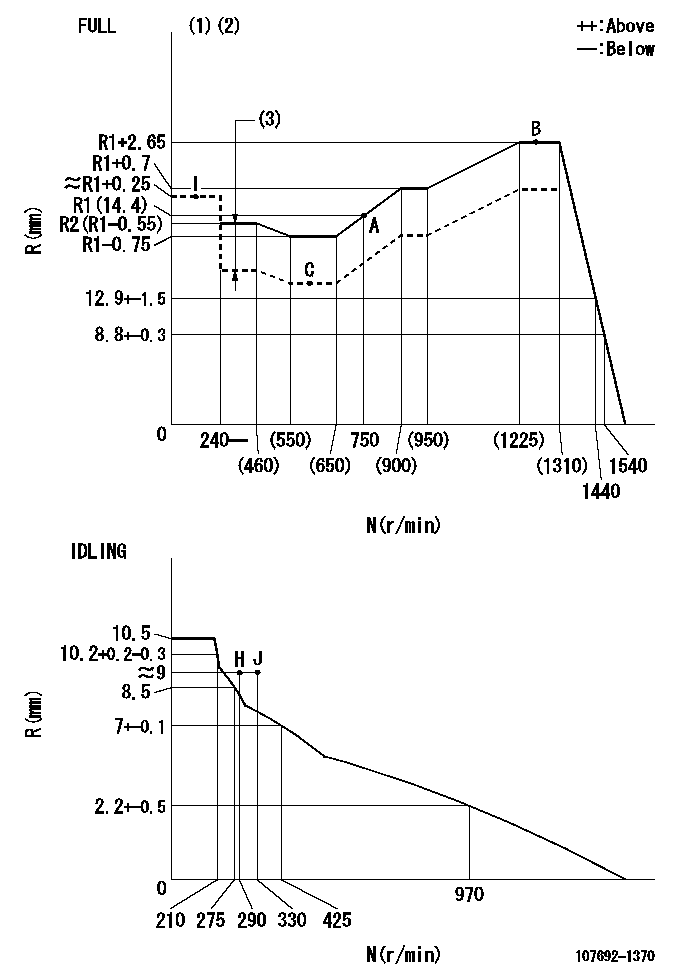
N:Pump speed
R:Rack position (mm)
(1)Torque cam stamping: T1
(2)Tolerance for racks not indicated: +-0.05mm.
(3)Boost compensator stroke: BCL
----------
T1=AB47 BCL=2.7+-0.1mm
----------
----------
T1=AB47 BCL=2.7+-0.1mm
----------
Speed control lever angle
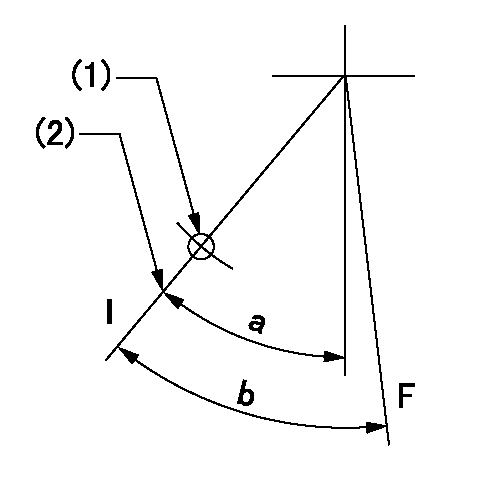
F:Full speed
I:Idle
(1)Use the hole at R = aa
(2)Stopper bolt set position 'H'
----------
aa=35mm
----------
a=31.5deg+-5deg b=32.5deg+-3deg
----------
aa=35mm
----------
a=31.5deg+-5deg b=32.5deg+-3deg
Stop lever angle
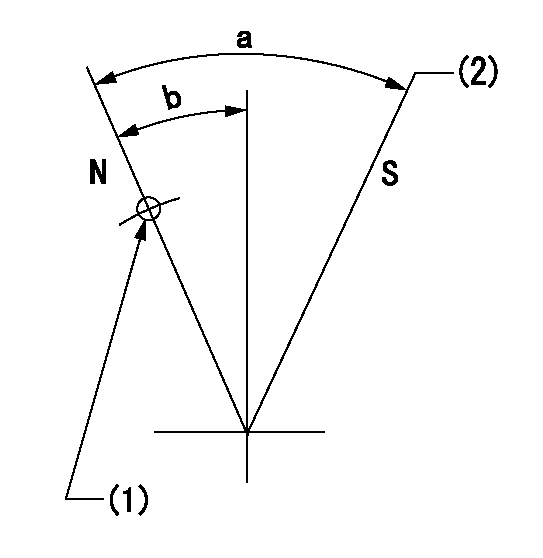
N:Pump normal
S:Stop the pump.
