Information injection-pump assembly
BOSCH
9 400 612 796
9400612796
ZEXEL
107691-3551
1076913551
HINO
220402242A
220402242a
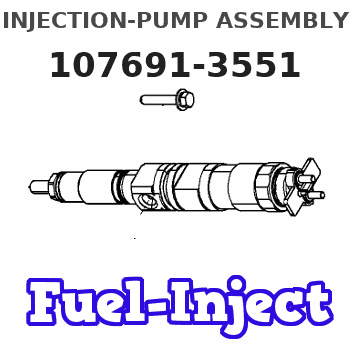
Rating:
Service parts 107691-3551 INJECTION-PUMP ASSEMBLY:
1.
_
7.
COUPLING PLATE
9.
_
11.
Nozzle and Holder
23600-3233B
12.
Open Pre:MPa(Kqf/cm2)
16.7{170}/21.6{220}
14.
NOZZLE
Include in #1:
107691-3551
as INJECTION-PUMP ASSEMBLY
Cross reference number
BOSCH
9 400 612 796
9400612796
ZEXEL
107691-3551
1076913551
HINO
220402242A
220402242a
Zexel num
Bosch num
Firm num
Name
9 400 612 796
220402242A HINO
INJECTION-PUMP ASSEMBLY
J08C * K 14CG TICS MD-TI6 TICS
J08C * K 14CG TICS MD-TI6 TICS
Calibration Data:
Adjustment conditions
Test oil
1404 Test oil ISO4113 or {SAEJ967d}
1404 Test oil ISO4113 or {SAEJ967d}
Test oil temperature
degC
40
40
45
Nozzle and nozzle holder
105780-8330
Nozzle
105780-0130
Nozzle holder
105780-2250
Opening pressure
MPa
16.7
Opening pressure
kgf/cm2
170
Injection pipe
Outer diameter - inner diameter - length (mm) mm 6-2-600
Outer diameter - inner diameter - length (mm) mm 6-2-600
Overflow valve
134424-4120
Overflow valve opening pressure
kPa
255
221
289
Overflow valve opening pressure
kgf/cm2
2.6
2.25
2.95
Tester oil delivery pressure
kPa
255
255
255
Tester oil delivery pressure
kgf/cm2
2.6
2.6
2.6
RED4 control unit part number
407915-0
590
RED4 rack sensor specifications
mm
19
PS/ACT control unit part no.
407980-2
24*
Digi switch no.
17
Direction of rotation (viewed from drive side)
Left L
Left L
Injection timing adjustment
Direction of rotation (viewed from drive side)
Left L
Left L
Injection order
1-4-2-6-
3-5
Pre-stroke
mm
5.1
5.07
5.13
Beginning of injection position
Governor side NO.1
Governor side NO.1
Difference between angles 1
Cal 1-4 deg. 60 59.75 60.25
Cal 1-4 deg. 60 59.75 60.25
Difference between angles 2
Cyl.1-2 deg. 120 119.75 120.25
Cyl.1-2 deg. 120 119.75 120.25
Difference between angles 3
Cal 1-6 deg. 180 179.75 180.25
Cal 1-6 deg. 180 179.75 180.25
Difference between angles 4
Cal 1-3 deg. 240 239.75 240.25
Cal 1-3 deg. 240 239.75 240.25
Difference between angles 5
Cal 1-5 deg. 300 299.75 300.25
Cal 1-5 deg. 300 299.75 300.25
Injection quantity adjustment
Rack position
(10.2)
PWM
%
45.6
Pump speed
r/min
800
800
800
Average injection quantity
mm3/st.
82
81
83
Max. variation between cylinders
%
0
-3.5
3.5
Basic
*
PS407980-224*
V
2.25+-0.
01
PS407980-224*
mm
3.1+-0.0
5
Injection quantity adjustment_02
Rack position
(6.6)
PWM
%
25.2+-2.
8
Pump speed
r/min
315
315
315
Each cylinder's injection qty
mm3/st.
13
12
14
PS407980-224*
V
V1+0.05+
-0.01
PS407980-224*
mm
5+-0.03
Remarks
Refer to items regarding the pre-stroke actuator
Refer to items regarding the pre-stroke actuator
Governor adjustment
Pump speed
r/min
1200--
Advance angle
deg.
0
0
0
Load
2/5
Remarks
Start
Start
Governor adjustment_02
Pump speed
r/min
1150
Advance angle
deg.
