Information injection-pump assembly
BOSCH
F 019 Z10 463
f019z10463
ZEXEL
107692-1111
1076921111
ISUZU
8943946051
8943946051
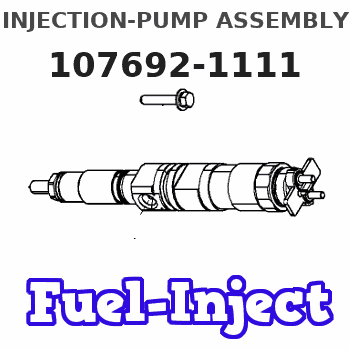
Rating:
Service parts 107692-1111 INJECTION-PUMP ASSEMBLY:
1.
_
5.
AUTOM. ADVANCE MECHANIS
9.
_
11.
Nozzle and Holder
8-94394-606-6
12.
Open Pre:MPa(Kqf/cm2)
21.6(220)
15.
NOZZLE SET
Include in #1:
107692-1111
as INJECTION-PUMP ASSEMBLY
Cross reference number
BOSCH
F 019 Z10 463
f019z10463
ZEXEL
107692-1111
1076921111
ISUZU
8943946051
8943946051
Zexel num
Bosch num
Firm num
Name
F 019 Z10 463
8943946051 ISUZU
INJECTION-PUMP ASSEMBLY
6HE1-XN * K 14CG TICS MD-TI6 TICS
6HE1-XN * K 14CG TICS MD-TI6 TICS
Calibration Data:
Adjustment conditions
Test oil
1404 Test oil ISO4113 or {SAEJ967d}
1404 Test oil ISO4113 or {SAEJ967d}
Test oil temperature
degC
40
40
45
Nozzle and nozzle holder
105780-8140
Bosch type code
EF8511/9A
Nozzle
105780-0000
Bosch type code
DN12SD12T
Nozzle holder
105780-2080
Bosch type code
EF8511/9
Opening pressure
MPa
17.2
Opening pressure
kgf/cm2
175
Injection pipe
Outer diameter - inner diameter - length (mm) mm 8-3-600
Outer diameter - inner diameter - length (mm) mm 8-3-600
Overflow valve
131424-9720
Overflow valve opening pressure
kPa
255
221
289
Overflow valve opening pressure
kgf/cm2
2.6
2.25
2.95
Tester oil delivery pressure
kPa
255
255
255
Tester oil delivery pressure
kgf/cm2
2.6
2.6
2.6
PS/ACT control unit part no.
407910-3
03*
Selector switch no.
00
PS/ACT control unit part no.
407980-2
24*
Digi switch no.
11
Direction of rotation (viewed from drive side)
Left L
Left L
Injection timing adjustment
Direction of rotation (viewed from drive side)
Left L
Left L
Injection order
1-5-3-6-
2-4
Pre-stroke
mm
1.9
1.87
1.93
Beginning of injection position
Governor side NO.1
Governor side NO.1
Difference between angles 1
Cal 1-5 deg. 60 59.75 60.25
Cal 1-5 deg. 60 59.75 60.25
Difference between angles 2
Cal 1-3 deg. 120 119.75 120.25
Cal 1-3 deg. 120 119.75 120.25
Difference between angles 3
Cal 1-6 deg. 180 179.75 180.25
Cal 1-6 deg. 180 179.75 180.25
Difference between angles 4
Cyl.1-2 deg. 240 239.75 240.25
Cyl.1-2 deg. 240 239.75 240.25
Difference between angles 5
Cal 1-4 deg. 300 299.75 300.25
Cal 1-4 deg. 300 299.75 300.25
Injection quantity adjustment
Adjusting point
-
Rack position
13.1
Pump speed
r/min
750
750
750
Average injection quantity
mm3/st.
107
105.4
108.6
Max. variation between cylinders
%
0
-2.5
2.5
Basic
*
Fixing the rack
*
PS407980-224*
V
1.88+-0.
