Information injection-pump assembly
BOSCH
9 400 612 794
9400612794
ZEXEL
107692-1190
1076921190
ISUZU
1156029470
1156029470
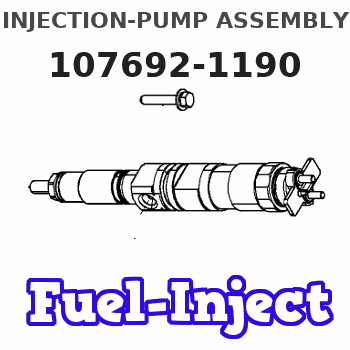
Rating:
Service parts 107692-1190 INJECTION-PUMP ASSEMBLY:
1.
_
5.
AUTOM. ADVANCE MECHANIS
9.
_
11.
Nozzle and Holder
1-15300-274-6
12.
Open Pre:MPa(Kqf/cm2)
19.6{200}
15.
NOZZLE SET
Include in #1:
107692-1190
as INJECTION-PUMP ASSEMBLY
Cross reference number
BOSCH
9 400 612 794
9400612794
ZEXEL
107692-1190
1076921190
ISUZU
1156029470
1156029470
Zexel num
Bosch num
Firm num
Name
107692-1190
9 400 612 794
1156029470 ISUZU
INJECTION-PUMP ASSEMBLY
6BG1-TC1 K 14CG INJECTION PUMP ASSY TICS MD-TI6 TICS
6BG1-TC1 K 14CG INJECTION PUMP ASSY TICS MD-TI6 TICS
Calibration Data:
Adjustment conditions
Test oil
1404 Test oil ISO4113 or {SAEJ967d}
1404 Test oil ISO4113 or {SAEJ967d}
Test oil temperature
degC
40
40
45
Nozzle and nozzle holder
105780-8140
Bosch type code
EF8511/9A
Nozzle
105780-0000
Bosch type code
DN12SD12T
Nozzle holder
105780-2080
Bosch type code
EF8511/9
Opening pressure
MPa
17.2
Opening pressure
kgf/cm2
175
Injection pipe
Outer diameter - inner diameter - length (mm) mm 8-3-600
Outer diameter - inner diameter - length (mm) mm 8-3-600
Overflow valve
131425-0520
Overflow valve opening pressure
kPa
255
221
289
Overflow valve opening pressure
kgf/cm2
2.6
2.25
2.95
Tester oil delivery pressure
kPa
157
157
157
Tester oil delivery pressure
kgf/cm2
1.6
1.6
1.6
PS/ACT control unit part no.
407910-3
03*
Selector switch no.
00
PS/ACT control unit part no.
407980-2
24*
Digi switch no.
11
Direction of rotation (viewed from drive side)
Right R
Right R
Injection timing adjustment
Direction of rotation (viewed from drive side)
Right R
Right R
Injection order
1-5-3-6-
2-4
Pre-stroke
mm
2.3
2.27
2.33
Beginning of injection position
Drive side NO.1
Drive side NO.1
Difference between angles 1
Cal 1-5 deg. 60 59.75 60.25
Cal 1-5 deg. 60 59.75 60.25
Difference between angles 2
Cal 1-3 deg. 120 119.75 120.25
Cal 1-3 deg. 120 119.75 120.25
Difference between angles 3
Cal 1-6 deg. 180 179.75 180.25
Cal 1-6 deg. 180 179.75 180.25
Difference between angles 4
Cyl.1-2 deg. 240 239.75 240.25
Cyl.1-2 deg. 240 239.75 240.25
Difference between angles 5
Cal 1-4 deg. 300 299.75 300.25
Cal 1-4 deg. 300 299.75 300.25
Injection quantity adjustment
Adjusting point
-
Rack position
12
Pump speed
r/min
975
975
975
Average injection quantity
mm3/st.
87.2
85.6
88.8
Max. variation between cylinders
%
0
-2.5
2.5
Basic
*
Fixing the rack
*
PS407980-224*
V
1.88+-0.
01
PS407980-224*
mm
3.6+-0.0
3
PS407910-303*
V
1.88+-0.
01
PS407910-303*
mm
3.6+-0.0
3
Standard for adjustment of the maximum variation between cylinders
*
Injection quantity adjustment_02
Adjusting point
Z
Rack position
8.1+-0.5
Pump speed
r/min
660
660
660
Average injection quantity
mm3/st.
12.5
11.2
13.8
Max. variation between cylinders
%
0
-14
14
Fixing the rack
*
PS407980-224*
V
1.88+-0.
