Information injection-pump assembly
BOSCH
9 400 619 626
9400619626
ZEXEL
107692-1170
1076921170
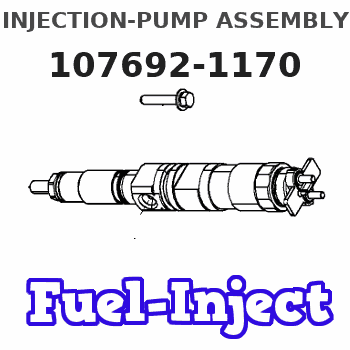
Rating:
Service parts 107692-1170 INJECTION-PUMP ASSEMBLY:
1.
_
5.
AUTOM. ADVANCE MECHANIS
9.
_
11.
Nozzle and Holder
8-94394-606-6
12.
Open Pre:MPa(Kqf/cm2)
21.6{220}
15.
NOZZLE SET
Include in #1:
107692-1170
as INJECTION-PUMP ASSEMBLY
Cross reference number
BOSCH
9 400 619 626
9400619626
ZEXEL
107692-1170
1076921170
Zexel num
Bosch num
Firm num
Name
Calibration Data:
Adjustment conditions
Test oil
1404 Test oil ISO4113 or {SAEJ967d}
1404 Test oil ISO4113 or {SAEJ967d}
Test oil temperature
degC
40
40
45
Nozzle and nozzle holder
105780-8240
Nozzle
105780-0110
Nozzle holder
105780-2170
Opening pressure
MPa
20.6
Opening pressure
kgf/cm2
210
Injection pipe
Outer diameter - inner diameter - length (mm) mm 8-3-600
Outer diameter - inner diameter - length (mm) mm 8-3-600
Overflow valve
131425-0520
Overflow valve opening pressure
kPa
255
221
289
Overflow valve opening pressure
kgf/cm2
2.6
2.25
2.95
Tester oil delivery pressure
kPa
255
255
255
Tester oil delivery pressure
kgf/cm2
2.6
2.6
2.6
PS/ACT control unit part no.
407910-3
03*
Selector switch no.
00
PS/ACT control unit part no.
407980-2
24*
Digi switch no.
11
Direction of rotation (viewed from drive side)
Left L
Left L
Injection timing adjustment
Direction of rotation (viewed from drive side)
Left L
Left L
Injection order
1-5-3-6-
2-4
Pre-stroke
mm
1.9
1.87
1.93
Beginning of injection position
Governor side NO.1
Governor side NO.1
Difference between angles 1
Cal 1-5 deg. 60 59.75 60.25
Cal 1-5 deg. 60 59.75 60.25
Difference between angles 2
Cal 1-3 deg. 120 119.75 120.25
Cal 1-3 deg. 120 119.75 120.25
Difference between angles 3
Cal 1-6 deg. 180 179.75 180.25
Cal 1-6 deg. 180 179.75 180.25
Difference between angles 4
Cyl.1-2 deg. 240 239.75 240.25
Cyl.1-2 deg. 240 239.75 240.25
Difference between angles 5
Cal 1-4 deg. 300 299.75 300.25
Cal 1-4 deg. 300 299.75 300.25
Injection quantity adjustment
Adjusting point
-
Rack position
13.3
Pump speed
r/min
750
750
750
Average injection quantity
mm3/st.
99.5
97.9
101.1
Max. variation between cylinders
%
0
-2.5
2.5
Basic
*
Fixing the rack
*
PS407980-224*
V
1.88+-0.
01
PS407980-224*
mm
3.2+-0.0
3
PS407910-303*
V
1.88+-0.
01
PS407910-303*
mm
3.2+-0.0
3
Standard for adjustment of the maximum variation between cylinders
*
Injection quantity adjustment_02
Adjusting point
Z
Rack position
9.1+-0.5
Pump speed
r/min
480
480
480
Average injection quantity
mm3/st.
