Information injection-pump assembly
BOSCH
F 01G 09U 0JG
f01g09u0jg
ZEXEL
107691-0201
1076910201
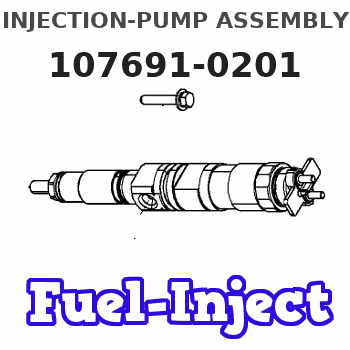
Rating:
Cross reference number
BOSCH
F 01G 09U 0JG
f01g09u0jg
ZEXEL
107691-0201
1076910201
Zexel num
Bosch num
Firm num
Name
Calibration Data:
Adjustment conditions
Test oil
1404 Test oil ISO4113 or {SAEJ967d}
1404 Test oil ISO4113 or {SAEJ967d}
Test oil temperature
degC
40
40
45
Nozzle and nozzle holder
105780-8250
Bosch type code
1 688 901 101
Nozzle
105780-0120
Bosch type code
1 688 901 990
Nozzle holder
105780-2190
Opening pressure
MPa
20.7
Opening pressure
kgf/cm2
211
Injection pipe
Outer diameter - inner diameter - length (mm) mm 8-3-600
Outer diameter - inner diameter - length (mm) mm 8-3-600
Overflow valve
134424-4120
Overflow valve opening pressure
kPa
255
221
289
Overflow valve opening pressure
kgf/cm2
2.6
2.25
2.95
Tester oil delivery pressure
kPa
255
255
255
Tester oil delivery pressure
kgf/cm2
2.6
2.6
2.6
RED4 control unit part number
407915-0
590
RED4 rack sensor specifications
mm
19
PS/ACT control unit part no.
407980-2
24*
Digi switch no.
14
Direction of rotation (viewed from drive side)
Right R
Right R
Injection timing adjustment
Direction of rotation (viewed from drive side)
Right R
Right R
Injection order
1-4-2-6-
3-5
Pre-stroke
mm
5.1
5.07
5.13
Beginning of injection position
Drive side NO.1
Drive side NO.1
Difference between angles 1
Cal 1-4 deg. 60 59.75 60.25
Cal 1-4 deg. 60 59.75 60.25
Difference between angles 2
Cyl.1-2 deg. 120 119.75 120.25
Cyl.1-2 deg. 120 119.75 120.25
Difference between angles 3
Cal 1-6 deg. 180 179.75 180.25
Cal 1-6 deg. 180 179.75 180.25
Difference between angles 4
Cal 1-3 deg. 240 239.75 240.25
Cal 1-3 deg. 240 239.75 240.25
Difference between angles 5
Cal 1-5 deg. 300 299.75 300.25
Cal 1-5 deg. 300 299.75 300.25
Injection quantity adjustment
Rack position
(11.3)
PWM
%
51.5
Pump speed
r/min
700
700
700
Average injection quantity
mm3/st.
108
107
109
Max. variation between cylinders
%
0
-4
4
Basic
*
PS407980-224*
V
2.25+-0.
01
PS407980-224*
mm
3.1+-0.0
5
Injection quantity adjustment_02
Rack position
(6.7)
PWM
%
25.6+-2.
8
Pump speed
r/min
445
445
445
Average injection quantity
mm3/st.
11
9.2
12.8
Max. variation between cylinders
%
0
-10
10
PS407980-224*
V
V1+0.05+
-0.01
PS407980-224*
mm
5+-0.03
Remarks
Refer to items regarding the pre-stroke actuator
Refer to items regarding the pre-stroke actuator
Governor adjustment
Pump speed
r/min
1150--
Advance angle
deg.
0
0
0
Remarks
Start
Start
Governor adjustment_02
Pump speed
r/min
1100
Advance angle
deg.
0.3
Governor adjustment_03
Pump speed
r/min
1250
Advance angle
deg.
2
1.2
2.8
Governor adjustment_04
Pump speed
r/min
(1300)
Advance angle
deg.
