Information injection-pump assembly
BOSCH
9 400 618 938
9400618938
ZEXEL
107691-2740
1076912740
MITSUBISHI
ME170420
me170420
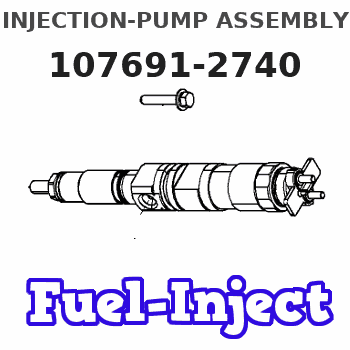
Rating:
Cross reference number
BOSCH
9 400 618 938
9400618938
ZEXEL
107691-2740
1076912740
MITSUBISHI
ME170420
me170420
Zexel num
Bosch num
Firm num
Name
107691-2740
9 400 618 938
ME170420 MITSUBISHI
INJECTION-PUMP ASSEMBLY
6D17-1 K 14CG INJECTION PUMP ASSY TICS MD-TI6 TICS
6D17-1 K 14CG INJECTION PUMP ASSY TICS MD-TI6 TICS
Calibration Data:
Adjustment conditions
Test oil
1404 Test oil ISO4113 or {SAEJ967d}
1404 Test oil ISO4113 or {SAEJ967d}
Test oil temperature
degC
40
40
45
Nozzle and nozzle holder
105780-8250
Bosch type code
1 688 901 101
Nozzle
105780-0120
Bosch type code
1 688 901 990
Nozzle holder
105780-2190
Opening pressure
MPa
20.7
Opening pressure
kgf/cm2
211
Injection pipe
Outer diameter - inner diameter - length (mm) mm 8-3-600
Outer diameter - inner diameter - length (mm) mm 8-3-600
Overflow valve
131424-8420
Overflow valve opening pressure
kPa
255
221
289
Overflow valve opening pressure
kgf/cm2
2.6
2.25
2.95
Tester oil delivery pressure
kPa
255
255
255
Tester oil delivery pressure
kgf/cm2
2.6
2.6
2.6
PS/ACT control unit part no.
407980-2
24*
Digi switch no.
17
Direction of rotation (viewed from drive side)
Left L
Left L
Injection timing adjustment
Direction of rotation (viewed from drive side)
Left L
Left L
Injection order
1-5-3-6-
2-4
Pre-stroke
mm
5.6
5.57
5.63
Beginning of injection position
Governor side NO.1
Governor side NO.1
Difference between angles 1
Cal 1-5 deg. 60 59.75 60.25
Cal 1-5 deg. 60 59.75 60.25
Difference between angles 2
Cal 1-3 deg. 120 119.75 120.25
Cal 1-3 deg. 120 119.75 120.25
Difference between angles 3
Cal 1-6 deg. 180 179.75 180.25
Cal 1-6 deg. 180 179.75 180.25
Difference between angles 4
Cyl.1-2 deg. 240 239.75 240.25
Cyl.1-2 deg. 240 239.75 240.25
Difference between angles 5
Cal 1-4 deg. 300 299.75 300.25
Cal 1-4 deg. 300 299.75 300.25
Injection quantity adjustment
Adjusting point
-
Rack position
11.7
Pump speed
r/min
850
850
850
Average injection quantity
mm3/st.
105
103
107
Max. variation between cylinders
%
0
-3
3
Basic
*
Fixing the rack
*
PS407980-224*
V
2.25+-0.
01
PS407980-224*
mm
3.6+-0.0
5
Standard for adjustment of the maximum variation between cylinders
*
Injection quantity adjustment_02
Adjusting point
Z
Rack position
8+-0.5
Pump speed
r/min
430
430
430
Average injection quantity
mm3/st.
10
8.2
11.8
Max. variation between cylinders
%
0
-15
15
Fixing the rack
*
PS407980-224*
V
V1+0.05+
-0.01
PS407980-224*
mm
5.5+-0.0
3
Standard for adjustment of the maximum variation between cylinders
*
Remarks
Refer to items regarding the pre-stroke actuator
Refer to items regarding the pre-stroke actuator
Injection quantity adjustment_03
Adjusting point
A
Rack position
R1(11.7)
Pump speed
r/min
850
850
850
Average injection quantity
mm3/st.
105
104
106
Basic
*
Fixing the lever
*
PS407980-224*
V
2.25+-0.