12.5
11.2
13.8
Max. variation between cylinders
%
0
-14
14
Fixing the rack
*
PS407980-224*
V
1.88+-0.
01
PS407980-224*
mm
3.2+-0.0
3
PS407910-303*
V
1.88+-0.
01
PS407910-303*
mm
3.2+-0.0
3
Standard for adjustment of the maximum variation between cylinders
*
Injection quantity adjustment_03
Adjusting point
A
Rack position
R1(13.3)
Pump speed
r/min
750
750
750
Average injection quantity
mm3/st.
99.5
98.5
100.5
Basic
*
Fixing the lever
*
Boost pressure
kPa
60
60
Boost pressure
mmHg
450
450
PS407980-224*
V
1.88+-0.
01
PS407980-224*
mm
3.2+-0.0
3
PS407910-303*
V
1.88+-0.
01
PS407910-303*
mm
3.2+-0.0
3
Boost compensator adjustment
Pump speed
r/min
300
300
300
Rack position
R2-1.9
Boost pressure
kPa
17.3
16
18.6
Boost pressure
mmHg
130
120
140
Boost compensator adjustment_02
Pump speed
r/min
300
300
300
Rack position
R2(R1-0.
35)
Boost pressure
kPa
46.7
46.7
46.7
Boost pressure
mmHg
350
350
350
0000001601
CU407980-224*
*
Actuator advancing type
*
Supply voltage
V
12
11.5
12.5
Ambient temperature
degC
23
18
28
Pre-stroke
mm
5
4.95
5.05
Output voltage
V
2.83
2.82
2.84
Adjustment
*
_02
CU407980-224*
*
Supply voltage
V
12
11.5
12.5
Ambient temperature
degC
23
18
28
Pre-stroke
mm
1.9
1.87
1.93
Output voltage
V
1.2
1
1.4
Confirmation
*
_03
CU407980-224*
*
Supply voltage
V
12
11.5
12.5
Ambient temperature
degC
23
18
28
Output voltage
V
3.05
3.05
Confirmation of operating range
*
_04
CU407910-303*
*
Actuator advancing type
*
Supply voltage
V
12
11.5
12.5
Ambient temperature
degC
23
18
28
Pre-stroke
mm
5
4.95
5.05
Output voltage
V
2.83
2.82
2.84
Adjustment
*
_05
CU407910-303*
*
Supply voltage
V
12
11.5
12.5
Ambient temperature
degC
23
18
28
Pre-stroke
mm
1.9
1.87
1.93
Output voltage
V
1.2
1
1.4
Confirmation
*
_06
CU407910-303*
*
Supply voltage
V
12
11.5
12.5
Ambient temperature
degC
23
18
28
Output voltage
V
3.05
3.05
Confirmation of operating range
*
Test data Ex:
Governor adjustment
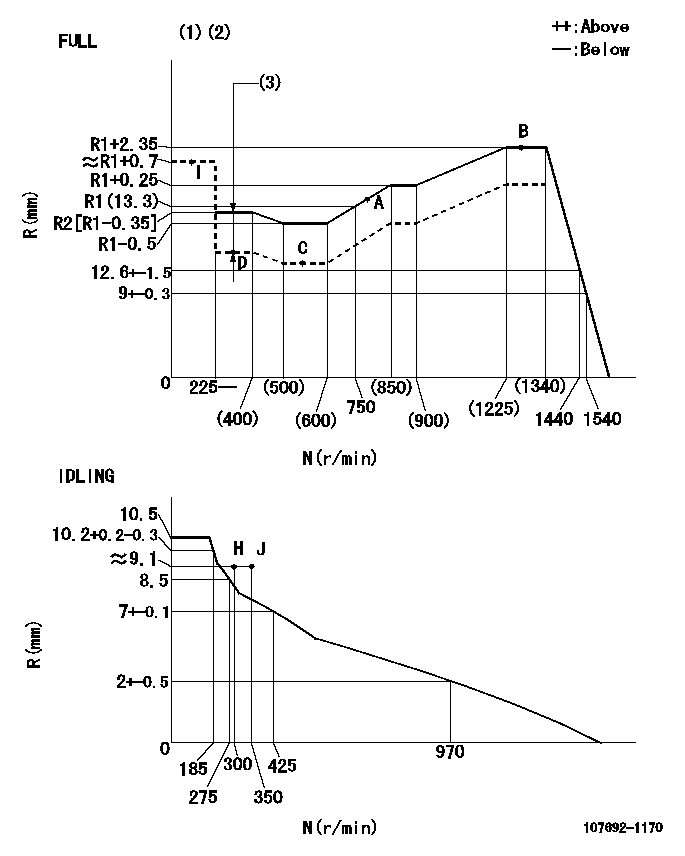
N:Pump speed
R:Rack position (mm)
(1)Torque cam stamping: T1
(2)Tolerance for racks not indicated: +-0.05mm.
