Information injection-pump assembly
ZEXEL
107492-2032
1074922032
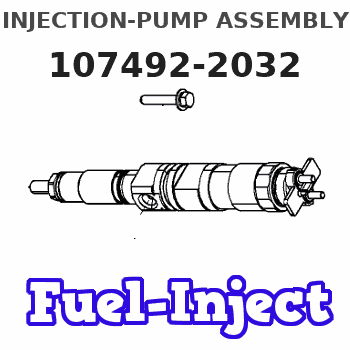
Rating:
Service parts 107492-2032 INJECTION-PUMP ASSEMBLY:
1.
_
5.
AUTOM. ADVANCE MECHANIS
6.
COUPLING PLATE
9.
_
11.
Nozzle and Holder
12.
Open Pre:MPa(Kqf/cm2)
21.6{220}
15.
NOZZLE SET
Include in #1:
107492-2032
as INJECTION-PUMP ASSEMBLY
Cross reference number
ZEXEL
107492-2032
1074922032
Zexel num
Bosch num
Firm num
Name
Calibration Data:
Adjustment conditions
Test oil
1404 Test oil ISO4113 or {SAEJ967d}
1404 Test oil ISO4113 or {SAEJ967d}
Test oil temperature
degC
40
40
45
Nozzle and nozzle holder
105780-8240
Nozzle
105780-0110
Nozzle holder
105780-2170
Opening pressure
MPa
20.6
Opening pressure
kgf/cm2
210
Injection pipe
Outer diameter - inner diameter - length (mm) mm 8-3-600
Outer diameter - inner diameter - length (mm) mm 8-3-600
Overflow valve
131424-8420
Overflow valve opening pressure
kPa
255
221
289
Overflow valve opening pressure
kgf/cm2
2.6
2.25
2.95
Tester oil delivery pressure
kPa
255
255
255
Tester oil delivery pressure
kgf/cm2
2.6
2.6
2.6
PS/ACT control unit part no.
407910-3
03*
Selector switch no.
02
PS/ACT control unit part no.
407980-2
24*
Digi switch no.
01
Direction of rotation (viewed from drive side)
Right R
Right R
Injection timing adjustment
Direction of rotation (viewed from drive side)
Right R
Right R
Injection order
1-3-4-2
Pre-stroke
mm
5.6
5.57
5.63
Beginning of injection position
Drive side NO.1
Drive side NO.1
Difference between angles 1
Cal 1-3 deg. 90 89.75 90.25
Cal 1-3 deg. 90 89.75 90.25
Difference between angles 2
Cal 1-4 deg. 180 179.75 180.25
Cal 1-4 deg. 180 179.75 180.25
Difference between angles 3
Cyl.1-2 deg. 270 269.75 270.25
Cyl.1-2 deg. 270 269.75 270.25
Injection quantity adjustment
Adjusting point
-
Rack position
12.5
Pump speed
r/min
900
900
900
Average injection quantity
mm3/st.
93
91.4
94.6
Max. variation between cylinders
%
0
-3
3
Basic
*
Fixing the rack
*
PS407980-224*
V
2.25+-0.
01
PS407980-224*
mm
3.6+-0.0
3
PS407910-303*
V
2.25+-0.
01
PS407910-303*
mm
3.6+-0.0
3
Standard for adjustment of the maximum variation between cylinders
*
Injection quantity adjustment_02
Adjusting point
Z
Rack position
8.5+-0.5
Pump speed
r/min
600
600
600
Average injection quantity
mm3/st.
10
8.5
11.5
Max. variation between cylinders
%
0
-15
15
Fixing the rack
*
PS407980-224*
V
2.25+-0.
01
PS407980-224*
mm
3.6+-0.0
3
PS407910-303*
V
2.25+-0.
01
PS407910-303*
mm
3.6+-0.0
3
Standard for adjustment of the maximum variation between cylinders
*
Injection quantity adjustment_03
Adjusting point
A
Rack position
R1(12.5)
Pump speed
r/min
900
900
900
Average injection quantity
mm3/st.