01
PS407980-224*
mm
3.6+-0.0
3
PS407910-303*
V
1.88+-0.
01
PS407910-303*
mm
3.6+-0.0
3
Standard for adjustment of the maximum variation between cylinders
*
Injection quantity adjustment_03
Adjusting point
A
Rack position
R1(12)
Pump speed
r/min
975
975
975
Average injection quantity
mm3/st.
87.2
86.2
88.2
Basic
*
Fixing the lever
*
Boost pressure
kPa
46.7
46.7
Boost pressure
mmHg
350
350
PS407980-224*
V
1.88+-0.
01
PS407980-224*
mm
3.6+-0.0
3
PS407910-303*
V
1.88+-0.
01
PS407910-303*
mm
3.6+-0.0
3
Boost compensator adjustment
Pump speed
r/min
600
600
600
Rack position
R2-1.6
Boost pressure
kPa
10.7
10.7
10.7
Boost pressure
mmHg
80
80
80
Boost compensator adjustment_02
Pump speed
r/min
600
600
600
Rack position
R2-0.8
Boost pressure
kPa
21.3
20
22.6
Boost pressure
mmHg
160
150
170
Boost compensator adjustment_03
Pump speed
r/min
600
600
600
Rack position
R2(R1-0.
85)
Boost pressure
kPa
33.3
26.6
40
Boost pressure
mmHg
250
200
300
0000001601
CU407980-224*
*
Actuator advancing type
*
Supply voltage
V
12
11.5
12.5
Ambient temperature
degC
23
18
28
Pre-stroke
mm
5.4
5.35
5.45
Output voltage
V
2.83
2.82
2.84
Adjustment
*
_02
CU407980-224*
*
Supply voltage
V
12
11.5
12.5
Ambient temperature
degC
23
18
28
Pre-stroke
mm
2.3
2.27
2.33
Output voltage
V
1.2
1
1.4
Confirmation
*
_03
CU407980-224*
*
Supply voltage
V
12
11.5
12.5
Ambient temperature
degC
23
18
28
Output voltage
V
3.05
3.05
Confirmation of operating range
*
_04
CU407910-303*
*
Actuator advancing type
*
Supply voltage
V
12
11.5
12.5
Ambient temperature
degC
23
18
28
Pre-stroke
mm
5.4
5.35
5.45
Output voltage
V
2.83
2.82
2.84
Adjustment
*
_05
CU407910-303*
*
Supply voltage
V
12
11.5
12.5
Ambient temperature
degC
23
18
28
Pre-stroke
mm
2.3
2.27
2.33
Output voltage
V
1.2
1
1.4
Confirmation
*
_06
CU407910-303*
*
Supply voltage
V
12
11.5
12.5
Ambient temperature
degC
23
18
28
Output voltage
V
3.05
3.05
Confirmation of operating range
*
Test data Ex:
Governor adjustment
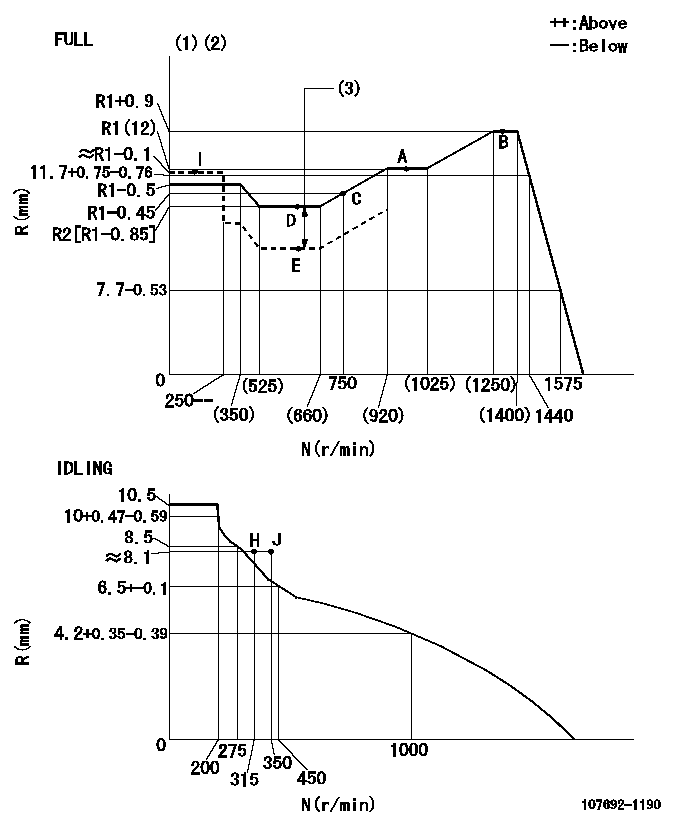
N:Pump speed
R:Rack position (mm)
(1)Torque cam stamping: T1
(2)Tolerance for racks not indicated: +-0.05mm.