0.3
Load
2/5
Governor adjustment_03
Pump speed
r/min
1400
Advance angle
deg.
3.3
3
3.6
Load
5/5
Remarks
Finish
Finish
0000001201
CU407980-224*
*
Actuator retarding type
*
Supply voltage
V
24
23.5
24.5
Ambient temperature
degC
23
18
28
Pre-stroke
mm
2
1.95
2.05
Output voltage
V
2.83
2.82
2.84
Adjustment
*
_02
CU407980-224*
*
Supply voltage
V
24
23.5
24.5
Ambient temperature
degC
23
18
28
Pre-stroke
mm
5.1
5.07
5.13
Output voltage
V
1.2
1
1.4
Confirmation
*
Remarks
Output voltage V1
Output voltage V1
_03
CU407980-224*
*
Supply voltage
V
24
23.5
24.5
Ambient temperature
degC
23
18
28
Output voltage
V
3.05
3.05
Confirmation of operating range
*
Test data Ex:
Speed control lever angle
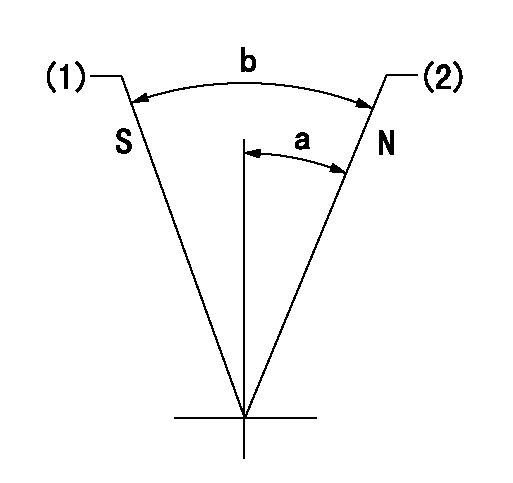
N:Pump normal
S:Stop the pump.
(1)Rack position = aa
(2)Rack position bb
----------
aa=1mm bb=20mm
----------
a=18.5deg+-5deg b=37deg+-5deg
----------
aa=1mm bb=20mm
----------
a=18.5deg+-5deg b=37deg+-5deg
0000000901

(1)Pump vertical direction
(2)Coupling's key groove position at No 1 cylinder's beginning of injection
(3)Pre-stroke: aa
(4)-
----------
aa=5.1+-0.03mm
----------
a=(20deg)
----------
aa=5.1+-0.03mm
----------
a=(20deg)
Stop lever angle
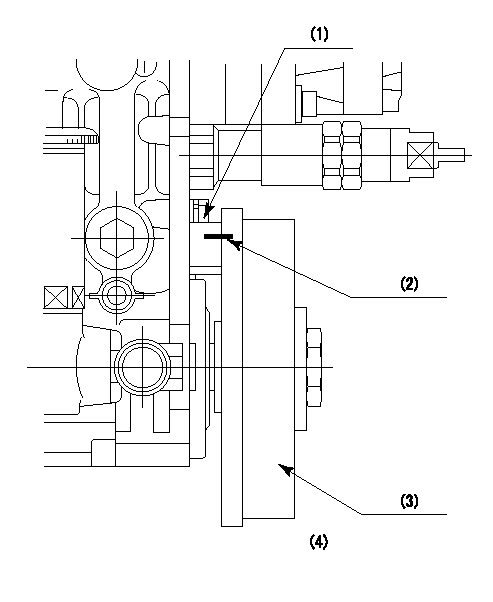
(1)Pointer
(2)Injection timing aligning mark
(3)Fly weight
(4)The actual shape and direction may be different from this illustration.
Operation sequence
1. Turn the prestroke actuator OFF.
2. Turn the camshaft as far as the No.1 cylinder's beginning of injection position.
3. Check that the pointer alignment mark of the injection pump and the alignment mark of the flywheel are matching.
4. If they are not matching, erase the alignment mark on the flywheel side, and stamp an alignment mark on the flywheel position that matches with the pointer side alignment mark.
