Information injection-pump assembly
ZEXEL
107691-2312
1076912312
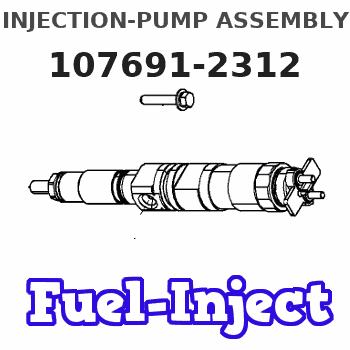
Rating:
Cross reference number
ZEXEL
107691-2312
1076912312
Zexel num
Bosch num
Firm num
Name
107691-2312
INJECTION-PUMP ASSEMBLY
Calibration Data:
Adjustment conditions
Test oil
1404 Test oil ISO4113 or {SAEJ967d}
1404 Test oil ISO4113 or {SAEJ967d}
Test oil temperature
degC
40
40
45
Nozzle and nozzle holder
105780-8250
Bosch type code
1 688 901 101
Nozzle
105780-0120
Bosch type code
1 688 901 990
Nozzle holder
105780-2190
Opening pressure
MPa
20.7
Opening pressure
kgf/cm2
211
Injection pipe
Outer diameter - inner diameter - length (mm) mm 8-3-600
Outer diameter - inner diameter - length (mm) mm 8-3-600
Overflow valve
131425-0520
Overflow valve opening pressure
kPa
255
221
289
Overflow valve opening pressure
kgf/cm2
2.6
2.25
2.95
Tester oil delivery pressure
kPa
255
255
255
Tester oil delivery pressure
kgf/cm2
2.6
2.6
2.6
PS/ACT control unit part no.
407910-3
03*
Selector switch no.
03
PS/ACT control unit part no.
407980-2
24*
Digi switch no.
16
Direction of rotation (viewed from drive side)
Left L
Left L
Injection timing adjustment
Direction of rotation (viewed from drive side)
Left L
Left L
Injection order
1-5-3-6-
2-4
Pre-stroke
mm
5.6
5.57
5.63
Beginning of injection position
Governor side NO.1
Governor side NO.1
Difference between angles 1
Cal 1-5 deg. 60 59.75 60.25
Cal 1-5 deg. 60 59.75 60.25
Difference between angles 2
Cal 1-3 deg. 120 119.75 120.25
Cal 1-3 deg. 120 119.75 120.25
Difference between angles 3
Cal 1-6 deg. 180 179.75 180.25
Cal 1-6 deg. 180 179.75 180.25
Difference between angles 4
Cyl.1-2 deg. 240 239.75 240.25
Cyl.1-2 deg. 240 239.75 240.25
Difference between angles 5
Cal 1-4 deg. 300 299.75 300.25
Cal 1-4 deg. 300 299.75 300.25
Injection quantity adjustment
Adjusting point
-
Rack position
12.3
Pump speed
r/min
800
800
800
Average injection quantity
mm3/st.
127
125.4
128.6
Max. variation between cylinders
%
0
-3
3
Basic
*
Fixing the rack
*
PS407980-224*
V
2.25+-0.
01
PS407980-224*
mm
3.6+-0.0
5
PS407910-303*
V
1.75+-0.
01
PS407910-303*
mm
3.6+-0.0
5
Standard for adjustment of the maximum variation between cylinders
*
Injection quantity adjustment_02
Adjusting point
Z
Rack position
7.4+-0.5
Pump speed
r/min
425
425
425
Average injection quantity
mm3/st.
16.5
14.7
18.3
Max. variation between cylinders
%
0
-15
15
Fixing the rack
*
PS407980-224*
V
V1+0.05+
-0.01
PS407980-224*
mm
5.5+-0.0
3
PS407910-303*
V
V1-0.05+
-0.01
PS407910-303*
mm
5.5+-0.0
3
Standard for adjustment of the maximum variation between cylinders
*
Remarks
Refer to items regarding the pre-stroke actuator
Refer to items regarding the pre-stroke actuator
Injection quantity adjustment_03
Adjusting point
A
Rack position
R1(12.3)
Pump speed
r/min
800
800
800
Average injection quantity
mm3/st.
127
126
128
Basic
*
Fixing the lever
*
Boost pressure
kPa
40
40
Boost pressure
mmHg
300
300
PS407980-224*
V
2.25+-0.