01
PS407980-224*
mm
3.2+-0.0
3
PS407910-303*
V
1.88+-0.
01
PS407910-303*
mm
3.2+-0.0
3
Standard for adjustment of the maximum variation between cylinders
*
Injection quantity adjustment_02
Adjusting point
Z
Rack position
8.5+-0.5
Pump speed
r/min
570
570
570
Average injection quantity
mm3/st.
12.5
11.2
13.8
Max. variation between cylinders
%
0
-14
14
Fixing the rack
*
PS407980-224*
V
1.88+-0.
01
PS407980-224*
mm
3.2+-0.0
3
PS407910-303*
V
1.88+-0.
01
PS407910-303*
mm
3.2+-0.0
3
Standard for adjustment of the maximum variation between cylinders
*
Injection quantity adjustment_03
Adjusting point
A
Rack position
R1(13.1)
Pump speed
r/min
750
750
750
Average injection quantity
mm3/st.
107
106
108
Basic
*
Fixing the lever
*
Boost pressure
kPa
58.7
58.7
Boost pressure
mmHg
440
440
PS407980-224*
V
1.88+-0.
01
PS407980-224*
mm
3.2+-0.0
3
PS407910-303*
V
1.88+-0.
01
PS407910-303*
mm
3.2+-0.0
3
Boost compensator adjustment
Pump speed
r/min
300
300
300
Rack position
R2-1.9
Boost pressure
kPa
20
18.7
21.3
Boost pressure
mmHg
150
140
160
Boost compensator adjustment_02
Pump speed
r/min
300
300
300
Rack position
R2(R1-0.
45)
Boost pressure
kPa
45.3
45.3
45.3
Boost pressure
mmHg
340
340
340
0000001601
CU407980-224*
*
Actuator advancing type
*
Supply voltage
V
12
11.5
12.5
Ambient temperature
degC
23
18
28
Pre-stroke
mm
5
4.95
5.05
Output voltage
V
2.83
2.82
2.84
Adjustment
*
_02
CU407980-224*
*
Supply voltage
V
12
11.5
12.5
Ambient temperature
degC
23
18
28
Pre-stroke
mm
1.9
1.87
1.93
Output voltage
V
1.2
1
1.4
Confirmation
*
_03
