Information injection-pump assembly
BOSCH
9 400 618 874
9400618874
ZEXEL
107691-0186
1076910186
NISSAN-DIESEL
16801Z5666
16801z5666
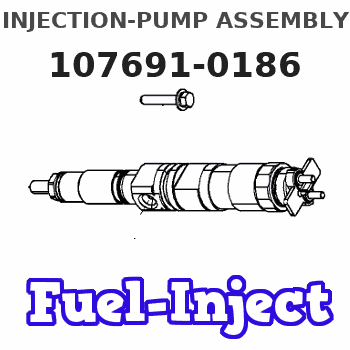
Rating:
Service parts 107691-0186 INJECTION-PUMP ASSEMBLY:
1.
_
7.
COUPLING PLATE
9.
_
11.
Nozzle and Holder
16600-Z5714
12.
Open Pre:MPa(Kqf/cm2)
16.7{170}/19.6{220}
14.
NOZZLE
Include in #1:
107691-0186
as INJECTION-PUMP ASSEMBLY
Cross reference number
BOSCH
9 400 618 874
9400618874
ZEXEL
107691-0186
1076910186
NISSAN-DIESEL
16801Z5666
16801z5666
Zexel num
Bosch num
Firm num
Name
9 400 618 874
16801Z5666 NISSAN-DIESEL
INJECTION-PUMP ASSEMBLY
FE6TA * K 14CG TICS MD-TI6 TICS
FE6TA * K 14CG TICS MD-TI6 TICS
Calibration Data:
Adjustment conditions
Test oil
1404 Test oil ISO4113 or {SAEJ967d}
1404 Test oil ISO4113 or {SAEJ967d}
Test oil temperature
degC
40
40
45
Nozzle and nozzle holder
105780-8250
Bosch type code
1 688 901 101
Nozzle
105780-0120
Bosch type code
1 688 901 990
Nozzle holder
105780-2190
Opening pressure
MPa
20.7
Opening pressure
kgf/cm2
211
Injection pipe
Outer diameter - inner diameter - length (mm) mm 8-3-600
Outer diameter - inner diameter - length (mm) mm 8-3-600
Overflow valve
134424-4120
Overflow valve opening pressure
kPa
255
221
289
Overflow valve opening pressure
kgf/cm2
2.6
2.25
2.95
Tester oil delivery pressure
kPa
255
255
255
Tester oil delivery pressure
kgf/cm2
2.6
2.6
2.6
RED4 control unit part number
407915-0
590
RED4 rack sensor specifications
mm
19
PS/ACT control unit part no.
407980-2
24*
Digi switch no.
14
Direction of rotation (viewed from drive side)
Right R
Right R
Injection timing adjustment
Direction of rotation (viewed from drive side)
Right R
Right R
Injection order
1-4-2-6-
3-5
Pre-stroke
mm
5.1
5.07
5.13
Beginning of injection position
Drive side NO.1
Drive side NO.1
Difference between angles 1
Cal 1-4 deg. 60 59.75 60.25
Cal 1-4 deg. 60 59.75 60.25
Difference between angles 2
Cyl.1-2 deg. 120 119.75 120.25
Cyl.1-2 deg. 120 119.75 120.25
Difference between angles 3
Cal 1-6 deg. 180 179.75 180.25
Cal 1-6 deg. 180 179.75 180.25
Difference between angles 4
Cal 1-3 deg. 240 239.75 240.25
Cal 1-3 deg. 240 239.75 240.25
Difference between angles 5
Cal 1-5 deg. 300 299.75 300.25
Cal 1-5 deg. 300 299.75 300.25
Injection quantity adjustment
Rack position
(11.3)
PWM
%
51.5
Pump speed
r/min
700
700
700
Average injection quantity
mm3/st.
108
107
109
Max. variation between cylinders
%
0
-4
4
Basic
*
PS407980-224*
V
2.25+-0.
