Information injection-pump assembly
BOSCH
9 400 613 281
9400613281
ZEXEL
107691-3570
1076913570
HINO
220402341B
220402341b
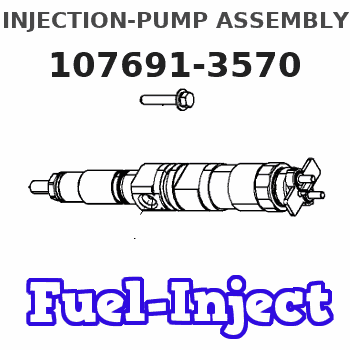
Rating:
Service parts 107691-3570 INJECTION-PUMP ASSEMBLY:
1.
_
7.
COUPLING PLATE
9.
_
11.
Nozzle and Holder
23600-3222B
12.
Open Pre:MPa(Kqf/cm2)
17.7{180}/21.6{220}
14.
NOZZLE
Include in #1:
107691-3570
as INJECTION-PUMP ASSEMBLY
Cross reference number
BOSCH
9 400 613 281
9400613281
ZEXEL
107691-3570
1076913570
HINO
220402341B
220402341b
Zexel num
Bosch num
Firm num
Name
9 400 613 281
220402341B HINO
INJECTION-PUMP ASSEMBLY
J08C-UJ * K 14CG TICS MD-TI6 TICS
J08C-UJ * K 14CG TICS MD-TI6 TICS
Calibration Data:
Adjustment conditions
Test oil
1404 Test oil ISO4113 or {SAEJ967d}
1404 Test oil ISO4113 or {SAEJ967d}
Test oil temperature
degC
40
40
45
Nozzle and nozzle holder
105780-8250
Bosch type code
1 688 901 101
Nozzle
105780-0120
Bosch type code
1 688 901 990
Nozzle holder
105780-2190
Opening pressure
MPa
20.7
Opening pressure
kgf/cm2
211
Injection pipe
Outer diameter - inner diameter - length (mm) mm 8-3-600
Outer diameter - inner diameter - length (mm) mm 8-3-600
Overflow valve
131425-0920
Overflow valve opening pressure
kPa
255
221
289
Overflow valve opening pressure
kgf/cm2
2.6
2.25
2.95
Tester oil delivery pressure
kPa
255
255
255
Tester oil delivery pressure
kgf/cm2
2.6
2.6
2.6
PS/ACT control unit part no.
407980-2
24*
Digi switch no.
17
Direction of rotation (viewed from drive side)
Left L
Left L
Injection timing adjustment
Direction of rotation (viewed from drive side)
Left L
Left L
Injection order
1-4-2-6-
3-5
Pre-stroke
mm
5.1
5.07
5.13
Beginning of injection position
Governor side NO.1
Governor side NO.1
Difference between angles 1
Cal 1-4 deg. 60 59.75 60.25
Cal 1-4 deg. 60 59.75 60.25
Difference between angles 2
Cyl.1-2 deg. 120 119.75 120.25
Cyl.1-2 deg. 120 119.75 120.25
Difference between angles 3
Cal 1-6 deg. 180 179.75 180.25
Cal 1-6 deg. 180 179.75 180.25
Difference between angles 4
Cal 1-3 deg. 240 239.75 240.25
Cal 1-3 deg. 240 239.75 240.25
Difference between angles 5
Cal 1-5 deg. 300 299.75 300.25
Cal 1-5 deg. 300 299.75 300.25
Injection quantity adjustment
Adjusting point
-
Rack position
12.7
Pump speed
r/min
750
750
750
Average injection quantity
mm3/st.
114.5
111.5
117.5
Max. variation between cylinders
%
0
-3.5
3.5
Basic
*
Fixing the rack
*
PS407980-224*
V
2.25+-0.
01
PS407980-224*
mm
3.1+-0.0
5
Standard for adjustment of the maximum variation between cylinders
*
Injection quantity adjustment_02
Adjusting point
Z
Rack position
8.2+-0.5
Pump speed
r/min
440
440
440
Each cylinder's injection qty
mm3/st.
13.5
12.15
14.85
Fixing the rack
*
PS407980-224*
V
V1+0.05+
-0.01
PS407980-224*
mm
5+-0.03
Standard for adjustment of the maximum variation between cylinders
*
Remarks
Refer to items regarding the pre-stroke actuator
Refer to items regarding the pre-stroke actuator
Injection quantity adjustment_03
Adjusting point
A
Rack position
R1(12.7)
Pump speed
r/min
750
750
750
Average injection quantity
mm3/st.
