Information injection-pump assembly
BOSCH
9 400 618 820
9400618820
ZEXEL
107491-3102
1074913102
HINO
220401252A
220401252a
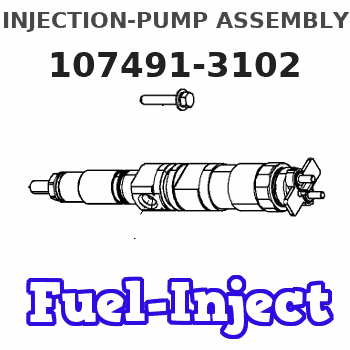
Rating:
Cross reference number
BOSCH
9 400 618 820
9400618820
ZEXEL
107491-3102
1074913102
HINO
220401252A
220401252a
Zexel num
Bosch num
Firm num
Name
9 400 618 820
220401252A HINO
INJECTION-PUMP ASSEMBLY
J05C-TF K 14CF INJECTION PUMP ASSY TICS MD-TI4 TICS
J05C-TF K 14CF INJECTION PUMP ASSY TICS MD-TI4 TICS
Calibration Data:
Adjustment conditions
Test oil
1404 Test oil ISO4113 or {SAEJ967d}
1404 Test oil ISO4113 or {SAEJ967d}
Test oil temperature
degC
40
40
45
Nozzle and nozzle holder
105780-8250
Bosch type code
1 688 901 101
Nozzle
105780-0120
Bosch type code
1 688 901 990
Nozzle holder
105780-2190
Opening pressure
MPa
20.7
Opening pressure
kgf/cm2
211
Injection pipe
Outer diameter - inner diameter - length (mm) mm 8-3-600
Outer diameter - inner diameter - length (mm) mm 8-3-600
Overflow valve
131425-0920
Overflow valve opening pressure
kPa
255
221
289
Overflow valve opening pressure
kgf/cm2
2.6
2.25
2.95
Tester oil delivery pressure
kPa
255
255
255
Tester oil delivery pressure
kgf/cm2
2.6
2.6
2.6
PS/ACT control unit part no.
407980-2
24*
Digi switch no.
17
Direction of rotation (viewed from drive side)
Left L
Left L
Injection timing adjustment
Direction of rotation (viewed from drive side)
Left L
Left L
Injection order
1-3-4-2
Pre-stroke
mm
5.1
5.07
5.13
Beginning of injection position
Governor side NO.1
Governor side NO.1
Difference between angles 1
Cal 1-3 deg. 90 89.75 90.25
Cal 1-3 deg. 90 89.75 90.25
Difference between angles 2
Cal 1-4 deg. 180 179.75 180.25
Cal 1-4 deg. 180 179.75 180.25
Difference between angles 3
Cyl.1-2 deg. 270 269.75 270.25
Cyl.1-2 deg. 270 269.75 270.25
Injection quantity adjustment
Adjusting point
-
Rack position
12.6
Pump speed
r/min
750
750
750
Average injection quantity
mm3/st.
118
115
121
Max. variation between cylinders
%
0
-3.5
3.5
Basic
*
Fixing the rack
*
PS407980-224*
V
2.25+-0.
01
PS407980-224*
mm
3.1+-0.0
5
Standard for adjustment of the maximum variation between cylinders
*
Injection quantity adjustment_02
Adjusting point
Z
Rack position
8+-0.5
Pump speed
r/min
505
505
505
Each cylinder's injection qty
mm3/st.
11.5
10.5
12.5
Fixing the rack
*
PS407980-224*
V
V1+0.05+
-0.01
PS407980-224*
mm
5+-0.03
Standard for adjustment of the maximum variation between cylinders
*
Remarks
Refer to items regarding the pre-stroke actuator
Refer to items regarding the pre-stroke actuator
Injection quantity adjustment_03
Adjusting point
A
Rack position
R1(12.6)
Pump speed
r/min
750
750
750
Average injection quantity
mm3/st.
118
116
120
Basic
*
Fixing the lever
*
Boost pressure
kPa
44
44
Boost pressure
mmHg
330
330
PS407980-224*
V
2.25+-0.
01
PS407980-224*
mm
3.1+-0.0
5
Injection quantity adjustment_04
Adjusting point
B
Rack position
R1+2.15
Pump speed
r/min
1250
1250
1250
Average injection quantity
mm3/st.
130
124
136
Fixing the lever
*
Boost pressure
kPa
44
44
Boost pressure
mmHg
330
330
PS407980-224*
V
2.25+-0.
