Information injection-pump assembly
BOSCH
9 400 619 917
9400619917
ZEXEL
106991-1315
1069911315
ISUZU
1156029962
1156029962
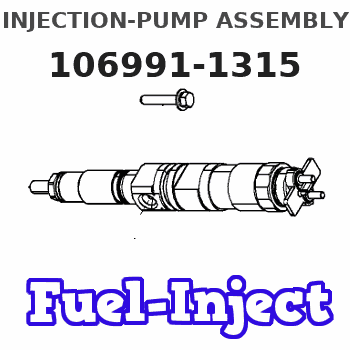
Rating:
Service parts 106991-1315 INJECTION-PUMP ASSEMBLY:
1.
_
6.
COUPLING PLATE
7.
COUPLING PLATE
8.
_
9.
_
11.
Nozzle and Holder
12.
Open Pre:MPa(Kqf/cm2)
15.7{160}/22.1{225}
15.
NOZZLE SET
Include in #1:
106991-1315
as INJECTION-PUMP ASSEMBLY
Cross reference number
BOSCH
9 400 619 917
9400619917
ZEXEL
106991-1315
1069911315
ISUZU
1156029962
1156029962
Zexel num
Bosch num
Firm num
Name
Calibration Data:
Adjustment conditions
Test oil
1404 Test oil ISO4113 or {SAEJ967d}
1404 Test oil ISO4113 or {SAEJ967d}
Test oil temperature
degC
40
40
45
Nozzle and nozzle holder
105780-8140
Bosch type code
EF8511/9A
Nozzle
105780-0000
Bosch type code
DN12SD12T
Nozzle holder
105780-2080
Bosch type code
EF8511/9
Opening pressure
MPa
17.2
Opening pressure
kgf/cm2
175
Injection pipe
Outer diameter - inner diameter - length (mm) mm 8-3-600
Outer diameter - inner diameter - length (mm) mm 8-3-600
Overflow valve (drive side)
134424-4320
Overflow valve opening pressure (drive side)
kPa
255
255
255
Overflow valve opening pressure (drive side)
kgf/cm2
2.6
2.6
2.6
Overflow valve (governor side)
134424-2720
Overflow valve opening pressure (governor side)
kPa
255
255
255
Overflow valve opening pressure (governor side)
kgf/cm2
2.6
2.6
2.6
Tester oil delivery pressure
kPa
157
157
157
Tester oil delivery pressure
kgf/cm2
1.6
1.6
1.6
Direction of rotation (viewed from drive side)
Right R
Right R
Injection timing adjustment
Direction of rotation (viewed from drive side)
Right R
Right R
Injection order
1-8-7-6-
5-4-3-10
-9-2
Pre-stroke
mm
4.2
4.17
4.23
Rack position
Point A R=A
Point A R=A
Beginning of injection position
Governor side NO.1
Governor side NO.1
Difference between angles 1
Cal 1-8 deg. 27 26.75 27.25
Cal 1-8 deg. 27 26.75 27.25
Difference between angles 2
Cal 1-7 deg. 72 71.75 72.25
Cal 1-7 deg. 72 71.75 72.25
Difference between angles 3
Cal 1-6 deg. 99 98.75 99.25
Cal 1-6 deg. 99 98.75 99.25
Difference between angles 4
Cal 1-5 deg. 144 143.75 144.25
Cal 1-5 deg. 144 143.75 144.25
Difference between angles 5
Cal 1-4 deg. 171 170.75 171.25
Cal 1-4 deg. 171 170.75 171.25
Difference between angles 6
Cal 1-3 deg. 216 215.75 216.25
Cal 1-3 deg. 216 215.75 216.25
Difference between angles 7
Cal 1-10 deg. 243 242.75 243.25
Cal 1-10 deg. 243 242.75 243.25
Difference between angles 8
Cal 1-9 deg. 288 287.75 288.25
Cal 1-9 deg. 288 287.75 288.25
Difference between angles 9
Cyl.1-2 deg. 315 314.75 315.25
Cyl.1-2 deg. 315 314.75 315.25
Injection quantity adjustment
Adjusting point
A
Rack position
8.1
Pump speed
r/min
800
800
800
Average injection quantity
mm3/st.