114.5
112.5
116.5
Basic
*
Fixing the lever
*
Boost pressure
kPa
62
62
Boost pressure
mmHg
465
465
PS407980-224*
V
2.25+-0.
01
PS407980-224*
mm
3.1+-0.0
5
Injection quantity adjustment_04
Adjusting point
B
Rack position
R1+2.05
Pump speed
r/min
1250
1250
1250
Average injection quantity
mm3/st.
124
118
130
Fixing the lever
*
Boost pressure
kPa
62
62
Boost pressure
mmHg
465
465
PS407980-224*
V
2.25+-0.
01
PS407980-224*
mm
3.1+-0.0
5
Boost compensator adjustment
Pump speed
r/min
300
300
300
Rack position
R2-1.15
Boost pressure
kPa
36
34.7
37.3
Boost pressure
mmHg
270
260
280
Boost compensator adjustment_02
Pump speed
r/min
300
300
300
Rack position
R2[R1-1]
Boost pressure
kPa
48.7
48.7
48.7
Boost pressure
mmHg
365
365
365
Timer adjustment
Pump speed
r/min
1200--
Advance angle
deg.
0
0
0
Remarks
Start
Start
Timer adjustment_02
Pump speed
r/min
1150
Advance angle
deg.
0
-0.3
0
Timer adjustment_03
Pump speed
r/min
1290
Advance angle
deg.
1.5
1.2
1.8
Remarks
Finish
Finish
0000001601
CU407980-224*
*
Actuator retarding type
*
Supply voltage
V
24
23.5
24.5
Ambient temperature
degC
23
18
28
Pre-stroke
mm
2
1.95
2.05
Output voltage
V
2.83
2.82
2.84
Adjustment
*
_02
CU407980-224*
*
Supply voltage
V
24
23.5
24.5
Ambient temperature
degC
23
18
28
Pre-stroke
mm
5.1
5.07
5.13
Output voltage
V
1.2
1
1.4
Confirmation
*
Remarks
Output voltage V1
Output voltage V1
_03
CU407980-224*
*
Supply voltage
V
24
23.5
24.5
Ambient temperature
degC
23
18
28
Output voltage
V
3.05
3.05
Confirmation of operating range
*
Test data Ex:
Governor adjustment
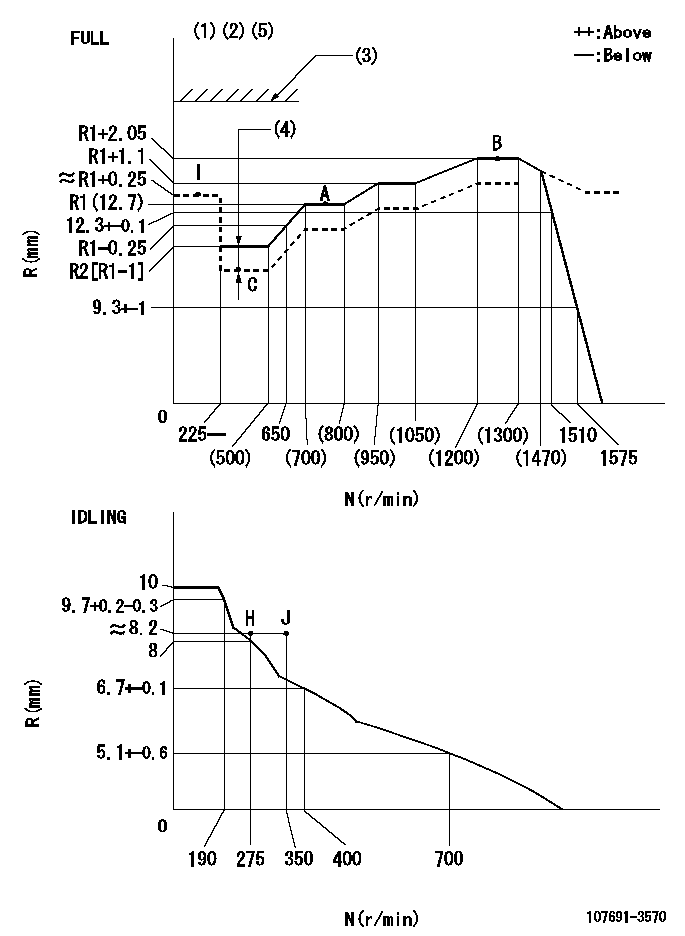
N:Pump speed
R:Rack position (mm)
(1)Torque cam stamping: T1
(2)Tolerance for racks not indicated: +-0.05mm.
(3)Stop lever's normal position setting: RA
(4)Boost compensator stroke: BCL
(5)When setting the stop lever after governor adjustment, confirm that rack position Ra (point B) can be obtained at the full setting.