01
PS407980-224*
mm
3.1+-0.0
5
Injection quantity adjustment_05
Adjusting point
C
Rack position
(R2-0.55
)
Pump speed
r/min
400
400
400
Average injection quantity
mm3/st.
102.5
99.5
105.5
Fixing the lever
*
Boost pressure
kPa
0
0
0
Boost pressure
mmHg
0
0
0
PS407980-224*
V
2.25+-0.
01
PS407980-224*
mm
3.1+-0.0
5
Boost compensator adjustment
Pump speed
r/min
400
400
400
Rack position
(R2-0.55
)
Boost pressure
kPa
22
20.7
23.3
Boost pressure
mmHg
165
155
175
Boost compensator adjustment_02
Pump speed
r/min
400
400
400
Rack position
R2(R1-0.
95)
Boost pressure
kPa
30.7
30.7
30.7
Boost pressure
mmHg
230
230
230
Timer adjustment
Pump speed
r/min
1170--
Advance angle
deg.
0
0
0
Remarks
Start
Start
Timer adjustment_02
Pump speed
r/min
1120
Advance angle
deg.
0
-0.3
0
Timer adjustment_03
Pump speed
r/min
1250-50
Advance angle
deg.
-1.5
-1.8
-1.2
Remarks
Finish
Finish
0000001601
CU407980-224*
*
Actuator retarding type
*
Supply voltage
V
24
23.5
24.5
Ambient temperature
degC
23
18
28
Pre-stroke
mm
2
1.95
2.05
Output voltage
V
2.83
2.82
2.84
Adjustment
*
_02
CU407980-224*
*
Supply voltage
V
24
23.5
24.5
Ambient temperature
degC
23
18
28
Pre-stroke
mm
5.1
5.07
5.13
Output voltage
V
1.2
1
1.4
Confirmation
*
Remarks
Output voltage V1
Output voltage V1
_03
CU407980-224*
*
Supply voltage
V
24
23.5
24.5
Ambient temperature
degC
23
18
28
Output voltage
V
3.05
3.05
Confirmation of operating range
*
Test data Ex:
Governor adjustment
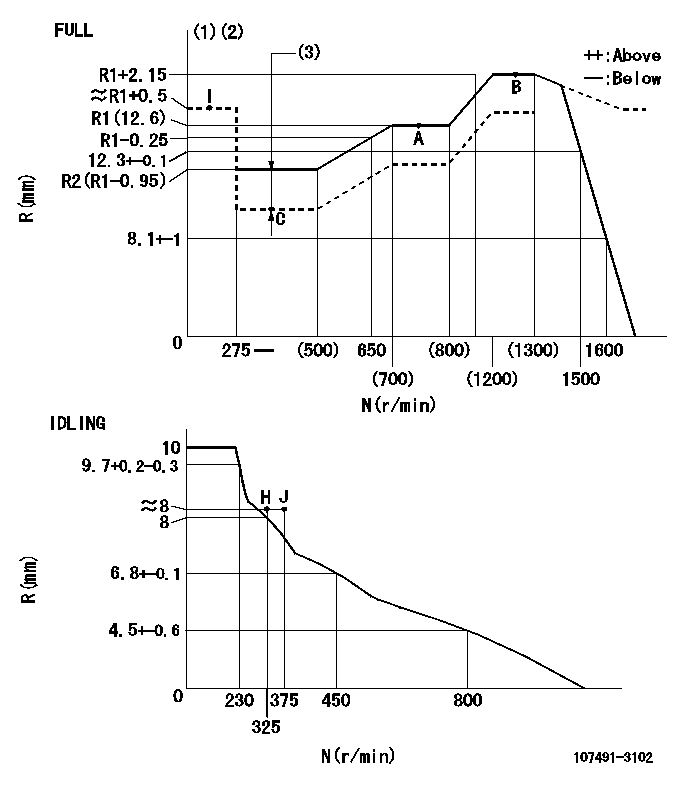
N:Pump speed
R:Rack position (mm)
(1)Torque cam stamping: T1
(2)Tolerance for racks not indicated: +-0.05mm.