01
PS407980-224*
mm
3.6+-0.0
5
PS407910-303*
V
1.75+-0.
01
PS407910-303*
mm
3.6+-0.0
5
Injection quantity adjustment_04
Adjusting point
B
Rack position
R1+1.5
Pump speed
r/min
1300
1300
1300
Average injection quantity
mm3/st.
129
125
133
Fixing the lever
*
Boost pressure
kPa
40
40
Boost pressure
mmHg
300
300
PS407980-224*
V
2.25+-0.
01
PS407980-224*
mm
3.6+-0.0
5
PS407910-303*
V
1.75+-0.
01
PS407910-303*
mm
3.6+-0.0
5
Injection quantity adjustment_05
Adjusting point
C
Rack position
(R2-1.25
)
Pump speed
r/min
400
400
400
Average injection quantity
mm3/st.
87.5
85.5
89.5
Fixing the lever
*
Boost pressure
kPa
0
0
0
Boost pressure
mmHg
0
0
0
PS407980-224*
V
2.25+-0.
01
PS407980-224*
mm
3.6+-0.0
5
PS407910-303*
V
1.75+-0.
01
PS407910-303*
mm
3.6+-0.0
5
Boost compensator adjustment
Pump speed
r/min
300
300
300
Rack position
(R2-1.25
)
Boost pressure
kPa
13.3
12
14.6
Boost pressure
mmHg
100
90
110
Boost compensator adjustment_02
Pump speed
r/min
300
300
300
Rack position
R2(R1-1)
Boost pressure
kPa
26.7
26.7
26.7
Boost pressure
mmHg
200
200
200
Timer adjustment
Pump speed
r/min
1050--
Advance angle
deg.
0
0
0
Remarks
Start
Start
Timer adjustment_02
Pump speed
r/min
1000
Advance angle
deg.
0
-0.5
0
Timer adjustment_03
Pump speed
r/min
1075
Advance angle
deg.
-1.5
-2
-1
Remarks
Finish
Finish
0000001601
CU407980-224*
*
Actuator retarding type
*
Supply voltage
V
12
11.5
12.5
Ambient temperature
degC
23
18
28
Pre-stroke
mm
2.5
2.45
2.55
Output voltage
V
2.83
2.82
2.84
Adjustment
*
_02
CU407980-224*
*
Supply voltage
V
12
11.5
12.5
Ambient temperature
degC
23
18
28
Pre-stroke
mm
5.6
5.57
5.63
Output voltage
V
1.2
1
1.4
Confirmation
*
Remarks
Output voltage V1
Output voltage V1
_03
CU407980-224*
*
Supply voltage
V
12
11.5
12.5
Ambient temperature
degC
23
18
28
Output voltage
V
3.05
3.05
Confirmation of operating range
*
_04
CU407910-303*
*
