Information injection-pump assembly
ZEXEL
107691-3251
1076913251
HINO
220401220B
220401220b

Rating:
Service parts 107691-3251 INJECTION-PUMP ASSEMBLY:
1.
_
7.
COUPLING PLATE
9.
_
11.
Nozzle and Holder
23600-3210C
12.
Open Pre:MPa(Kqf/cm2)
21.6{220}
15.
NOZZLE SET
Include in #1:
107691-3251
as INJECTION-PUMP ASSEMBLY
Cross reference number
ZEXEL
107691-3251
1076913251
HINO
220401220B
220401220b
Zexel num
Bosch num
Firm num
Name
Calibration Data:
Adjustment conditions
Test oil
1404 Test oil ISO4113 or {SAEJ967d}
1404 Test oil ISO4113 or {SAEJ967d}
Test oil temperature
degC
40
40
45
Nozzle and nozzle holder
105780-8250
Bosch type code
1 688 901 101
Nozzle
105780-0120
Bosch type code
1 688 901 990
Nozzle holder
105780-2190
Opening pressure
MPa
20.7
Opening pressure
kgf/cm2
211
Injection pipe
Outer diameter - inner diameter - length (mm) mm 8-3-600
Outer diameter - inner diameter - length (mm) mm 8-3-600
Overflow valve
131425-0920
Overflow valve opening pressure
kPa
255
221
289
Overflow valve opening pressure
kgf/cm2
2.6
2.25
2.95
Tester oil delivery pressure
kPa
255
255
255
Tester oil delivery pressure
kgf/cm2
2.6
2.6
2.6
PS/ACT control unit part no.
407980-2
24*
Digi switch no.
17
Direction of rotation (viewed from drive side)
Left L
Left L
Injection timing adjustment
Direction of rotation (viewed from drive side)
Left L
Left L
Injection order
1-4-2-6-
3-5
Pre-stroke
mm
5.1
5.07
5.13
Beginning of injection position
Governor side NO.1
Governor side NO.1
Difference between angles 1
Cal 1-4 deg. 60 59.75 60.25
Cal 1-4 deg. 60 59.75 60.25
Difference between angles 2
Cyl.1-2 deg. 120 119.75 120.25
Cyl.1-2 deg. 120 119.75 120.25
Difference between angles 3
Cal 1-6 deg. 180 179.75 180.25
Cal 1-6 deg. 180 179.75 180.25
Difference between angles 4
Cal 1-3 deg. 240 239.75 240.25
Cal 1-3 deg. 240 239.75 240.25
Difference between angles 5
Cal 1-5 deg. 300 299.75 300.25
Cal 1-5 deg. 300 299.75 300.25
Injection quantity adjustment
Adjusting point
-
Rack position
10.6
Pump speed
r/min
750
750
750
Average injection quantity
mm3/st.
101
98
104
Max. variation between cylinders
%
0
-2
2
Basic
*
Fixing the rack
*
PS407980-224*
V
2.25+-0.
01
PS407980-224*
mm
3.1+-0.0
5
Standard for adjustment of the maximum variation between cylinders
*
Injection quantity adjustment_02
Adjusting point
Z
Rack position
6.1+-0.5
Pump speed
r/min
455
455
455
Average injection quantity
mm3/st.
8
7
9
Max. variation between cylinders
%
0
-15
15
Fixing the rack
*
PS407980-224*
V
V1+0.05+
-0.01
PS407980-224*
mm
5+-0.03
Standard for adjustment of the maximum variation between cylinders
*
Remarks
Refer to items regarding the pre-stroke actuator
Refer to items regarding the pre-stroke actuator
Injection quantity adjustment_03
Adjusting point
A
Rack position
R1(10.6)
Pump speed
r/min
750
750
750
Average injection quantity
mm3/st.
101
99
103
Basic
*
Fixing the lever
*
Boost pressure
kPa
61.3
61.3
Boost pressure
mmHg
460
460
PS407980-224*
V
2.25+-0.
01
PS407980-224*
mm
3.1+-0.0
5
Injection quantity adjustment_04
Adjusting point
B
Rack position
R1+2
Pump speed
r/min
1250
1250
1250
Average injection quantity
mm3/st.
108.5
102.5
114.5
Fixing the lever
*
Boost pressure
kPa
61.3
61.3
Boost pressure
mmHg
460
460
PS407980-224*
V
2.25+-0.
01
PS407980-224*
mm
3.1+-0.0
5
Injection quantity adjustment_05
Adjusting point
C
Rack position
R2-0.25
Pump speed
r/min
350
350
350
Average injection quantity
mm3/st.