(3)Boost compensator stroke: BCL
----------
T1=AF54 BCL=(0.55)+-0.1mm
----------
----------
T1=AF54 BCL=(0.55)+-0.1mm
----------
Speed control lever angle

F:Full speed
I:Idle
(1)Use the hole at R = aa
(2)Stopper bolt set position 'H'
----------
aa=40mm
----------
a=5deg+-5deg b=34.5deg+-3deg
----------
aa=40mm
----------
a=5deg+-5deg b=34.5deg+-3deg
Stop lever angle
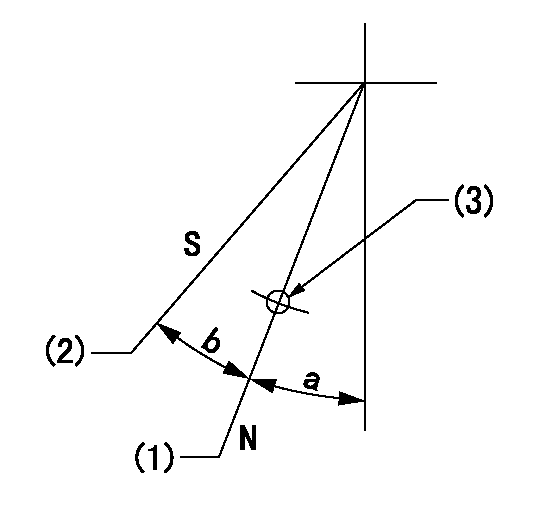
N:Pump normal
S:Stop the pump.
(1)Position at the normal side lever position (back off the stop screw and move fully to the normal side). Next, screw in the stop screw and set where it contacts the stop lever.
(2)Pump speed aa, rack position bb
(3)Use the hole above R = cc
----------
aa=0r/min bb=3.5+-0.1mm cc=35mm
----------
a=10.5deg+-5deg b=40deg+-5deg
----------
aa=0r/min bb=3.5+-0.1mm cc=35mm
----------
a=10.5deg+-5deg b=40deg+-5deg
0000001301
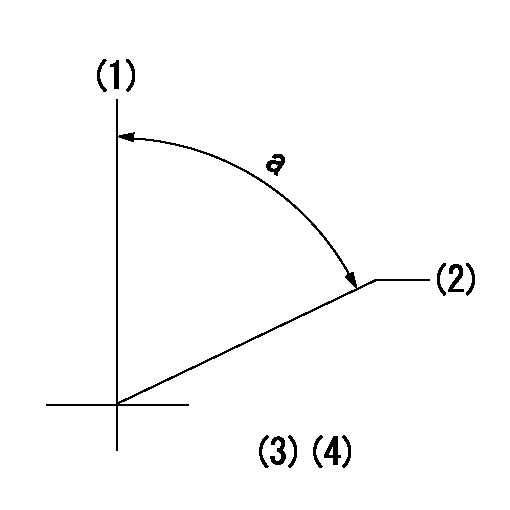
(1)Pump vertical direction
(2)Coupling's key groove position at No 1 cylinder's beginning of injection
(3)Pre-stroke: aa
(4)-
----------
aa=5.1+-0.03mm
----------
a=(80deg)
----------
aa=5.1+-0.03mm
----------
a=(80deg)
0000001401
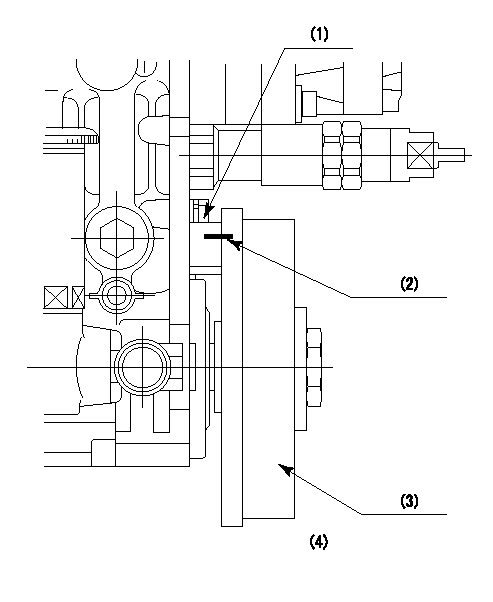
(1)Pointer
(2)Injection timing aligning mark
(3)Fly weight
(4)The actual shape and direction may be different from this illustration.
Operation sequence
1. Turn the prestroke actuator OFF.
2. Turn the camshaft as far as the No.1 cylinder's beginning of injection position.
3. Check that the pointer alignment mark of the injection pump and the alignment mark of the flywheel are matching.
4. If they are not matching, erase the alignment mark on the flywheel side, and stamp an alignment mark on the flywheel position that matches with the pointer side alignment mark.