01
PS407980-224*
mm
3.6+-0.0
5
Injection quantity adjustment_04
Adjusting point
B
Rack position
R1+1.2
Pump speed
r/min
1450
1450
1450
Average injection quantity
mm3/st.
104
100
108
Fixing the lever
*
PS407980-224*
V
2.25+-0.
01
PS407980-224*
mm
3.6+-0.0
5
Injection quantity adjustment_05
Adjusting point
C
Rack position
R1-1.2
Pump speed
r/min
500
500
500
Average injection quantity
mm3/st.
88.5
84.5
92.5
Fixing the lever
*
PS407980-224*
V
2.25+-0.
01
PS407980-224*
mm
3.6+-0.0
5
Timer adjustment
Pump speed
r/min
1250--
Advance angle
deg.
0
0
0
Remarks
Start
Start
Timer adjustment_02
Pump speed
r/min
1200
Advance angle
deg.
0.5
Timer adjustment_03
Pump speed
r/min
1470
Advance angle
deg.
3
2.5
3.5
Remarks
Finish
Finish
0000001601
CU407980-224*
*
Actuator retarding type
*
Supply voltage
V
24
23.5
24.5
Ambient temperature
degC
23
18
28
Pre-stroke
mm
2.5
2.45
2.55
Output voltage
V
2.83
2.82
2.84
Adjustment
*
_02
CU407980-224*
*
Supply voltage
V
24
23.5
24.5
Ambient temperature
degC
23
18
28
Pre-stroke
mm
5.6
5.57
5.63
Output voltage
V
1.2
1
1.4
Confirmation
*
Remarks
Output voltage V1
Output voltage V1
_03
CU407980-224*
*
Supply voltage
V
24
23.5
24.5
Ambient temperature
degC
23
18
28
Output voltage
V
3.05
3.05
Confirmation of operating range
*
Test data Ex:
Governor adjustment
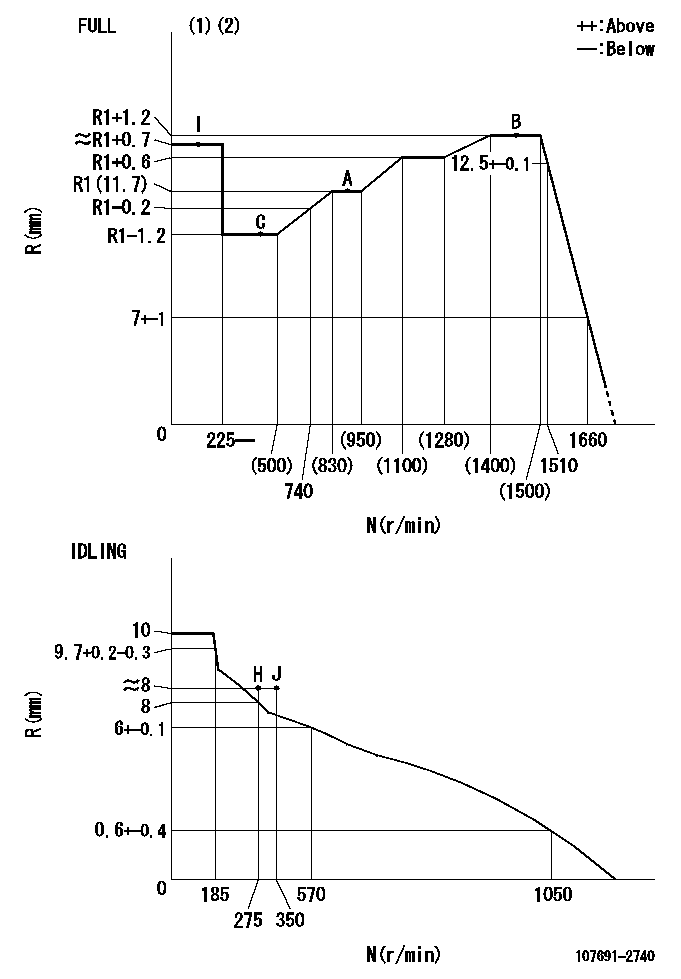
N:Pump speed
R:Rack position (mm)
(1)Torque cam stamping: T1
(2)Tolerance for racks not indicated: +-0.05mm.