4
3.7
4.3
Remarks
Finish
Finish
0000001201
CU407980-224*
*
Actuator retarding type
*
Supply voltage
V
24
23.5
24.5
Ambient temperature
degC
23
18
28
Pre-stroke
mm
2
1.95
2.05
Output voltage
V
2.83
2.82
2.84
Adjustment
*
_02
CU407980-224*
*
Supply voltage
V
24
23.5
24.5
Ambient temperature
degC
23
18
28
Pre-stroke
mm
5.1
5.07
5.13
Output voltage
V
1.2
1
1.4
Confirmation
*
Remarks
Output voltage V1
Output voltage V1
_03
CU407980-224*
*
Supply voltage
V
24
23.5
24.5
Ambient temperature
degC
23
18
28
Output voltage
V
3.05
3.05
Confirmation of operating range
*
Test data Ex:
Speed control lever angle
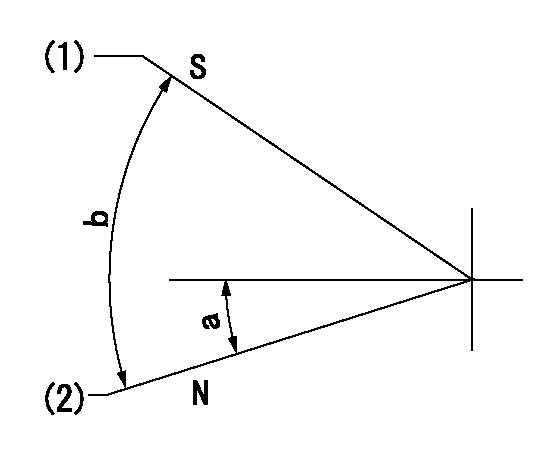
N:Pump normal
S:Stop the pump.
(1)Rack position = aa
(2)Rack position bb
----------
aa=1mm bb=20mm
----------
a=20deg+-5deg b=37deg+-5deg
----------
aa=1mm bb=20mm
----------
a=20deg+-5deg b=37deg+-5deg
0000000901
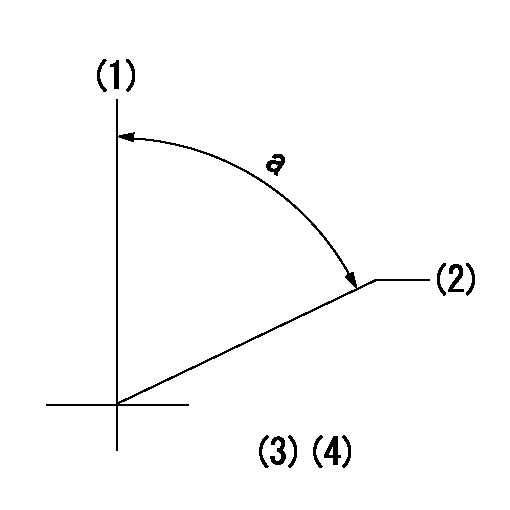
(1)Pump vertical direction
(2)Position of timer's threaded hole at No 1 cylinder's beginning of injection
(3)Pre-stroke: aa
(4)-
----------
aa=5.1+-0.03mm
----------
a=(70deg)
----------
aa=5.1+-0.03mm
----------
a=(70deg)
Stop lever angle
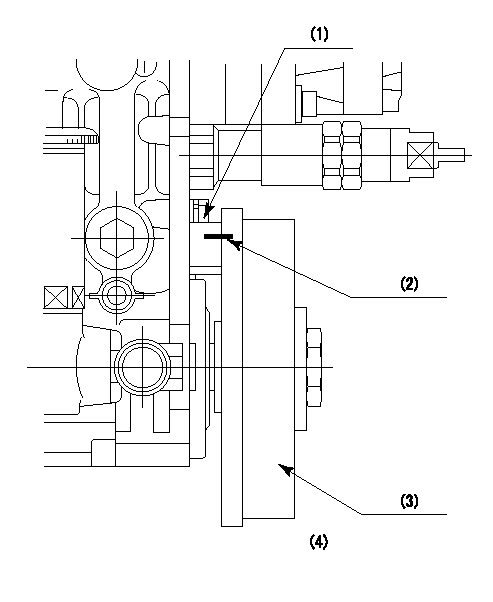
(1)Pointer
(2)Injection timing aligning mark
(3)Fly weight
(4)The actual shape and direction may be different from this illustration.