(3)Boost compensator stroke: BCL
----------
T1=AB10 BCL=1.9+-0.1mm
----------
----------
T1=AB10 BCL=1.9+-0.1mm
----------
Speed control lever angle

F:Full speed
I:Idle
(1)Stopper bolt setting
(2)Use the pin at R = aa
----------
aa=35mm
----------
a=2deg+-5deg b=32deg+-3deg
----------
aa=35mm
----------
a=2deg+-5deg b=32deg+-3deg
Stop lever angle

N:Pump normal
S:Stop the pump.
(1)-
(2)Set the stopper bolt at speed = aa and rack position = bb and confirm non-injection.
(3)Use the pin above R = cc
----------
aa=0r/min bb=1.5+-0.3mm cc=40mm
----------
a=12deg+-5deg b=44deg+-5deg
----------
aa=0r/min bb=1.5+-0.3mm cc=40mm
----------
a=12deg+-5deg b=44deg+-5deg
0000001301
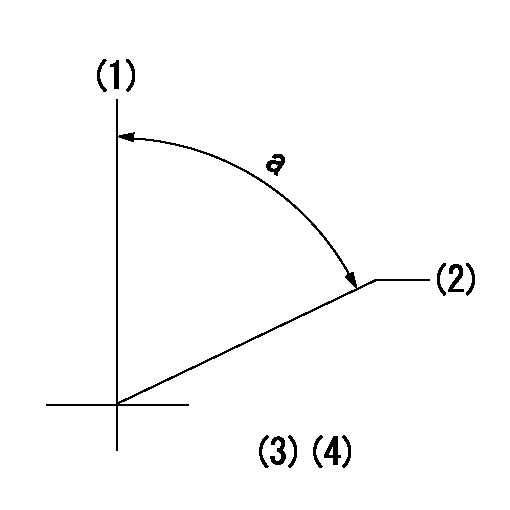
(1)Pump vertical direction
(2)Position of flywheel's threaded hole at No 1 cylinder's beginning of injection
(3)B.T.D.C.: aa
(4)Pre-stroke: bb
----------
aa=22deg bb=1.9+-0.03mm
----------
a=(60deg)
----------
aa=22deg bb=1.9+-0.03mm
----------
a=(60deg)
0000001401
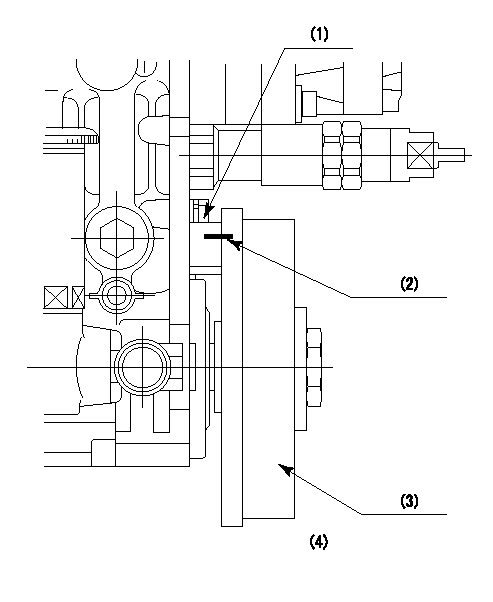
(1)Pointer
(2)Injection timing aligning mark
(3)Fly weight
(4)The actual shape and direction may be different from this illustration.