81.5
75.5
87.5
Fixing the lever
*
Boost pressure
kPa
0
0
0
Boost pressure
mmHg
0
0
0
PS407980-224*
V
2.25+-0.
01
PS407980-224*
mm
3.1+-0.0
5
Boost compensator adjustment
Pump speed
r/min
350
350
350
Rack position
R2-0.25
Boost pressure
kPa
42.7
41.4
44
Boost pressure
mmHg
320
310
330
Boost compensator adjustment_02
Pump speed
r/min
350
350
350
Rack position
R2(R1-1.
35)
Boost pressure
kPa
48
48
48
Boost pressure
mmHg
360
360
360
Timer adjustment
Pump speed
r/min
0
Advance angle
deg.
0
0
0
Timer adjustment_02
Pump speed
r/min
-
Advance angle
deg.
0
0
0
Remarks
Measure speed (beginning of operation).
Measure speed (beginning of operation).
Timer adjustment_03
Pump speed
r/min
-
Advance angle
deg.
-1.5
-1.8
-1.2
Remarks
Measure the actual speed, stop
Measure the actual speed, stop
0000001601
CU407980-224*
*
Actuator retarding type
*
Supply voltage
V
24
23.5
24.5
Ambient temperature
degC
23
18
28
Pre-stroke
mm
2
1.95
2.05
Output voltage
V
2.83
2.82
2.84
Adjustment
*
_02
CU407980-224*
*
Supply voltage
V
24
23.5
24.5
Ambient temperature
degC
23
18
28
Pre-stroke
mm
5.1
5.07
5.13
Output voltage
V
1.2
1
1.4
Confirmation
*
Remarks
Output voltage V1
Output voltage V1
_03
CU407980-224*
*
Supply voltage
V
24
23.5
24.5
Ambient temperature
degC
23
18
28
Output voltage
V
3.05
3.05
Confirmation of operating range
*
Test data Ex:
Governor adjustment
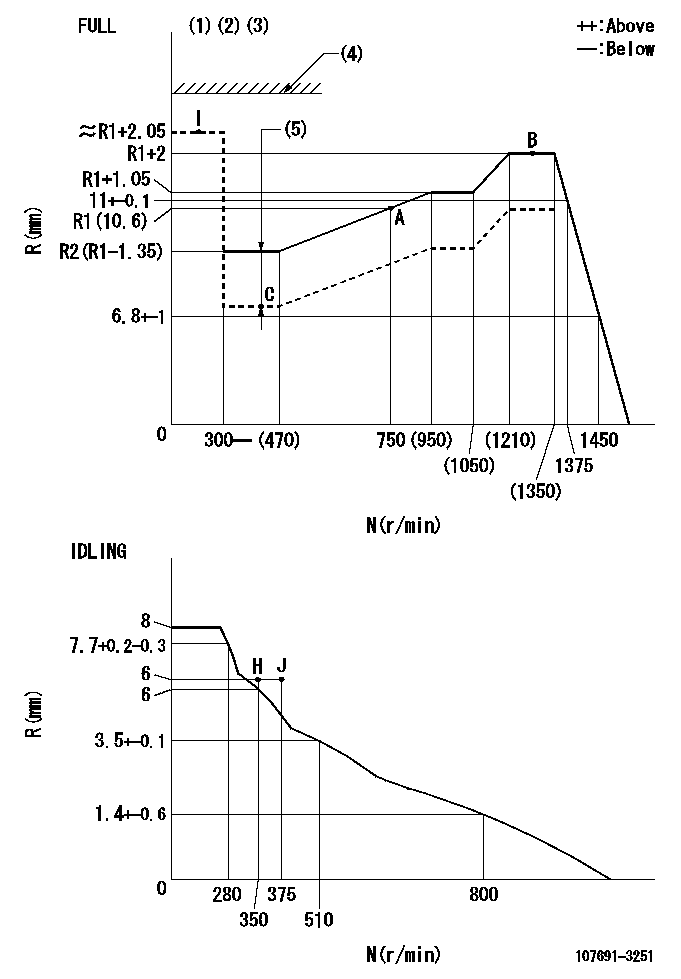
N:Pump speed
R:Rack position (mm)
(1)Torque cam stamping: T1
(2)Tolerance for racks not indicated: +-0.05mm.
(3)When setting the stop lever after governor adjustment, confirm that rack position Ra (point B) can be obtained at the full setting.