----------
T1=AH02 RA=(18)mm BCL=1.15+-0.1mm Ra=R1(12.7)+2.05mm
----------
----------
T1=AH02 RA=(18)mm BCL=1.15+-0.1mm Ra=R1(12.7)+2.05mm
----------
Speed control lever angle
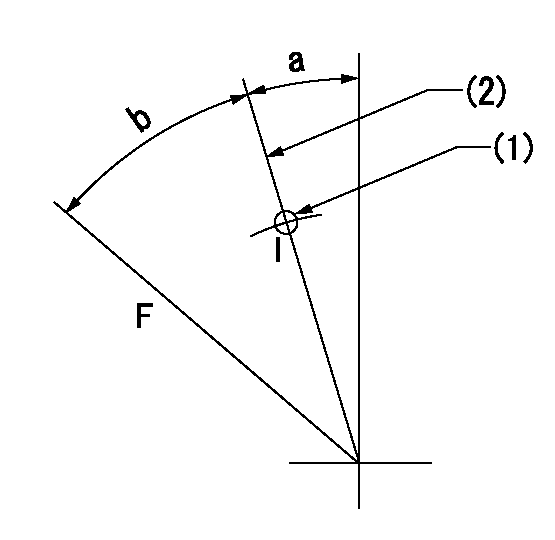
F:Full speed
I:Idle
(1)Use the hole at R = aa
(2)Stopper bolt setting
----------
aa=44mm
----------
a=8.5deg+-5deg b=(38deg)+-3deg
----------
aa=44mm
----------
a=8.5deg+-5deg b=(38deg)+-3deg
Stop lever angle

N:Pump normal
S:Stop the pump.
(1)Rack position = aa, stopper bolt setting
(2)Speed = bb, rack position = cc
(3)Use the hole above R = dd
----------
aa=(18)mm bb=0r/min cc=1.5+-0.1mm dd=40mm
----------
a=15deg+-5deg b=35deg+-5deg
----------
aa=(18)mm bb=0r/min cc=1.5+-0.1mm dd=40mm
----------
a=15deg+-5deg b=35deg+-5deg
0000001301

(1)Pump vertical direction
(2)Coupling's key groove position at No 1 cylinder's beginning of injection
(3)Pre-stroke: aa
(4)-
----------
aa=5.1+-0.03mm
----------
a=(30deg)
----------
aa=5.1+-0.03mm
----------
a=(30deg)
0000001401
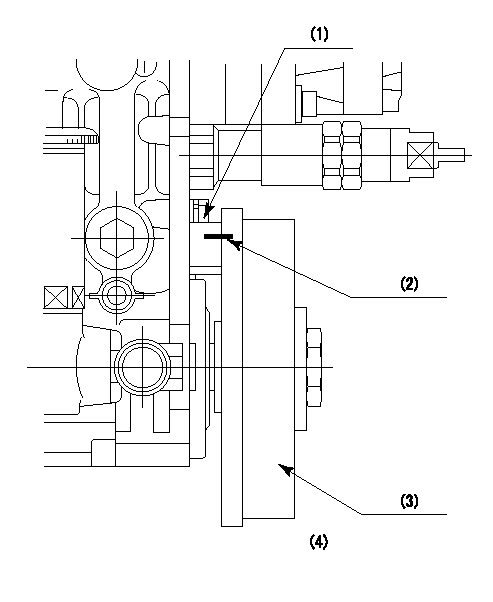
(1)Pointer
(2)Injection timing aligning mark
(3)Fly weight
(4)The actual shape and direction may be different from this illustration.
Operation sequence
1. Turn the prestroke actuator OFF.
2. Turn the camshaft as far as the No.1 cylinder's beginning of injection position.
3. Check that the pointer alignment mark of the injection pump and the alignment mark of the flywheel are matching.
4. If they are not matching, erase the alignment mark on the flywheel side, and stamp an alignment mark on the flywheel position that matches with the pointer side alignment mark.