CU407980-224*
*
Supply voltage
V
12
11.5
12.5
Ambient temperature
degC
23
18
28
Output voltage
V
3.05
3.05
Confirmation of operating range
*
_04
CU407910-303*
*
Actuator advancing type
*
Supply voltage
V
12
11.5
12.5
Ambient temperature
degC
23
18
28
Pre-stroke
mm
5
4.95
5.05
Output voltage
V
2.83
2.82
2.84
Adjustment
*
_05
CU407910-303*
*
Supply voltage
V
12
11.5
12.5
Ambient temperature
degC
23
18
28
Pre-stroke
mm
1.9
1.87
1.93
Output voltage
V
1.2
1
1.4
Confirmation
*
_06
CU407910-303*
*
Supply voltage
V
12
11.5
12.5
Ambient temperature
degC
23
18
28
Output voltage
V
3.05
3.05
Confirmation of operating range
*
Test data Ex:
Governor adjustment
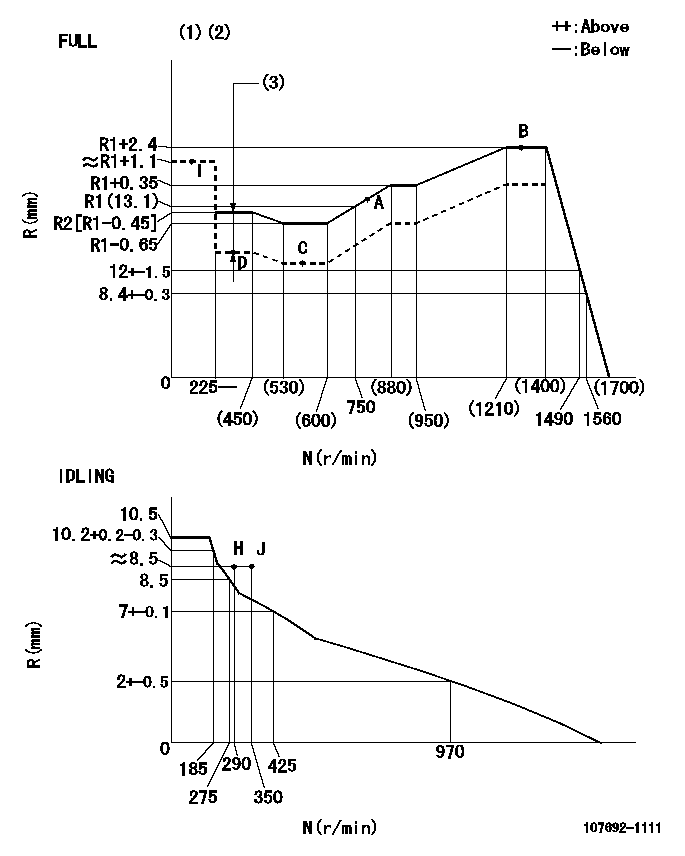
N:Pump speed
R:Rack position (mm)
(1)Torque cam stamping: T1
(2)Tolerance for racks not indicated: +-0.05mm.
(3)Boost compensator stroke: BCL
----------
T1=AA12 BCL=1.9+-0.1mm
----------
----------
T1=AA12 BCL=1.9+-0.1mm
----------
Speed control lever angle
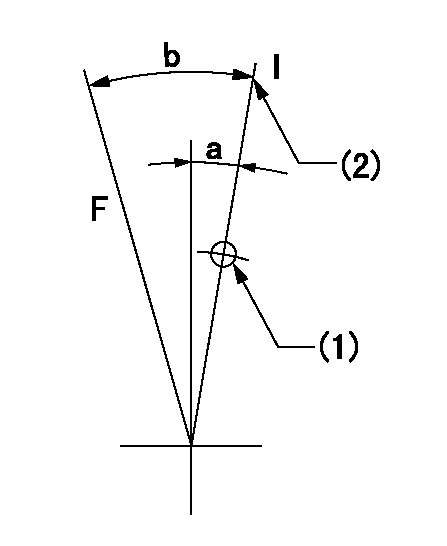
F:Full speed
I:Idle
(1)Use the pin at R = aa
(2)Stopper bolt setting
----------
aa=35mm
----------
a=0deg+-5deg b=(35deg)+-3deg
----------
aa=35mm
----------
a=0deg+-5deg b=(35deg)+-3deg
Stop lever angle

N:Pump normal
S:Stop the pump.
(1)-
(2)Set the stopper bolt at speed = aa and rack position = bb and confirm non-injection.
(3)Use the pin above R = cc
----------
aa=0r/min bb=1.5+-0.3mm cc=40mm
----------
a=12deg+-5deg b=44deg+-5deg
----------
aa=0r/min bb=1.5+-0.3mm cc=40mm
----------
a=12deg+-5deg b=44deg+-5deg
0000001301
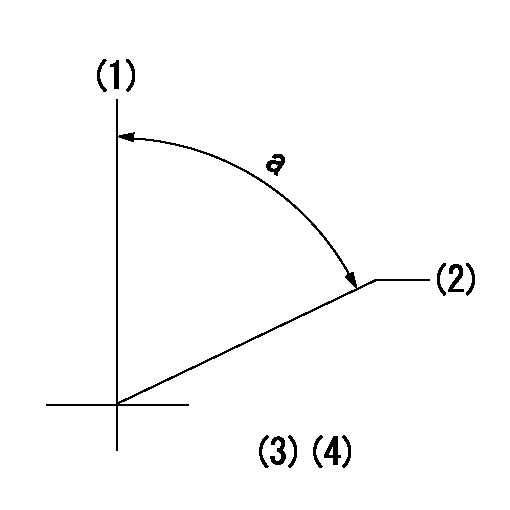