(4)Stop lever's normal position setting: RA
(5)Boost compensator stroke: BCL
----------
T1=AF00 Ra=R1+2mm RA=(18)mm BCL=0.25+-0.1mm
----------
----------
T1=AF00 Ra=R1+2mm RA=(18)mm BCL=0.25+-0.1mm
----------
Speed control lever angle

F:Full speed
I:Idle
(1)Use the hole at R = aa
(2)Stopper bolt set position 'H'
----------
aa=39.5mm
----------
a=32deg+-5deg b=37deg+-3deg
----------
aa=39.5mm
----------
a=32deg+-5deg b=37deg+-3deg
Stop lever angle
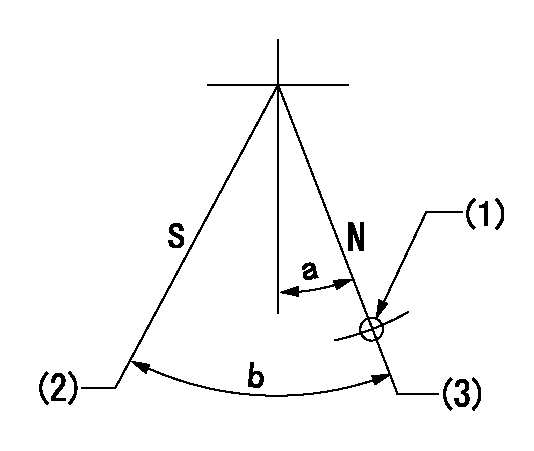
N:Pump normal
S:Stop the pump.
(1)Use the hole at R = aa
(2)Speed = bb, rack position = cc
(3)Position at the normal side lever position (back off the stop screw and move fully to the normal side). Next, screw in the stop screw and set where it contacts the stop lever.
----------
aa=28mm bb=0r/min cc=1.5+-0.1mm
----------
a=15deg+-5deg b=40deg+-5deg
----------
aa=28mm bb=0r/min cc=1.5+-0.1mm
----------
a=15deg+-5deg b=40deg+-5deg
0000001301
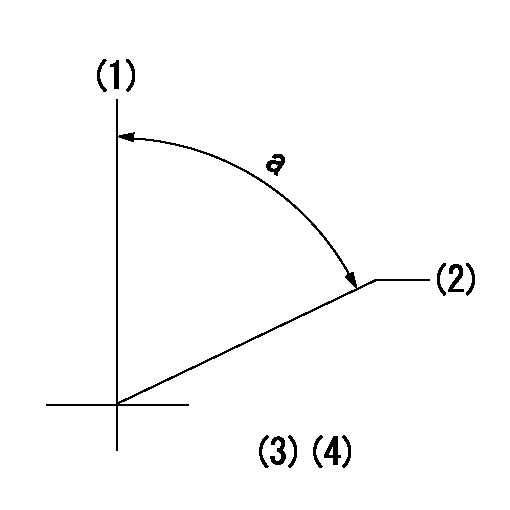
(1)Pump vertical direction
(2)Coupling's key groove position at No 1 cylinder's beginning of injection
(3)Pre-stroke: aa
(4)-
----------
aa=5.1+-0.03mm
----------
a=(80deg)
----------
aa=5.1+-0.03mm
----------
a=(80deg)
0000001401
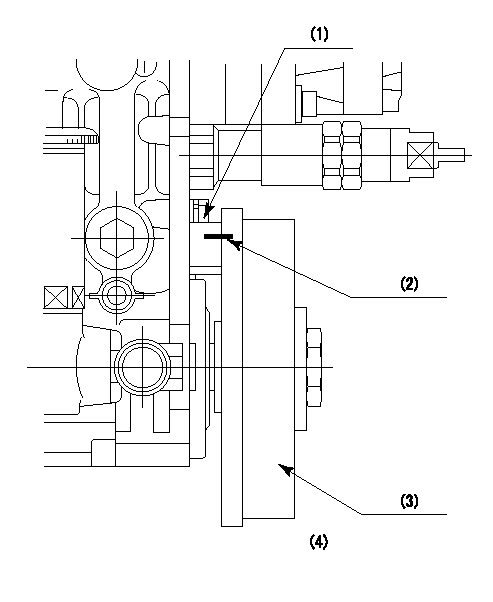
(1)Pointer
(2)Injection timing aligning mark
(3)Fly weight
(4)The actual shape and direction may be different from this illustration.
Operation sequence
1. Turn the prestroke actuator OFF.
2. Turn the camshaft as far as the No.1 cylinder's beginning of injection position.
3. Check that the pointer alignment mark of the injection pump and the alignment mark of the flywheel are matching.
4. If they are not matching, erase the alignment mark on the flywheel side, and stamp an alignment mark on the flywheel position that matches with the pointer side alignment mark.