Actuator retarding type
*
Supply voltage
V
12
11.5
12.5
Ambient temperature
degC
23
18
28
Pre-stroke
mm
2.5
2.45
2.55
Output voltage
V
1.17
1.16
1.18
Adjustment
*
_05
CU407910-303*
*
Supply voltage
V
12
11.5
12.5
Ambient temperature
degC
23
18
28
Pre-stroke
mm
5.6
5.57
5.63
Output voltage
V
2.8
2.6
3
Confirmation
*
Remarks
Output voltage V1
Output voltage V1
_06
CU407910-303*
*
Supply voltage
V
12
11.5
12.5
Ambient temperature
degC
23
18
28
Output voltage
V
0.95
Confirmation of operating range
*
Test data Ex:
Governor adjustment
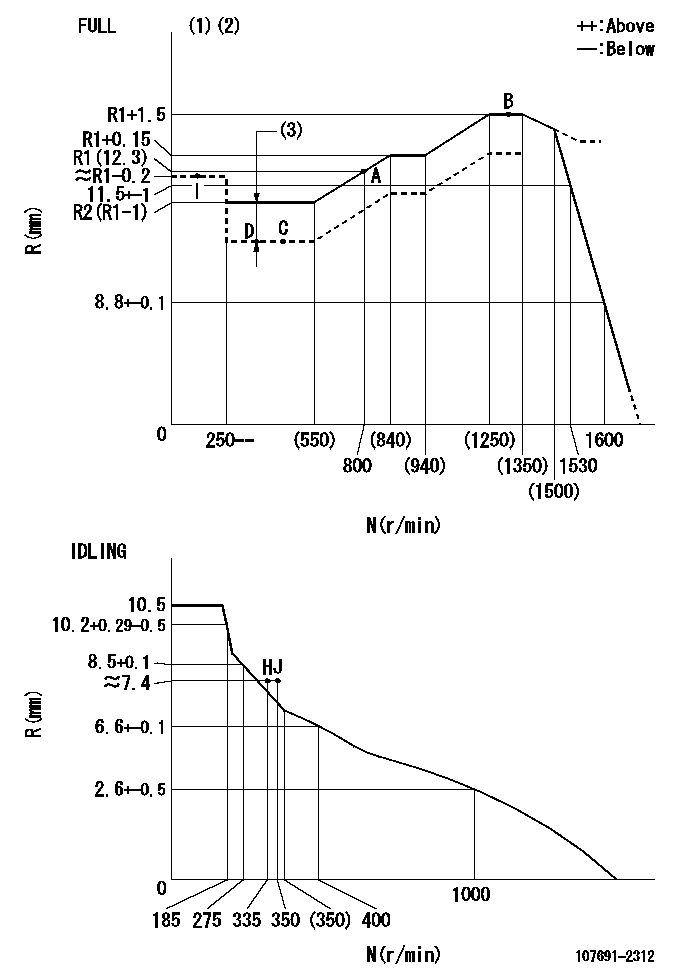
N:Pump speed
R:Rack position (mm)
(1)Torque cam stamping: T1
(2)Tolerance for racks not indicated: +-0.05mm.
(3)Boost compensator stroke: BCL
----------
T1=AD00 BCL=(1.25)+-0.1mm
----------
----------
T1=AD00 BCL=(1.25)+-0.1mm
----------
Speed control lever angle
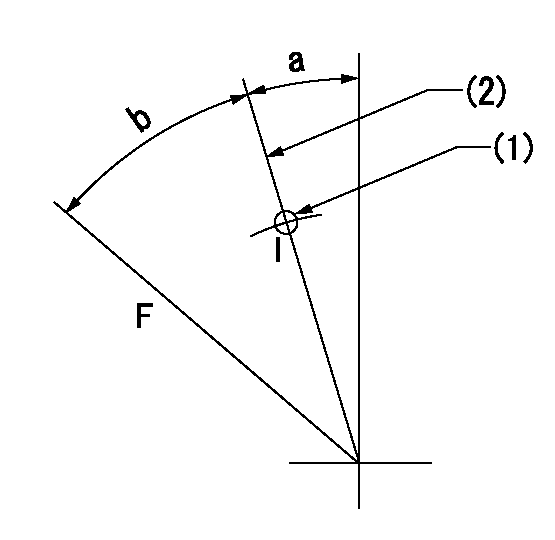
F:Full speed
I:Idle
(1)Use the hole at R = aa
(2)Stopper bolt set position 'H'
----------
aa=40mm
----------
a=39deg+-5deg b=36.5deg+-3deg
----------
aa=40mm
----------
a=39deg+-5deg b=36.5deg+-3deg
Stop lever angle

N:Pump normal
S:Stop the pump.
(1)Use the hole at R = aa
(2)Set the stopper bolt so that speed = bb and rack position = cc. (Confirm non-injection.)
----------
aa=40mm bb=1300r/min cc=1.5+-0.3mm
----------
a=6deg+-5deg b=45deg+-5deg
----------
aa=40mm bb=1300r/min cc=1.5+-0.3mm
----------
a=6deg+-5deg b=45deg+-5deg
0000001301

(1)Pump vertical direction
(2)Coupling's key groove position at No 1 cylinder's beginning of injection
(3)B.T.D.C.: aa
(4)Pre-stroke: bb
----------
aa=8deg bb=5.6+-0.03mm
----------
a=(3deg)
----------
aa=8deg bb=5.6+-0.03mm
----------
a=(3deg)
0000001401
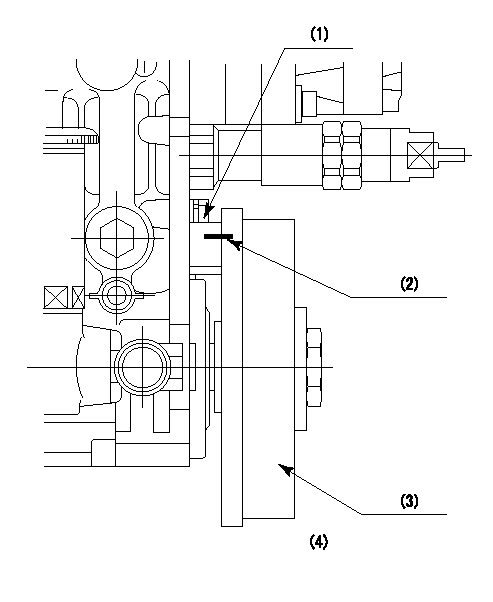
(1)Pointer
(2)Injection timing aligning mark
(3)Fly weight
(4)The actual shape and direction may be different from this illustration.