----------
T1=AE44
----------
----------
T1=AE44
----------
Speed control lever angle
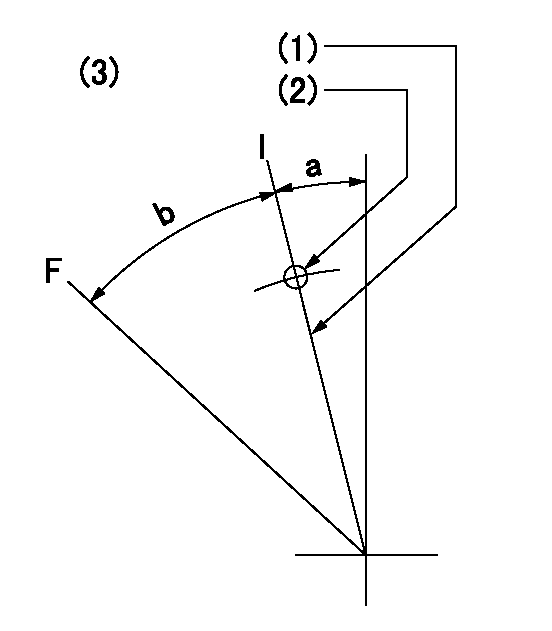
F:Full speed
I:Idle
(1)Stopper bolt set position 'H'
(2)Use the hole at R = aa
(3)Accelerator lever
----------
aa=38mm
----------
a=29deg+-5deg b=42deg+-3deg
----------
aa=38mm
----------
a=29deg+-5deg b=42deg+-3deg
Stop lever angle
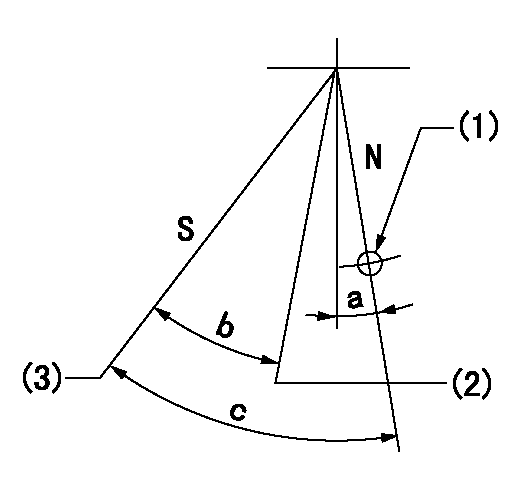
N:Pump normal
S:Stop the pump.
(1)Use the hole at R = aa
(2)Normal engine position (Rack position corresponding to bb)
(3)Set the stopper bolt at rack position = cc and speed = dd and confirm non-injection
----------
aa=47mm bb=17.4mm cc=3.5+-0.3mm dd=0r/min
----------
a=4deg+-5deg b=(31deg) c=41deg+-5deg
----------
aa=47mm bb=17.4mm cc=3.5+-0.3mm dd=0r/min
----------
a=4deg+-5deg b=(31deg) c=41deg+-5deg
0000001301

(1)Pump vertical direction
(2)Coupling's key groove position at No 1 cylinder's beginning of injection
(3)B.T.D.C.: aa
(4)Pre-stroke: bb
----------
aa=5deg bb=5.6+-0.03mm
----------
a=(0deg)
----------
aa=5deg bb=5.6+-0.03mm
----------
a=(0deg)
0000001401
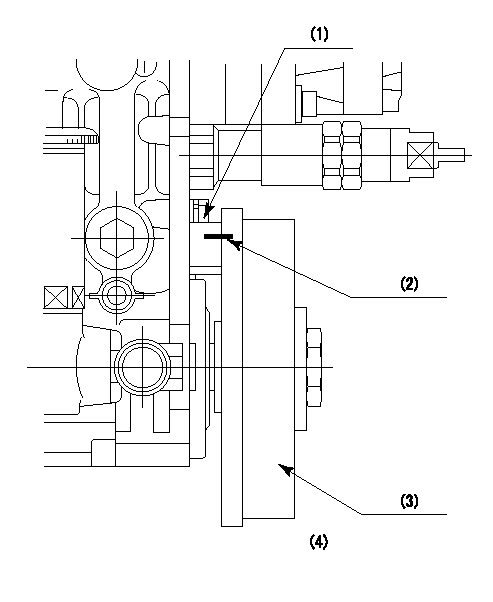
(1)Pointer
(2)Injection timing aligning mark
(3)Fly weight
(4)The actual shape and direction may be different from this illustration.
Operation sequence
1. Turn the prestroke actuator OFF.
2. Turn the camshaft as far as the No.1 cylinder's beginning of injection position.
3. Check that the pointer alignment mark of the injection pump and the alignment mark of the flywheel are matching.
4. If they are not matching, erase the alignment mark on the flywheel side, and stamp an alignment mark on the flywheel position that matches with the pointer side alignment mark.