5. Check again that the coupling's key groove position is in the No.1 cylinder's beginning of injection position.
----------
----------
----------
----------
0000001701
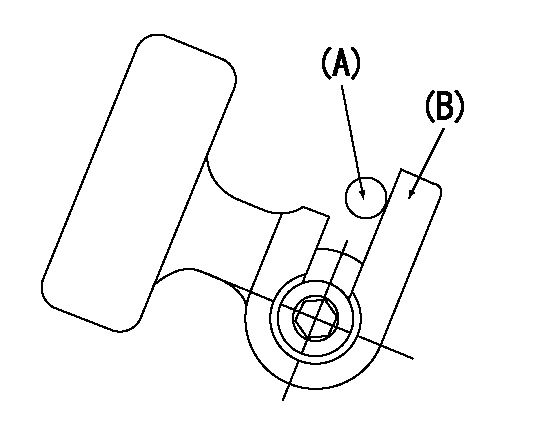
A : Stopper pin
B: Connector
----------
----------
----------
----------
0000001801
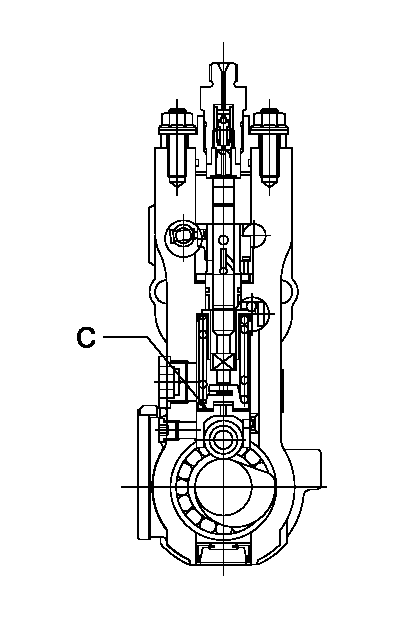
C:Shim
----------
----------
----------
----------
0000001901
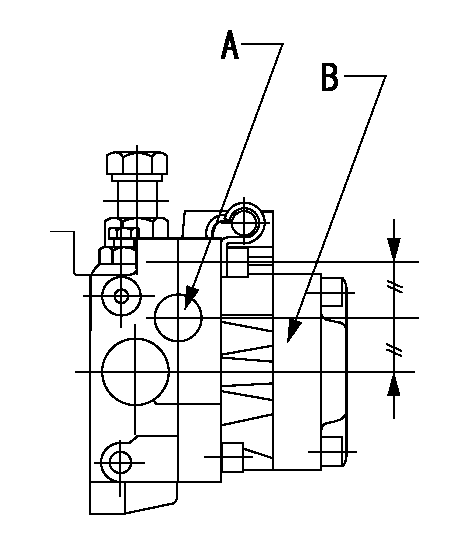
A:Sealing position
B:Pre-stroke actuator
1. When installing the pre-stroke actuator on the pump, first tighten the installation bolts loosely, then move the actuator fully clockwise (viewed from the drive side).
Temporary tightening torque: 1 - 1.5 N.m (0.1 - 0.15 kgf.m)
2. Move the actuator in the counterclockwise direction when viewed from the drive side, and adjust so that it becomes the adjustment point of the adjustment value. Then tighten it.
Tightening torque: 7^9 N.m (0.7^0.9 kgf.m)
3. After prestroke actuator installation adjustment, simultaneously stamp both the actuator side and housing side.
----------
----------
----------
----------
0000002201 RACK SENSOR
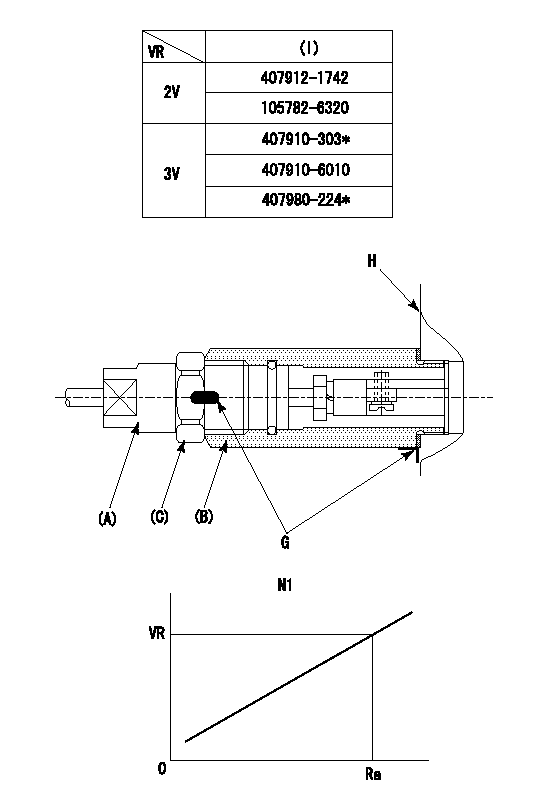
(VR) measurement voltage
(I) Part number of the control unit
(G) Apply red paint.