5. Check again that the coupling's key groove position is in the No.1 cylinder's beginning of injection position.
----------
----------
----------
----------
0000001301
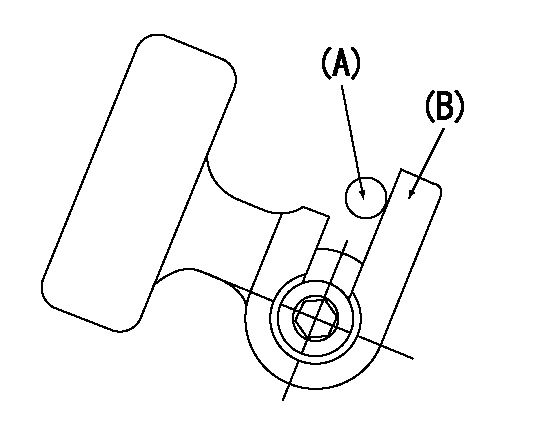
A : Stopper pin
B: Connector
----------
----------
----------
----------
0000001401
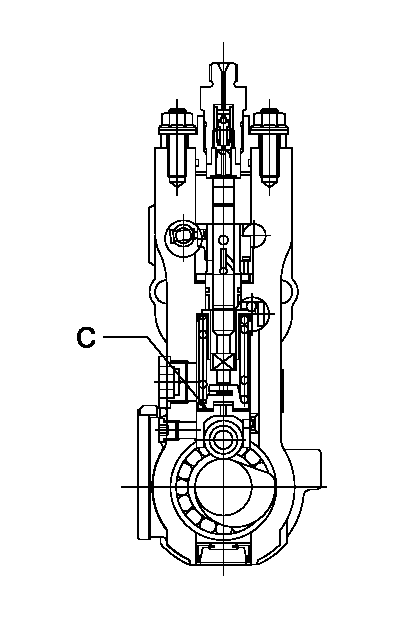
C:Shim
----------
----------
----------
----------
0000001501
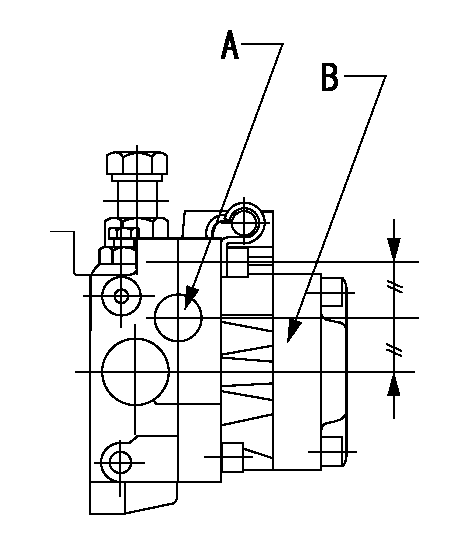
A:Sealing position
B:Pre-stroke actuator
1. When installing the pre-stroke actuator on the pump, first tighten the installation bolts loosely, then move the actuator fully clockwise (viewed from the drive side).
Temporary tightening torque: 1 - 1.5 N.m (0.1 - 0.15 kgf.m)
2. Move the actuator in the counterclockwise direction when viewed from the drive side, and adjust so that it becomes the adjustment point of the adjustment value. Then tighten it.
Tightening torque: 7^9 N.m (0.7^0.9 kgf.m)
3. After prestroke actuator installation adjustment, simultaneously stamp both the actuator side and housing side.
----------
----------
----------
----------
0000001701

(PWM) Pulse width modulation (%)
(R) Rack position (mm)
Rack sensor output characteristics
1. Rack limit adjustment
(1)Measure the rack position R2 for PWM a2%.
(2)Confirm that it is within the range R2 = 15+-1 mm.
(3)Measure the rack position R1 at PWM a %.
(4)Confirm that it is within the range R2 - R1 = 10+-0.1 mm.
2. Check the limp home operation.
(1)Move the switch box's limp home switch to the limp home side.
(2)Confirm rack position L1 (mm ) and L2 (mm) for PWM in the above table.
3. Check the pull down operation.
(1)Confirm that the rack position is 19 mm at PWM B%.
(2)In the conditions described in the above table, move the switch box's pull down switch to the pull down side and confirm that the rack position momentarily becomes 1 mm or less.
----------
a1=16.25% a2=72.5% L1=1--mm L2=19++mm A=5 % B=95%
----------
----------
a1=16.25% a2=72.5% L1=1--mm L2=19++mm A=5 % B=95%
----------
Information:
The Primary Engine Checks consist of quick and easy procedures that could identify the problem with a minimum loss of time. Always make these checks before starting the more involved troubleshooting procedures.Whenever a problem is found and corrected, always run the test again to that point to be sure there is not a combination of problems. When the problem has been corrected and the complaint resolved, stop the test. Do not continue through the complete procedure unless it is necessary. Possible Causes/CorrectionsPrestart Checks
Make sure the air filter elements are in good condition and are not plugged. Also, make sure the engine oil and coolant are at the correct levels.Check Accelerator Linkage
To check the linkage adjustment, push the pedal down until it hits the stop. If the linkage adjustment is correct, the governor linkage will move to the break-over position when the pedal is against the stop. This is shown by clearance on both sides of the tang (see the illustration). When there is clearance on both sides of the tang, the governor linkage is adjusted correctly to permit the engine to operate at high idle. If clearance is not present on both sides of the tang, adjust the governor linkage to give the needed clearance.