(1)Pump vertical direction
(2)Position of flywheel's threaded hole at No 1 cylinder's beginning of injection
(3)B.T.D.C.: aa
(4)Pre-stroke: bb
----------
aa=22deg bb=1.9+-0.03mm
----------
a=(60deg)
----------
aa=22deg bb=1.9+-0.03mm
----------
a=(60deg)
0000001401
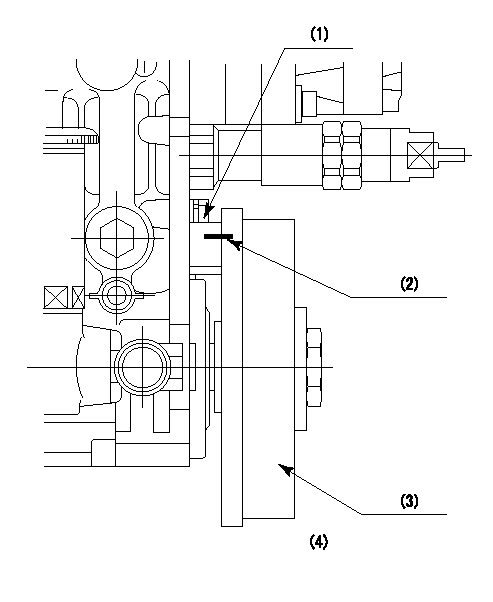
(1)Pointer
(2)Injection timing aligning mark
(3)Fly weight
(4)The actual shape and direction may be different from this illustration.
Operation sequence
1. Turn the prestroke actuator OFF.
2. Turn the camshaft as far as the No.1 cylinder's beginning of injection position.
3. Check that the pointer alignment mark of the injection pump and the alignment mark of the flywheel are matching.
4. If they are not matching, erase the alignment mark on the flywheel side, and stamp an alignment mark on the flywheel position that matches with the pointer side alignment mark.
5. Check again that the coupling's key groove position is in the No.1 cylinder's beginning of injection position.
----------
----------
----------
----------
0000001701
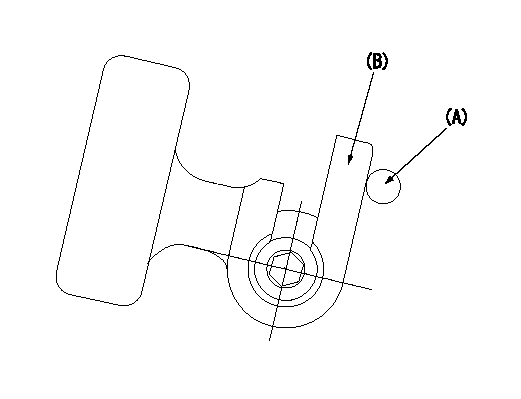
A : Stopper pin
B: Connector
----------
----------
----------
----------
0000001801
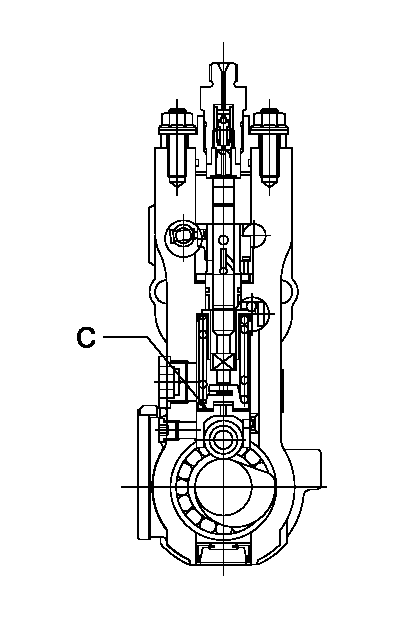
C:Shim
----------
----------
----------
----------
0000001901
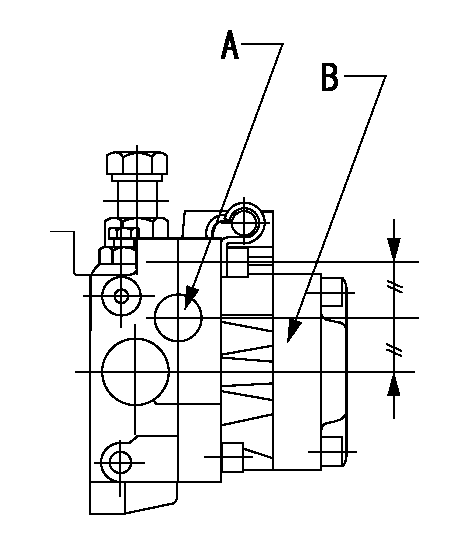
A:Sealing position
B:Pre-stroke actuator
1. When installing the pre-stroke actuator on the pump, first tighten the installation bolts loosely, then move the actuator fully clockwise (viewed from the drive side).