01
PS407980-224*
mm
3.1+-0.0
5
Injection quantity adjustment_02
Rack position
(6.7)
PWM
%
25.6+-2.
8
Pump speed
r/min
445
445
445
Average injection quantity
mm3/st.
11
9.2
12.8
Max. variation between cylinders
%
0
-10
10
PS407980-224*
V
V1+0.05+
-0.01
PS407980-224*
mm
5+-0.03
Remarks
Refer to items regarding the pre-stroke actuator
Refer to items regarding the pre-stroke actuator
Governor adjustment
Pump speed
r/min
1150--
Advance angle
deg.
0
0
0
Remarks
Start
Start
Governor adjustment_02
Pump speed
r/min
1100
Advance angle
deg.
0.3
Governor adjustment_03
Pump speed
r/min
1300
Advance angle
deg.
4
3.7
4.3
Remarks
Finish
Finish
0000001201
CU407980-224*
*
Actuator advancing type
*
Supply voltage
V
24
23.5
24.5
Ambient temperature
degC
23
18
28
Pre-stroke
mm
2
1.95
2.05
Output voltage
V
2.83
2.82
2.84
Adjustment
*
_02
CU407980-224*
*
Supply voltage
V
24
23.5
24.5
Ambient temperature
degC
23
18
28
Pre-stroke
mm
5.1
5.07
5.13
Output voltage
V
1.2
1
1.4
Confirmation
*
Remarks
Output voltage V1
Output voltage V1
_03
CU407980-224*
*
Supply voltage
V
24
23.5
24.5
Ambient temperature
degC
23
18
28
Output voltage
V
3.05
3.05
Confirmation of operating range
*
Test data Ex:
Speed control lever angle

N:Pump normal
S:Stop the pump.
(1)Rack position = aa
(2)Rack position bb
----------
aa=20mm bb=1mm
----------
a=27deg+-5deg b=37deg+-5deg
----------
aa=20mm bb=1mm
----------
a=27deg+-5deg b=37deg+-5deg
0000000901

(1)Pump vertical direction
(2)Coupling's key groove position at No 1 cylinder's beginning of injection
(3)Pre-stroke: aa
(4)-
----------
aa=5.1+-0.03mm
----------
a=(20deg)
----------
aa=5.1+-0.03mm
----------
a=(20deg)
Stop lever angle
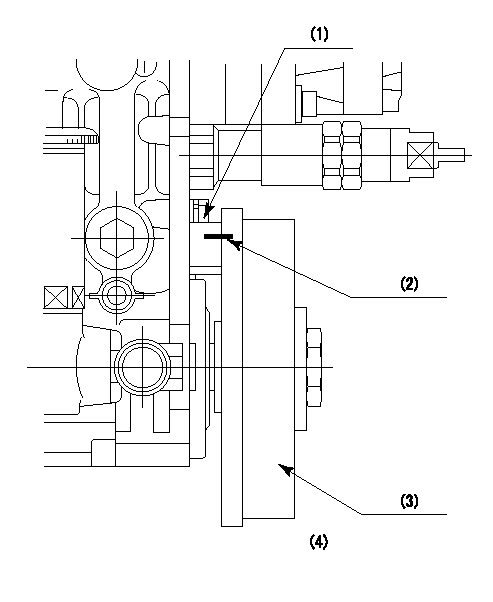
(1)Pointer
(2)Injection timing aligning mark
(3)Fly weight
(4)The actual shape and direction may be different from this illustration.
Operation sequence
1. Turn the prestroke actuator OFF.
2. Turn the camshaft as far as the No.1 cylinder's beginning of injection position.
3. Check that the pointer alignment mark of the injection pump and the alignment mark of the flywheel are matching.
4. If they are not matching, erase the alignment mark on the flywheel side, and stamp an alignment mark on the flywheel position that matches with the pointer side alignment mark.