(3)Boost compensator stroke: BCL
----------
T1=G47 BCL=1.6+-0.1mm
----------
----------
T1=G47 BCL=1.6+-0.1mm
----------
Speed control lever angle

F:Full speed
I:Idle
(1)Use the pin at R = aa
(2)Stopper bolt setting
----------
aa=35mm
----------
a=43deg+-5deg b=38deg+-3deg
----------
aa=35mm
----------
a=43deg+-5deg b=38deg+-3deg
Stop lever angle

N:Pump normal
S:Stop the pump.
(1)-
(2)Set the stopper bolt at speed = aa and rack position = bb and confirm non-injection.
----------
aa=1300r/min bb=5-0.5mm
----------
a=20deg+-5deg b=37deg+-5deg
----------
aa=1300r/min bb=5-0.5mm
----------
a=20deg+-5deg b=37deg+-5deg
0000001301
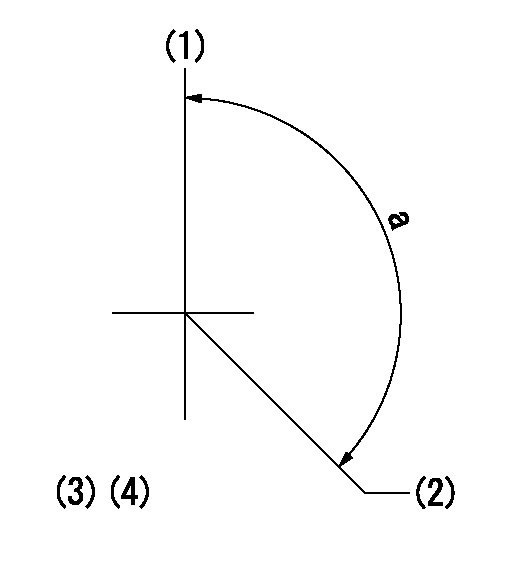
(1)Pump vertical direction
(2)Position of flywheel's threaded hole at No 1 cylinder's beginning of injection
(3)Pre-stroke: aa
(4)-
----------
aa=2.3+-0.03mm
----------
a=(140deg)
----------
aa=2.3+-0.03mm
----------
a=(140deg)
0000001401
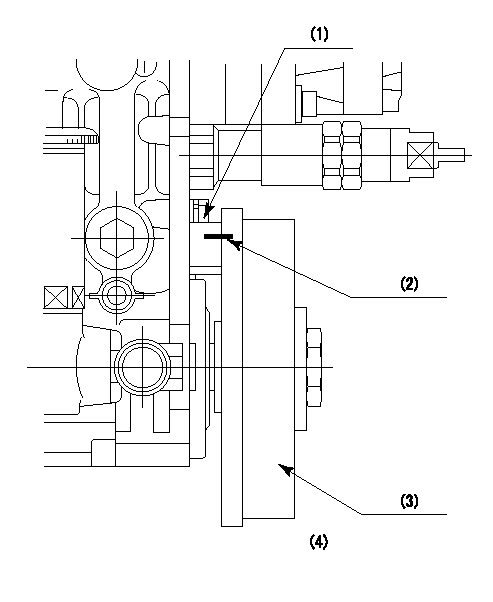
(1)Pointer
(2)Injection timing aligning mark
(3)Fly weight
(4)The actual shape and direction may be different from this illustration.
Operation sequence
1. Turn the prestroke actuator OFF.
2. Turn the camshaft as far as the No.1 cylinder's beginning of injection position.
3. Check that the pointer alignment mark of the injection pump and the alignment mark of the flywheel are matching.
4. If they are not matching, erase the alignment mark on the flywheel side, and stamp an alignment mark on the flywheel position that matches with the pointer side alignment mark.