93
92
94
Basic
*
Fixing the lever
*
Boost pressure
kPa
44
44
Boost pressure
mmHg
330
330
PS407980-224*
V
2.25+-0.
01
PS407980-224*
mm
3.6+-0.0
3
PS407910-303*
V
2.25+-0.
01
PS407910-303*
mm
3.6+-0.0
3
Injection quantity adjustment_04
Adjusting point
B
Rack position
R1+1.55
Pump speed
r/min
1500
1500
1500
Average injection quantity
mm3/st.
100.5
96.5
104.5
Fixing the lever
*
Boost pressure
kPa
44
44
Boost pressure
mmHg
330
330
PS407980-224*
V
2.25+-0.
01
PS407980-224*
mm
3.6+-0.0
3
PS407910-303*
V
2.25+-0.
01
PS407910-303*
mm
3.6+-0.0
3
Boost compensator adjustment
Pump speed
r/min
300
300
300
Rack position
R2-0.9
Boost pressure
kPa
21.3
20
22.6
Boost pressure
mmHg
160
150
170
Boost compensator adjustment_02
Pump speed
r/min
300
300
300
Rack position
R2(R1-0.
85)
Boost pressure
kPa
30.7
30.7
30.7
Boost pressure
mmHg
230
230
230
0000001601
CU407980-224*
*
Actuator retarding type
*
Supply voltage
V
12
11.5
12.5
Ambient temperature
degC
23
18
28
Pre-stroke
mm
2.5
2.45
2.55
Output voltage
V
2.83
2.82
2.84
Adjustment
*
_02
CU407980-224*
*
Supply voltage
V
12
11.5
12.5
Ambient temperature
degC
23
18
28
Pre-stroke
mm
5.6
5.57
5.63
Output voltage
V
1.2
1
1.4
Confirmation
*
_03
CU407980-224*
*
Supply voltage
V
12
11.5
12.5
Ambient temperature
degC
23
18
28
Output voltage
V
3.05
3.05
Confirmation of operating range
*
_04
CU407910-303*
*
Actuator retarding type
*
Supply voltage
V
12
11.5
12.5
Ambient temperature
degC
23
18
28
Pre-stroke
mm
2.5
2.45
2.55
Output voltage
V
2.83
2.82
2.84
Adjustment
*
_05
CU407910-303*
*
Supply voltage
V
12
11.5
12.5
Ambient temperature
degC
23
18
28
Pre-stroke
mm
5.6
5.57
5.63
Output voltage
V
1.2
1
1.4
Confirmation
*
_06
CU407910-303*
*
Supply voltage
V
12
11.5
12.5
Ambient temperature
degC
23
18
28
Output voltage
V
3.05
3.05
Confirmation of operating range
*
Test data Ex:
Governor adjustment

N:Pump speed
R:Rack position (mm)
(1)Torque cam stamping: T1
(2)Tolerance for racks not indicated: +-0.05mm.