5. Check again that the coupling's key groove position is in the No.1 cylinder's beginning of injection position.
----------
----------
----------
----------
0000001701
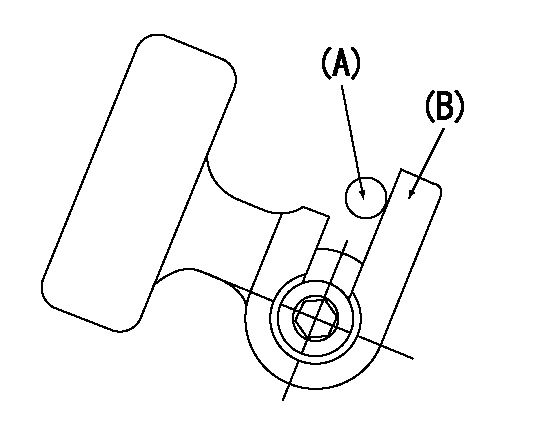
A : Stopper pin
B: Connector
----------
----------
----------
----------
0000001801
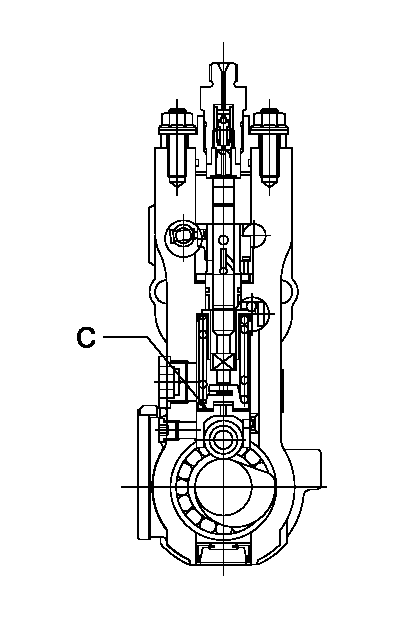
C:Shim
----------
----------
----------
----------
0000001901
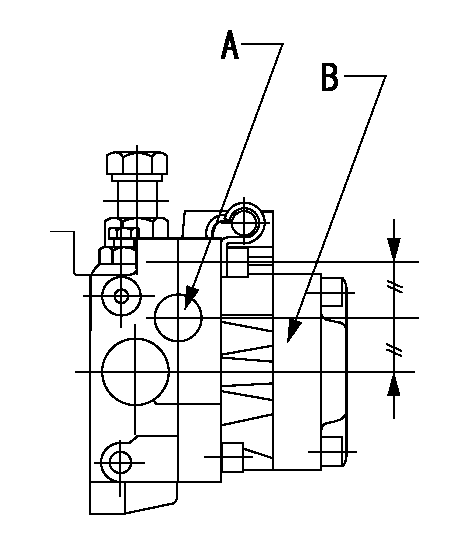
A:Sealing position
B:Pre-stroke actuator
1. When installing the pre-stroke actuator on the pump, first tighten the installation bolts loosely, then move the actuator fully clockwise (viewed from the drive side).
Temporary tightening torque: 1 - 1.5 N.m (0.1 - 0.15 kgf.m)
2. Move the actuator in the counterclockwise direction when viewed from the drive side, and adjust so that it becomes the adjustment point of the adjustment value. Then tighten it.
Tightening torque: 7^9 N.m (0.7^0.9 kgf.m)
3. After prestroke actuator installation adjustment, simultaneously stamp both the actuator side and housing side.
----------
----------
----------
----------
0000002201 RACK SENSOR
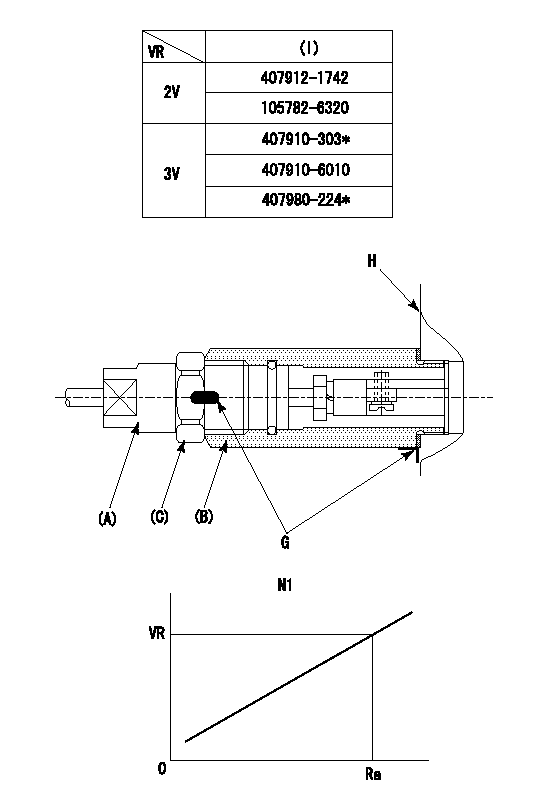
(VR) measurement voltage
(I) Part number of the control unit
(G) Apply red paint.