(H): End surface of the pump
1. Rack sensor adjustment (-0620)
(1)Fix the speed control lever at the full position
(2)Set the speed to N1 r/min.
(If the boost compensator is provided, apply boost pressure.)
(3)Adjust the bobbin (A) so that the rack sensor's output voltage is VR+-0.01.
(4)At that time, rack position must be Ra.
(5)Apply G at two places.
Connecting part between the joint (B) and the nut (F)
Connecting part between the joint (B) and the end surface of the pump (H)
----------
N1=1250r/min Ra=R1(12.6)+2.15mm
----------
----------
N1=1250r/min Ra=R1(12.6)+2.15mm
----------
Information:
TECHNICAL INFORMATION BULLETIN July 7, 2004
Engines
Machines 3054E (304, CRX)
3056E (356, CPT)
315C (ANF)
320C (CCD)
924G (DDA, DFZ, RBB, WGX, WMB)
928G (DJD, WLG)
AP-655C (CDG)
CP-563E (BWE, CNT)
CP-573E (ASY)
CS-563E (ASA, CNG)
CS-583E (DAJ)
CS-663E (DAG)
IT28G (DBT, EWF, WAC)
M313C (BDR)
M315C (BDM)
M316C (BDX)
M318C (BCZ)
M322C (BDK)
TH330B (SLB)
Component Code 1251SUBJECT: Replace Failed 3054E and 3056E Fuel Injection Pumps with New Pumps from Cat Parts
PROBLEM:
The 3054E and 3056E engines use electronic Bosch fuel injection pumps. These are new engine applications for these pumps. Therefore, initially, Bosch is requesting that all failed pumps are to be replaced by new pumps from Cat Parts. Replaced pumps are to be returned to Bosch through Peoria, IL or Peterborough, U.K. as described below, depending on location.
SOLUTION:
Failed fuel injection pumps are to be replaced by new pumps out of Cat Parts. Pumps should only be replaced after a full diagnostic check of the Engine and Machine. Troubleshooting Guide, RENR2417, should be used in order to perform the full diagnostic check. Replaced pumps must be returned to Caterpillar Inc. for forwarding to the supplier for full failure analysis.
Pumps from NACD and LACD territories are to be packaged and shipped to:
Caterpillar Service Claims Room
8201 N. University
Peoria, IL 61615 USA
Attn: 3000 Series Engine Service Engineer
Pumps from EAME and APD territories are to be packaged and shipped to:
Perkins Engines Ltd.
Return Parts Centre-C/O Ron Chandler
Peterborough PE1 5NA
U.K.
All failure information is to be submitted with each pump. Dealers are requested to supply FULL details regarding their investigations into the failure of the pump. This information will allow for a more detailed analysis of the pump failure. Attach the normal service claim form. The following list represents the minimum amount of additional information that should be submitted with the faulty pump and the service claim form.
A breakdown of the fault finding process employed using RENR2417
Details of the failure including symptoms that were experienced (Hard to start, etc?)
Screen prints from Caterpillar Electronic Technician (Cat ET) describing both the logged and active fault codes at the time of investigation
Other relevant details from customers include engine and machine history and the usage at the time of the incident
Dealers from EAME should email the above information to Alex Radjenovic at Radjenovic_Alex@perkins.com
Dealers from NACD and LACD should email the above information to Robert Stoetzer at Stoetzer_Robert_A
All returned fuel injection pump ports must be sealed prior to shipment to prevent contamination. The protective caps used on the new pump ports MUST be transferred to the failed pump ports prior to return shipment to avoid contamination in route to the supplier. Also, it is imperative that the pump be protected against damage during transit. Damage during transit may prevent assessment by the supplier.
Dealers in the NACD territory are to follow the established parts return procedures per Service Warranty Bulletin No. 7.1.
Dealers outside of the NACD territory are required to pay for the shipping cost of the returned pump, then claim the shipping cost as a miscellaneous expense on the warranty claim.
COPYRIGHT 2004 CATERPILLAR
ALL RIGHTS RESERVED