(3)Boost compensator stroke: BCL
----------
T1=J47 BCL=0.9+-0.1mm
----------
----------
T1=J47 BCL=0.9+-0.1mm
----------
Speed control lever angle
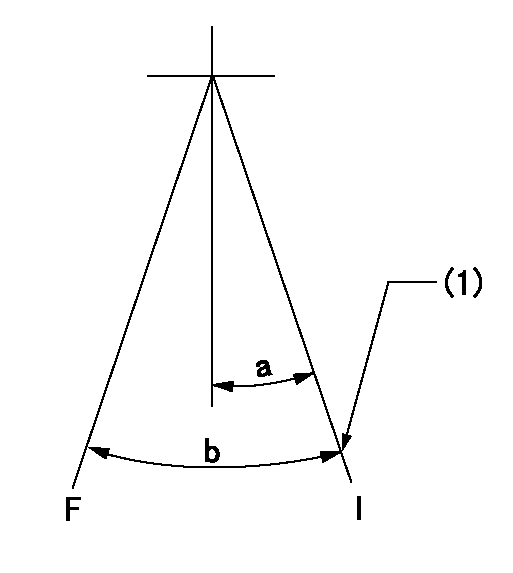
F:Full speed
I:Idle
(1)Stopper bolt set position 'H'
----------
----------
a=22deg+-5deg b=(37.5deg)+-3deg
----------
----------
a=22deg+-5deg b=(37.5deg)+-3deg
Stop lever angle
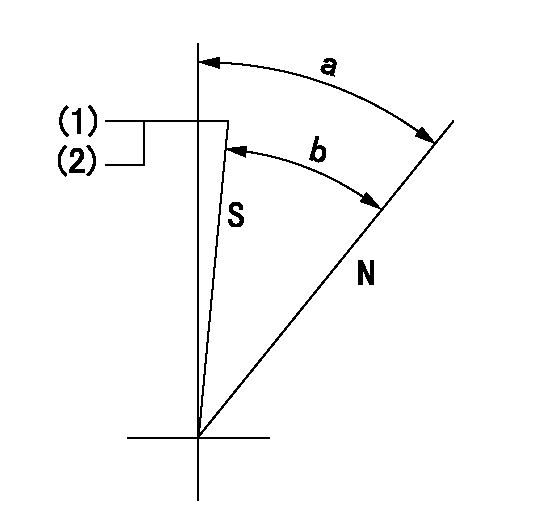
N:Pump normal
S:Stop the pump.
(1)Set the stopper bolt at speed = aa and rack position = bb and confirm non-injection.
(2)After setting the stopper bolt, confirm non-injection at speed cc.
----------
aa=1450r/min bb=6.2-0.5mm cc=300r/min
----------
a=36.5deg+-5deg b=(33deg)+-5deg
----------
aa=1450r/min bb=6.2-0.5mm cc=300r/min
----------
a=36.5deg+-5deg b=(33deg)+-5deg
0000001301

(1)Pump vertical direction
(2)Position of gear mark '3' at No 1 cylinder's beginning of injection
(3)B.T.D.C.: aa
(4)Pre-stroke: bb
----------
aa=7deg bb=5.6+-0.03mm
----------
a=(130deg)
----------
aa=7deg bb=5.6+-0.03mm
----------
a=(130deg)
0000001401
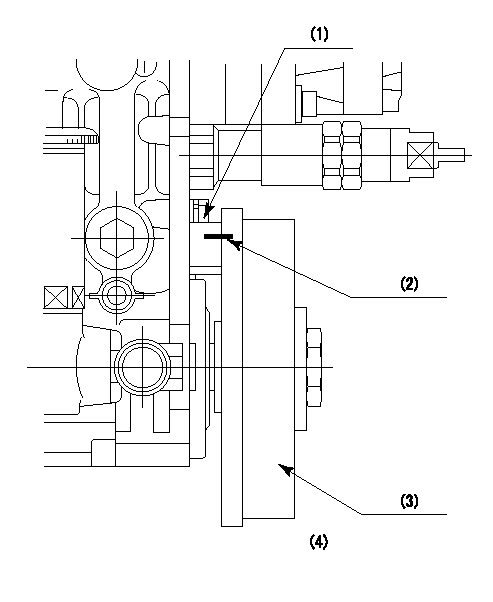
(1)Pointer
(2)Injection timing aligning mark
(3)Fly weight
(4)The actual shape and direction may be different from this illustration.
Operation sequence
1. Turn the prestroke actuator OFF.
2. Turn the camshaft as far as the No.1 cylinder's beginning of injection position.
3. Check that the pointer alignment mark of the injection pump and the alignment mark of the flywheel are matching.
4. If they are not matching, erase the alignment mark on the flywheel side, and stamp an alignment mark on the flywheel position that matches with the pointer side alignment mark.