5. Check again that the coupling's key groove position is in the No.1 cylinder's beginning of injection position.
----------
----------
----------
----------
0000001701
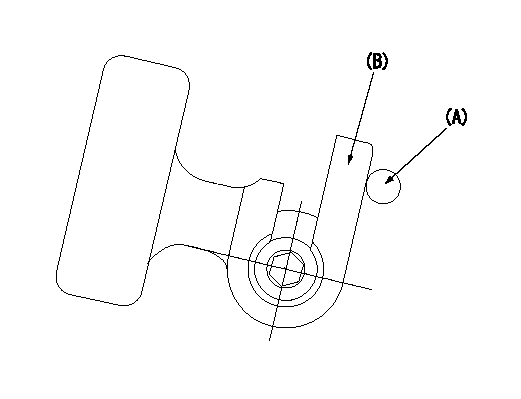
A : Stopper pin
B: Connector
----------
----------
----------
----------
0000001801
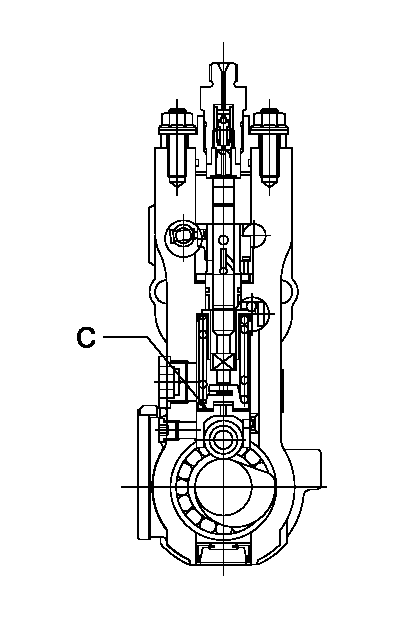
C:Shim
----------
----------
----------
----------
0000001901
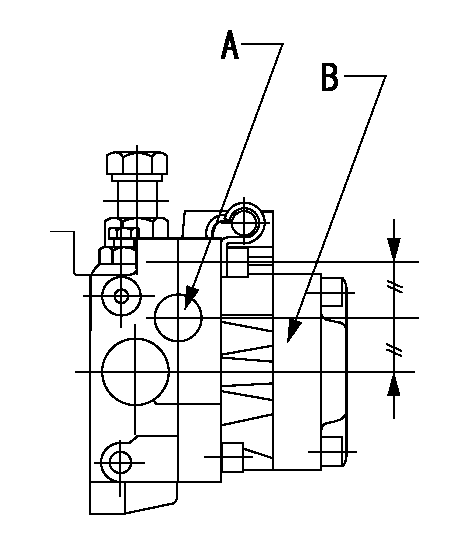
A:Sealing position
B:Pre-stroke actuator
1. When installing the pre-stroke actuator on the pump, first tighten the installation bolts loosely, then move the actuator fully clockwise (viewed from the drive side).
Temporary tightening torque: 1 - 1.5 N.m (0.1 - 0.15 kgf.m)
2. Move the actuator in the counterclockwise direction when viewed from the drive side, and adjust so that it becomes the adjustment point of the adjustment value. Then tighten it.
Tightening torque: 7^9 N.m (0.7^0.9 kgf.m)
3. After prestroke actuator installation adjustment, simultaneously stamp both the actuator side and housing side.
----------
----------
----------
----------
0000002201 RACK SENSOR
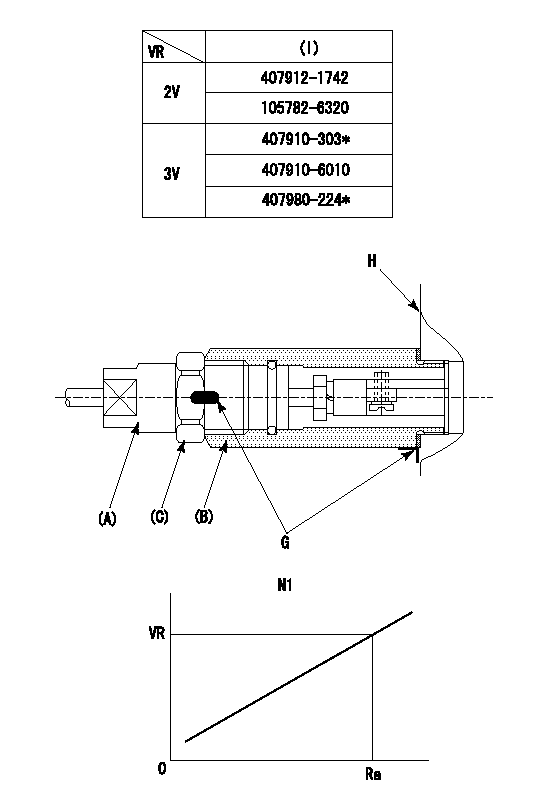
(VR) measurement voltage
(I) Part number of the control unit
(G) Apply red paint.