5. Check again that the coupling's key groove position is in the No.1 cylinder's beginning of injection position.
----------
----------
----------
----------
0000001301
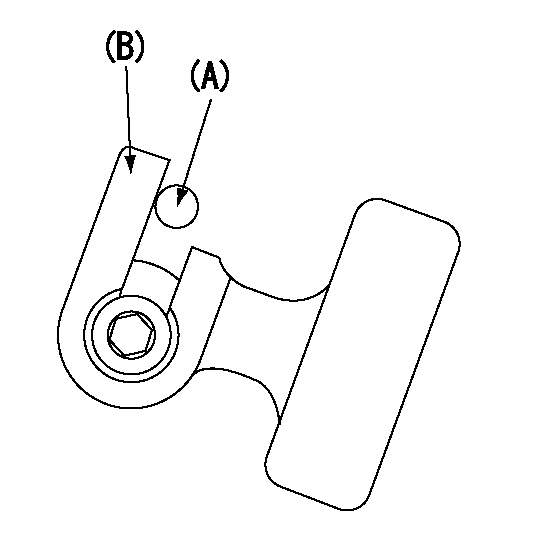
A : Stopper pin
B: Connector
----------
----------
----------
----------
0000001401
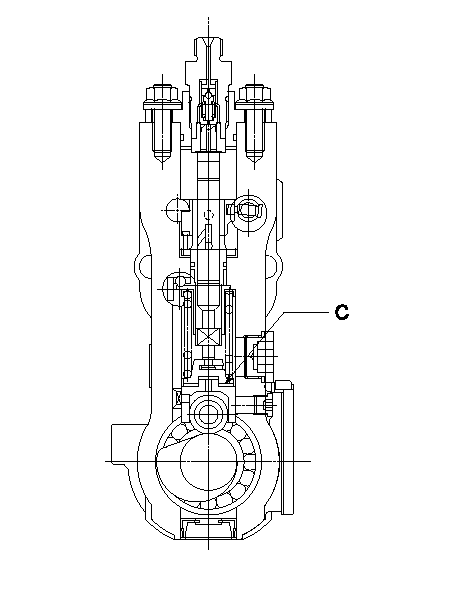
C:Shim
----------
----------
----------
----------
0000001501
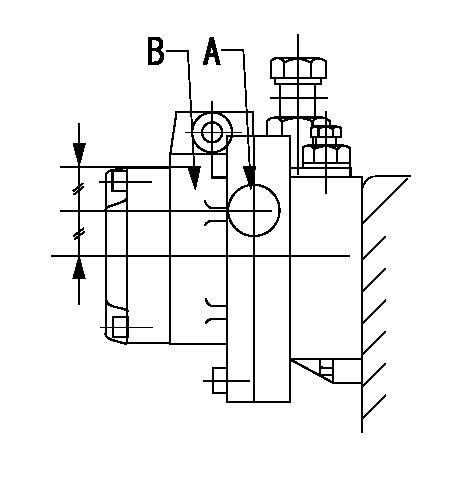
A:Sealing position
B:Pre-stroke actuator
1. When installing the pre-stroke actuator on the pump, first tighten the installation bolts loosely, then move the actuator fully counterclockwise (viewed from the drive side).
Temporary tightening torque: 1 - 1.5 N.m (0.1 - 0.15 kgf.m)
2. Move the actuator in the clockwise direction when viewed from the drive side, and adjust so that it becomes the adjustment point of the adjustment value. Then tighten it.
Tightening torque: 7^9 N.m (0.7^0.9 kgf.m)
3. After prestroke actuator installation adjustment, simultaneously stamp both the actuator side and housing side.
----------
----------
----------
----------
0000001701

(PWM) Pulse width modulation (%)
(R) Rack position (mm)
Rack sensor output characteristics
1. Rack limit adjustment
(1)Measure the rack position R2 for PWM a2%.
(2)Confirm that it is within the range R2 = 15+-1 mm.
(3)Measure the rack position R1 at PWM a %.