Operation sequence
1. Turn the prestroke actuator OFF.
2. Turn the camshaft as far as the No.1 cylinder's beginning of injection position.
3. Check that the pointer alignment mark of the injection pump and the alignment mark of the flywheel are matching.
4. If they are not matching, erase the alignment mark on the flywheel side, and stamp an alignment mark on the flywheel position that matches with the pointer side alignment mark.
5. Check again that the coupling's key groove position is in the No.1 cylinder's beginning of injection position.
----------
----------
----------
----------
0000001701
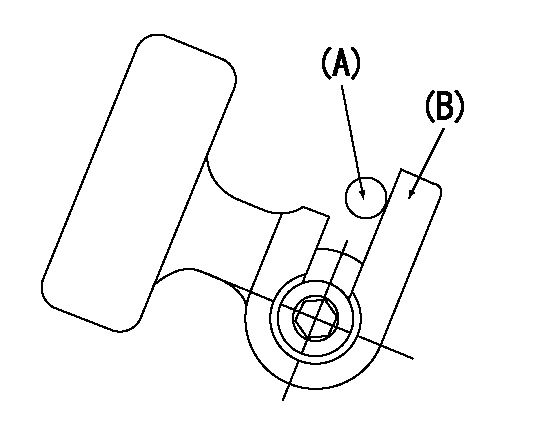
A : Stopper pin
B: Connector
----------
----------
----------
----------
0000001801
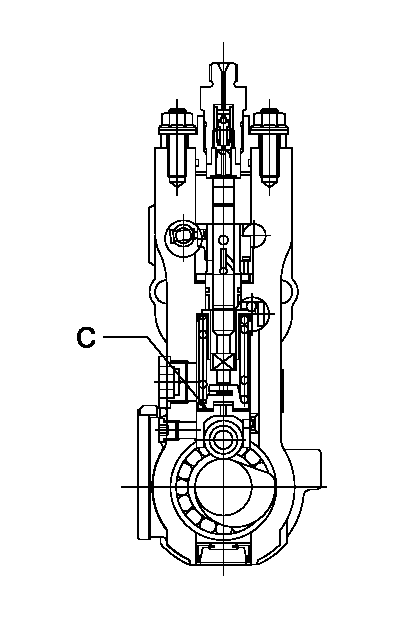
C:Shim
----------
----------
----------
----------
0000001901
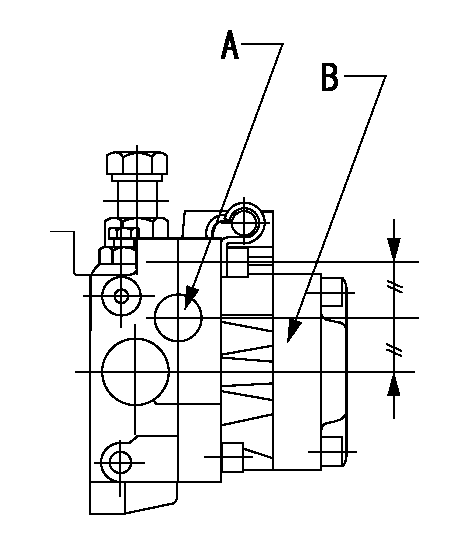
A:Sealing position
B:Pre-stroke actuator
1. When installing the pre-stroke actuator on the pump, first tighten the installation bolts loosely, then move the actuator fully clockwise (viewed from the drive side).
Temporary tightening torque: 1 - 1.5 N.m (0.1 - 0.15 kgf.m)
2. Move the actuator in the counterclockwise direction when viewed from the drive side, and adjust so that it becomes the adjustment point of the adjustment value. Then tighten it.