(1)Use the pin at R = aa
(2)Set the stopper bolt at speed = bb and rack position = cc (non-injection rack position). Confirm non-injection.
----------
aa=40mm bb=0r/min cc=1.5+-0.3mm
----------
a=44deg+-5deg b=12deg+-5deg
----------
aa=40mm bb=0r/min cc=1.5+-0.3mm
----------
a=44deg+-5deg b=12deg+-5deg
0000001301
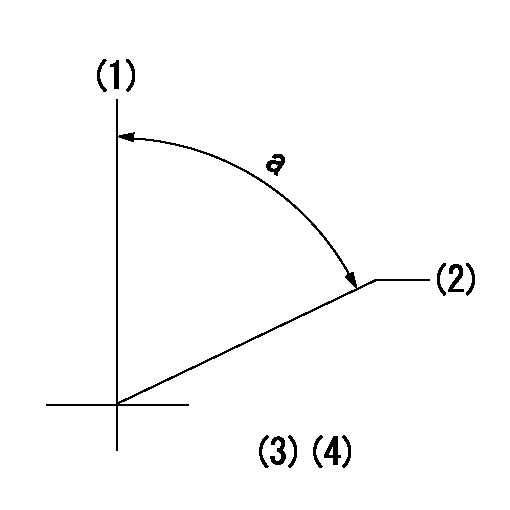
(1)Pump vertical direction
(2)Position of flywheel's threaded hole at No 1 cylinder's beginning of injection
(3)B.T.D.C.: aa
(4)Pre-stroke: bb
----------
aa=19deg bb=1.9+-0.03mm
----------
a=(60deg)
----------
aa=19deg bb=1.9+-0.03mm
----------
a=(60deg)
0000001401
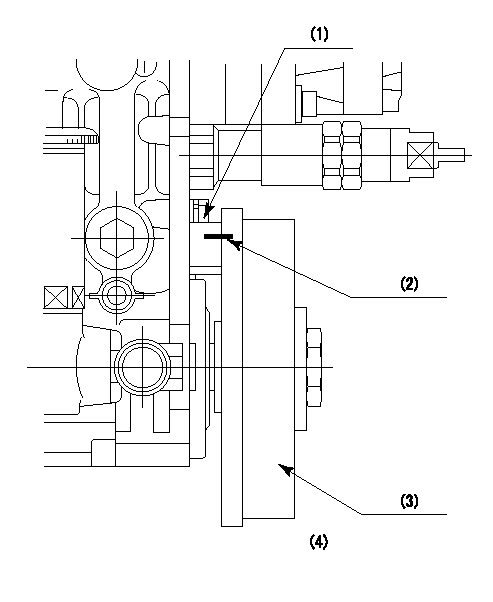
(1)Pointer
(2)Injection timing aligning mark
(3)Fly weight
(4)The actual shape and direction may be different from this illustration.
Operation sequence
1. Turn the prestroke actuator OFF.
2. Turn the camshaft as far as the No.1 cylinder's beginning of injection position.
3. Check that the pointer alignment mark of the injection pump and the alignment mark of the flywheel are matching.
4. If they are not matching, erase the alignment mark on the flywheel side, and stamp an alignment mark on the flywheel position that matches with the pointer side alignment mark.