5. Check again that the coupling's key groove position is in the No.1 cylinder's beginning of injection position.
----------
----------
----------
----------
0000001701
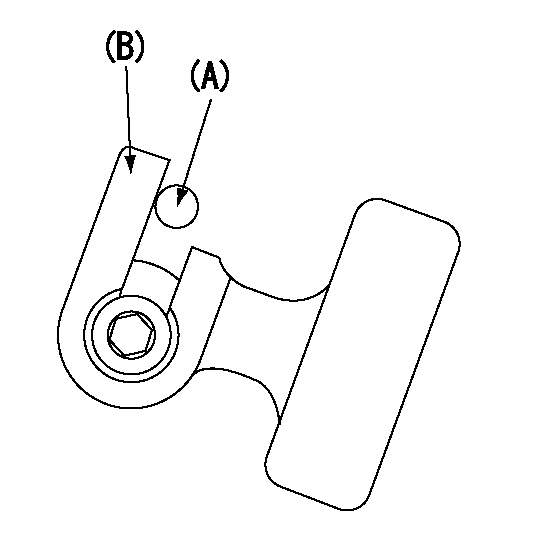
A : Stopper pin
B: Connector
----------
----------
----------
----------
0000001801
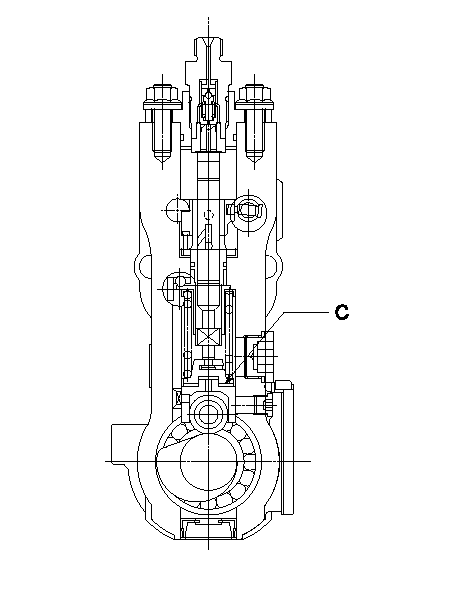
C:Shim
----------
----------
----------
----------
0000001901
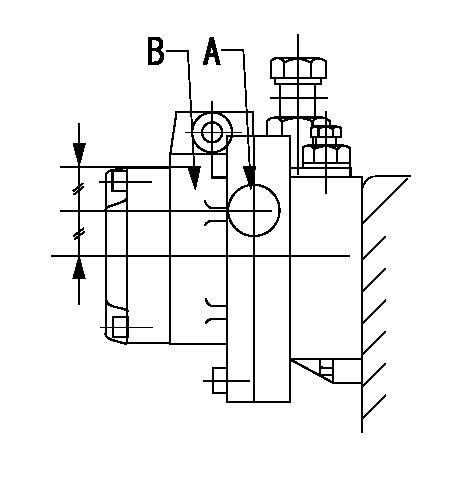
A:Sealing position
B:Pre-stroke actuator
1. When installing the pre-stroke actuator on the pump, first tighten the installation bolts loosely, then move the actuator fully counterclockwise (viewed from the drive side).
Temporary tightening torque: 1 - 1.5 N.m (0.1 - 0.15 kgf.m)
2. Move the actuator in the clockwise direction when viewed from the drive side, and adjust so that it becomes the adjustment point of the adjustment value. Then tighten it.
Tightening torque: 7^9 N.m (0.7^0.9 kgf.m)