Tightening torque: 7^9 N.m (0.7^0.9 kgf.m)
3. After prestroke actuator installation adjustment, simultaneously stamp both the actuator side and housing side.
----------
----------
----------
----------
0000002201 SPEED SENSOR

(A) Flyweight projection
(B) Pickup sensor
(c) Lock nut
Speed sensor installation
(1)Install the speed sensor so that the clearance between the sensor and the flyweight projection is L.
(This gap is the gap when the pickup sensor is returned 1 turn from where it contacts the flyweight tooth.)
----------
L=0.8~1mm
----------
----------
L=0.8~1mm
----------
0000002301 RACK SENSOR
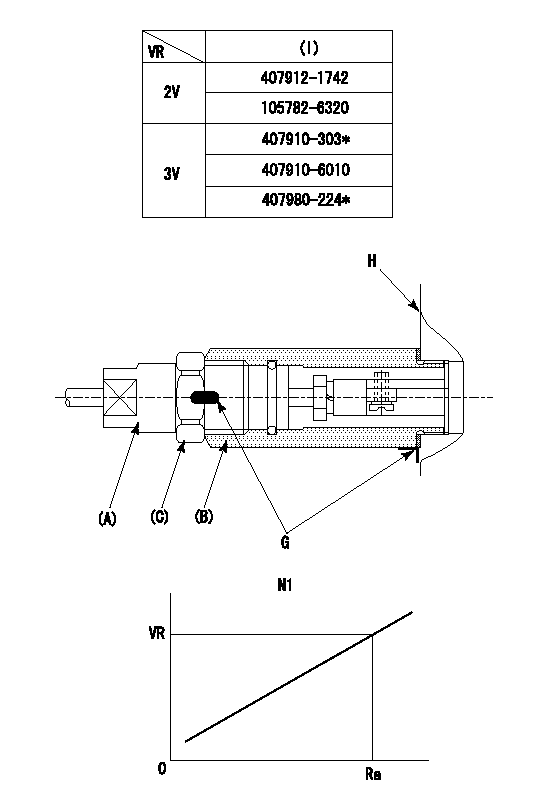
(VR) measurement voltage
(I) Part number of the control unit
(G) Apply red paint.
(H): End surface of the pump
1. Rack sensor adjustment (-0620)
(1)Fix the speed control lever at the full position
(2)Set the speed to N1 r/min.
(If the boost compensator is provided, apply boost pressure.)
(3)Adjust the bobbin (A) so that the rack sensor's output voltage is VR+-0.01.
(4)At that time, rack position must be Ra.
(5)Apply G at two places.
Connecting part between the joint (B) and the nut (F)
Connecting part between the joint (B) and the end surface of the pump (H)
----------
N1=1300r/min Ra=R1(12.3)+1.5mm
----------
----------
N1=1300r/min Ra=R1(12.3)+1.5mm
----------
Information:
The information supplied in this service letter may not be valid after the termination date of this program. Do not perform the work outlined in this Service Letter after the termination date without first contacting your Caterpillar product analyst.
This Program can only be administered after a failure occurs. The decision whether to apply the Program is made by the dealer. When reporting the repair, use "PS0852" as the Part Number and "7755" as the Group Number. Use "96" as the Warranty Claim Description Code and use "Z" as the SIMS Description Code.
This Revised Service Letter replaces the June 22, 1995 (Revised July 1996) Service Letter. Changes have been made to the TERMINATION DATE.
Termination Date
June 30, 1997Problem
The fuel injector tip may fail on certain 3406E Truck Engines.
Affected Product
Model & Identification Number
3406E (5EK1812-14203)
Parts Needed
6 - 0R4893 Injector Group (reman part number for 1171148) (used on 435-5EK1-1820 HP ratings)or6 - 0R4894 Injector Group (reman part number for 1188010) (used on 355-5EK1-1820, 375-5EK1-1820, 375-5EK1-1820, 435-5EK1821-Up, 455, and 475 HP ratings)or6 - 0R4895 Injector Group (reman part number for 1187929) (used on 355-5EK1821-Up, 375-5EK1821-Up, and 410 HP ratings)Action Required
See attached rework procedure.
Service Claim Allowances
Labor should be claimed in accordance with labor times listed in the 3406E Time Requirement Guide.