Governor Control Linkage Adjustment
(1) Clearance on both sides of tang. (2) Governor control linkage. (3) Pedal (full travel). (4) Governor control. (5) Lever assembly.Check Vehicle Tachometer
Install the 6V3121 Multitach Group. Start the engine and make sure that the vehicle tachometer is accurately indicating engine rpm. Some electric vehicle tachometers can be adjusted. Correct the tachometer as required. A bad tachometer can cause operation at the wrong engine rpm, this can give the feel of low power.Check For Air In The Fuel
Disconnect the fuel return line. With the engine in operation, let the fuel from the injection pump housing flow into a container. Look for air bubbles in the fuel coming from the return line. Approximately 5 to 100 visible air bubbles in the fuel is normal. If there is excessive air in the fuel find the cause and correct it. Such as checking all fuel lines and connections for leaks and repair or replacement of parts as needed.Check Fuel API Gravity Rating
Caterpillar diesel engines are set in production to produce rated power with a fuel of 35 API gravity (0.85 specific gravity). This limit provides a grade of fuel that aids engine starting and avoids vapor lock. Fuel with higher API gravities (i.e., lower specific gravities), will produce less horsepower at the factory power setting and vice versa for lower than 35 API gravity fuels. The engine fuel setting should not be adjusted to compensate for a power loss with fuels lighter than 35 as fuel system component life may be decreased.For more information see Special Instruction Form No. SEHS7067, Fuel Recommendations For Caterpillar Diesel Engines. Also, Special Instruction, Form No. SEHS6947 has fuel correction factors and tables.Check For Proper Fuel Heater Application
Make sure that fuel heaters are correctly used. In some cold climates,
Make sure the air filter elements are in good condition and are not plugged. Also, make sure the engine oil and coolant are at the correct levels.Check Accelerator Linkage
To check the linkage adjustment, push the pedal down until it hits the stop. If the linkage adjustment is correct, the governor linkage will move to the break-over position when the pedal is against the stop. This is shown by clearance on both sides of the tang (see the illustration). When there is clearance on both sides of the tang, the governor linkage is adjusted correctly to permit the engine to operate at high idle. If clearance is not present on both sides of the tang, adjust the governor linkage to give the needed clearance.
Governor Control Linkage Adjustment
(1) Clearance on both sides of tang. (2) Governor control linkage. (3) Pedal (full travel). (4) Governor control. (5) Lever assembly.Check Vehicle Tachometer
Install the 6V3121 Multitach Group. Start the engine and make sure that the vehicle tachometer is accurately indicating engine rpm. Some electric vehicle tachometers can be adjusted. Correct the tachometer as required. A bad tachometer can cause operation at the wrong engine rpm, this can give the feel of low power.Check For Air In The Fuel
Disconnect the fuel return line. With the engine in operation, let the fuel from the injection pump housing flow into a container. Look for air bubbles in the fuel coming from the return line. Approximately 5 to 100 visible air bubbles in the fuel is normal. If there is excessive air in the fuel find the cause and correct it. Such as checking all fuel lines and connections for leaks and repair or replacement of parts as needed.Check Fuel API Gravity Rating
Caterpillar diesel engines are set in production to produce rated power with a fuel of 35 API gravity (0.85 specific gravity). This limit provides a grade of fuel that aids engine starting and avoids vapor lock. Fuel with higher API gravities (i.e., lower specific gravities), will produce less horsepower at the factory power setting and vice versa for lower than 35 API gravity fuels. The engine fuel setting should not be adjusted to compensate for a power loss with fuels lighter than 35 as fuel system component life may be decreased.For more information see Special Instruction Form No. SEHS7067, Fuel Recommendations For Caterpillar Diesel Engines. Also, Special Instruction, Form No. SEHS6947 has fuel correction factors and tables.Check For Proper Fuel Heater Application
Make sure that fuel heaters are correctly used. In some cold climates,