Temporary tightening torque: 1 - 1.5 N.m (0.1 - 0.15 kgf.m)
2. Move the actuator in the counterclockwise direction when viewed from the drive side, and adjust so that it becomes the adjustment point of the adjustment value. Then tighten it.
Tightening torque: 7^9 N.m (0.7^0.9 kgf.m)
3. After prestroke actuator installation adjustment, simultaneously stamp both the actuator side and housing side.
----------
----------
----------
----------
0000002201 RACK SENSOR
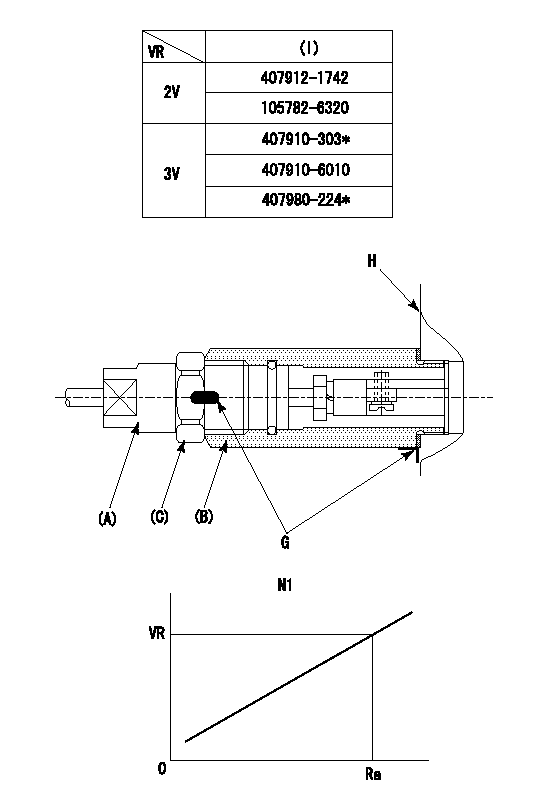
(VR) measurement voltage
(I) Part number of the control unit
(G) Apply red paint.
(H): End surface of the pump
1. Rack sensor adjustment (-0620)
(1)Fix the speed control lever at the full position
(2)Set the speed to N1 r/min.
(If the boost compensator is provided, apply boost pressure.)
(3)Adjust the bobbin (A) so that the rack sensor's output voltage is VR+-0.01.
(4)At that time, rack position must be Ra.
(5)Apply G at two places.