3. After prestroke actuator installation adjustment, simultaneously stamp both the actuator side and housing side.
----------
----------
----------
----------
0000002201 RACK SENSOR
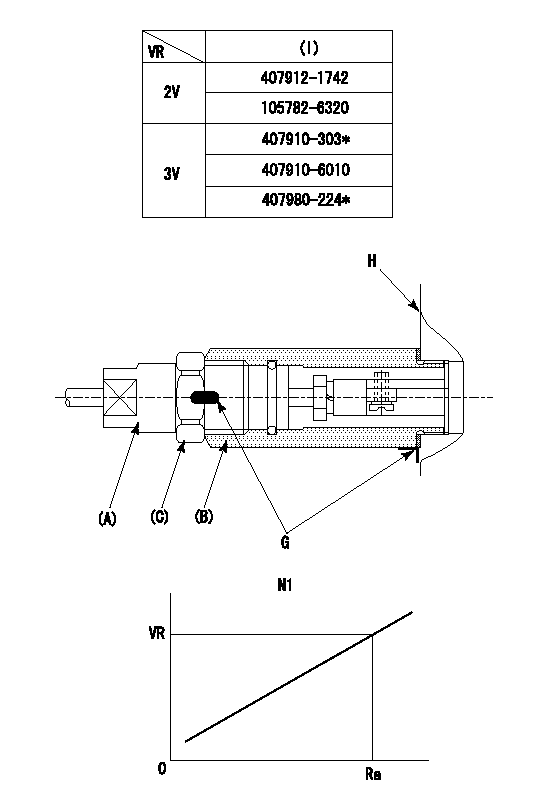
(VR) measurement voltage
(I) Part number of the control unit
(G) Apply red paint.
(H): End surface of the pump
1. Rack sensor adjustment (-0620)
(1)Fix the speed control lever at the full position
(2)Set the speed to N1 r/min.
(If the boost compensator is provided, apply boost pressure.)
(3)Adjust the bobbin (A) so that the rack sensor's output voltage is VR+-0.01.
(4)At that time, rack position must be Ra.
(5)Apply G at two places.
Connecting part between the joint (B) and the nut (F)
Connecting part between the joint (B) and the end surface of the pump (H)
----------
N1=1500r/min Ra=R1(12.5)+1.55mm
----------
----------
N1=1500r/min Ra=R1(12.5)+1.55mm
----------
Information:
Table 3
Injector Resistance Measurement
Step Instruction Completed
(Yes/No) Results
Comments Units
1 Turn the keyswitch to the OFF position. Allow 2 minutes to elapse before proceeding.
2 Disconnect the DEF injector from the applicable harness.
3 Inspect the connector for damage or debris (if damaged take photo)
4 Measure the temperature of the injector (aluminum body) C
5 Connect two 398-4987 connectors to the DEF injector. The connectors must be used to prevent damage to the DEF injector connector.
6 Measure the resistance of the DEF injector. Ohms
Table 4
Dosing Accuracy Test
Step Instruction Completed
(Yes/No) Results
Comments Units
1 Follow the Testing and Adjusting, Aftertreatment SCR System Dosing - Test.
2 Remove the injector from the DPF outlet.
3 Take a photograph of the DEF injector mount on the DPF outlet and the tip of the DEF injector.
4 Install the injector on the beaker.
5 Run the DEF System Dosing Accuracy test through Cat ET.
6 Use the breaker to measure the amount of fluid from the dosing test. ml
7 Repeat the test to verify consistency. ml
8 Install the injector back onto the DPF outlet.
Illustration 2 g06068068
DEF Injector Resistance Measurement
Illustration 3 g06067706
Injector Mount on DPF (Outlet Sample Picture)
Illustration 4 g06067753
DEF Injector Tip (Sample Picture)
When troubleshooting requests the DEF quality check, DEF injector resistance measurement or Dosing Accuracy Test, please document results in the Tables shown above.
After completing troubleshooting and performing the Aftertreatment System Functional Test, download a new Product Status Report with all ECM's.
Table 5
Injector Failure Report
Step Instruction Completed
(Yes/No) Results
Comments Units
1 Download "Product Status Report" (PSR) from the engine ECM and send to the email address in the instructions.
2 Download "Warranty Report" (WR) from the engine ECM and send to the email address in the instructions.
3 Take a picture of the injector part number / serial number.
4 Follow the correct TSG based on Table 1 and complete tables 2 through 4 when they apply.
5 Perform an "Aftertreatment System Functional Test".
6 Download "Product Status Report" (PSR) from the engine ECM and send to the email address in the instructions.
7 Submit "TIB Check List", "Product Status Reports", DEF injector deposits photographs, CEM deposit photographs, and DEF injector part number and serial number photograph to the email address in the instructions.
Fill out the Injector Failure Report and send all information including product status reports, warranty reports, DEF injector and mount photos, DEF injector part number and serial number and test results to the email address provided above.