5. Check again that the coupling's key groove position is in the No.1 cylinder's beginning of injection position.
----------
----------
----------
----------
0000001701
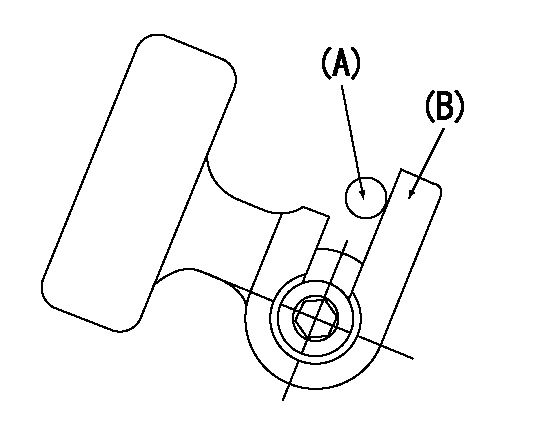
A : Stopper pin
B: Connector
----------
----------
----------
----------
0000001801
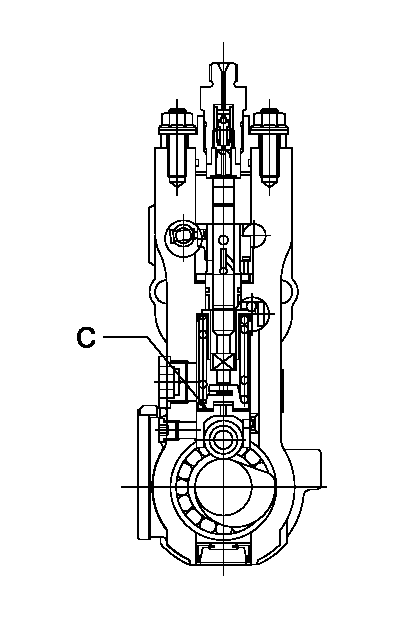
C:Shim
----------
----------
----------
----------
0000001901
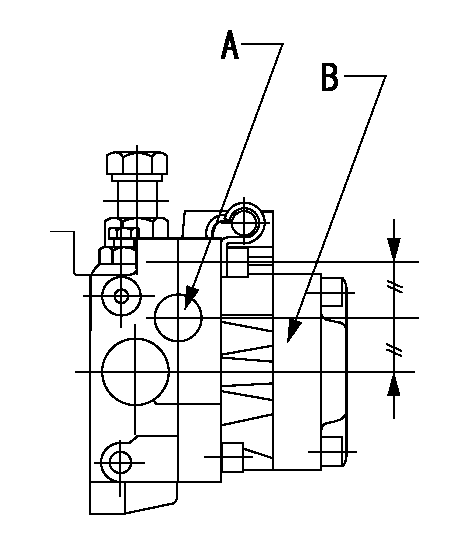
A:Sealing position
B:Pre-stroke actuator
1. When installing the pre-stroke actuator on the pump, first tighten the installation bolts loosely, then move the actuator fully clockwise (viewed from the drive side).
Temporary tightening torque: 1 - 1.5 N.m (0.1 - 0.15 kgf.m)
2. Move the actuator in the counterclockwise direction when viewed from the drive side, and adjust so that it becomes the adjustment point of the adjustment value. Then tighten it.
Tightening torque: 7^9 N.m (0.7^0.9 kgf.m)
3. After prestroke actuator installation adjustment, simultaneously stamp both the actuator side and housing side.
----------
----------
----------
----------
0000002201 RACK SENSOR

G:Red paint
H:Pump end face
P/N: part number of suitable shim
(1)Threaded type rack block
(2)Welded type rack block
Rack sensor adjustment
1. Threaded type rack sensor (-5*20, P type, no TICS rack limit).
(1)Screw in the bobbin (A) until it contacts the joint (B).
(2)Fix the pump lever.
(3)At speed N1 and rack position Ra, adjust the amount that the bobbin is screwed in so that the amp's output voltage is V1.
(4)Fix using the nut (F).
(5)Affix the caution plate to the upper part of the joint (B).
(6)Apply (G) at two places.
Connecting part between the joint (B) and the nut (F)
Connecting part between the end surface of the pump (H) and the joint (B)
2. Range for screw-in adjustment between the bobbin (A) and the joint (B) is 9 threads.
Screw in to the end from (the position where the bobbin (A) is rotated 9 turns).
Speed N1, rack position Ra, output voltage V1, rack sensor supply voltage 5+-0.01 (V)
----------
Ra=R1(12.7)+2.05mm N1=1250r/min V1=3+-0.01V
----------
----------
Ra=R1(12.7)+2.05mm N1=1250r/min V1=3+-0.01V
----------
Information:
Exhaust Smoke Can Be Seen While Starting
Possible Causes/Corrections Cold Outside TemperaturesIt may be necessary to use starting aids, or to heat engine oil or coolant at temperatures below -12°C (10°F).Air in Fuel System
With air in the fuel system, the engine will normally be difficult to start, run rough, and release a large amount of white smoke. If the engine will not start, loosen a fuel injection line nut at the through the head adapter and crank the engine until fuel comes out. Tighten the fuel line nut. Start the engine. If the engine still does not run smooth or releases a large amount of white smoke, loosen the fuel line nuts one at a time at the through the head adapters until the fuel that comes out is free of air. Tighten the fuel line nuts. If the air can not be removed in this way, put 35 kPa (5 psi) of air pressure to the fuel tank.