5. Check again that the coupling's key groove position is in the No.1 cylinder's beginning of injection position.
----------
----------
----------
----------
0000001701
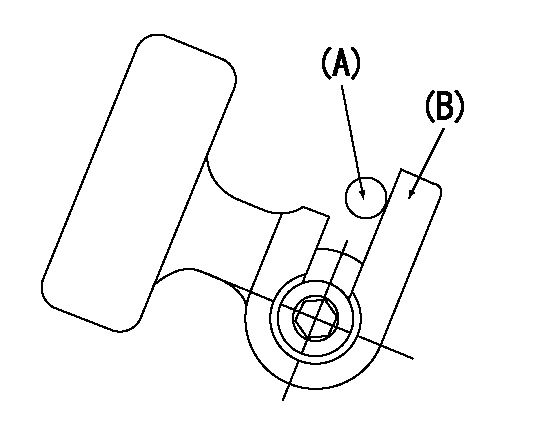
A : Stopper pin
B: Connector
----------
----------
----------
----------
0000001801
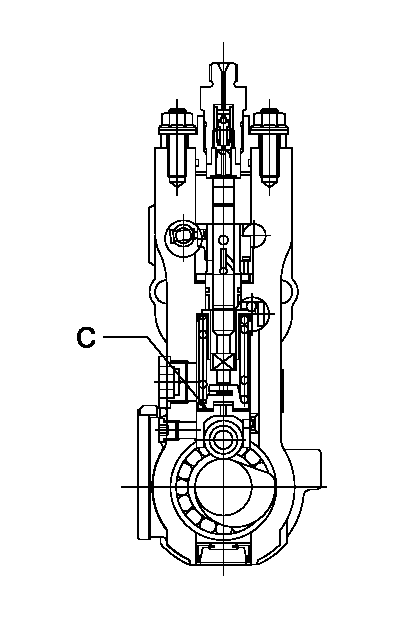
C:Shim
----------
----------
----------
----------
0000001901
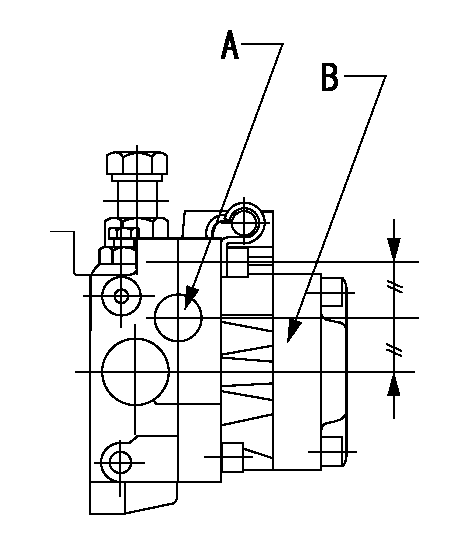
A:Sealing position
B:Pre-stroke actuator
1. When installing the pre-stroke actuator on the pump, first tighten the installation bolts loosely, then move the actuator fully clockwise (viewed from the drive side).
Temporary tightening torque: 1 - 1.5 N.m (0.1 - 0.15 kgf.m)
2. Move the actuator in the counterclockwise direction when viewed from the drive side, and adjust so that it becomes the adjustment point of the adjustment value. Then tighten it.
Tightening torque: 7^9 N.m (0.7^0.9 kgf.m)
3. After prestroke actuator installation adjustment, simultaneously stamp both the actuator side and housing side.
----------
----------
----------
----------
0000002201 RACK SENSOR
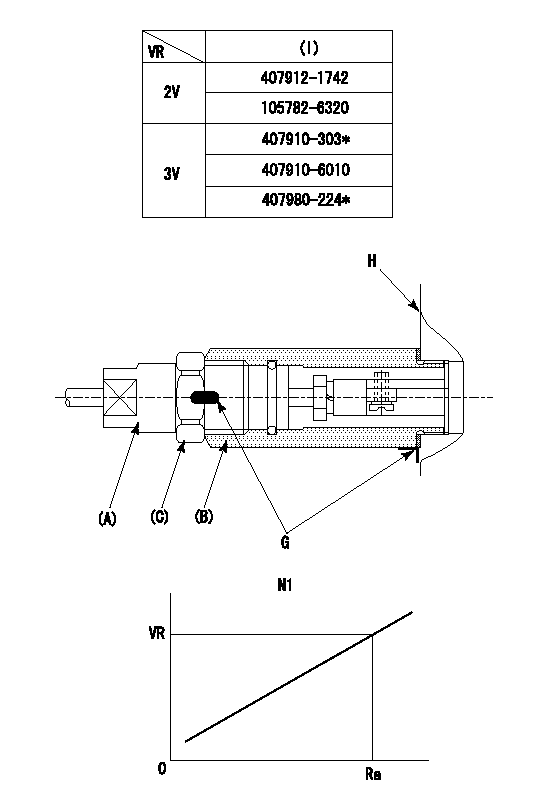
(VR) measurement voltage
(I) Part number of the control unit
(G) Apply red paint.