(4)Confirm that it is within the range R2 - R1 = 10+-0.1 mm.
2. Check the limp home operation.
(1)Move the switch box's limp home switch to the limp home side.
(2)Confirm rack position L1 (mm ) and L2 (mm) for PWM in the above table.
3. Check the pull down operation.
(1)Confirm that the rack position is 19 mm at PWM B%.
(2)In the conditions described in the above table, move the switch box's pull down switch to the pull down side and confirm that the rack position momentarily becomes 1 mm or less.
----------
a1=16.25% a2=72.5% L1=1--mm L2=19++mm A=5% B=95%
----------
----------
a1=16.25% a2=72.5% L1=1--mm L2=19++mm A=5% B=95%
----------
Information:
Illustration 1 g06140436
(1) 277-7637 Bracket
(2) 8T-3490 Weld NutWeld the 8T-3490 Weld Nut (2) on the 277-7637 Bracket (1) as shown in Illustration 1.
Illustration 2 g06140437
Weld location
Illustration 3 g06140439
View of area A
(1) Welded bracket
Illustration 4 g06140464
(B) 10 mm (0.4 inch)
(C) 36 mm (1.4 inch)
(E) 27 mm (1.1 inch)
(W1) 3 mm (0.1 inch) Fillet weldWeld the 277-7637 Bracket (1) on the frame as shown in Illustration 4.CEM Hose Removal and Install Procedure
Illustration 5 g06140472
(3) 418-2057 Hose
(4) 418-2055 HoseRemove the 418-2057 Hose (3) and the 418-2055 Hose (4).
Illustration 6 g06140489
(5) 428-8808 Hose Clamp
(6) 468-4707 Hose
(7) 326-4516 Cable Tie
(8) 468-4709 Hose
(9) 449-2092 Hose
(10) 428-8808 Hose Clamp
Assemble the 468-4707 Hose (6), the 468-4709 Hose (8), and the 449-2092 Hose (9) as shown in Illustration 6.
Secure the 468-4707 Hose (6) with a 326-4516 Cable Tie (7)
Tighten the two 428-8808 Hose Clamps (5) to 6.5 to 6.8 N m (58 to 60 lb in).
Tighten the four 428-8808 Hose Clamps (10) to 6.5 to 6.8 N m (58 to 60 lb in) and install hose clamp same as original hose clamp position before the rework.374F Phase Change Tank
Illustration 7 g06140762
(11) 8T-4189 Bolt
(12) 8T-4224 Hard Washer
(13) 357-4586 Elbow As
(F) 30 degree
Tighten the 8T-4189 Bolt (11) to 28 7 N m (248 62 lb in).
Assemble the 357-4586 Elbow As (13) at an angle 30 degree (F) as shown in Illustration 7 and tighten to 28 4 N m (248 35 lb in).390F Phase Change Tank
Illustration 8 g06140765
(11) 8T-4189 Bolt
(12) 8T-4224 Hard Washer
(13) 357-4586 Elbow As
(14) 468-4722 Plate As
(F) 30 degreePhase change tank and related parts are same as 374F. The difference is only support plate 468-4722 Plate As (14). Repeat the Step 1 and Step 2.Support Plate Mount
Illustration 9 g06140788
(15) 8T-4137 Bolt
(16) 7X-7729 Washer
(17) 135-8575 Bolt As (Reuse)Illustration 9 is showing example for the 374F. The different bracket is used on the 390F however the procedure is same.
Tighten the 8T-4137 Bolt (15) to 100 20 N m (74 15 lb ft).
Tighten the 135-8575 Bolt As (17) to 100 20 N m (74 15 lb ft).Software
Download the latest software from SIS Web. Refer Illustration 10 for flash software download.
Illustration 10 g06140790Tune Value Update
Illustration 11 g06140791Update threshold to 525 °C using Cat Electronic Technician (Cat ET) as shown in Illustration 11. Factory password is required to change the value. When you input your CWS ID, the factory password can be provided.