(H): End surface of the pump
1. Rack sensor adjustment (-0620)
(1)Fix the speed control lever at the full position
(2)Set the speed to N1 r/min.
(If the boost compensator is provided, apply boost pressure.)
(3)Adjust the bobbin (A) so that the rack sensor's output voltage is VR+-0.01.
(4)At that time, rack position must be Ra.
(5)Apply G at two places.
Connecting part between the joint (B) and the nut (F)
Connecting part between the joint (B) and the end surface of the pump (H)
----------
N1=1250r/min Ra=R1(10.6)+2mm
----------
----------
N1=1250r/min Ra=R1(10.6)+2mm
----------
Information:
FEED ENGAGED
21. Slot. 22. Pin. 23. Knob. To set the feed mechanism into feed on later units, turn lever (A) up (the direction of arrow).
LATER FEED MECHANISM
A. Lever.Place adapter (24) into boring bar and tighten setscrew (25).
ADAPTER INSTALLED
24. 1P2364 Adapter. 25. Setscrew.Apply layout bluing to the bearing cap and bearing bore. Oil the centering rings. Do not use lubricant on the cutter. Use a one-half inch electric drill with universal joint (26) to feed tool through the bore. Service main bearings with .010 in. (0.25 mm) oversize outside diameter are available to permit the bore to be bored oversize. Bore the bore to 3.7175 .0005 in. (94.425 0.013 mm).
BORING BEARING BORE
26. 1P2363 Universal. If you use the later feed mechanism, the tool can be driven from either the boring bar or the feed mechanism.
DRIVING THROUGH FEED MECHANISM (Typical Example)
26. 1P2363 Universal.The bluing applied to the bearing bore indicates the condition of the bore at the correct bore size. If bluing shows an out of round condition, check the largest diameter (indicated by remaining bluing) in relation to the smallest diameter (indicated by lack of bluing). The difference of the two must not exceed .0010 in. (0.025 mm).If bluing indicates a step in the joint face, measure the diameter at the step in relation to the smallest diameter. A step of .0005 in. (0.013 mm) on one or both sides is permissible. A maximum of .0010 in. (0.025 mm) over the nominal finish bore diameter is permissible if within the described limits.To check the bore diameter, set the 1P3535 Dial Bore Gauge to 3.7175 in. (94.425 mm).
CHECKING BORE (Typical Example)Line Boring Main Bearing Bores
Line bore all main bearing bores if bearing caps or saddles are distorted.Clean bearing caps and saddles. Remove all nicks from pan rail. Plug oil holes in block with grease to prevent chips from entering oil passages.Place 1P2344 Centering Rings (1), with oiler (2) up, at each end of block. If an end bore is distorted, use the next good bore. There must be two good bores for locating centering rings.
CENTERING RINGS IN BLOCK
1. 1P2344 Centering Rings. 2. Oiler.Place original bearing caps (4) over the centering rings (1). Tighten bolts (3) hand tight.
CENTERING RINGS INSTALLED
1. 1P2344 Centering Rings. 3. Bolts (four). 4. Bearing caps.
BORING BAR INSTALLED
1. 1P2344 Centering Rings. 3. Bolts (four). 5. 1P2352 Boring Bar.Oil boring bar (5) and insert it through centering rings (1). Tighten bolts (3) to a minimum of 20 lb. ft. (25 N m) and a maximum of 50 lb. ft. (70 N m) while spinning boring bar (5) to check for binding. Centering rings (1) must be seated in bearing saddles after tightening.Slide boring bar (5) out of one end of block and install bearing assemblies (6) on boring bar (5). Slide boring bar (5) back through centering ring. Adjust bearing by tightening bolt (7) until bar begins to bind, then back off until boring bar (5) spins easily.
INSTALLING BEARING ASSEMBLIES
5. 1P2352 Boring Bar. 6. 1P2373 Bearing assembly