Do not use more than 55 kPa (8 psi) of air pressure in the fuel tank or damage to the tank may result.
Check for leakage at the connections between the fuel tank and the fuel transfer pump. If leaks are found, tighten the connections or replace the lines. It there are no visual leaks, remove the fuel supply line from the tank and connect it to an outside fuel supply. If this corrects the problem, the suction line (standpipe) inside the fuel tank has a leak.Low Quality Fuel
Remove a small amount of fuel from the tank and check for water in the fuel. If there is water in the fuel, remove fuel from the tank until it is free of water and fill with good quality fuel. For more information see Special Instruction, Form No. SEHS7067, Fuel Recommendations For Caterpillar Diesel Engines.Change the fuel filter and "prime" (remove the air and/or low quality fuel from the fuel system) the fuel system with the fuel priming pump. If there is no water in the fuel, prime and start the engine by using an outside source of fuel. If engine starts correctly using different fuel, remove all fuel from the tank and fill with good quality fuel. Prime the fuel system if necessary.Low Fuel Pressure
Change the primary and secondary fuel filters and check to make sure the fuel lines are not plugged or damaged. If the filters or lines are not the cause, a repair or replacement of the fuel transfer pump is needed.Fuel Injection Timing Not Correct
Check and make necessary adjustments as in Testing and Adjusting section of this Service Manual.Valve Adjustment Not Correct
Check and make necessary adjustments as in Testing and Adjusting section of this Service Manual. Intake valve clearance is 0.38 mm (.015 in) and exhaust valve clearance is 0.76 mm (.030 in).Bad Fuel Nozzle(s)
Remove the fuel nozzles and test as in Testing and Adjusting section of this Service Manual.Low Compression
See Misfiring and Running Rough.Exhaust Smoke Cannot Be Seen While Starting
Possible Causes/CorrectionsNo Fuel in Tank(s)
Check fuel level visually (do not
Possible Causes/Corrections Cold Outside TemperaturesIt may be necessary to use starting aids, or to heat engine oil or coolant at temperatures below -12°C (10°F).Air in Fuel System
With air in the fuel system, the engine will normally be difficult to start, run rough, and release a large amount of white smoke. If the engine will not start, loosen a fuel injection line nut at the through the head adapter and crank the engine until fuel comes out. Tighten the fuel line nut. Start the engine. If the engine still does not run smooth or releases a large amount of white smoke, loosen the fuel line nuts one at a time at the through the head adapters until the fuel that comes out is free of air. Tighten the fuel line nuts. If the air can not be removed in this way, put 35 kPa (5 psi) of air pressure to the fuel tank.
Do not use more than 55 kPa (8 psi) of air pressure in the fuel tank or damage to the tank may result.
Check for leakage at the connections between the fuel tank and the fuel transfer pump. If leaks are found, tighten the connections or replace the lines. It there are no visual leaks, remove the fuel supply line from the tank and connect it to an outside fuel supply. If this corrects the problem, the suction line (standpipe) inside the fuel tank has a leak.Low Quality Fuel
Remove a small amount of fuel from the tank and check for water in the fuel. If there is water in the fuel, remove fuel from the tank until it is free of water and fill with good quality fuel. For more information see Special Instruction, Form No. SEHS7067, Fuel Recommendations For Caterpillar Diesel Engines.Change the fuel filter and "prime" (remove the air and/or low quality fuel from the fuel system) the fuel system with the fuel priming pump. If there is no water in the fuel, prime and start the engine by using an outside source of fuel. If engine starts correctly using different fuel, remove all fuel from the tank and fill with good quality fuel. Prime the fuel system if necessary.Low Fuel Pressure
Change the primary and secondary fuel filters and check to make sure the fuel lines are not plugged or damaged. If the filters or lines are not the cause, a repair or replacement of the fuel transfer pump is needed.Fuel Injection Timing Not Correct
Check and make necessary adjustments as in Testing and Adjusting section of this Service Manual.Valve Adjustment Not Correct
Check and make necessary adjustments as in Testing and Adjusting section of this Service Manual. Intake valve clearance is 0.38 mm (.015 in) and exhaust valve clearance is 0.76 mm (.030 in).Bad Fuel Nozzle(s)
Remove the fuel nozzles and test as in Testing and Adjusting section of this Service Manual.Low Compression
See Misfiring and Running Rough.Exhaust Smoke Cannot Be Seen While Starting
Possible Causes/CorrectionsNo Fuel in Tank(s)
Check fuel level visually (do not