Operation sequence
1. Turn the prestroke actuator OFF.
2. Turn the camshaft as far as the No.1 cylinder's beginning of injection position.
3. Check that the pointer alignment mark of the injection pump and the alignment mark of the flywheel are matching.
4. If they are not matching, erase the alignment mark on the flywheel side, and stamp an alignment mark on the flywheel position that matches with the pointer side alignment mark.
5. Check again that the coupling's key groove position is in the No.1 cylinder's beginning of injection position.
----------
----------
----------
----------
0000001301
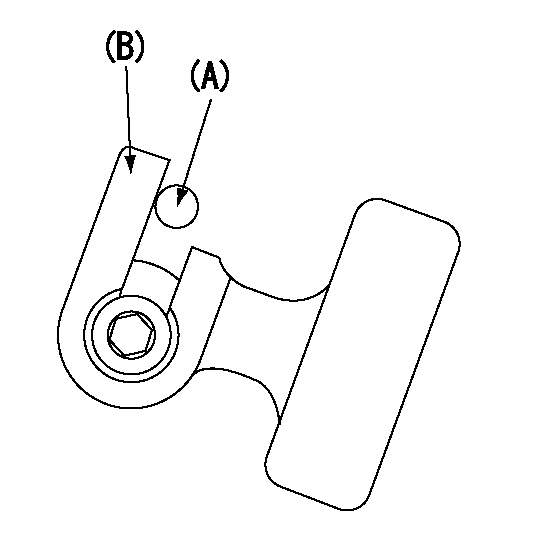
A : Stopper pin
B: Connector
----------
----------
----------
----------
0000001401
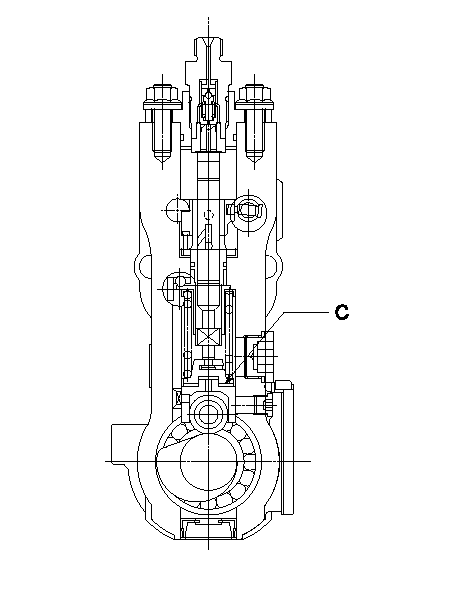
C:Shim
----------
----------
----------
----------
0000001501
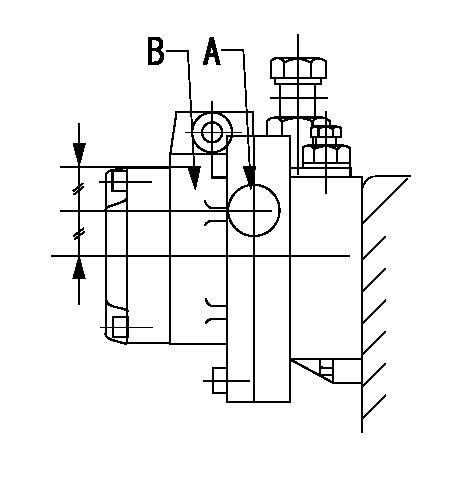
A:Sealing position
B:Pre-stroke actuator
1. When installing the pre-stroke actuator on the pump, first tighten the installation bolts loosely, then move the actuator fully counterclockwise (viewed from the drive side).
Temporary tightening torque: 1 - 1.5 N.m (0.1 - 0.15 kgf.m)
2. Move the actuator in the clockwise direction when viewed from the drive side, and adjust so that it becomes the adjustment point of the adjustment value. Then tighten it.
Tightening torque: 7^9 N.m (0.7^0.9 kgf.m)
3. After prestroke actuator installation adjustment, simultaneously stamp both the actuator side and housing side.
----------
----------
----------
----------
0000001701

(PWM) Pulse width modulation (%)
(R) Rack position (mm)
Rack sensor output characteristics
1. Rack limit adjustment
(1)Measure the rack position R2 for PWM a2%.
(2)Confirm that it is within the range R2 = 15+-1 mm.
(3)Measure the rack position R1 at PWM a %.