Operation sequence
1. Turn the prestroke actuator OFF.
2. Turn the camshaft as far as the No.1 cylinder's beginning of injection position.
3. Check that the pointer alignment mark of the injection pump and the alignment mark of the flywheel are matching.
4. If they are not matching, erase the alignment mark on the flywheel side, and stamp an alignment mark on the flywheel position that matches with the pointer side alignment mark.
5. Check again that the coupling's key groove position is in the No.1 cylinder's beginning of injection position.
----------
----------
----------
----------
0000001701
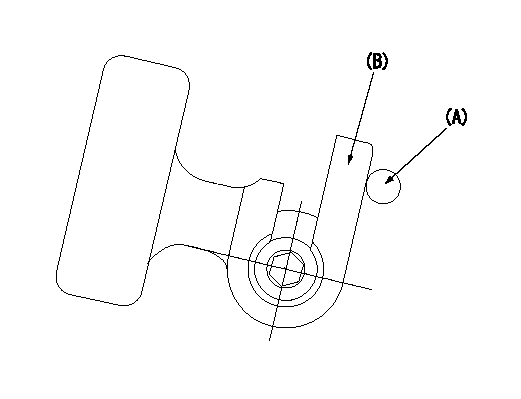
A : Stopper pin
B: Connector
----------
----------
----------
----------
0000001801
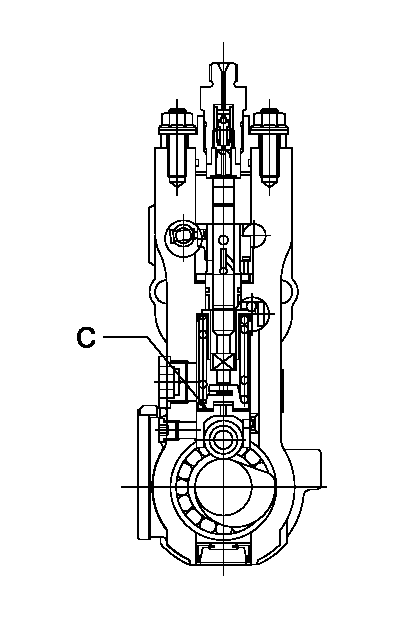
C:Shim
----------
----------
----------
----------
0000001901
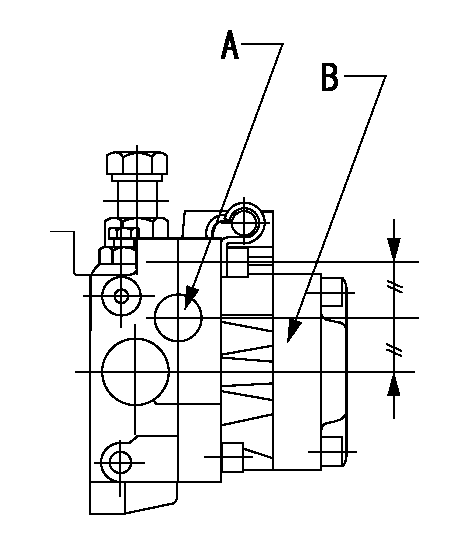
A:Sealing position
B:Pre-stroke actuator
1. When installing the pre-stroke actuator on the pump, first tighten the installation bolts loosely, then move the actuator fully clockwise (viewed from the drive side).
Temporary tightening torque: 1 - 1.5 N.m (0.1 - 0.15 kgf.m)
2. Move the actuator in the counterclockwise direction when viewed from the drive side, and adjust so that it becomes the adjustment point of the adjustment value. Then tighten it.