104
102.5
105.5
Max. variation between cylinders
%
0
-2
2
Basic
*
Fixing the lever
*
Injection quantity adjustment_02
Adjusting point
C
Rack position
7.6
Pump speed
r/min
1100
1100
1100
Average injection quantity
mm3/st.
109.6
107.6
111.6
Max. variation between cylinders
%
0
-13
13
Fixing the lever
*
Injection quantity adjustment_03
Adjusting point
D
Rack position
4.8+-0.5
Pump speed
r/min
225
225
225
Average injection quantity
mm3/st.
8.7
7.4
10
Fixing the rack
*
Timer adjustment
Pump speed
r/min
600--
Advance angle
deg.
0
0
0
Remarks
Start
Start
Timer adjustment_02
Pump speed
r/min
550
Advance angle
deg.
0.3
Timer adjustment_03
Pump speed
r/min
820+-30
Advance angle
deg.
2
1.5
2.5
Timer adjustment_04
Pump speed
r/min
1100
Advance angle
deg.
5.5
5
6
Remarks
Finish
Finish
Test data Ex:
Governor adjustment
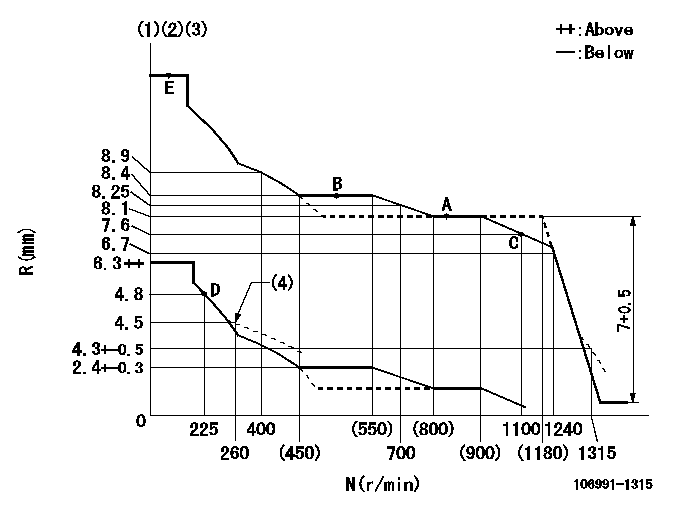
N:Pump speed
R:Rack position (mm)
(1)Lever ratio: RT
(2)Target shim dimension: TH
(3)Tolerance for racks not indicated: +-0.05mm.
(4)Damper spring setting
----------
RT=0.8 TH=1.9mm
----------
----------
RT=0.8 TH=1.9mm
----------
Speed control lever angle

F:Full speed
----------
----------
a=6deg+-5deg
----------
----------
a=6deg+-5deg
0000000901
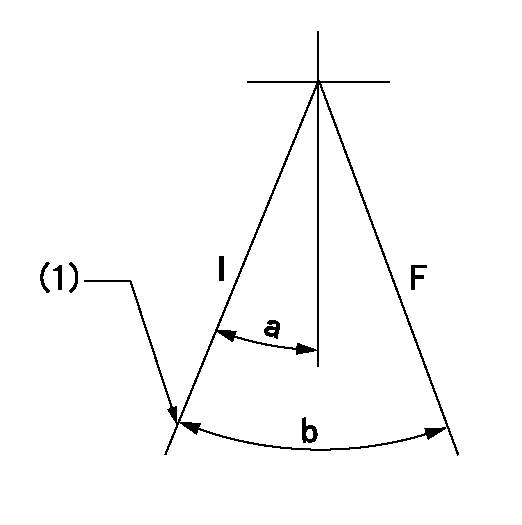
F:Full load
I:Idle
(1)Stopper bolt setting
----------
----------
a=10deg+-5deg b=32deg+-3deg
----------
----------
a=10deg+-5deg b=32deg+-3deg
Stop lever angle

N:Pump normal
S:Stop the pump.