(4)Confirm that it is within the range R2 - R1 = 10+-0.1 mm.
2. Check the limp home operation.
(1)Move the switch box's limp home switch to the limp home side.
(2)Confirm rack position L1 (mm ) and L2 (mm) for PWM in the above table.
3. Check the pull down operation.
(1)Confirm that the rack position is 19 mm at PWM B%.
(2)In the conditions described in the above table, move the switch box's pull down switch to the pull down side and confirm that the rack position momentarily becomes 1 mm or less.
----------
a1=16.25% a2=72.5% L1=1--mm L2=19++mm A=5% B=95%
----------
----------
a1=16.25% a2=72.5% L1=1--mm L2=19++mm A=5% B=95%
----------
Information:
ACTION REQUIRED
Check Plug Replacement:
1) Check engine serial number to ensure it is included in the affected rework population.
2) Inspect fuel injection pump outlet check plugs installed on pump. Refer to Image1 for check plug location. If the fuel injection pump outlet check plugs have dimples as shown in Image2 DO NOT perform plug rework.
3) If check plugs do not have dimples as shown in Image2 the plugs need to be replaced, refer to Special Instructions REHS3841 for proper plug installation.
Fuel Line Inspect and Possibly Replace:
Refer to Special Instructions REHS3842 for C7, and REHS3846 for C9. Inspect all high pressure fuel lines that require clamping to ensure proper clamping location and torque for each clamp that holds each high pressure fuel line in place. Verify all rubber grommets are present in each clamp. The fuel line(s) must be replaced if the clamp location/torque and or the grommets are not correct.
Reference line kit part numbers below for C7 and C9 if needed after inspection is complete.
DESCRIPTION______________________KIT
C7
Tube As.-Fuel_(Pump Line)______310-6027
Tube As.-Fuel_(Line 1)_________310-6029
Tube As.-Fuel_(Line 6)_________310-6030
C9
Tube As.-Fuel_(Pump Line)______310-6031
Tube As.-Fuel_(Line 1)_________310-6032
Tube As.-Fuel_(Lines 5 & 6)____310-6033
Image1
Image2
OWNER NOTIFICATION
U.S. and Canadian owners will receive the attached Owner Notification.
SERVICE CLAIM ALLOWANCES
Caterpillar Dealer Suggested Customer Suggested
Parts % Labor Hrs% Parts % Labor Hrs% Parts % Labor Hrs%
100% 100% 0% 0% 0% 0%
This is a 1.0-hour job
Add an additional 0.2 Hrs per high pressure fuel line replaced in step 4 in the Action Required if needed.
PARTS DISPOSITION
Handle the parts in accordance with your Warranty Bulletin on warranty parts handling.
Only return high pressure fuel line(s) replaced during this rework to the address below.
Make sure the outside of the shipping container is marked PIXXXX.
Caterpillar Inc.
Attn: PIXXXXX
Route 29 And Old Galena Road
Building DD, Dock 8,Engineering Parts Return Area
MOSSVILLE, IL 61552
USA
MAKE EVERY EFFORT TO COMPLETE THIS PROGRAM AS SOON AS POSSIBLE.
IMPORTANT: SAFETY
SAFETY ? RECALL FOR REPLACING THE FUEL PUMP PLUGS
MODELS INVOLVED - Certain C7 and C9 Truck and Bus Engines
Dear Caterpillar Product Owner:
This notice is sent to you in accordance with the requirements of the National Traffic and Motor Vehicle Safety Act, and the requirements of the Canadian Motor Vehicle Safety Act. Caterpillar has decided that a defect which relates to motor vehicle safety exists in 2008 and 2009 model year trucks and buses equipped with certain Caterpillar C7 and C9 diesel engines.
A fuel pump plug may crack, which could cause fuel to spray and leak. Fuel in the presence of an ignition source can result in a fire. The driver may also become aware due to decrease in engine power or the illumination of a check engine lamp or engine protection lamp. New fuel pump plugs will be installed on the engine. You will not be charged for the service performed.
Please contact your local Caterpillar dealer immediately to schedule this service. The dealer will advise you of the time required to complete this service.
If you are a lessor of these vehicles, you must forward this letter to your lessee within ten days.
If you have had your vehicle repaired for this concern prior to receipt of this notice and incurred any costs, you may be eligible for