Tightening torque: 7^9 N.m (0.7^0.9 kgf.m)
3. After prestroke actuator installation adjustment, simultaneously stamp both the actuator side and housing side.
----------
----------
----------
----------
0000002201 RACK SENSOR
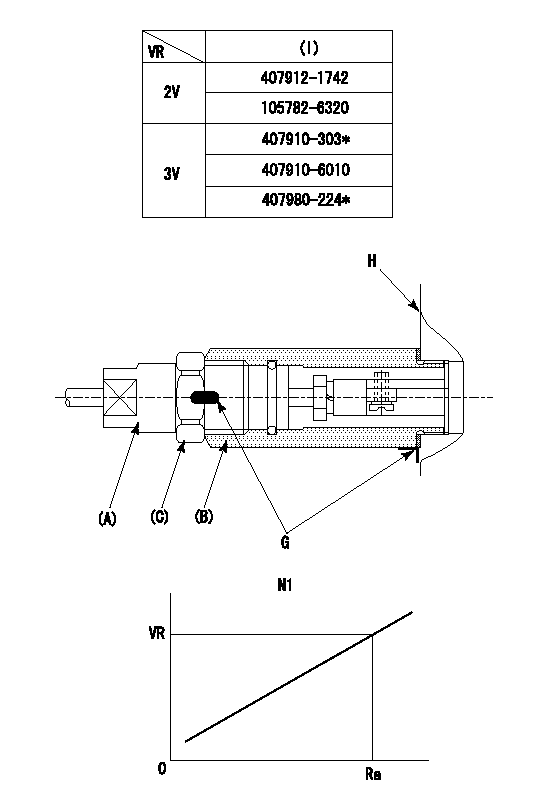
(VR) measurement voltage
(I) Part number of the control unit
(G) Apply red paint.
(H): End surface of the pump
1. Rack sensor adjustment (-0620)
(1)Fix the speed control lever at the full position
(2)Set the speed to N1 r/min.
(If the boost compensator is provided, apply boost pressure.)
(3)Adjust the bobbin (A) so that the rack sensor's output voltage is VR+-0.01.
(4)At that time, rack position must be Ra.
(5)Apply G at two places.
Connecting part between the joint (B) and the nut (F)
Connecting part between the joint (B) and the end surface of the pump (H)
----------
N1=1250r/min Ra=R1(13.3)+2.35mm
----------
----------
N1=1250r/min Ra=R1(13.3)+2.35mm
----------
Information:
Cold Weather Battery Maintenance
General Maintenance
1. After adding make-up water, charge the battery. The added water could dilute the electrolyte enough without charging to cause freezing and permanent damage to the battery.2. Keep the batteries fully charged either by operating the charging system or by using a battery charger.3. Keep the battery warm when not in use. In an unheated area, the heat from a lighted electric bulb is usually sufficient.
Use only a shop cord with a heavy wire guard around the light bulb.
Do not lay a lighted bulb directly on a battery case; the heat at point of contact could melt the battery case.Do not lay cloth or flammable material in contact with a lighted bulb; charring and/or fire could result.4. Use starting aids as instructed for starting the engine.5. Use booster batteries as required. Connect the batteries as instructed below.6. If a battery is not going to be used for a period of time, be sure the battery is fully charged while stored. Use a battery hydrometer to check the specific gravity of each cell, and use a battery charger to keep the battery charged. See the instructions below.Voltage Test (After Load)
A load test should be made on a battery that discharges very rapidly when in use. To do this apply a resistance of three times the ampere/hour rating of the battery across the battery main terminals. Allow the resistance to discharge the the battery for 15 seconds and immediately test the battery voltage. A 6 volt battery in good condition will test 4.5 volts; a 12 volt battery in good condition will test 9 volts and a 24 volt battery will test 18 volts.Starter
No periodic service is indicated for the electric starter brushes between general reconditioning periods. The brushes should only be inspected after removal of the starter from the engine and removal of the commutator end bearing frame. The electric starter commutator end and drive end bearings are equipped with wicks for lubrication purposes. The wicks should be saturated with oil whenever the electric starter is removed or disassembled.It is suggested that cleaning and reconditioning be entrusted to your authorized dealer.Pinion Clearance Adjustment
Whenever the solenoid is installed, the pinion clearance should be adjusted. The adjustment should be made with the starting motor removed.Bench test and adjust the pinion clearance at installation of solenoid as follows:
CIRCUIT FOR CHECKING AND ADJUSTING PINION CLEARANCE1. Install the solenoid without connector from the MOTOR terminal on solenoid to the motor.2. Connect a battery, of the same voltage as the solenoid, to the terminal marked SW.3. Connect the other side of battery to ground terminal or to solenoid frame.