5. Check again that the coupling's key groove position is in the No.1 cylinder's beginning of injection position.
----------
----------
----------
----------
0000001701
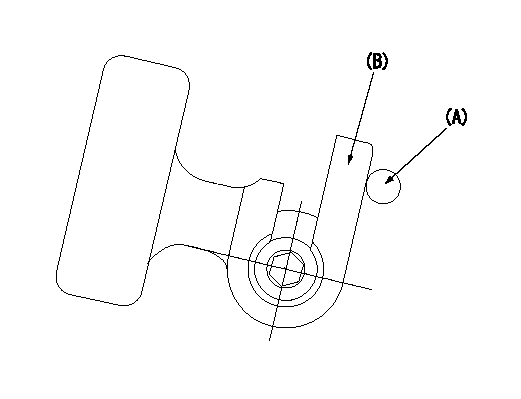
A : Stopper pin
B: Connector
----------
----------
----------
----------
0000001801
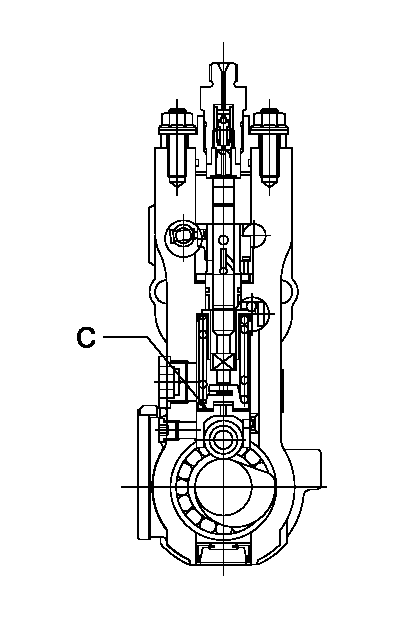
C:Shim
----------
----------
----------
----------
0000001901
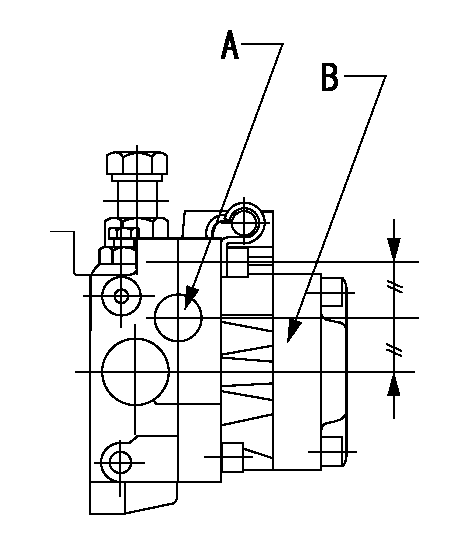
A:Sealing position
B:Pre-stroke actuator
1. When installing the pre-stroke actuator on the pump, first tighten the installation bolts loosely, then move the actuator fully clockwise (viewed from the drive side).
Temporary tightening torque: 1 - 1.5 N.m (0.1 - 0.15 kgf.m)
2. Move the actuator in the counterclockwise direction when viewed from the drive side, and adjust so that it becomes the adjustment point of the adjustment value. Then tighten it.
Tightening torque: 7^9 N.m (0.7^0.9 kgf.m)
3. After prestroke actuator installation adjustment, simultaneously stamp both the actuator side and housing side.
----------
----------
----------
----------
0000002201 RACK SENSOR

G:Red paint
H:Pump end face
P/N: part number of suitable shim
(1)Threaded type rack block
(2)Welded type rack block
Rack sensor adjustment
1. Threaded type rack sensor (-5*20, P type, no TICS rack limit).
(1)Screw in the bobbin (A) until it contacts the joint (B).
(2)Fix the pump lever.
(3)At speed N1 and rack position Ra, adjust the amount that the bobbin is screwed in so that the amp's output voltage is V1.
(4)Fix using the nut (F).
(5)Affix the caution plate to the upper part of the joint (B).
(6)Apply (G) at two places.
Connecting part between the joint (B) and the nut (F)
Connecting part between the end surface of the pump (H) and the joint (B)
2. Range for screw-in adjustment between the bobbin (A) and the joint (B) is 9 threads.
Screw in to the end from (the position where the bobbin (A) is rotated 9 turns).