Parts Disposition
Handle the parts in accordance with your Warranty Bulletin on warranty parts handling.
Attach.(Rework Procedure)Rework Procedure
1. Remove the necessary air piping, air cleaners, valve covers, Jake Brakes, and rocker arm assemblies.2. Before removing fuel injectors from engine, be sure to drain fuel from fuel system. The recommended procedure is to blow compressed air through system via the fuel filter air bleed cap. Remove the fuel injectors from the engine. Immediately clean off excess engine oil and place the fuel injectors in individual clean plastic bags. Use care to prevent dirt from entering the fuel passages in the side of the injector.3. Wrap each injector individually with padding. Be sure to provide adequate padding around the injectors to prevent damage to the electrical terminals and nozzle during shipment. Pack the injectors in a sturdy box for immediate shipment back to Caterpillar. (See PARTS DISPOSITION.)4. If the tip of the injector is cracked, inspect top of cylinder and injector bore for foreign material. If the tip is missing, inspect the cylinder head and turbocharger for foreign material. Also inspect the injector for a screen that may have fallen from the removed injector.5. Lubricate the two larger o-ring seals with engine oil and install the injectors. Tighten the injector hold down bolt to a torque of 55 N m (41 ft lb).6. Adjust the valves, injectors, and Jake Brakes if so equipped. Complete the assembly.7. Prime the fuel system as described in Systems Operation Testing and Adjusting, SENR5578, page 69, "Fuel Priming Procedure".8. Stamp the engine block with the letters "PS0852".
This Program can only be administered after a failure occurs. The decision whether to apply the Program is made by the dealer. When reporting the repair, use "PS0852" as the Part Number and "7755" as the Group Number. Use "96" as the Warranty Claim Description Code and use "Z" as the SIMS Description Code.
This Revised Service Letter replaces the June 22, 1995 (Revised July 1996) Service Letter. Changes have been made to the TERMINATION DATE.
Termination Date
June 30, 1997Problem
The fuel injector tip may fail on certain 3406E Truck Engines.
Affected Product
Model & Identification Number
3406E (5EK1812-14203)
Parts Needed
6 - 0R4893 Injector Group (reman part number for 1171148) (used on 435-5EK1-1820 HP ratings)or6 - 0R4894 Injector Group (reman part number for 1188010) (used on 355-5EK1-1820, 375-5EK1-1820, 375-5EK1-1820, 435-5EK1821-Up, 455, and 475 HP ratings)or6 - 0R4895 Injector Group (reman part number for 1187929) (used on 355-5EK1821-Up, 375-5EK1821-Up, and 410 HP ratings)Action Required
See attached rework procedure.
Service Claim Allowances
Labor should be claimed in accordance with labor times listed in the 3406E Time Requirement Guide.
Parts Disposition
Handle the parts in accordance with your Warranty Bulletin on warranty parts handling.
Attach.(Rework Procedure)Rework Procedure
1. Remove the necessary air piping, air cleaners, valve covers, Jake Brakes, and rocker arm assemblies.2. Before removing fuel injectors from engine, be sure to drain fuel from fuel system. The recommended procedure is to blow compressed air through system via the fuel filter air bleed cap. Remove the fuel injectors from the engine. Immediately clean off excess engine oil and place the fuel injectors in individual clean plastic bags. Use care to prevent dirt from entering the fuel passages in the side of the injector.3. Wrap each injector individually with padding. Be sure to provide adequate padding around the injectors to prevent damage to the electrical terminals and nozzle during shipment. Pack the injectors in a sturdy box for immediate shipment back to Caterpillar. (See PARTS DISPOSITION.)4. If the tip of the injector is cracked, inspect top of cylinder and injector bore for foreign material. If the tip is missing, inspect the cylinder head and turbocharger for foreign material. Also inspect the injector for a screen that may have fallen from the removed injector.5. Lubricate the two larger o-ring seals with engine oil and install the injectors. Tighten the injector hold down bolt to a torque of 55 N m (41 ft lb).6. Adjust the valves, injectors, and Jake Brakes if so equipped. Complete the assembly.7. Prime the fuel system as described in Systems Operation Testing and Adjusting, SENR5578, page 69, "Fuel Priming Procedure".8. Stamp the engine block with the letters "PS0852".
Have questions with 107691-2312?
Group cross 107691-2312 ZEXEL
107691-2312
INJECTION-PUMP ASSEMBLY