(1)Use the hole at R = aa
----------
aa=25mm
----------
a=64deg+-5deg b=51deg+-5deg
----------
aa=25mm
----------
a=64deg+-5deg b=51deg+-5deg
Timing setting

(1)Pump vertical direction
(2)Position of "Z" mark at the No 1 cylinder's beginning of injection (governor side)
(3)B.T.D.C.: aa (set timing)
(4)-
----------
aa=8deg
----------
a=(180deg)
----------
aa=8deg
----------
a=(180deg)
Information:
Storage Procedure
When a generator is in storage for any length of time, moisture condenses in the windings. Minimize the condensation by use of a dry storage space and space heaters. Refer to step 2 belowIf a brush-type generator (SRCR) is to be in storage for a year or more, lift the brushes off the slip ring to prevent damage to the slip ring by chemical action.After Storage
Test the main stator windings with a megohmmeter in the following situations: 1. Before initial startup of generator set.2. Every 3 months* if generator is operating in a humid environment.3. If generator has not been run under load for 3 months* or more.*This is a guideline only. It may be necessary to megger more frequently if environment is extremely humid, salty or if the last megger test was close to 1 megohm.The megohmmeter test is described in Service Manuals SENR2180 or SENR7968. A reading of 1 meghom or less indicates that the winding has absorbed too much moisture.To Remove Moisture
To remove moisture caused by high humidity, use one of the following methods to make the generator dry:1. Energize space heaters in generator if so equipped.2. Put the generator in an oven at a temperature of not more than 85°C (185°F) for four hours.
If an oven is used for drying, use a forced air type rather than a radiant type. Radiant ovens can cause localized overheating.
3. Space heaters of the same type used in marine applications, can be installed on generators. (See the Parts Book.) These heaters heat the windings to remove moisture and should be connected at all times in high humidity conditions whenever the generator is not running.4. Use a canvas enclosure around the generator and heating lamps to increase the temperature. Make an opening in the top for release of moisture.5. Send a low voltage current through the windings to increase the temperature of the windings. Do not exceed 85°C (185°F).If the megohmmeter test reads under 1 megohm after the drying or if it goes below 1 megohm shortly after drying, contact your Caterpillar dealer. The insulation has deteriorated and should be reconditioned.
When a generator is in storage for any length of time, moisture condenses in the windings. Minimize the condensation by use of a dry storage space and space heaters. Refer to step 2 belowIf a brush-type generator (SRCR) is to be in storage for a year or more, lift the brushes off the slip ring to prevent damage to the slip ring by chemical action.After Storage
Test the main stator windings with a megohmmeter in the following situations: 1. Before initial startup of generator set.2. Every 3 months* if generator is operating in a humid environment.3. If generator has not been run under load for 3 months* or more.*This is a guideline only. It may be necessary to megger more frequently if environment is extremely humid, salty or if the last megger test was close to 1 megohm.The megohmmeter test is described in Service Manuals SENR2180 or SENR7968. A reading of 1 meghom or less indicates that the winding has absorbed too much moisture.To Remove Moisture
To remove moisture caused by high humidity, use one of the following methods to make the generator dry:1. Energize space heaters in generator if so equipped.2. Put the generator in an oven at a temperature of not more than 85°C (185°F) for four hours.
If an oven is used for drying, use a forced air type rather than a radiant type. Radiant ovens can cause localized overheating.
3. Space heaters of the same type used in marine applications, can be installed on generators. (See the Parts Book.) These heaters heat the windings to remove moisture and should be connected at all times in high humidity conditions whenever the generator is not running.4. Use a canvas enclosure around the generator and heating lamps to increase the temperature. Make an opening in the top for release of moisture.5. Send a low voltage current through the windings to increase the temperature of the windings. Do not exceed 85°C (185°F).If the megohmmeter test reads under 1 megohm after the drying or if it goes below 1 megohm shortly after drying, contact your Caterpillar dealer. The insulation has deteriorated and should be reconditioned.