Speed N1, rack position Ra, output voltage V1, rack sensor supply voltage 5+-0.01 (V)
----------
Ra=R1(14.4)+2.65mm N1=1250r/min V1=3+-0.01V
----------
----------
Ra=R1(14.4)+2.65mm N1=1250r/min V1=3+-0.01V
----------
Information:
Self-Diagnostics
The 3176 Truck Engine has a limited ability to diagnose itself. When the System detects a problem, a Diagnostic Code is generated which activates the Diagnostic Lamp. In most cases the code will be stored in permanent memory in the ECM.Diagnostic Codes that represent current faults are called ACTIVE and indicate that a problem exists. These active diagnostic codes should be investigated first.Diagnostic Codes stores in memory are called LOGGED. The problem may have been temporary or repaired since the time it was LOGGED. These codes may not mean something needs to be repaired, but may be helpful indicators when INTERMITTENT problems exist, which could be used to troubleshoot and analyze potential problems. In addition, some logged diagnostic codes record events and performance history, rather than failures.Diagnostic Codes-Interpretation
When the vehicle is equipped with Cruise Control (CC)
1. Turn ignition key ON (engine does not need to be started to view codes).2. The Diagnostic Lamp will illuminate for five seconds, blink off, turn on again for five seconds, then off for five seconds. The lamp will then begin to flash the first number of the two-digit code (count the flashes). The lamp will blink off for two seconds, then begin to flash the second number of the two-digit code in the same manner as the first. If more than one code is present, they will follow the first code after a few seconds and be displayed in the same manner.3. Active diagnostic codes may be displayed at any time by using the Cruise Control (CC) Switches. The engine can be running or the ignition key ON. Turn the Cruise Control ON/OFF switch to OFF and move the SET/RESUME switch to RESUME position. The Check Engine Light will flash to indicate a 2-digit fault code and the switch may be released from the RESUME position.When the vehicle is NOT equipped with Cruise Control (CC):
Some trucks are equipped with a Check Engine Light Switch to check diagnostic codes. The Check Engine Light can be used to communicate the specific 3176 system diagnostic fault. The Check Engine light will flash to indicate the 2-digit diagnostic fault code. This can be done by connecting a push button momentary switch from position H of connector P7 thru the momentary switch and back to position B of connector P7.With the switch depressed, the "Check Engine" light will begin to flash. The sequence of flashes represents the 3176 system diagnostic message.The first sequence of flashes adds up to the first digit of the diagnostic code. After a two second pause, a second sequence of flashes will occur which represents the second digit of the diagnostic code. Any additional codes will follow and will be displayed in the same manner.Refer to 3176 Truck Engine Test Procedures, Form SENR5112 and the Service Manual for troubleshooting the 3176 System. For further information or assistance for repairs, contact an authorized Caterpillar dealer.Some trucks have electronic dashboards that provide a direct readout of 3176 engine diagnostic codes. Follow the truck manufacturer's instructions
The 3176 Truck Engine has a limited ability to diagnose itself. When the System detects a problem, a Diagnostic Code is generated which activates the Diagnostic Lamp. In most cases the code will be stored in permanent memory in the ECM.Diagnostic Codes that represent current faults are called ACTIVE and indicate that a problem exists. These active diagnostic codes should be investigated first.Diagnostic Codes stores in memory are called LOGGED. The problem may have been temporary or repaired since the time it was LOGGED. These codes may not mean something needs to be repaired, but may be helpful indicators when INTERMITTENT problems exist, which could be used to troubleshoot and analyze potential problems. In addition, some logged diagnostic codes record events and performance history, rather than failures.Diagnostic Codes-Interpretation
When the vehicle is equipped with Cruise Control (CC)
1. Turn ignition key ON (engine does not need to be started to view codes).2. The Diagnostic Lamp will illuminate for five seconds, blink off, turn on again for five seconds, then off for five seconds. The lamp will then begin to flash the first number of the two-digit code (count the flashes). The lamp will blink off for two seconds, then begin to flash the second number of the two-digit code in the same manner as the first. If more than one code is present, they will follow the first code after a few seconds and be displayed in the same manner.3. Active diagnostic codes may be displayed at any time by using the Cruise Control (CC) Switches. The engine can be running or the ignition key ON. Turn the Cruise Control ON/OFF switch to OFF and move the SET/RESUME switch to RESUME position. The Check Engine Light will flash to indicate a 2-digit fault code and the switch may be released from the RESUME position.When the vehicle is NOT equipped with Cruise Control (CC):
Some trucks are equipped with a Check Engine Light Switch to check diagnostic codes. The Check Engine Light can be used to communicate the specific 3176 system diagnostic fault. The Check Engine light will flash to indicate the 2-digit diagnostic fault code. This can be done by connecting a push button momentary switch from position H of connector P7 thru the momentary switch and back to position B of connector P7.With the switch depressed, the "Check Engine" light will begin to flash. The sequence of flashes represents the 3176 system diagnostic message.The first sequence of flashes adds up to the first digit of the diagnostic code. After a two second pause, a second sequence of flashes will occur which represents the second digit of the diagnostic code. Any additional codes will follow and will be displayed in the same manner.Refer to 3176 Truck Engine Test Procedures, Form SENR5112 and the Service Manual for troubleshooting the 3176 System. For further information or assistance for repairs, contact an authorized Caterpillar dealer.Some trucks have electronic dashboards that provide a direct readout of 3176 engine diagnostic codes. Follow the truck manufacturer's instructions
Have questions with 107692-1370?
Group cross 107692-1370 ZEXEL
Isuzu
Isuzu
Isuzu
Isuzu
107692-1370
9 400 619 011
8943924390
INJECTION-PUMP ASSEMBLY
6HE1-TC
6HE1-TC