ADJUSTING PINION CLEARANCE4. MOMENTARILY flash a jumper wire from the solenoid terminal marked MOTOR to the frame or ground terminal. The pinion will shift into cranking position and will remain there until the battery is disconnected.5. Push pinion towards commutator end to eliminate free movement.6. Pinion clearance should be .36 in. (9.14 mm).7. Adjust clearance by removing plug and turning shaft nut.
ADJUSTING PINION
General Maintenance
1. After adding make-up water, charge the battery. The added water could dilute the electrolyte enough without charging to cause freezing and permanent damage to the battery.2. Keep the batteries fully charged either by operating the charging system or by using a battery charger.3. Keep the battery warm when not in use. In an unheated area, the heat from a lighted electric bulb is usually sufficient.
Use only a shop cord with a heavy wire guard around the light bulb.
Do not lay a lighted bulb directly on a battery case; the heat at point of contact could melt the battery case.Do not lay cloth or flammable material in contact with a lighted bulb; charring and/or fire could result.4. Use starting aids as instructed for starting the engine.5. Use booster batteries as required. Connect the batteries as instructed below.6. If a battery is not going to be used for a period of time, be sure the battery is fully charged while stored. Use a battery hydrometer to check the specific gravity of each cell, and use a battery charger to keep the battery charged. See the instructions below.Voltage Test (After Load)
A load test should be made on a battery that discharges very rapidly when in use. To do this apply a resistance of three times the ampere/hour rating of the battery across the battery main terminals. Allow the resistance to discharge the the battery for 15 seconds and immediately test the battery voltage. A 6 volt battery in good condition will test 4.5 volts; a 12 volt battery in good condition will test 9 volts and a 24 volt battery will test 18 volts.Starter
No periodic service is indicated for the electric starter brushes between general reconditioning periods. The brushes should only be inspected after removal of the starter from the engine and removal of the commutator end bearing frame. The electric starter commutator end and drive end bearings are equipped with wicks for lubrication purposes. The wicks should be saturated with oil whenever the electric starter is removed or disassembled.It is suggested that cleaning and reconditioning be entrusted to your authorized dealer.Pinion Clearance Adjustment
Whenever the solenoid is installed, the pinion clearance should be adjusted. The adjustment should be made with the starting motor removed.Bench test and adjust the pinion clearance at installation of solenoid as follows:
CIRCUIT FOR CHECKING AND ADJUSTING PINION CLEARANCE1. Install the solenoid without connector from the MOTOR terminal on solenoid to the motor.2. Connect a battery, of the same voltage as the solenoid, to the terminal marked SW.3. Connect the other side of battery to ground terminal or to solenoid frame.
ADJUSTING PINION CLEARANCE4. MOMENTARILY flash a jumper wire from the solenoid terminal marked MOTOR to the frame or ground terminal. The pinion will shift into cranking position and will remain there until the battery is disconnected.5. Push pinion towards commutator end to eliminate free movement.6. Pinion clearance should be .36 in. (9.14 mm).7. Adjust clearance by removing plug and turning shaft nut.
ADJUSTING PINION