(H): End surface of the pump
1. Rack sensor adjustment (-0620)
(1)Fix the speed control lever at the full position
(2)Set the speed to N1 r/min.
(If the boost compensator is provided, apply boost pressure.)
(3)Adjust the bobbin (A) so that the rack sensor's output voltage is VR+-0.01.
(4)At that time, rack position must be Ra.
(5)Apply G at two places.
Connecting part between the joint (B) and the nut (F)
Connecting part between the joint (B) and the end surface of the pump (H)
----------
N1=1300r/min Ra=R1(12)+0.9mm
----------
----------
N1=1300r/min Ra=R1(12)+0.9mm
----------
0000002301 BCS
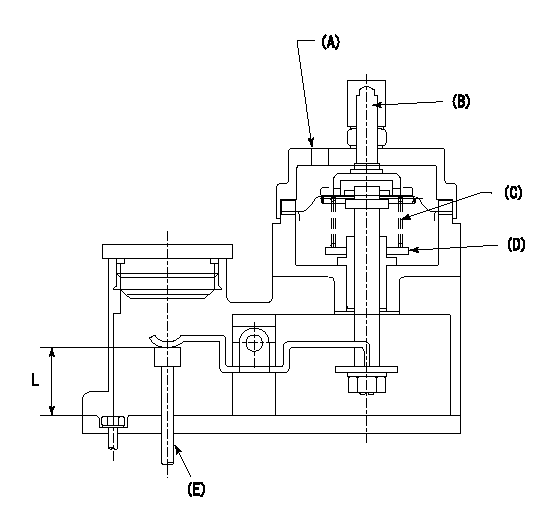
(A) Boost pressure inlet
(B) Screw for rack position adjustment
(C): boost compensator spring
(D): spring setting adjusting notch
(E): Push rod
1. Instructions for adjusting the boost compensator
(1)Select a pushrod to obtain dimension L at full boost.
(2)(B) Adjust the boost compensator stroke with the screw.
(3)(D) Move the adjusting nut to adjust the start of boost compensator operation.
----------
L=24+-0.5mm
----------
----------
L=24+-0.5mm
----------
Information:
Proper operation and maintenance are key factors in determining the useful life and economy of a truck engine. Follow the directions in this guide for trouble-free, economical truck engine operation. After the engine starts, reduce engine RPM to low idle with no load.(1674 and 1693: Before normal oil pressure is reached the governor control linkage travel is limited to below half engine speed by an oil pressure actuated stop inside the governor.) Do not attempt to force the governor control linkage past the stop. When normal oil pressure is reached, operate the engine at low load for 5 minutes before applying full load.Select the lowest gear for a smooth, easy start without slipping the clutch. Rapid engine acceleration causes heavy exhaust smoke and high fuel consumption with no increase in vehicle performance. For best performance, do not skip gears when loaded.Caterpillar engines have good lugging characteristics; however, avoid operating in a lug condition for extended periods of time as it causes exhaust temperatures to rise and results in high fuel consumption. A lug condition exists when an increase in engine speed cannot be achieved with an increase in accelerator pedal position, or when engine speed decreases with the accelerator pedal in its maximum position. A lug condition can exist at any engine speed below full load speed.Continue to upshift until cruising speed is reached. Cruising speed should be between three-fourths and full governed RPM. (The governor will maintain a constant speed without accelerator pedal correction.)On upgrade, begin downshifting if engine starts to labor. Downshift until a gear is reached in which the engine will pull the load without lugging. For best performance, downshift before engine RPM falls below peak torque RPM (see page 2).On downgrade, do not coast or put transmission in neutral. Select the correct gear to keep engine speed below idle and retard the vehicle. A simple rule to follow is to select the same gear that would be used to go up the grade. Do not allow engine speed to exceed high idle.Before stopping the engine, operate at low load for 5 minutes, then at low idle for 30 seconds. (This procedure allows hot areas in the engine to cool gradually, extending the engine life.) To stop the engine, use one of the methods listed. TO STOP THE ENGINE, DO ONE OF THE FOLLOWING, DEPENDING ON TRUCK ARRANGEMENT1. Turn the key to the spring-loaded position and hold until engine stops, then release key, or2. Pull out the manual shutoff control, or3. Push in and hold stop button until engine stops, then release button, or4. Pull up on the accelerator.
Have questions with 107692-1190?
Group cross 107692-1190 ZEXEL
Isuzu
Isuzu
Isuzu
Isuzu
107692-1190
9 400 612 794
1156029470
INJECTION-PUMP ASSEMBLY
6BG1-TC1
6BG1-TC1