Connecting part between the joint (B) and the nut (F)
Connecting part between the joint (B) and the end surface of the pump (H)
----------
N1=1250r/min Ra=R1(13.1)+2.4mm
----------
----------
N1=1250r/min Ra=R1(13.1)+2.4mm
----------
0000002301 BCS
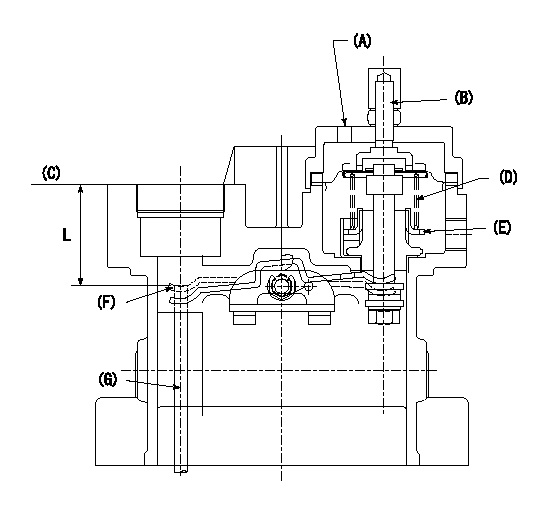
(A) Boost pressure inlet
(B) Screw for rack position adjustment
(C) End surface of the cover boss
(D) Boost compensator spring
(E) Spring set adjusting notch
(F) Lever surface
(G) Push rod
1. Instructions for adjusting the boost compensator
(1)Select a pushrod to obtain dimension L at full boost.
(2)(B) Adjust the boost compensator stroke with the screw.
(3)(E) Adjust the beginning of boost compensator operation by moving the notch.
----------
L=37.5+-0.5mm
----------
----------
L=37.5+-0.5mm
----------
Information:
This guide contains operation instructions and lubrication and maintenance information.The operation section is a reference for the new operator and a refresher for the experienced one. Read - study - and keep it handy.Illustrations guide the operator through correct procedures of checking, starting, operating and stopping the engine.The maintenance section is a guide to equipment care. The illustrated, step-by-step instructions are grouped by servicing intervals. Items in the "Lubrication and Maintenance Chart" are referenced to the detailed instructions that follow.Use the service meter to determine servicing intervals. Calendar intervals shown may be used instead of service meter intervals if they provide more convenient servicing schedules and approximate the indicated service meter reading. Recommended service should always be performed at the interval that occurs first.Under extremely severe, dusty or wet operating conditions, more frequent lubrication than is specified in the "Lubrication and Maintenance Chart" may be necessary.Perform service on items at multiples of the original requirement. For example, at Every 500 Service Meter Units, also service those items listed under Every 250 Service Meter Units, Every 50 Service Meter Units and Every 10 Service Meter Units.Some photographs in this publication show details or attachments that may be different from your engine. Also, guards and covers may have been removed for illustrative purposes.Continuing improvement and advancement of product design may have caused changes to your engine which are not included in this publication.Each publication is reviewed and revised, as required, to update and include these changes in later editions.Whenever a question arises regarding your engine or this publication, please consult your Caterpillar dealer for the latest available information.Engine Identification
Caterpillar engines are identified with SERIAL NUMBERS and ARRANGEMENT NUMBERS. In some cases MODIFICATION NUMBERS are also used. These numbers are shown on the serial number plate mounted on the engine.Caterpillar dealers need all of these numbers to determine which components were included on the engine when it was assembled at the factory. This permits accurate identification of replacement part numbers.Ordering Parts
Quality Caterpillar replacement parts are available from Caterpillar dealers throughout the world. Their parts stocks are up to date and include all parts normally required to protect your investment in Caterpillar engines. When ordering parts, your order should specify the quantity, part number, part name and serial number, arrangement number and modification number of the engine for which the parts are needed. If in doubt about the part number, please provide your dealer with a complete description of the needed item.
Caterpillar engines are identified with SERIAL NUMBERS and ARRANGEMENT NUMBERS. In some cases MODIFICATION NUMBERS are also used. These numbers are shown on the serial number plate mounted on the engine.Caterpillar dealers need all of these numbers to determine which components were included on the engine when it was assembled at the factory. This permits accurate identification of replacement part numbers.Ordering Parts
Quality Caterpillar replacement parts are available from Caterpillar dealers throughout the world. Their parts stocks are up to date and include all parts normally required to protect your investment in Caterpillar engines. When ordering parts, your order should specify the quantity, part number, part name and serial number, arrangement number and modification number of the engine for which the parts are needed. If in doubt about the part number, please provide your dealer with a complete description of the needed item.