(H): End surface of the pump
1. Rack sensor adjustment (-0620)
(1)Fix the speed control lever at the full position
(2)Set the speed to N1 r/min.
(If the boost compensator is provided, apply boost pressure.)
(3)Adjust the bobbin (A) so that the rack sensor's output voltage is VR+-0.01.
(4)At that time, rack position must be Ra.
(5)Apply G at two places.
Connecting part between the joint (B) and the nut (F)
Connecting part between the joint (B) and the end surface of the pump (H)
----------
N1=1450r/min Ra=R1(11.7)+1.2mm
----------
----------
N1=1450r/min Ra=R1(11.7)+1.2mm
----------
0000002301 SPEED SENSOR

(A) Flyweight projection
(B) Pickup sensor
(c) Lock nut
Speed sensor installation
(1)Install the speed sensor so that the clearance between the sensor and the flyweight projection is L.
(This gap is the gap when the pickup sensor is returned 1 turn from where it contacts the flyweight tooth.)
----------
L=0.8~1mm
----------
----------
L=0.8~1mm
----------
Information:
1. Fuel consumption records must be available before the high fuel consumption complaint can be verified. If symptoms indicate low power, then the low power test should be conducted first, because it could be the cause of the fuel consumption problem. This Primary Engine Test for High Fuel Consumption is the same as the Primary Engine Test for Low Power.2. Visually inspect the fuel system from the fuel tank to the fuel injection lines to see if there are any indications of fuel leaks. Tighten any loose connections found and, if necessary, replace lines that can not be repaired.3. Check the crankcase oil level and the coolant level of the radiator. Remove the boost air line from the AFRC (air-fuel ratio control) during the Primary Engine Test. This will prevent the AFRC from becoming pnuematically activated during the checks. If activated, the AFRC could give an indication of a problem when there is none.4. A slightly lower rpm (15 rpm below low limit) should be expected for the engine in vehicle than the rpm shown in the RACK SETTING INFORMATION. This is caused by the parasitic loads of the engine accessories involved.5. With the engine running, the throttle must have enough travel for the governor control lever to break over (go past the normal governor stop for high idle position) a small amount when the throttle pedal is fully depressed. If full travel is not available, disconnect throttle linkage from governor lever. With throttle linkage disconnected, full travel of governor lever will indicate linkage problems, and the linkage will have to be adjusted. Limited travel of the governor lever will indicate a problem within the governor.6. Only a mechanic with the correct training should change the high idle setting. The procedure is given in this Service Manual under the subject GOVERNOR ADJUSTMENTS.7. If high idle rpm can not be made correct with the high idle adjustment screw, there is a problem inside the governor. Disassemble the governor and check for damaged parts or wrong parts installed in the governor. Some common problems are worn bushings, worn spring seat, or a broken or wrong governor spring.8. Before 8S4627 Circuit Tester is installed, be sure to test the light for correct operation. Test light must come on when the clip of the wire is placed against the probe of the light (replace batteries or bulb if light does not come on). If light comes on and stays on when attached to governor, the insulation is bad or installed wrong in torque spring group or brass terminal. This must be corrected before test is performed.9. With the continuity light installed, quickly push accelerator pedal all the way to the floor. If the fuel control shaft and governor function properly, the continuity light will come on during this free acceleration until high idle is maintained. If the light comes on, this is an indication that the mechanical movement of the governor and fuel injection pump parts operate properly. The vehicle will
Have questions with 107691-2740?
Group cross 107691-2740 ZEXEL
Mitsubishi
Mitsubishi
107691-2740
9 400 618 938
ME170420
INJECTION-PUMP ASSEMBLY
6D17-1
6D17-1